- お役立ち記事
- How to overcome inventory management challenges faced by purchasing managers
How to overcome inventory management challenges faced by purchasing managers
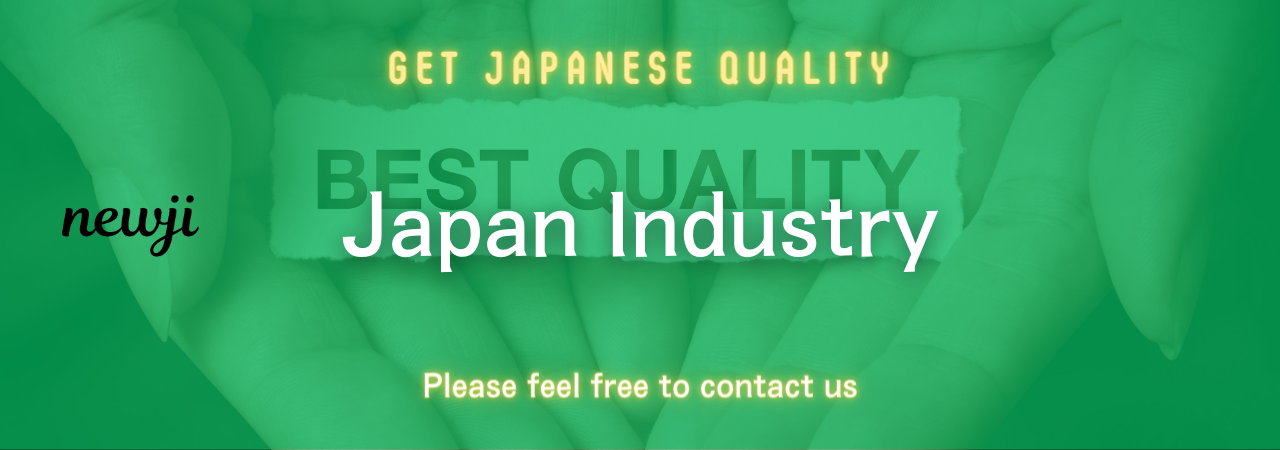
目次
Understanding Inventory Management Challenges
Inventory management is one of the critical responsibilities faced by purchasing managers across industries.
With the growing complexity of supply chains, managing inventory effectively becomes more challenging.
Purchasing managers need to find ways to ensure that inventory levels are just right.
Both overstocking and understocking can significantly impact a company’s bottom line.
In this article, we will explore some of the common inventory management challenges and ways to overcome them.
Balancing Supply and Demand
One of the primary challenges in inventory management is balancing supply and demand.
Demand forecasting can be unpredictable, affected by factors such as seasonal changes, market trends, and unforeseen events.
Purchasing managers face the challenge of maintaining an adequate inventory level without overstocking or understocking.
To overcome this, companies can invest in advanced analytics and forecasting tools to better predict demand patterns.
Communicating with sales and marketing departments can also provide valuable insights to refine forecasts.
Managing Lead Times
Another significant challenge is managing lead times, which can vary depending on suppliers and products.
Longer lead times require purchasing managers to plan purchases far in advance.
Disruptions in supplier networks can further complicate this issue, leading to delays and inventory shortages.
To mitigate these challenges, purchasing managers should work on establishing strong relationships with reliable suppliers.
Implementing a supplier management system can also help monitor lead times and improve communication.
Optimizing Storage Costs
Storage costs are a major concern in inventory management.
Purchasing managers must consider the cost of storing excess inventory, which can consume valuable resources.
Holding too much inventory can lead to increased warehousing expenses and potential obsolescence of products.
Adopting a just-in-time (JIT) inventory strategy can minimize storage costs by ensuring that products arrive only as needed.
Regular inventory audits can also help identify slow-moving items that occupy unnecessary space.
Reducing Stockouts and Excess Inventory
Avoiding stockouts and excess inventory are twin goals for purchasing managers.
Stockouts can result in lost sales and weakened customer relationships, while excess inventory ties up capital and space.
Effective inventory management requires a delicate balance between these two extremes.
Implementing an automated inventory management system can provide real-time data and insights.
This technology can help track inventory levels accurately and trigger replenishment orders automatically when stock reaches a predefined threshold.
Enhancing Supplier Performance
Supplier performance plays a crucial role in inventory management.
Purchasing managers must work with suppliers who deliver on time, maintain quality standards, and offer competitive pricing.
A supplier failing in any of these aspects can disrupt the inventory flow.
To address this, companies can establish key performance indicators (KPIs) to evaluate supplier performance regularly.
Conducting supplier audits and maintaining open communication channels can help build more robust partnerships.
Addressing Inventory Accuracy
Inventory accuracy is essential for efficient inventory management.
Discrepancies between recorded inventory levels and actual stock can lead to errors in planning and replenishment.
To improve accuracy, companies should invest in reliable inventory management software.
Conducting regular physical inventory counts can help detect and rectify discrepancies between system and actual inventory levels.
Implementing Technology Solutions
Leveraging technology is important to overcome inventory management challenges.
Purchasing managers can benefit from integrated inventory management systems that offer real-time visibility into inventory levels.
These systems help in optimizing inventory, tracking locations, and generating detailed reports.
Using RFID and barcode technology can streamline processes like goods receipt, tracking, and picking.
Automation can reduce manual errors and facilitate efficient inventory management.
Training and Development
Another critical aspect of overcoming inventory management challenges is investing in training and development.
Purchasing managers should be equipped with the knowledge and skills to handle complex inventory systems.
Offering training programs can enhance their ability to analyze data, predict demand, and make informed decisions.
Companies can also encourage cross-functional training to improve collaboration between different departments involved in inventory management.
Adapting to Market Changes
The market environment is dynamic, with frequent changes affecting inventory management.
Purchasing managers must stay adaptive and responsive to changes in consumer behavior, competition, and economic conditions.
Conducting market research and staying updated with industry trends can help manage inventory more effectively.
Developing contingency plans for unexpected events like supply chain disruptions or sudden demand fluctuations is crucial.
Conclusion
Inventory management challenges faced by purchasing managers are multifaceted and require proactive solutions.
Balancing supply and demand, optimizing storage costs, and ensuring inventory accuracy are essential to maintain operational efficiency.
Investing in technology, enhancing supplier relationships, and improving employee skills are effective strategies to overcome these challenges.
By staying adaptive and informed, purchasing managers can enhance their inventory management practices and contribute to their company’s success.
資料ダウンロード
QCD調達購買管理クラウド「newji」は、調達購買部門で必要なQCD管理全てを備えた、現場特化型兼クラウド型の今世紀最高の購買管理システムとなります。
ユーザー登録
調達購買業務の効率化だけでなく、システムを導入することで、コスト削減や製品・資材のステータス可視化のほか、属人化していた購買情報の共有化による内部不正防止や統制にも役立ちます。
NEWJI DX
製造業に特化したデジタルトランスフォーメーション(DX)の実現を目指す請負開発型のコンサルティングサービスです。AI、iPaaS、および先端の技術を駆使して、製造プロセスの効率化、業務効率化、チームワーク強化、コスト削減、品質向上を実現します。このサービスは、製造業の課題を深く理解し、それに対する最適なデジタルソリューションを提供することで、企業が持続的な成長とイノベーションを達成できるようサポートします。
オンライン講座
製造業、主に購買・調達部門にお勤めの方々に向けた情報を配信しております。
新任の方やベテランの方、管理職を対象とした幅広いコンテンツをご用意しております。
お問い合わせ
コストダウンが利益に直結する術だと理解していても、なかなか前に進めることができない状況。そんな時は、newjiのコストダウン自動化機能で大きく利益貢献しよう!
(Β版非公開)