- お役立ち記事
- Revolutionizing Japanese Manufacturing: The Rise of the Painting Robot
Revolutionizing Japanese Manufacturing: The Rise of the Painting Robot
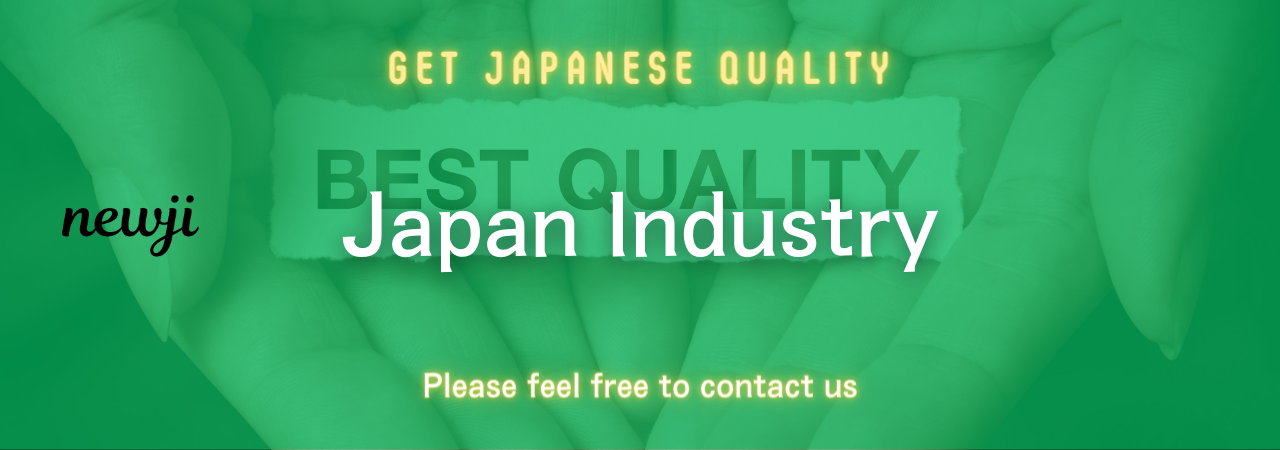
目次
Introduction to Painting Robots in Japanese Manufacturing
The manufacturing landscape in Japan has undergone significant transformations over the past few decades. Central to this evolution is the integration of automation technologies, particularly painting robots. These sophisticated machines are redefining production processes, enhancing quality, and boosting efficiency across various industries.
The Role of Painting Robots in Modern Manufacturing
Painting robots are automated systems designed to apply paint and coatings with precision and consistency. In Japanese manufacturing, their adoption has been pivotal in achieving high standards of product finish and durability. These robots are employed in automotive, electronics, and consumer goods sectors, where aesthetic and protective coatings are critical.
Enhancing Quality and Consistency
One of the primary advantages of painting robots is their ability to maintain consistent quality across large production volumes. Unlike manual painting, which can vary based on the technician’s skill and fatigue levels, robots deliver uniform coats, reducing defects and rework rates.
Increasing Production Efficiency
Painting robots operate at higher speeds compared to human workers, significantly increasing production throughput. Their ability to work continuously without breaks ensures that manufacturing schedules are met more reliably, enhancing overall operational efficiency.
Advantages of Integrating Painting Robots
Adopting painting robots offers numerous benefits to manufacturers, particularly those sourcing from Japan.
Cost Reduction
While the initial investment in painting robots can be substantial, the long-term cost savings are noteworthy. Reduced labor costs, minimized waste from overspray, and lower defect rates contribute to overall cost efficiency.
Improved Workplace Safety
Painting processes often involve hazardous chemicals and fumes. Robots mitigate safety risks by handling these materials, thereby reducing workplace injuries and ensuring compliance with safety regulations.
Flexibility and Scalability
Modern painting robots are highly programmable, allowing manufacturers to switch between different products and paint types with minimal downtime. This flexibility is essential for companies looking to diversify their product lines without significant retooling costs.
Challenges and Disadvantages
Despite their numerous benefits, integrating painting robots presents certain challenges that manufacturers must address.
High Initial Investment
The cost of purchasing and installing painting robots can be a barrier for smaller manufacturers. Additionally, there are ongoing costs related to maintenance, software updates, and potential downtime during integration.
Technical Expertise Requirement
Operating and maintaining painting robots requires specialized skills. Manufacturers may need to invest in training for their workforce or hire skilled technicians, adding to the overall cost and complexity.
Adaptation to Existing Systems
Integrating robots into existing production lines can be challenging. Compatibility issues with current machinery, layout modifications, and workflow adjustments are often necessary, which can disrupt operations during the transition period.
Supplier Negotiation Techniques for Painting Robots
Effective negotiation with Japanese suppliers is crucial to obtaining the best terms and ensuring successful integration of painting robots.
Understanding Supplier Capabilities
Before entering negotiations, it is essential to have a comprehensive understanding of the supplier’s product offerings, technological capabilities, and service support. This knowledge enables informed decision-making and the ability to identify areas for value addition.
Leveraging Long-Term Relationships
Japanese business culture places a high value on long-term relationships. Building trust with suppliers can lead to more favorable terms, priority support, and collaborative problem-solving approaches.
Emphasizing Quality and Reliability
When negotiating, highlighting the importance of quality and reliability can help ensure that the supplier prioritizes these aspects in their offerings. This focus aligns with Japanese manufacturing standards and can lead to better product outcomes.
Negotiating Service and Support
Securing favorable terms for ongoing service and support is critical. This includes maintenance contracts, software updates, and training programs. Clear agreements on these aspects help prevent future operational disruptions.
Market Conditions Influencing the Adoption of Painting Robots
Several market factors drive the adoption of painting robots in Japanese manufacturing.
Demand for High-Quality Products
As consumers increasingly demand high-quality and aesthetically pleasing products, manufacturers must adopt technologies that can consistently meet these expectations. Painting robots provide the precision and reliability required to satisfy these market demands.
Labor Shortages
Japan faces challenges related to an aging workforce and labor shortages in manufacturing sectors. Automation, including the use of painting robots, helps mitigate these issues by reducing dependence on manual labor.
Competitive Pressure
Global competition necessitates continuous improvement in manufacturing processes to maintain market position. Painting robots offer a way to enhance production capabilities, reduce costs, and improve product quality, thereby strengthening competitiveness.
Technological Advancements
Ongoing advancements in robotics, artificial intelligence, and machine learning have made painting robots more capable and accessible. These technologies enhance the functionality and adaptability of robots, making them more attractive to manufacturers.
Best Practices for Procuring Painting Robots from Japan
To maximize the benefits of procuring painting robots from Japanese suppliers, manufacturers should adhere to certain best practices.
Comprehensive Needs Assessment
Before purchasing, conduct a thorough assessment of production needs, including volume requirements, product specifications, and integration capabilities. This ensures that the chosen robot aligns with operational goals and technical requirements.
Evaluating Supplier Reputation
Choose suppliers with a proven track record of reliability, quality, and innovation. Researching supplier history, customer reviews, and case studies can provide insights into their performance and suitability.
Collaborative Planning and Implementation
Work closely with suppliers during the planning and implementation phases. Collaborative efforts can facilitate smooth integration, address potential challenges proactively, and ensure that the robot meets all specified requirements.
Investing in Training and Support
Ensure that adequate training is provided for staff who will operate and maintain the painting robots. Additionally, establish a robust support system with the supplier to address any technical issues promptly.
Continuous Monitoring and Improvement
After implementation, continuously monitor the performance of painting robots. Use data analytics to identify areas for improvement, optimize processes, and ensure that the robots contribute effectively to production goals.
Impact on Supply Chain Management
Integrating painting robots affects various aspects of supply chain management, particularly in procurement and purchasing.
Streamlined Procurement Processes
Automation in painting processes leads to more predictable and consistent supply chain demands. This allows for better planning and scheduling, reducing inventory holding costs and minimizing supply chain disruptions.
Enhanced Supplier Relationships
Collaborating with suppliers on robotic integration fosters stronger partnerships. Shared goals and mutual dependence on technology advancements can lead to more strategic and long-term supplier relationships.
Improved Inventory Management
With increased efficiency and reduced variability in production, inventory management becomes more streamlined. Manufacturers can adopt just-in-time inventory practices, reducing storage costs and improving cash flow.
Case Studies: Success Stories in Japanese Manufacturing
Examining real-world examples provides valuable insights into the successful integration of painting robots.
Automotive Industry Transformation
Japanese automotive manufacturers have been pioneers in adopting painting robots. These robots have enabled consistent paint finishes, reduced production times, and minimized waste. As a result, companies like Toyota and Honda have maintained high-quality standards and competitive pricing.
Electronics Manufacturing Enhancement
Electronics manufacturers in Japan have utilized painting robots to apply precise coatings on components and devices. This precision is crucial for ensuring product functionality and longevity, leading to increased customer satisfaction and brand reputation.
Consumer Goods Optimization
Manufacturers of household appliances and other consumer goods have benefited from painting robots by achieving uniform finishes and reducing manual labor costs. This has allowed them to scale production and meet growing market demands efficiently.
Future Trends in Painting Robot Technology
The landscape of painting robots continues to evolve, driven by technological advancements and changing market needs.
Integration with Artificial Intelligence
Artificial intelligence is enhancing the capabilities of painting robots, enabling them to adapt to varying production conditions, optimize paint usage, and predict maintenance needs. This integration leads to smarter and more autonomous robotic systems.
Collaborative Robots (Cobots)
The development of collaborative robots that can work alongside human workers is gaining traction. These cobots enhance flexibility in production lines by handling tasks that require precision while allowing humans to focus on more complex activities.
Sustainability and Eco-Friendly Practices
There is a growing emphasis on sustainable manufacturing practices. Painting robots are being designed to reduce environmental impact by minimizing waste, optimizing energy consumption, and utilizing eco-friendly paints and coatings.
Enhanced Customization Capabilities
Future painting robots will offer greater customization options, allowing manufacturers to produce more personalized products without sacrificing efficiency. This capability aligns with the increasing consumer demand for customized goods.
Strategies for Maximizing ROI on Painting Robots
Ensuring a strong return on investment (ROI) from painting robots involves strategic planning and execution.
Optimizing Utilization
Maximize the usage of painting robots by integrating them into high-demand production processes. This ensures that the investment generates continuous value and justifies the initial costs.
Regular Maintenance and Upgrades
Implement a proactive maintenance schedule to prevent downtime and extend the lifespan of painting robots. Additionally, stay updated with technological advancements and upgrade systems as necessary to maintain competitiveness.
Data-Driven Decision Making
Leverage data collected from painting robots to make informed decisions about production processes, quality control, and supply chain management. Data analytics can identify inefficiencies and areas for improvement, enhancing overall productivity.
Training and Workforce Development
Invest in training programs to develop a skilled workforce capable of operating and maintaining advanced robotic systems. A knowledgeable team can ensure optimal performance and quickly address any issues that arise.
Conclusion: The Future of Japanese Manufacturing with Painting Robots
Painting robots are at the forefront of the technological revolution in Japanese manufacturing. Their ability to enhance quality, increase efficiency, and reduce costs makes them indispensable in today’s competitive market. While challenges such as high initial investment and the need for technical expertise exist, the long-term benefits far outweigh the drawbacks.
By adopting best practices in procurement, building strong supplier relationships, and staying abreast of technological advancements, manufacturers can fully leverage the potential of painting robots. As the industry continues to evolve, painting robots will play a critical role in driving innovation, ensuring sustainability, and maintaining Japan’s position as a leader in global manufacturing.
資料ダウンロード
QCD調達購買管理クラウド「newji」は、調達購買部門で必要なQCD管理全てを備えた、現場特化型兼クラウド型の今世紀最高の購買管理システムとなります。
ユーザー登録
調達購買業務の効率化だけでなく、システムを導入することで、コスト削減や製品・資材のステータス可視化のほか、属人化していた購買情報の共有化による内部不正防止や統制にも役立ちます。
NEWJI DX
製造業に特化したデジタルトランスフォーメーション(DX)の実現を目指す請負開発型のコンサルティングサービスです。AI、iPaaS、および先端の技術を駆使して、製造プロセスの効率化、業務効率化、チームワーク強化、コスト削減、品質向上を実現します。このサービスは、製造業の課題を深く理解し、それに対する最適なデジタルソリューションを提供することで、企業が持続的な成長とイノベーションを達成できるようサポートします。
オンライン講座
製造業、主に購買・調達部門にお勤めの方々に向けた情報を配信しております。
新任の方やベテランの方、管理職を対象とした幅広いコンテンツをご用意しております。
お問い合わせ
コストダウンが利益に直結する術だと理解していても、なかなか前に進めることができない状況。そんな時は、newjiのコストダウン自動化機能で大きく利益貢献しよう!
(Β版非公開)