- お役立ち記事
- Price fluctuation risk management methods in raw material procurement that purchasing personnel should be aware of
Price fluctuation risk management methods in raw material procurement that purchasing personnel should be aware of
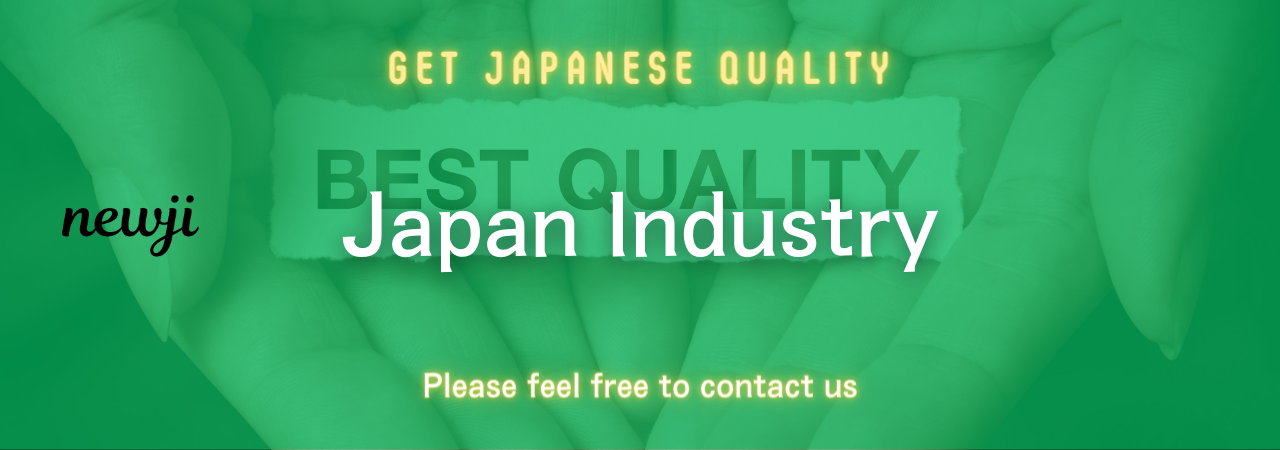
目次
Understanding Price Fluctuation Risk in Raw Material Procurement
Price fluctuation in raw material procurement is a common challenge faced by purchasing personnel.
Raw materials are fundamental components for manufacturing and production, and their costs can greatly influence a company’s bottom line.
Fluctuating prices can impact production costs, profitability, and ultimately, the end prices of products.
Understanding the nature of these fluctuations is crucial for implementing effective risk management strategies.
Price fluctuations occur due to various factors, including supply and demand dynamics, geopolitical events, natural disasters, and changes in currency exchange rates.
These variables can create volatile market conditions, making it difficult to predict future prices accurately.
Purchasing managers must remain vigilant and adaptable to navigate these shifting landscapes efficiently.
Identifying Common Sources of Price Fluctuation
There are several primary sources of price volatility in the raw materials market.
First, supply and demand play a significant role.
When the demand for certain raw materials increases, prices often rise.
Conversely, an oversupply can lead to decreased prices.
Understanding the current supply and demand trends can help purchasing personnel anticipate potential price changes.
Weather conditions and natural disasters are also influential factors.
Events such as hurricanes, droughts, or floods can disrupt supply chains, leading to scarcity and increased costs.
Geopolitical tensions, including trade disputes and political instability, can affect the availability and cost of raw materials as well.
Purchasing managers must monitor global political climates and consider developing contingency plans.
Finally, currency exchange rates can lead to price changes, especially for international procurement.
Fluctuations in currency value can increase or decrease the costs of imported raw materials, depending on the country’s exchange rate policies.
Being aware of these changes is essential for effective financial forecasting and budgeting.
Implementing Effective Risk Management Strategies
To mitigate the impact of price fluctuations, purchasing personnel should implement robust risk management strategies.
One effective approach is developing long-term contracts with suppliers.
These contracts often include fixed pricing, which can provide stability and predictability over a specified period.
Fixed-price agreements can shield companies from sudden market changes but may require renegotiation if market conditions change considerably.
Diversifying suppliers is another key strategy.
By not relying on a single supplier, companies can reduce the risk associated with price fluctuations.
Sourcing raw materials from multiple suppliers in different geographic regions can provide more flexibility and negotiating power.
Furthermore, this approach can help mitigate risks related to regional disruptions, such as natural disasters or political instability.
Additionally, purchasing personnel should consider using financial instruments like hedging to manage price risk.
Hedging involves using futures contracts or options to lock in prices for raw materials.
While these tools can be complex, they offer a way to secure pricing and protect against unforeseen market changes.
Building Strong Supplier Relationships
Developing strong relationships with suppliers can provide significant advantages in managing price fluctuations.
Open communication and mutual trust enable better negotiation of terms and conditions.
When suppliers understand a company’s needs and concerns, they are more likely to offer favorable terms, such as flexible pricing or priority access to materials in times of shortage.
Regularly assessing supplier performance and conducting audits can ensure they meet the required quality standards and delivery timelines.
Engaging with suppliers through collaborative initiatives, such as joint cost reduction projects, can also lead to cost savings and improved supply chain efficiency.
Utilizing Technology for Better Forecasting
Technological advancements provide valuable tools for predicting and managing price fluctuations.
Data analytics and artificial intelligence can analyze historical data and current market trends to forecast future pricing scenarios.
These predictions empower purchasing personnel to make informed decisions regarding procurement strategies.
Implementing supply chain management software can help track real-time price changes, inventory levels, and supplier performance.
Such systems enhance visibility across the supply chain, allowing for quick responses to market changes.
They also facilitate scenario planning, enabling companies to prepare for various pricing outcomes.
Training and Developing Procurement Teams
Investing in the skill development of procurement teams is crucial for effective price fluctuation risk management.
Training programs should focus on market analysis, negotiation skills, and the use of financial instruments like hedging.
Equipping teams with knowledge and skills empowers them to make strategic decisions and implement cost-saving initiatives.
Furthermore, fostering a culture of continuous learning ensures that teams remain updated on industry trends and best practices.
Encouraging collaboration and knowledge sharing within the procurement department can lead to innovative risk management solutions.
Conclusion: Navigating Price Fluctuation with Confidence
Managing price fluctuations in raw material procurement is a multifaceted challenge requiring a strategic approach.
By understanding the sources of price volatility and implementing proactive risk management strategies, purchasing personnel can safeguard against market unpredictability.
Building strong supplier relationships, utilizing technology, and investing in team development are essential components of a robust procurement strategy.
These actions not only minimize financial risks but also contribute to the overall stability and success of a company.
By remaining adaptable and informed, purchasing personnel can navigate the complexities of global markets with confidence.
Ultimately, effective price fluctuation risk management not only protects a company’s profitability but also enhances its competitive advantage in the ever-evolving business landscape.
資料ダウンロード
QCD調達購買管理クラウド「newji」は、調達購買部門で必要なQCD管理全てを備えた、現場特化型兼クラウド型の今世紀最高の購買管理システムとなります。
ユーザー登録
調達購買業務の効率化だけでなく、システムを導入することで、コスト削減や製品・資材のステータス可視化のほか、属人化していた購買情報の共有化による内部不正防止や統制にも役立ちます。
NEWJI DX
製造業に特化したデジタルトランスフォーメーション(DX)の実現を目指す請負開発型のコンサルティングサービスです。AI、iPaaS、および先端の技術を駆使して、製造プロセスの効率化、業務効率化、チームワーク強化、コスト削減、品質向上を実現します。このサービスは、製造業の課題を深く理解し、それに対する最適なデジタルソリューションを提供することで、企業が持続的な成長とイノベーションを達成できるようサポートします。
オンライン講座
製造業、主に購買・調達部門にお勤めの方々に向けた情報を配信しております。
新任の方やベテランの方、管理職を対象とした幅広いコンテンツをご用意しております。
お問い合わせ
コストダウンが利益に直結する術だと理解していても、なかなか前に進めることができない状況。そんな時は、newjiのコストダウン自動化機能で大きく利益貢献しよう!
(Β版非公開)