- お役立ち記事
- Checklist for compliance with purchasing process regulations in the medical device manufacturing industry
Checklist for compliance with purchasing process regulations in the medical device manufacturing industry
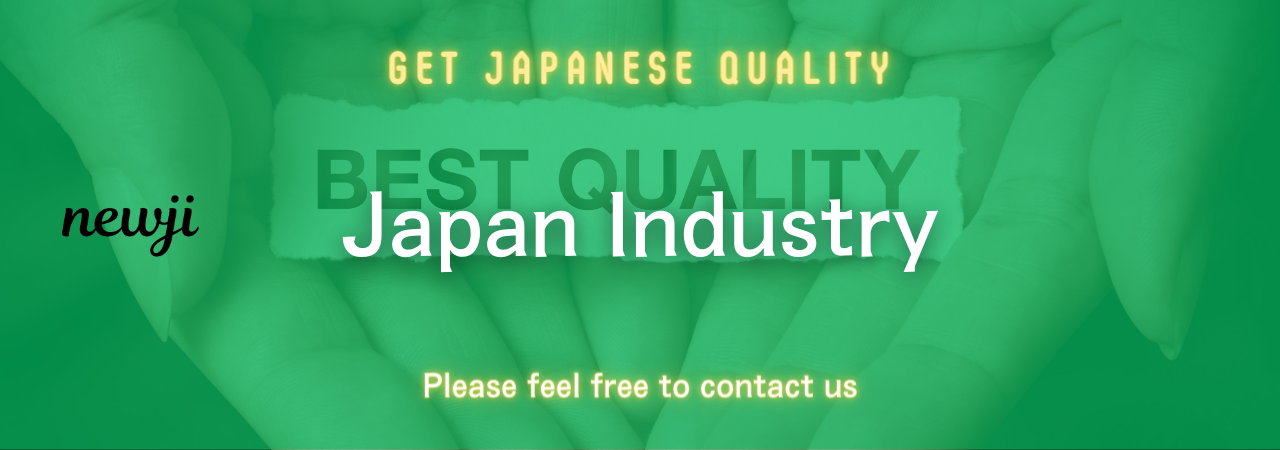
目次
Understanding the Importance of Compliance in Medical Device Manufacturing
Medical device manufacturing is a highly regulated industry, where compliance with purchasing process regulations is critical for ensuring product safety and efficacy.
The purchasing process involves a series of steps that ensure materials and components used in device manufacturing meet specific standards and quality controls.
Compliance with these regulations is not just a legal obligation but also a fundamental aspect of maintaining trust with healthcare providers and patients.
Manufacturers must adhere to guidelines set by authorities such as the Food and Drug Administration (FDA) in the United States and the European Medicines Agency (EMA) in Europe.
These regulations encompass various aspects, from supplier evaluations to material quality checks, documentation, and traceability, ensuring that every step of the purchasing process upholds the highest standards.
Key Regulations Governing the Purchasing Process
Supplier Evaluation and Selection
One of the primary steps in the purchasing process is the evaluation and selection of suppliers.
Manufacturers must have a robust process to assess suppliers based on their ability to meet regulatory and quality requirements.
This involves conducting audits, reviewing past performance, and assessing their processes and capabilities.
Quality Agreements
Quality agreements are crucial in defining the responsibilities and quality standards between manufacturers and suppliers.
These documents ensure that suppliers understand their obligations regarding the quality and compliance of materials and components.
Clearly defined quality agreements help prevent misunderstandings and ensure consistent adherence to regulatory requirements.
Material Verification and Testing
Upon receiving materials from suppliers, manufacturers must conduct thorough verification and testing to confirm compliance with predetermined standards.
This step involves assessing the physical and chemical properties of materials using standardized testing methods.
Only materials that pass these rigorous assessments can proceed to the production phase, ensuring that the final products are safe and reliable.
Documentation and Record-Keeping
Comprehensive documentation is a cornerstone of regulatory compliance in the medical device industry.
Every step of the purchasing process, from initial supplier assessments to material acceptance, must be meticulously documented.
These records serve as evidence of compliance and are crucial during regulatory audits and inspections.
Essential Elements of a Compliance Checklist
To ensure adherence to purchasing process regulations, medical device manufacturers should develop a detailed compliance checklist.
This checklist should cover all aspects of the acquisition process, promoting consistency and minimizing the risk of non-compliance.
Risk Assessment and Management
Identify potential risks associated with the purchasing process and implement strategies to mitigate them.
This includes assessing supplier reliability, potential material shortages, and changes in regulatory requirements.
Supplier Performance Monitoring
Regularly monitor and evaluate supplier performance to ensure ongoing compliance.
Track metrics such as delivery times, material quality, and adherence to quality agreements.
Address any deviations promptly to maintain a strong supply chain.
Training and Awareness
Ensure that employees involved in the purchasing process are adequately trained and aware of regulatory requirements.
Conduct regular training sessions to update them on the latest guidelines and industry best practices.
Creating a culture of compliance begins with informed and knowledgeable staff.
Benefits of a Robust Compliance Strategy
Implementing a thorough compliance strategy not only ensures adherence to regulations but also offers several benefits to medical device manufacturers.
Enhanced Product Safety and Quality
A well-structured purchasing process guarantees the use of high-quality materials, leading to safer and more reliable medical devices.
This enhances end-user trust and satisfaction, contributing to the manufacturer’s reputation.
Risk Mitigation
By systematically assessing potential risks and addressing them early, manufacturers can reduce the likelihood of supply chain disruptions and regulatory fines.
A proactive approach to compliance safeguards the company against unforeseen challenges.
Streamlined Operations
Compliance checklists and documentation processes streamline operations by providing clear guidelines and standards.
This minimizes process variances and improves overall efficiency, allowing manufacturers to focus on innovation and growth.
Conclusion: The Path Forward
In the medical device manufacturing industry, compliance with purchasing process regulations is indispensable for ensuring product safety, quality, and regulatory adherence.
By implementing comprehensive checklists and maintaining meticulous documentation, manufacturers can confidently navigate the complexities of the purchasing process.
Embracing a culture of compliance not only benefits the organization but also instills confidence in healthcare providers and patients relying on medical devices for critical care.
資料ダウンロード
QCD調達購買管理クラウド「newji」は、調達購買部門で必要なQCD管理全てを備えた、現場特化型兼クラウド型の今世紀最高の購買管理システムとなります。
ユーザー登録
調達購買業務の効率化だけでなく、システムを導入することで、コスト削減や製品・資材のステータス可視化のほか、属人化していた購買情報の共有化による内部不正防止や統制にも役立ちます。
NEWJI DX
製造業に特化したデジタルトランスフォーメーション(DX)の実現を目指す請負開発型のコンサルティングサービスです。AI、iPaaS、および先端の技術を駆使して、製造プロセスの効率化、業務効率化、チームワーク強化、コスト削減、品質向上を実現します。このサービスは、製造業の課題を深く理解し、それに対する最適なデジタルソリューションを提供することで、企業が持続的な成長とイノベーションを達成できるようサポートします。
オンライン講座
製造業、主に購買・調達部門にお勤めの方々に向けた情報を配信しております。
新任の方やベテランの方、管理職を対象とした幅広いコンテンツをご用意しております。
お問い合わせ
コストダウンが利益に直結する術だと理解していても、なかなか前に進めることができない状況。そんな時は、newjiのコストダウン自動化機能で大きく利益貢献しよう!
(Β版非公開)