- お役立ち記事
- Unlocking the Secrets of Japanese Frozen Food OEM: Innovation, Quality, and Efficiency at its Best
Unlocking the Secrets of Japanese Frozen Food OEM: Innovation, Quality, and Efficiency at its Best
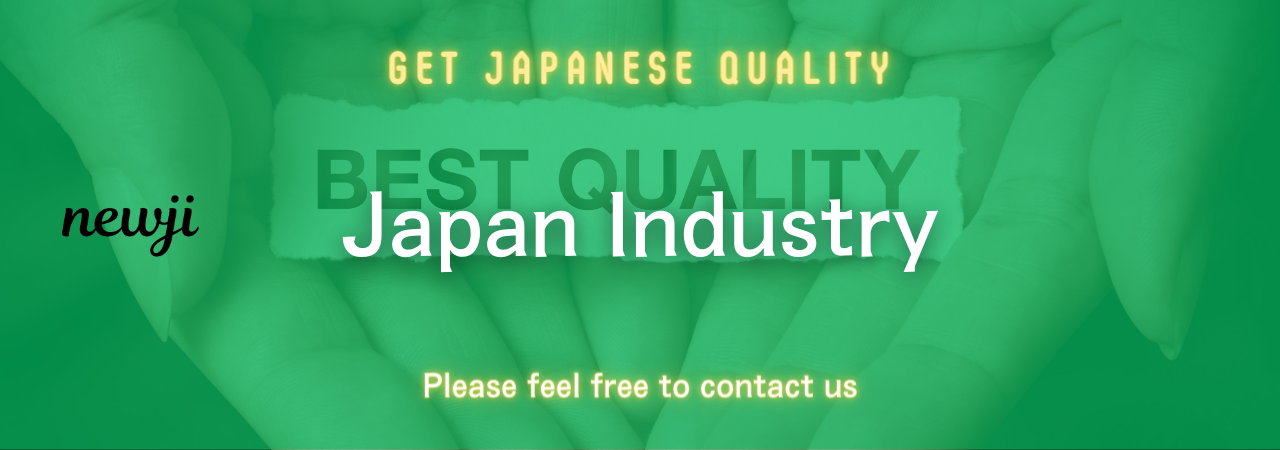
目次
Introduction to Japanese Frozen Food OEM
The Japanese frozen food Original Equipment Manufacturing (OEM) sector has garnered significant attention in the global market. Renowned for its commitment to innovation, quality, and efficiency, Japan’s manufacturing prowess offers unparalleled opportunities for international businesses. Understanding the dynamics of Japanese OEM can unlock numerous benefits for companies seeking to enhance their product offerings and operational standards.
The Pillars of Japanese Frozen Food OEM
Innovation
Japanese manufacturers are at the forefront of food technology and innovation. They invest heavily in research and development to create products that meet evolving consumer demands. From advanced freezing techniques that preserve flavor and nutrients to the introduction of novel food items, innovation drives the competitiveness of Japanese OEMs in the global market.
Quality
Quality is a non-negotiable aspect of Japanese manufacturing. Stringent quality control measures ensure that every product meets high standards. This commitment to quality extends from raw material selection to the final packaging, guaranteeing consistency and reliability. For international partners, this means access to superior products that enhance their brand reputation.
Efficiency
Efficiency in production processes is another hallmark of Japanese OEMs. Lean manufacturing principles, just-in-time inventory management, and advanced automation contribute to streamlined operations. These efficiencies not only reduce production costs but also ensure timely delivery, providing a competitive edge in the fast-paced food industry.
Advantages of Partnering with Japanese Frozen Food OEMs
Access to Advanced Technology
Japanese OEMs leverage cutting-edge technology to enhance product quality and production efficiency. Collaborating with these manufacturers allows international companies to incorporate the latest advancements into their product lines, staying ahead of market trends.
Consistent Quality Assurance
The rigorous quality control systems in place guarantee that products meet international standards. This consistency reduces the risk of defects and recalls, ensuring that the end consumers receive products they can trust.
Strong Supply Chain Management
Japanese OEMs excel in supply chain management, ensuring reliable and timely delivery of products. Their robust logistics networks minimize disruptions and enhance the overall reliability of the supply chain, which is crucial for maintaining production schedules and meeting market demand.
Cultural Compatibility and Business Practices
Japanese business practices emphasize respect, punctuality, and meticulous attention to detail. These cultural traits foster strong, long-term partnerships based on mutual trust and understanding. Such compatibility often translates into smoother negotiations and more effective collaboration.
Challenges in Collaborating with Japanese OEMs
Language and Communication Barriers
While many Japanese OEMs have personnel proficient in English, language barriers can still pose challenges. Effective communication requires clarity and often the use of professional translators or bilingual staff to ensure that requirements and expectations are clearly understood.
Cultural Differences
Japanese business culture values hierarchy, consensus, and indirect communication. International partners must navigate these cultural nuances to build strong relationships and avoid misunderstandings that could impact collaboration.
Higher Initial Costs
The emphasis on quality and advanced technology can result in higher production costs. While the long-term benefits of quality and efficiency often outweigh these initial expenses, companies must carefully assess their budgets and cost structures when partnering with Japanese OEMs.
Supplier Negotiation Techniques
Building Trust and Long-term Relationships
Establishing trust is paramount in Japanese business culture. Investing time in relationship-building activities, such as regular visits and meetings, can foster a strong partnership conducive to successful negotiations.
Understanding Cultural Etiquette
Respecting Japanese business etiquette, such as exchanging business cards with both hands, punctuality, and formal communication, can create a positive impression and facilitate smoother negotiations.
Clear Communication of Requirements
Clearly articulating product specifications, quality standards, and delivery timelines is essential. Providing detailed documentation and being open to feedback helps ensure that both parties are aligned in their expectations.
Flexibility and Compromise
Demonstrating flexibility in negotiations and being willing to make concessions on certain aspects can lead to mutually beneficial agreements. Understanding the priorities of the Japanese OEM and finding common ground is key to successful negotiations.
Market Conditions Affecting Japanese Frozen Food OEM
Global Supply Chain Disruptions
Global events, such as pandemics or geopolitical tensions, can disrupt supply chains. Japanese OEMs have developed robust strategies to mitigate these risks, including diversified sourcing and strong local supplier networks, ensuring continuity in production and delivery.
Changing Consumer Preferences
As consumers become more health-conscious and demand diverse food options, Japanese OEMs adapt by developing products that cater to these trends. Staying attuned to market shifts allows OEMs to innovate and remain relevant.
Regulatory Compliance
Adhering to international food safety and import regulations is crucial. Japanese OEMs are adept at navigating these regulatory landscapes, ensuring that their products meet the necessary standards for different markets.
Economic Factors
Fluctuations in exchange rates, inflation, and economic growth can impact production costs and pricing strategies. Japanese OEMs employ financial strategies to manage these economic variables effectively, maintaining stable pricing and profitability.
Best Practices for Successful Collaboration
Thorough Vendor Assessment
Conducting comprehensive evaluations of potential OEM partners, including their financial stability, production capabilities, and quality control systems, is essential for selecting the right partner.
Clear Contractual Agreements
Defining terms and conditions clearly in contractual agreements, including product specifications, pricing, delivery schedules, and quality standards, helps prevent disputes and ensures accountability.
Regular Performance Reviews
Implementing a system for regular performance evaluations allows for continuous improvement. Feedback mechanisms enable both parties to address issues promptly and enhance overall collaboration.
Joint Innovation Initiatives
Collaborating on research and development projects can lead to innovative product offerings. Joint initiatives foster a sense of partnership and drive mutual growth.
Strategies for Enhancing Factory Efficiency and Automation
Implementing Lean Manufacturing Principles
Adopting lean manufacturing techniques helps eliminate waste, streamline processes, and improve overall efficiency. Japanese OEMs excel in applying these principles to optimize production workflows.
Investing in Advanced Automation Technologies
Automation reduces manual labor, minimizes errors, and increases production speed. Investing in robotics, AI-driven systems, and automated quality control ensures consistent and high-quality output.
Continuous Training and Development
Ensuring that the workforce is well-trained in the latest technologies and processes is vital. Continuous education and training programs empower employees to operate efficiently and adapt to technological advancements.
Data-Driven Decision Making
Utilizing data analytics to monitor production metrics, identify bottlenecks, and make informed decisions enhances operational efficiency. Real-time data provides actionable insights for optimizing manufacturing processes.
Quality Control in Japanese Frozen Food OEM
Comprehensive Quality Management Systems
Japanese OEMs implement rigorous quality management systems, such as ISO certifications, to maintain high standards. These systems encompass every stage of production, ensuring consistency and reliability.
Regular Audits and Inspections
Frequent audits and inspections identify potential quality issues early. Proactive measures allow for timely corrections, maintaining the integrity of the products.
Supplier Quality Assurance
Ensuring that raw materials meet quality standards is crucial. Japanese OEMs work closely with their suppliers, conducting thorough evaluations and maintaining strict quality criteria to guarantee the excellence of the final product.
Customer Feedback Integration
Incorporating customer feedback into the quality control process helps refine products and address any issues promptly. This responsiveness enhances customer satisfaction and loyalty.
Logistics and Supply Chain Management
Optimized Transportation Networks
Efficient transportation networks ensure timely delivery of products. Japanese OEMs leverage their extensive logistics expertise to manage transport routes, reduce transit times, and minimize costs.
Inventory Management Solutions
Implementing advanced inventory management systems enables accurate tracking of stock levels, reducing the risk of overstocking or stockouts. Just-in-time inventory practices further enhance supply chain efficiency.
Risk Mitigation Strategies
Identifying potential risks within the supply chain and developing contingency plans is essential for maintaining smooth operations. Japanese OEMs employ strategies such as diversified sourcing and buffer inventories to mitigate disruptions.
Collaboration with Logistics Partners
Working closely with reliable logistics partners ensures seamless coordination and enhances the overall efficiency of the supply chain. Strong partnerships facilitate better communication and problem-solving.
Production Management and Engineering Excellence
Advanced Production Planning
Effective production planning coordinates various manufacturing activities, ensuring that resources are utilized optimally. Japanese OEMs excel in forecasting demand, scheduling production runs, and managing resources efficiently.
Integration of Industry 4.0 Technologies
Incorporating Industry 4.0 technologies, such as the Internet of Things (IoT) and smart manufacturing systems, enhances production flexibility and responsiveness. These technologies enable real-time monitoring and adaptive manufacturing processes.
Sustainability in Production
Japanese OEMs prioritize sustainable manufacturing practices, reducing waste and minimizing environmental impact. Sustainable production not only aligns with global environmental standards but also appeals to eco-conscious consumers.
Continuous Improvement Culture
A culture of continuous improvement encourages ongoing optimization of production processes. Japanese OEMs foster this mindset through Kaizen practices, promoting incremental enhancements that collectively lead to significant gains in efficiency and quality.
Procurement and Purchasing Strategies
Strategic Sourcing
Implementing strategic sourcing practices ensures that procurement efforts align with overall business objectives. Japanese OEMs focus on sourcing high-quality materials at competitive prices, balancing cost-effectiveness with quality assurance.
Supplier Relationship Management
Maintaining strong relationships with suppliers fosters collaboration and trust. Regular communication, performance evaluations, and mutual support enhance the reliability and quality of supplied materials.
Cost Management Techniques
Employing cost management strategies, such as bulk purchasing and long-term contracts, helps reduce procurement costs. Japanese OEMs leverage their buying power and negotiation skills to secure favorable terms.
Risk Assessment and Mitigation
Evaluating and addressing potential procurement risks, such as supplier insolvency or material shortages, is critical for maintaining a stable supply chain. Japanese OEMs implement risk mitigation measures to ensure uninterrupted production.
Conclusion
Collaborating with Japanese frozen food OEMs offers numerous advantages, including access to advanced technology, consistent quality, and efficient production processes. While challenges such as cultural differences and initial costs exist, the benefits of partnering with these manufacturers often outweigh the drawbacks. By employing effective negotiation techniques, understanding market conditions, and adopting best practices, international businesses can unlock the full potential of Japanese OEMs. Emphasizing innovation, quality, and efficiency, Japanese frozen food OEMs continue to set industry standards, making them invaluable partners in the global marketplace.
資料ダウンロード
QCD調達購買管理クラウド「newji」は、調達購買部門で必要なQCD管理全てを備えた、現場特化型兼クラウド型の今世紀最高の購買管理システムとなります。
ユーザー登録
調達購買業務の効率化だけでなく、システムを導入することで、コスト削減や製品・資材のステータス可視化のほか、属人化していた購買情報の共有化による内部不正防止や統制にも役立ちます。
NEWJI DX
製造業に特化したデジタルトランスフォーメーション(DX)の実現を目指す請負開発型のコンサルティングサービスです。AI、iPaaS、および先端の技術を駆使して、製造プロセスの効率化、業務効率化、チームワーク強化、コスト削減、品質向上を実現します。このサービスは、製造業の課題を深く理解し、それに対する最適なデジタルソリューションを提供することで、企業が持続的な成長とイノベーションを達成できるようサポートします。
オンライン講座
製造業、主に購買・調達部門にお勤めの方々に向けた情報を配信しております。
新任の方やベテランの方、管理職を対象とした幅広いコンテンツをご用意しております。
お問い合わせ
コストダウンが利益に直結する術だと理解していても、なかなか前に進めることができない状況。そんな時は、newjiのコストダウン自動化機能で大きく利益貢献しよう!
(Β版非公開)