- お役立ち記事
- How to implement a data integration platform to transform manufacturing purchasing processes
How to implement a data integration platform to transform manufacturing purchasing processes
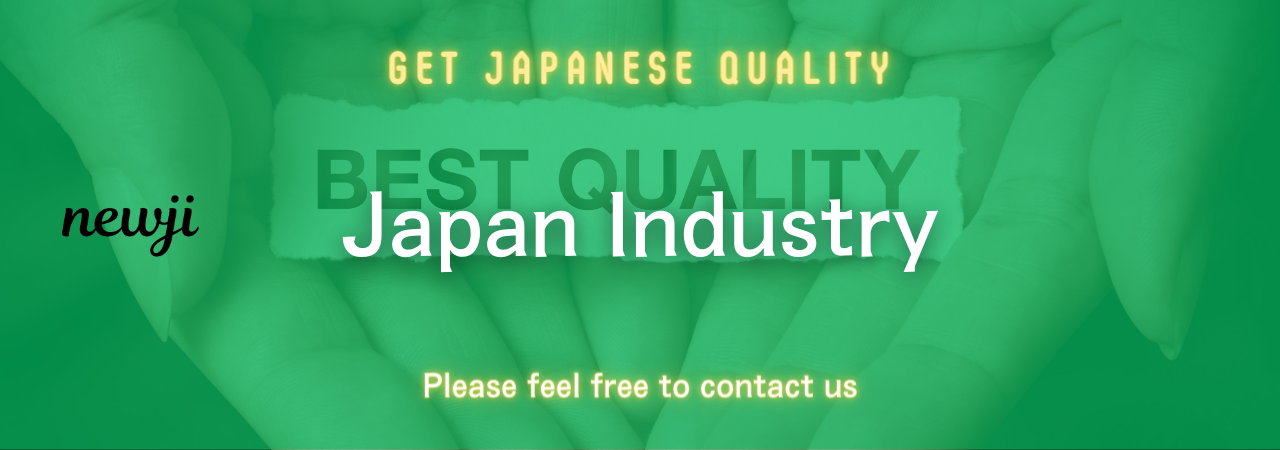
目次
Introduction to Data Integration in Manufacturing
In the fast-paced world of manufacturing, efficiency and accuracy are critical to maintaining a competitive edge.
One of the core areas where this principle is evident is in the purchasing process.
Traditionally, the purchasing process in manufacturing has been fragmented, involving multiple systems and stakeholders.
This can lead to inefficiencies, errors, and increased costs.
To address these challenges, many manufacturing companies are turning to data integration platforms.
A data integration platform helps streamline and transform purchasing processes by enabling seamless communication between disparate systems.
This results in improved data accuracy, enhanced decision-making, and more efficient supply chain operations.
Understanding Data Integration Platforms
A data integration platform is a suite of tools or software that allows for the integration of data from multiple sources into a central system.
This can include databases, cloud services, mobile devices, and more.
These platforms offer functionalities such as data cleansing, transformation, and loading, ensuring that the integrated data is consistent and accurate.
By implementing a data integration platform, manufacturing companies can achieve a unified view of their purchasing data.
It enables the consolidation of supplier information, inventory levels, and order statuses into a single interface.
This unified view is crucial for making informed decisions and developing strategic purchasing plans.
Key Features of a Data Integration Platform
When selecting a data integration platform, it is important to look for key features that support the unique requirements of manufacturing purchasing processes.
1. **Real-Time Data Processing**
The ability to process data in real-time is critical for manufacturing, as it allows for timely decisions.
This feature ensures that all stakeholders have access to the most current information.
2. **Scalability**
As your manufacturing operations grow, your data integration platform should be able to scale accordingly.
This involves handling increased data volumes and accommodating additional data sources without compromising performance.
3. **Data Quality Management**
High-quality data is essential for accurate purchasing processes.
A robust data integration platform should offer tools for data profiling, cleansing, and enrichment to ensure data integrity.
4. **Seamless Connectivity**
The platform should support a wide range of connectors that enable integration with various data sources, including ERP systems, CRM platforms, and IoT devices.
The Benefits of Implementing a Data Integration Platform
Implementing a data integration platform in manufacturing brings numerous benefits that enhance the purchasing process.
Improved Decision-Making
With a centralized system that integrates data from multiple sources, decision-makers have access to comprehensive, accurate data.
This allows them to evaluate suppliers, monitor inventory levels, and negotiate better terms effectively.
Real-time data analysis also facilitates proactive decision-making, helping to avoid potential issues before they become problems.
Increased Efficiency
Data integration eliminates the manual tasks associated with data entry and reconciliation.
Automating these processes reduces human error, frees up employee time, and speeds up the purchasing cycle.
This increased efficiency translates into cost savings and better supplier relationships.
Enhanced Collaboration
A data integration platform fosters collaboration between different departments by providing a single source of truth.
Sales, procurement, and logistics teams can coordinate seamlessly, ensuring that purchasing processes align with overall business objectives.
This improved communication results in a more agile and responsive supply chain.
Steps to Implement a Data Integration Platform
Successfully implementing a data integration platform requires careful planning and execution.
Step 1: Define Your Goals
Begin by identifying the specific challenges and goals you aim to address through data integration.
This could include reducing procurement costs, improving order accuracy, or enhancing supplier relationships.
Clearly define the objectives to ensure that the chosen platform aligns with your business needs.
Step 2: Evaluate and Select a Platform
Conduct a thorough evaluation of available data integration platforms on the market.
Consider factors such as ease of use, adaptability, and vendor support.
It is crucial to choose a platform that can integrate smoothly with your existing systems and accommodate future growth.
Step 3: Plan and Map Data Sources
Work with your IT team to identify and map out all relevant data sources.
Determine how data will be extracted, transformed, and loaded into the central system.
Ensuring data consistency and accuracy during this stage is paramount for a successful integration.
Step 4: Develop a Pilot Program
Before full-scale implementation, consider running a pilot program.
This will help identify potential challenges and allow you to make adjustments as needed.
Involve key stakeholders to ensure that the platform meets their needs and requirements.
Step 5: Execute Full Implementation
After a successful pilot, proceed with the full implementation of the data integration platform.
Provide training to employees to ensure that they are comfortable with the new system.
Continuous monitoring and support are essential to address any issues that may arise post-implementation.
Conclusion
Integrating a data integration platform into manufacturing purchasing processes is a strategic move that can greatly enhance efficiency, accuracy, and decision-making.
By centralizing data and automating manual processes, companies can achieve significant cost savings and improve supplier relationships.
The journey to implementation requires careful planning, but the long-term benefits make it a worthwhile investment.
Embracing data integration is more than just a technological upgrade; it is a transformation that positions manufacturing companies to thrive in an increasingly data-driven world.
Enhance your purchasing processes today by considering a data integration platform that meets your organization’s unique needs.
資料ダウンロード
QCD調達購買管理クラウド「newji」は、調達購買部門で必要なQCD管理全てを備えた、現場特化型兼クラウド型の今世紀最高の購買管理システムとなります。
ユーザー登録
調達購買業務の効率化だけでなく、システムを導入することで、コスト削減や製品・資材のステータス可視化のほか、属人化していた購買情報の共有化による内部不正防止や統制にも役立ちます。
NEWJI DX
製造業に特化したデジタルトランスフォーメーション(DX)の実現を目指す請負開発型のコンサルティングサービスです。AI、iPaaS、および先端の技術を駆使して、製造プロセスの効率化、業務効率化、チームワーク強化、コスト削減、品質向上を実現します。このサービスは、製造業の課題を深く理解し、それに対する最適なデジタルソリューションを提供することで、企業が持続的な成長とイノベーションを達成できるようサポートします。
オンライン講座
製造業、主に購買・調達部門にお勤めの方々に向けた情報を配信しております。
新任の方やベテランの方、管理職を対象とした幅広いコンテンツをご用意しております。
お問い合わせ
コストダウンが利益に直結する術だと理解していても、なかなか前に進めることができない状況。そんな時は、newjiのコストダウン自動化機能で大きく利益貢献しよう!
(Β版非公開)