- お役立ち記事
- Revolutionizing Precision: Japanese Manufacturing Mastery in Thin-Walled Stainless Steel Tubular Components
Revolutionizing Precision: Japanese Manufacturing Mastery in Thin-Walled Stainless Steel Tubular Components
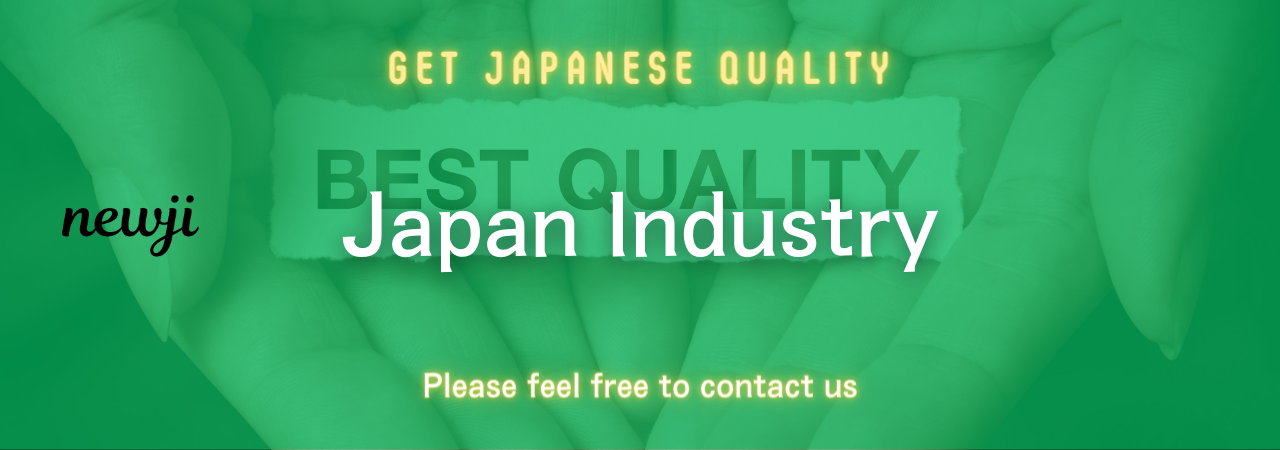
目次
Introduction to Japanese Precision in Thin-Walled Stainless Steel Tubular Components
Japanese manufacturing has long been revered for its precision and quality. Among the numerous sectors where Japan excels, the production of thin-walled stainless steel tubular components stands out. These components are critical in various industries, including automotive, aerospace, medical devices, and construction. This article delves into the mastery of Japanese manufacturing in this niche, exploring its advantages, challenges, procurement strategies, and best practices.
Understanding Thin-Walled Stainless Steel Tubular Components
Thin-walled stainless steel tubular components are specialized products characterized by their minimal wall thickness and robust structural integrity. They are essential in applications where weight reduction and strength are paramount. The precision required in manufacturing these components ensures they meet stringent specifications and performance standards.
Applications Across Industries
These components are integral to:
– **Automotive Industry**: Used in fuel lines, exhaust systems, and structural frameworks.
– **Aerospace**: Essential for aircraft structural components and hydraulic systems.
– **Medical Devices**: Utilized in surgical instruments and imaging equipment.
– **Construction**: Employed in lightweight structural frameworks and piping systems.
The Japanese Manufacturing Advantage
Japanese manufacturers are synonymous with high-quality production. Their expertise in thin-walled stainless steel tubular components stems from a combination of advanced technology, meticulous quality control, and a culture of continuous improvement.
Advanced Manufacturing Technologies
Japanese factories leverage state-of-the-art machinery and automation to achieve high precision. Techniques such as laser cutting, precision welding, and automated assembly lines ensure consistency and reduce human error.
Meticulous Quality Control
Quality is ingrained in the Japanese manufacturing ethos. Rigorous inspection protocols at every production stage guarantee that components meet exacting standards. This focus on quality minimizes defects and enhances reliability.
Continuous Improvement (Kaizen)
The principle of Kaizen, or continuous improvement, drives Japanese manufacturers to constantly refine their processes. This relentless pursuit of excellence leads to incremental advancements in efficiency and product quality.
Advantages of Procuring from Japanese Suppliers
Choosing Japanese suppliers for thin-walled stainless steel tubular components offers several benefits.
Unmatched Precision and Quality
Japanese manufacturers are leaders in precision engineering. Their ability to produce components with tight tolerances ensures superior performance and longevity.
Reliability and Consistency
Japanese suppliers maintain high standards of reliability. Consistent delivery schedules and product quality foster long-term partnerships and reduce supply chain disruptions.
Innovative Solutions
Japanese companies invest heavily in research and development. This focus on innovation results in advanced products and cutting-edge manufacturing techniques.
Strong Supplier Relationships
Japanese business culture emphasizes building strong, trust-based relationships. This approach facilitates better communication, collaboration, and problem-solving with suppliers.
Challenges in Procuring from Japan
While there are significant advantages, procuring from Japanese suppliers also presents certain challenges.
Higher Costs
Japanese manufacturing often comes with higher price points due to the advanced technology and high labor standards involved. Companies must balance the cost against the quality and reliability benefits.
Cultural and Language Barriers
Differences in business practices, language, and cultural norms can pose challenges in communication and negotiations. Understanding and bridging these gaps is essential for successful procurement.
Lead Times and Logistics
The geographic distance between Japan and other regions can result in longer lead times and complex logistics. Efficient supply chain management is crucial to mitigate these issues.
Effective Supplier Negotiation Techniques
Negotiating with Japanese suppliers requires a nuanced approach that respects their business culture and practices.
Building Trust and Relationships
Trust is the foundation of Japanese business relationships. Invest time in building rapport and demonstrating commitment to a long-term partnership.
Understanding Cultural Nuances
Familiarize yourself with Japanese business etiquette. Showing respect and understanding of their cultural practices fosters smoother negotiations.
Clear Communication
Ensure all specifications, expectations, and terms are clearly communicated. Use precise language and, if necessary, engage bilingual staff or translators to avoid misunderstandings.
Win-Win Mindset
Approach negotiations with a collaborative mindset. Aim for agreements that benefit both parties, fostering mutual respect and ongoing cooperation.
Market Conditions Impacting Procurement
The global manufacturing landscape is dynamic, influenced by various economic and geopolitical factors that affect procurement strategies.
Supply Chain Disruptions
Events such as natural disasters, pandemics, or geopolitical tensions can disrupt supply chains. Diversifying suppliers and having contingency plans are essential to mitigate risks.
Fluctuating Material Costs
The prices of raw materials like stainless steel can fluctuate due to market demand and supply dynamics. Monitoring market trends and negotiating flexible contracts can help manage costs effectively.
Technological Advancements
Rapid advancements in manufacturing technologies can shift supplier capabilities. Staying abreast of these changes ensures that procurement strategies align with the latest industry standards.
Best Practices in Procuring from Japanese Manufacturers
Adopting best practices can enhance the efficiency and success of procurement processes when dealing with Japanese suppliers.
Conduct Thorough Supplier Assessments
Evaluate potential suppliers based on their technical capabilities, quality standards, financial stability, and previous performance. Site visits and audits can provide deeper insights into their operations.
Establish Clear Contracts
Draft comprehensive contracts that outline specifications, delivery schedules, quality standards, and payment terms. Clear contracts help prevent misunderstandings and ensure accountability.
Foster Open Communication
Maintain regular and transparent communication with suppliers. Use collaborative tools and regular meetings to address issues promptly and keep projects on track.
Implement Robust Quality Control Measures
Work closely with suppliers to establish stringent quality control protocols. Regular inspections and testing ensure that components meet the required standards before shipment.
Leverage Technology for Supply Chain Management
Utilize advanced supply chain management software to track orders, monitor inventory levels, and manage logistics. Technology can enhance visibility and efficiency across the procurement process.
Case Study: Successful Procurement from a Japanese Supplier
To illustrate the application of these principles, consider the case of a global automotive manufacturer seeking thin-walled stainless steel tubular components for its new car models.
Identifying the Right Supplier
The company conducted a thorough supplier assessment, evaluating several Japanese manufacturers based on their expertise, production capabilities, and quality control processes. They selected a supplier renowned for its precision engineering and reliability.
Establishing the Partnership
Both parties engaged in detailed negotiations, emphasizing a long-term partnership. Clear communication channels were established, and a comprehensive contract was signed outlining all specifications and expectations.
Implementing Quality Controls
Joint quality control measures were implemented, including regular inspections and testing. This collaboration ensured that the components consistently met the high standards required for the automotive applications.
Optimizing Logistics
To address lead time challenges, the company worked with the supplier to streamline logistics. They adopted a Just-In-Time (JIT) inventory system, reducing inventory costs and ensuring timely delivery of components.
Results
The collaboration resulted in high-quality components that enhanced the performance and reliability of the new car models. The successful partnership also paved the way for future collaborations and mutual growth.
Strategies for Enhancing Procurement Efficiency
Improving procurement efficiency is vital for maximizing benefits when working with Japanese suppliers. The following strategies can be employed to achieve this goal.
Streamline the Procurement Process
Simplify procurement workflows to reduce delays and enhance efficiency. Implement standardized procedures for sourcing, ordering, and payment to ensure consistency and speed.
Invest in Supplier Relationship Management
Use Supplier Relationship Management (SRM) tools to manage interactions and track performance. SRM fosters better collaboration and helps identify areas for improvement.
Optimize Inventory Management
Maintain optimal inventory levels to balance supply and demand. Techniques like demand forecasting and safety stock calculations can prevent overstocking and stockouts.
Enhance Data Analytics
Leverage data analytics to gain insights into procurement patterns, supplier performance, and market trends. Data-driven decisions lead to more effective procurement strategies.
Future Trends in Japanese Manufacturing of Thin-Walled Stainless Steel Tubular Components
The Japanese manufacturing sector continues to evolve, driven by technological advancements and changing market demands. Several trends are shaping the future of thin-walled stainless steel tubular component production.
Adoption of Industry 4.0
Industry 4.0 technologies, including the Internet of Things (IoT), artificial intelligence (AI), and robotics, are being integrated into manufacturing processes. These technologies enhance precision, improve efficiency, and enable predictive maintenance.
Sustainability and Green Manufacturing
There is a growing emphasis on sustainable manufacturing practices. Japanese manufacturers are adopting eco-friendly processes, reducing waste, and improving energy efficiency to meet environmental standards and consumer demands.
Customization and Flexibility
Manufacturers are increasingly offering customized solutions to meet specific client needs. Flexible production systems allow for quick adjustments to design and production processes, catering to diverse requirements.
Advanced Materials and Innovations
Research into new materials and innovative manufacturing techniques continues to drive the industry forward. These advancements enable the production of more durable, lightweight, and high-performance components.
Conclusion
Japanese mastery in the manufacturing of thin-walled stainless steel tubular components sets a benchmark for precision and quality. Despite challenges such as higher costs and cultural barriers, the advantages of procuring from Japanese suppliers—unmatched precision, reliability, and innovative solutions—make it a compelling choice for global manufacturers. By adopting effective procurement strategies, building strong supplier relationships, and staying abreast of market trends, companies can harness the benefits of Japanese manufacturing excellence. As the industry evolves with new technologies and sustainable practices, the partnership between procurers and Japanese manufacturers will continue to drive innovation and success in various sectors.
資料ダウンロード
QCD調達購買管理クラウド「newji」は、調達購買部門で必要なQCD管理全てを備えた、現場特化型兼クラウド型の今世紀最高の購買管理システムとなります。
ユーザー登録
調達購買業務の効率化だけでなく、システムを導入することで、コスト削減や製品・資材のステータス可視化のほか、属人化していた購買情報の共有化による内部不正防止や統制にも役立ちます。
NEWJI DX
製造業に特化したデジタルトランスフォーメーション(DX)の実現を目指す請負開発型のコンサルティングサービスです。AI、iPaaS、および先端の技術を駆使して、製造プロセスの効率化、業務効率化、チームワーク強化、コスト削減、品質向上を実現します。このサービスは、製造業の課題を深く理解し、それに対する最適なデジタルソリューションを提供することで、企業が持続的な成長とイノベーションを達成できるようサポートします。
オンライン講座
製造業、主に購買・調達部門にお勤めの方々に向けた情報を配信しております。
新任の方やベテランの方、管理職を対象とした幅広いコンテンツをご用意しております。
お問い合わせ
コストダウンが利益に直結する術だと理解していても、なかなか前に進めることができない状況。そんな時は、newjiのコストダウン自動化機能で大きく利益貢献しよう!
(Β版非公開)