- お役立ち記事
- Example of standardization of new supplier selection process in manufacturing industry
Example of standardization of new supplier selection process in manufacturing industry
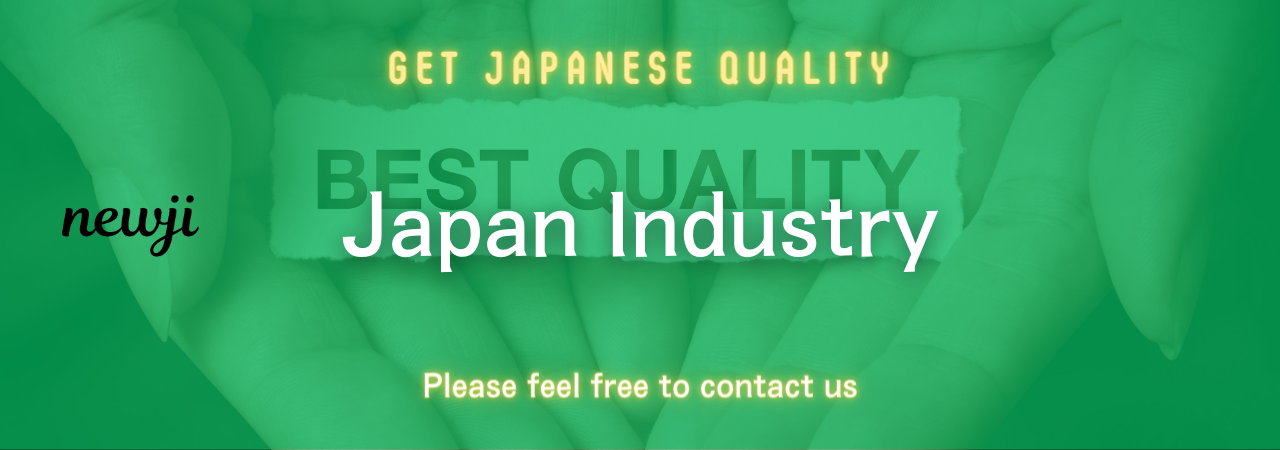
目次
Introduction to Supplier Selection in Manufacturing
In the manufacturing industry, having the right suppliers can make a significant difference in the production process and overall business success.
The selection of suppliers involves evaluating and choosing the best partners who can provide quality materials or components at the right cost and within the specified timelines.
A standardized supplier selection process helps companies maintain consistency, improve efficiency, and ensure that high-quality standards are met.
To achieve these goals, it’s essential to establish clear criteria and structured procedures for evaluating potential suppliers.
By implementing a standardized process, businesses can mitigate risks, enhance supplier relationships, and achieve a competitive edge in the market.
Importance of Standardizing Supplier Selection
A standardized supplier selection process is crucial for many reasons.
First and foremost, it helps ensure that the quality of materials or products received meets the company’s standards, which is vital for producing high-quality end products.
Furthermore, it reduces the risk of supply chain disruptions by carefully assessing suppliers’ reliability and capabilities.
This not only helps in maintaining production schedules but also in avoiding costly delays.
Another benefit of a standardized selection process is cost efficiency.
By evaluating suppliers based on consistent criteria, companies can identify cost-saving opportunities, negotiate better terms, and make informed decisions that positively impact their bottom line.
Additionally, a well-defined process reduces subjectivity and potential biases in supplier selection, promoting fairness and transparency.
This is particularly important when dealing with multiple suppliers, as it ensures a level playing field and helps in building trust and long-term partnerships.
Steps in Standardizing Supplier Selection
To develop a standardized supplier selection process, manufacturing companies should follow a series of steps:
1. Define Selection Criteria
The first step is to establish specific criteria for supplier selection.
These should align with the company’s strategic goals and operational needs.
Common criteria include quality, cost, delivery performance, financial stability, and ethical standards.
It’s important to weigh each criterion based on its importance to the business.
2. Develop a Supplier Evaluation Framework
Once the criteria are defined, a supplier evaluation framework should be developed.
This framework serves as a structured tool for assessing and comparing suppliers.
It typically includes scoring or rating systems that objectively measure a supplier’s capabilities and performance against each criteria.
3. Conduct Market Research
Conducting thorough market research is essential to identify potential suppliers that meet the established criteria.
This involves gathering information on suppliers’ reputation, experience, and capabilities through various sources such as industry reports, trade shows, and online databases.
4. Request for Proposal (RFP) Process
After identifying potential suppliers, an RFP process should be initiated.
The RFP outlines the company’s requirements and invites suppliers to submit their proposals.
This process allows for a direct comparison of suppliers based on how well they meet the specified criteria.
5. Evaluate and Select Suppliers
With the proposals in hand, the evaluation process begins.
Using the established framework, suppliers are assessed and scored based on their proposals and any additional information obtained during the process.
The top-performing suppliers are then selected for negotiations.
6. Negotiate Terms and Agreements
Negotiating favorable terms and agreements is a critical step to ensure mutual benefits for both the company and the supplier.
This includes discussions on pricing, delivery schedules, payment terms, and guarantees of quality and service.
7. Monitor and Review Supplier Performance
Even after suppliers are selected, the process doesn’t end.
Regular performance monitoring and reviews are necessary to ensure suppliers continue to meet expectations.
Feedback mechanisms and performance metrics can help address any issues promptly and maintain strong supplier relationships.
Challenges in Standardizing Supplier Selection
While a standardized selection process offers numerous benefits, there are challenges in implementation.
One of the main challenges is resistance to change.
Companies may face pushback from staff accustomed to informal or historical selection methods.
Training and change management strategies can help overcome this resistance.
Another challenge is the initial time and resource investment required to develop and implement a comprehensive process.
However, the long-term benefits in terms of efficiency, quality, and cost savings often outweigh these initial costs.
Adapting the process to a rapidly changing market environment can also be challenging.
Companies need to remain flexible and continuously update their criteria and processes to reflect industry trends and technological advancements.
Conclusion
Standardizing the supplier selection process is essential for manufacturing companies aiming to maintain high quality, efficiency, and competitiveness.
By establishing clear criteria and a structured approach, businesses can reduce risks, lower costs, and improve supplier relationships.
While there are challenges in implementing a standardized process, the long-term benefits greatly contribute to the company’s success and sustainability in the industry.
Through careful planning and execution, companies can ensure that their supplier selection process aligns with their strategic goals and operational requirements, paving the way for a resilient and efficient supply chain.
資料ダウンロード
QCD調達購買管理クラウド「newji」は、調達購買部門で必要なQCD管理全てを備えた、現場特化型兼クラウド型の今世紀最高の購買管理システムとなります。
ユーザー登録
調達購買業務の効率化だけでなく、システムを導入することで、コスト削減や製品・資材のステータス可視化のほか、属人化していた購買情報の共有化による内部不正防止や統制にも役立ちます。
NEWJI DX
製造業に特化したデジタルトランスフォーメーション(DX)の実現を目指す請負開発型のコンサルティングサービスです。AI、iPaaS、および先端の技術を駆使して、製造プロセスの効率化、業務効率化、チームワーク強化、コスト削減、品質向上を実現します。このサービスは、製造業の課題を深く理解し、それに対する最適なデジタルソリューションを提供することで、企業が持続的な成長とイノベーションを達成できるようサポートします。
オンライン講座
製造業、主に購買・調達部門にお勤めの方々に向けた情報を配信しております。
新任の方やベテランの方、管理職を対象とした幅広いコンテンツをご用意しております。
お問い合わせ
コストダウンが利益に直結する術だと理解していても、なかなか前に進めることができない状況。そんな時は、newjiのコストダウン自動化機能で大きく利益貢献しよう!
(Β版非公開)