- お役立ち記事
- The issue of balancing cost optimization and quality assurance faced by purchasing departments in the manufacturing industry
The issue of balancing cost optimization and quality assurance faced by purchasing departments in the manufacturing industry
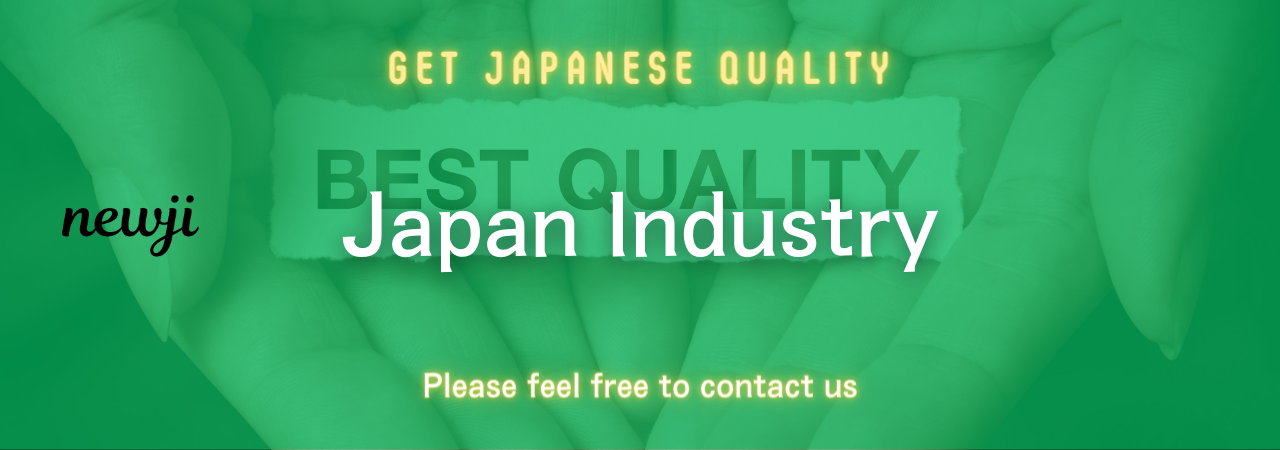
目次
Understanding the Dilemma
The manufacturing industry plays a crucial role in the global economy, striving to produce high-quality products at competitive prices.
One of the most significant challenges these industries face is balancing cost optimization and quality assurance, a responsibility that often falls on the shoulders of the purchasing departments.
Understanding this dilemma is essential to optimize operations without compromising on product quality.
Let’s delve into the complexities of this challenge.
The Role of Purchasing Departments
Purchasing departments play a pivotal role in manufacturing firms.
They are responsible for acquiring raw materials, components, and services necessary for production at the best possible costs.
While optimizing these inputs for cost, they must also ensure they meet quality standards set by the company.
This dual responsibility requires a delicate balancing act.
Cost Optimization: A Necessary Strategy
Cost optimization is crucial for maintaining competitive pricing and improving profit margins.
Purchasing departments are often tasked with negotiating better prices with suppliers, seeking discounts, and exploring alternative sources for materials.
However, this pursuit of reducing costs must not lead to sacrificing the quality of the inputs.
Quality Assurance: The Paramount Concern
Manufacturers rely heavily on the quality of the materials they use in their products.
The purchasing department must ensure that all acquired materials meet the stringent quality standards necessary for maintaining the company’s reputation.
Quality assurance involves rigorous checking, supplier audits, and strategic partnerships that prioritize quality as much as cost.
The Challenges in Balancing Cost and Quality
Supplier Selection and Management
Choosing the right suppliers is a critical decision for purchasing departments.
Suppliers must be evaluated not just on the basis of cost, but also their ability to deliver consistent quality.
Building strong partnerships with dependable suppliers can facilitate better terms and conditions, reducing risks associated with cost fluctuations and quality inconsistencies.
Risk Management
Purchasing departments must also address risks related to supply chain disruptions, which can impact both cost and quality.
These can be mitigated by diversifying the supplier base, ensuring that no single supplier has an overwhelming influence over production processes.
Technological Advancements
The integration of technology in the purchasing process can provide valuable insights and data that aid in decision-making.
Advanced analytics can help departments identify cost-effective suppliers who also meet quality prerequisites, allowing for more informed choices.
Strategies for Balancing Cost and Quality
Implementing a Total Cost of Ownership (TCO) Approach
A Total Cost of Ownership approach considers not just the initial purchasing price, but the additional costs incurred throughout the product lifecycle.
By adopting TCO, purchasing departments can make decisions that balance cost with quality, considering factors like maintenance, operation, and disposal.
Developing Long-term Supplier Relationships
Building long-lasting relationships with suppliers can lead to mutual benefits.
Suppliers are often more willing to provide concessions or prioritize orders for long-standing partners who consistently value their quality outputs.
Investment in Employee Training
Ensuring that purchasing staff are well-trained is crucial for making informed decisions.
By understanding the market, materials, and quality assessments, employees can better negotiate with suppliers and make balanced purchasing decisions.
Adopting Quality Management Systems
Quality management systems like ISO certifications can help maintain a standard of quality assurance.
These systems provide frameworks for purchasing departments to follow, ensuring that quality is always a focal point in procurement processes.
Conclusion: Striking the Right Balance
Balancing cost optimization and quality assurance is not an easy task, but it is essential for the success of manufacturing industries.
The purchasing departments hold a crucial position in this balancing act, requiring them to continuously evaluate and adjust their strategies.
By focusing on long-term supplier relationships, considering total cost implications, leveraging technology, and investing in quality management systems, these departments can strike a balance that benefits both the company and its customers.
Ultimately, the goal is to maintain a harmonious relationship between cost and quality, ensuring the uninterrupted production of superior products.
資料ダウンロード
QCD調達購買管理クラウド「newji」は、調達購買部門で必要なQCD管理全てを備えた、現場特化型兼クラウド型の今世紀最高の購買管理システムとなります。
ユーザー登録
調達購買業務の効率化だけでなく、システムを導入することで、コスト削減や製品・資材のステータス可視化のほか、属人化していた購買情報の共有化による内部不正防止や統制にも役立ちます。
NEWJI DX
製造業に特化したデジタルトランスフォーメーション(DX)の実現を目指す請負開発型のコンサルティングサービスです。AI、iPaaS、および先端の技術を駆使して、製造プロセスの効率化、業務効率化、チームワーク強化、コスト削減、品質向上を実現します。このサービスは、製造業の課題を深く理解し、それに対する最適なデジタルソリューションを提供することで、企業が持続的な成長とイノベーションを達成できるようサポートします。
オンライン講座
製造業、主に購買・調達部門にお勤めの方々に向けた情報を配信しております。
新任の方やベテランの方、管理職を対象とした幅広いコンテンツをご用意しております。
お問い合わせ
コストダウンが利益に直結する術だと理解していても、なかなか前に進めることができない状況。そんな時は、newjiのコストダウン自動化機能で大きく利益貢献しよう!
(Β版非公開)