- お役立ち記事
- The secret to improving on-time delivery rates in the procurement process
The secret to improving on-time delivery rates in the procurement process
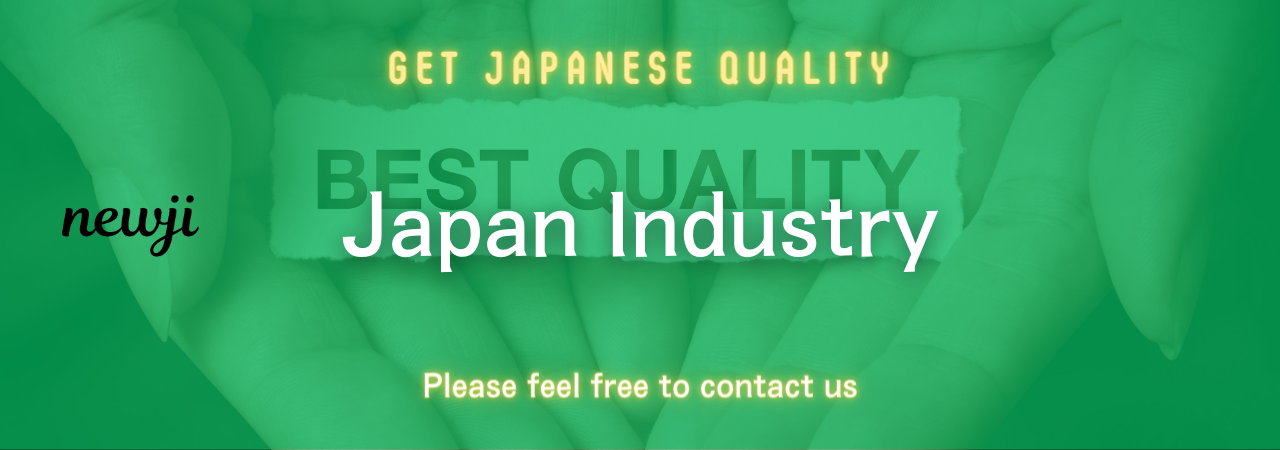
目次
Understanding On-Time Delivery in Procurement
On-time delivery is a critical aspect of the procurement process.
It refers to the timely receipt of purchased goods or services as per the agreed schedule.
When a company can consistently achieve this, it fosters better relationships with suppliers and customers, while also optimizing its supply chain efficiency.
Late deliveries can disrupt operations, lead to financial penalties, and damage reputations.
Hence, improving on-time delivery rates is essential for any organization seeking to enhance its efficiency and customer satisfaction.
Identifying Root Causes of Delivery Delays
To improve on-time delivery rates effectively, it’s important to first understand why delays occur.
Common causes include poor communication with suppliers, inadequate inventory management, and unforeseen logistic challenges.
By identifying these root causes, businesses can tailor strategies to address specific issues.
For example, if delays are due to miscommunication, improving supplier relationships and establishing clearer communication channels could be beneficial.
Communication with Suppliers
Often, delays in the procurement process stem from a lack of effective communication with suppliers.
Maintaining clear and constant communication can help avoid misunderstandings.
Regular meetings and updates on shipment statuses should be part of the procurement routine.
Inventory Management
Inefficient inventory management is another common cause of delayed deliveries.
Companies should implement robust inventory management systems to track stock levels and anticipate demand.
Using modern software solutions can provide real-time data, making it easier to keep the supply chain moving smoothly.
Logistic Challenges
Logistical issues such as transportation delays or customs holdups can also impact delivery times.
While some aspects may be out of your control, planning for potential disruptions by having contingency strategies in place can minimize the impact.
Strategies to Improve On-Time Delivery Rates
Improving on-time delivery rates isn’t just about fixing what’s broken.
It’s also about creating a robust system that can adapt to changes and handle unforeseen issues effectively.
Enhancing Supplier Relationships
Building strong, collaborative relationships with suppliers is vital.
Choose suppliers who have a track record of reliability and share your commitment to on-time deliveries.
Regularly review supplier performance and provide feedback.
Develop long-term partnerships with key suppliers, as this can lead to better terms and improved delivery timeframes.
Consider multiple suppliers for critical goods to reduce dependency on a single supplier, which can safeguard against delays.
Implementing Technology Solutions
Adopting new technologies can revolutionize how a company manages its procurement process.
Supply chain management software can automate ordering processes, track shipments, and optimize inventory levels.
Technologies such as artificial intelligence and machine learning can forecast potential delays before they happen, allowing preemptive measures to be taken.
Implementing these tools can greatly enhance the speed and accuracy of deliveries.
Using Data Analytics for Improvement
Data analytics plays a crucial role in improving on-time delivery rates.
By analyzing past performance data, procurement teams can identify trends and patterns that could indicate potential delays.
This insight allows companies to adjust their processes and strategies accordingly.
For example, data might reveal that certain suppliers are consistently late, prompting a review or change of suppliers.
Data analytics can also help in demand forecasting, ensuring that procurement decisions align with actual market needs, thereby reducing the risk of overstock or stockouts causing delivery issues.
Monitoring Performance
Establishing key performance indicators (KPIs) for on-time delivery is essential.
These KPIs should be monitored regularly to ensure that procurement goals align with the company’s overall objectives.
By tracking metrics such as order processing times, delivery lead times, and supplier performance, businesses can make informed decisions on how to optimize their procurement processes.
Conclusion
Improving on-time delivery rates in the procurement process requires a comprehensive approach that addresses communication, inventory management, and logistical challenges.
By fostering good relationships with suppliers, leveraging technology, and utilizing data analytics, companies can create more resilient and responsive supply chain systems.
Ultimately, the goal is to ensure that deliveries are made promptly, satisfying customer needs while minimizing operational disruptions.
Successful procurement strategies that focus on improving delivery rates can enhance overall business performance and provide a competitive edge in the market.
資料ダウンロード
QCD調達購買管理クラウド「newji」は、調達購買部門で必要なQCD管理全てを備えた、現場特化型兼クラウド型の今世紀最高の購買管理システムとなります。
ユーザー登録
調達購買業務の効率化だけでなく、システムを導入することで、コスト削減や製品・資材のステータス可視化のほか、属人化していた購買情報の共有化による内部不正防止や統制にも役立ちます。
NEWJI DX
製造業に特化したデジタルトランスフォーメーション(DX)の実現を目指す請負開発型のコンサルティングサービスです。AI、iPaaS、および先端の技術を駆使して、製造プロセスの効率化、業務効率化、チームワーク強化、コスト削減、品質向上を実現します。このサービスは、製造業の課題を深く理解し、それに対する最適なデジタルソリューションを提供することで、企業が持続的な成長とイノベーションを達成できるようサポートします。
オンライン講座
製造業、主に購買・調達部門にお勤めの方々に向けた情報を配信しております。
新任の方やベテランの方、管理職を対象とした幅広いコンテンツをご用意しております。
お問い合わせ
コストダウンが利益に直結する術だと理解していても、なかなか前に進めることができない状況。そんな時は、newjiのコストダウン自動化機能で大きく利益貢献しよう!
(Β版非公開)