- お役立ち記事
- Exploring the Innovation: The Role of Three-Dimensional Wiring Molded Components in Japanese Manufacturing
Exploring the Innovation: The Role of Three-Dimensional Wiring Molded Components in Japanese Manufacturing
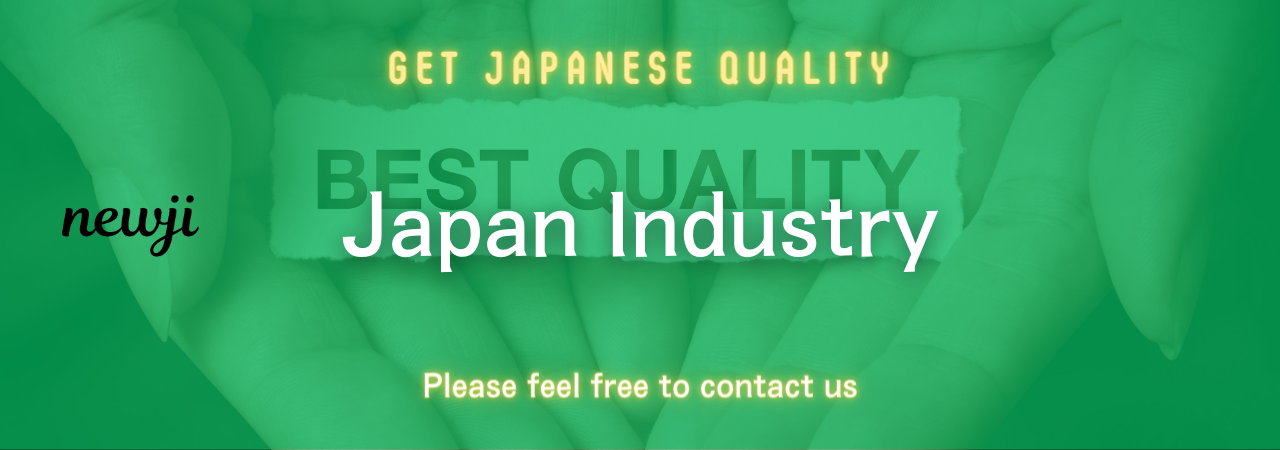
目次
Introduction to Three-Dimensional Wiring Molded Components
Three-dimensional (3D) wiring molded components represent a significant advancement in manufacturing technology.
These components integrate wiring systems directly into molded parts, enhancing the functionality and efficiency of electronic devices.
In Japanese manufacturing, the adoption of 3D wiring molded components has been pivotal in maintaining global competitiveness.
This innovation streamlines the production process, reduces material usage, and improves the overall quality of electronic products.
Understanding the role of 3D wiring molded components is essential for procurement and purchasing professionals aiming to leverage Japanese manufacturing expertise.
Importance in Japanese Manufacturing
Japanese manufacturing has long been synonymous with precision, quality, and innovation.
The integration of 3D wiring molded components exemplifies Japan’s commitment to advancing manufacturing technologies.
These components are crucial in various industries, including automotive, electronics, and consumer goods.
By embedding wiring into molded parts, manufacturers can achieve more compact and lightweight designs.
This innovation not only enhances product performance but also contributes to sustainability by minimizing waste and reducing material consumption.
Japanese suppliers excel in producing high-quality 3D wiring molded components, making them valuable partners in the global supply chain.
Advantages of 3D Wiring Molded Components
Enhanced Product Design and Functionality
3D wiring molded components allow for more intricate and compact designs.
They enable the integration of electrical systems within the structural components of a product.
This integration leads to enhanced functionality and aesthetics, as wiring is concealed within the molded parts.
Consumers benefit from sleeker, more reliable products with fewer visible wiring issues.
Improved Manufacturing Efficiency
Incorporating wiring into molded components streamlines the production process.
It reduces the need for separate wiring assemblies, which can be time-consuming and prone to errors.
This consolidation leads to faster production times and lower labor costs.
Additionally, it simplifies the assembly process, enhancing overall manufacturing efficiency.
Cost Savings and Material Reduction
By embedding wiring within molded components, manufacturers can reduce the amount of material used.
This reduction not only lowers production costs but also contributes to environmental sustainability.
Fewer materials mean less waste and lower transportation costs, benefiting both manufacturers and consumers.
Quality and Reliability
3D wiring molded components are known for their durability and reliability.
The encapsulation of wiring within molded parts protects it from environmental factors such as moisture, dust, and mechanical stress.
This protection results in longer-lasting products with fewer failures, enhancing brand reputation and customer satisfaction.
Disadvantages and Challenges
Initial Investment and Setup
Implementing 3D wiring molded components requires significant initial investment in specialized equipment and training.
Manufacturers must invest in advanced molding technologies and skilled personnel to handle the complex integration processes.
This upfront cost can be a barrier for smaller companies or those new to this technology.
Design Complexity
Designing products with embedded wiring adds a layer of complexity to the development process.
Engineers must carefully plan the placement and routing of wires within molded parts to ensure functionality and maintain structural integrity.
This complexity can extend development timelines and require more rigorous testing and quality control measures.
Repair and Maintenance Challenges
Once wiring is embedded within molded components, accessing and repairing these wires becomes more challenging.
In the event of a failure, components may need to be replaced entirely, increasing maintenance costs and downtime.
This limitation necessitates robust quality assurance processes to minimize the occurrence of defects.
Supply Chain Considerations
Relying on specialized 3D wiring molded components may limit supplier options.
Manufacturers must establish strong relationships with reliable suppliers capable of producing high-quality components consistently.
Any disruptions in the supply chain can have significant impacts on production timelines and product quality.
Procurement and Purchasing Perspectives
Supplier Selection
Selecting the right supplier for 3D wiring molded components is critical.
Procurement professionals must evaluate potential suppliers based on their technical capabilities, quality standards, and reliability.
Japanese suppliers are often preferred for their expertise and commitment to excellence in manufacturing.
Conducting thorough due diligence and site visits can help ensure that suppliers meet the required specifications and standards.
Negotiation Techniques with Japanese Suppliers
Effective negotiation with Japanese suppliers involves understanding and respecting their business culture.
Building trust and fostering long-term relationships are essential for successful negotiations.
Key techniques include:
- Clear and transparent communication to avoid misunderstandings.
- Demonstrating a willingness to collaborate and share information.
- Emphasizing mutual benefits and long-term partnerships rather than short-term gains.
- Being patient and accommodating, as Japanese business negotiations may take longer to reach consensus.
These approaches help in achieving favorable terms and establishing a strong working relationship.
Market Conditions and Trends
The market for 3D wiring molded components is evolving rapidly, driven by advancements in technology and changing consumer demands.
Key trends impacting this market include:
Increasing Demand for Compact and Lightweight Devices
As consumer electronics become more advanced, there is a growing demand for smaller and lighter devices.
3D wiring molded components address this need by integrating wiring systems within compact structures, enabling sleek and portable designs.
Advancements in Manufacturing Technologies
Technological innovations, such as automation and artificial intelligence, are enhancing the production capabilities of 3D wiring molded components.
These advancements lead to higher precision, reduced production times, and improved quality, making Japanese manufacturers leaders in this field.
Emphasis on Sustainability
Sustainability is becoming a critical factor in manufacturing decisions.
3D wiring molded components contribute to sustainability by reducing material usage and waste.
Manufacturers are increasingly adopting eco-friendly practices and seeking suppliers who prioritize environmental responsibility.
Global Supply Chain Dynamics
Global supply chain disruptions, such as those caused by the COVID-19 pandemic, have highlighted the importance of reliable and flexible supply chains.
Japanese suppliers are known for their resilience and ability to maintain production standards under challenging conditions, making them valuable partners in a volatile market.
Best Practices in Procurement and Purchasing
Building Strong Supplier Relationships
Establishing and maintaining strong relationships with suppliers is fundamental to successful procurement.
This involves regular communication, mutual respect, and collaborative problem-solving.
Building trust with Japanese suppliers can lead to better terms, priority in supply shortages, and access to the latest technological advancements.
Quality Control and Assurance
Implementing rigorous quality control processes is essential when procuring 3D wiring molded components.
This includes conducting regular inspections, audits, and testing to ensure components meet specified standards.
Working closely with suppliers to address quality issues promptly can prevent defects and maintain product reliability.
Leveraging Technological Innovations
Staying abreast of the latest technological trends can provide a competitive edge.
Integrating advanced manufacturing technologies, such as automation and digitalization, can enhance efficiency and quality.
Collaborating with suppliers who invest in research and development can lead to innovative solutions and improved component performance.
Strategic Sourcing
Adopting a strategic sourcing approach involves evaluating and selecting suppliers based on long-term value rather than just cost.
This includes assessing suppliers’ capabilities, reliability, and alignment with the company’s strategic goals.
Strategic sourcing helps in building a resilient supply chain and ensures a steady supply of high-quality components.
Risk Management
Identifying and mitigating risks associated with procurement is crucial for maintaining supply continuity.
This includes risks related to supplier reliability, geopolitical factors, and market volatility.
Developing contingency plans, diversifying the supplier base, and maintaining safety stock are effective strategies for managing procurement risks.
Conclusion
Three-dimensional wiring molded components are revolutionizing Japanese manufacturing by enhancing product design, improving manufacturing efficiency, and contributing to sustainability.
For procurement and purchasing professionals, understanding the advantages and challenges associated with these components is essential for making informed sourcing decisions.
Building strong relationships with Japanese suppliers, adopting best practices in quality control and strategic sourcing, and staying informed about market trends are key to leveraging the benefits of 3D wiring molded components.
As manufacturing technology continues to advance, the role of 3D wiring molded components will likely expand, offering new opportunities for innovation and growth in the global market.
資料ダウンロード
QCD調達購買管理クラウド「newji」は、調達購買部門で必要なQCD管理全てを備えた、現場特化型兼クラウド型の今世紀最高の購買管理システムとなります。
ユーザー登録
調達購買業務の効率化だけでなく、システムを導入することで、コスト削減や製品・資材のステータス可視化のほか、属人化していた購買情報の共有化による内部不正防止や統制にも役立ちます。
NEWJI DX
製造業に特化したデジタルトランスフォーメーション(DX)の実現を目指す請負開発型のコンサルティングサービスです。AI、iPaaS、および先端の技術を駆使して、製造プロセスの効率化、業務効率化、チームワーク強化、コスト削減、品質向上を実現します。このサービスは、製造業の課題を深く理解し、それに対する最適なデジタルソリューションを提供することで、企業が持続的な成長とイノベーションを達成できるようサポートします。
オンライン講座
製造業、主に購買・調達部門にお勤めの方々に向けた情報を配信しております。
新任の方やベテランの方、管理職を対象とした幅広いコンテンツをご用意しております。
お問い合わせ
コストダウンが利益に直結する術だと理解していても、なかなか前に進めることができない状況。そんな時は、newjiのコストダウン自動化機能で大きく利益貢献しよう!
(Β版非公開)