- お役立ち記事
- An example of RPA implementation that fundamentally changes the purchasing process in the manufacturing industry
An example of RPA implementation that fundamentally changes the purchasing process in the manufacturing industry
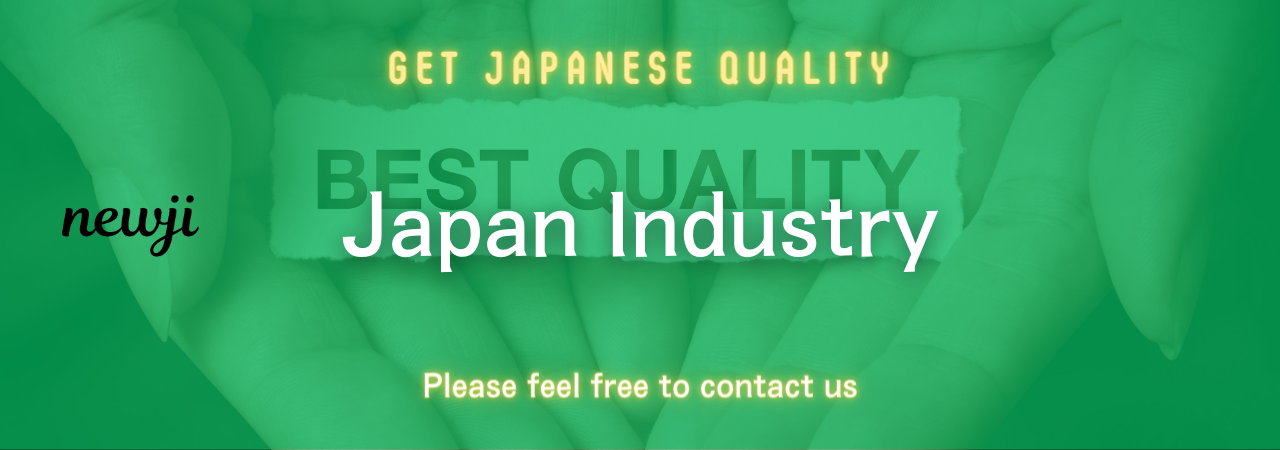
目次
Understanding RPA and Its Role in the Manufacturing Industry
Robotic Process Automation, commonly known as RPA, is a technology that uses software robots or “bots” to automate repetitive and mundane tasks traditionally performed by humans.
In the manufacturing industry, these tasks often include data entry, invoice processing, and inventory management.
RPA can significantly improve efficiency, reduce errors, and free up human resources for more strategic tasks.
This technology is increasingly being adopted by manufacturers to streamline operations and drive productivity.
The Importance of RPA in Streamlining Purchasing Processes
Purchasing processes in manufacturing are intricate and multifaceted, involving numerous steps such as order placement, supplier communication, and invoice verification.
These processes are vital as they ensure that materials and components are acquired at the right time and at the right cost.
Inefficient purchasing processes can lead to production delays, increased costs, and missed opportunities.
RPA can transform purchasing by automating routine tasks, such as generating purchase orders, confirming receipts, and updating inventory levels.
By implementing RPA, manufacturers can achieve real-time processing and enhanced accuracy, which are crucial for maintaining competitive advantage.
RPA Implementation to Revolutionize the Purchasing Process
Implementing RPA in the purchasing process begins with identifying the tasks that are suitable for automation.
In manufacturing, tasks such as checking inventory levels, sending purchase orders, and processing invoices are prime candidates for automation.
Once identified, these tasks can be automated using RPA tools, which are designed to mimic human actions like logging into systems, entering data, and extracting information from documents.
Step-by-Step RPA Implementation
1. **Assessment and Identification:**
The first step is a thorough assessment of the current purchasing process.
This involves mapping out each step to identify which tasks are repetitive and rule-based, thus suitable for automation.
2. **Choosing the Right RPA Tool:**
Selecting an RPA tool that aligns with the company’s existing systems and future goals is crucial.
The tool must be scalable, user-friendly, and capable of integrating with other technologies.
3. **Design and Development:**
After selecting the RPA tool, the next step is designing and developing the bots to perform selected tasks.
This involves configuring the bot to understand existing processes and adapt to perform tasks efficiently.
4. **Testing and Validation:**
Once developed, it’s essential to test the bot in a controlled environment to ensure it performs as expected.
Any issues discovered during testing can be rectified promptly.
5. **Deployment and Monitoring:**
After successful testing, the bot is deployed into the live environment.
Continuous monitoring is required to identify any areas for improvement and ensure smooth operation.
Real-life Example of RPA Implementation
Consider a manufacturing company that produces automotive parts.
The company used to rely on a manual purchasing process that involved paper-based order forms, manual data entry, and regular communication with numerous suppliers.
The process was time-consuming and prone to errors, resulting in production delays.
By implementing RPA, the company transformed its purchasing process.
RPA bots were deployed to automatically generate order forms based on real-time inventory data.
They also handled supplier communication by sending out requests for quotes and order confirmations.
Additionally, bots streamlined invoice processing by extracting information from digital invoices and updating the company’s ERP system.
As a result, the manufacturer experienced a 30% reduction in processing time, improved accuracy in order fulfillment, and cost savings due to reduced human labor involvement.
Benefits of RPA in the Manufacturing Purchasing Process
The adoption of RPA in manufacturing purchasing offers numerous benefits:
– **Increased Efficiency:**
By automating repetitive and mundane tasks, RPA significantly increases process efficiency.
– **Improved Accuracy:**
Automation minimizes human error, ensuring data is processed accurately and consistently.
– **Cost Efficiency:**
RPA reduces the need for manual labor, leading to cost savings that can be redirected to strategic areas.
– **Scalability:**
RPA systems can easily scale with growing business needs without requiring additional resources.
– **Enhanced Supplier Relationships:**
With quicker and more reliable order processing, manufacturers can maintain better relationships with suppliers, leading to favorable terms.
Challenges in RPA Implementation
While the benefits are significant, implementing RPA in the manufacturing purchasing process comes with challenges:
– **Change Management:**
Transitioning from manual to automated processes requires change management to ensure employee buy-in and smooth adaptation.
– **Integration Issues:**
RPA must seamlessly integrate with existing systems, which can be problematic if not handled properly.
– **Technical Hurdles:**
Developing and maintaining RPA bots require technical expertise and ongoing support.
– **Initial Costs:**
The setup cost for RPA can be significant, although the ROI typically justifies the investment over time.
Conclusion
RPA has the potential to fundamentally change the purchasing processes in the manufacturing industry by automating repetitive tasks, reducing errors, and improving efficiency.
Functional implementation requires careful planning, tool selection, and consistent monitoring.
Despite the challenges, the benefits of RPA in enhancing operational efficiency and reducing costs make it a crucial investment for manufacturers aiming to stay competitive in a dynamic market.
With proper execution, RPA can revolutionize how purchasing processes are handled, leading to healthier bottom-line outcomes and stronger supplier relationships.
資料ダウンロード
QCD調達購買管理クラウド「newji」は、調達購買部門で必要なQCD管理全てを備えた、現場特化型兼クラウド型の今世紀最高の購買管理システムとなります。
ユーザー登録
調達購買業務の効率化だけでなく、システムを導入することで、コスト削減や製品・資材のステータス可視化のほか、属人化していた購買情報の共有化による内部不正防止や統制にも役立ちます。
NEWJI DX
製造業に特化したデジタルトランスフォーメーション(DX)の実現を目指す請負開発型のコンサルティングサービスです。AI、iPaaS、および先端の技術を駆使して、製造プロセスの効率化、業務効率化、チームワーク強化、コスト削減、品質向上を実現します。このサービスは、製造業の課題を深く理解し、それに対する最適なデジタルソリューションを提供することで、企業が持続的な成長とイノベーションを達成できるようサポートします。
オンライン講座
製造業、主に購買・調達部門にお勤めの方々に向けた情報を配信しております。
新任の方やベテランの方、管理職を対象とした幅広いコンテンツをご用意しております。
お問い合わせ
コストダウンが利益に直結する術だと理解していても、なかなか前に進めることができない状況。そんな時は、newjiのコストダウン自動化機能で大きく利益貢献しよう!
(Β版非公開)