- お役立ち記事
- Successful example of multi-tier supplier management to improve procurement efficiency in manufacturing industry
Successful example of multi-tier supplier management to improve procurement efficiency in manufacturing industry
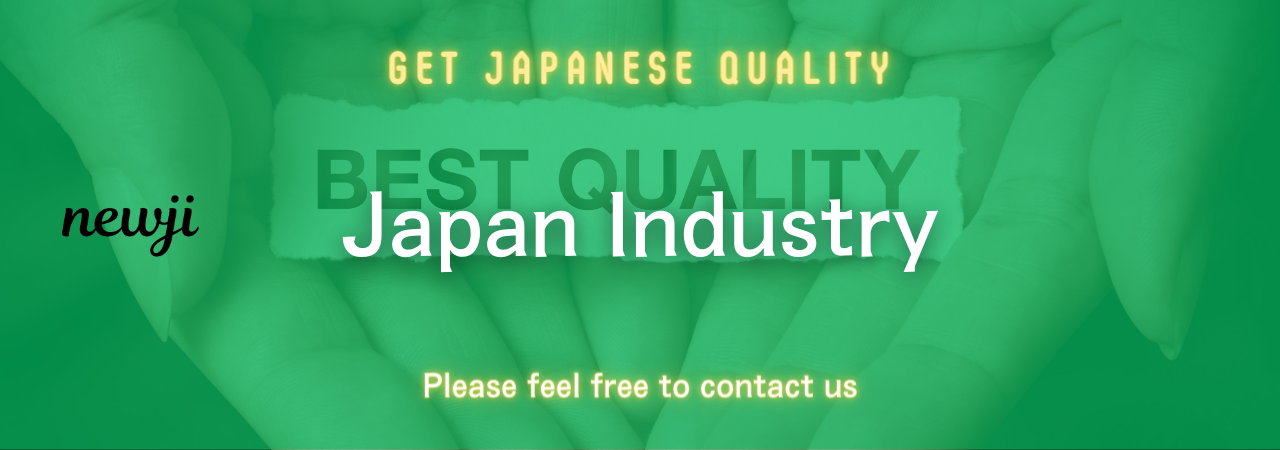
目次
Understanding Multi-Tier Supplier Management
Multi-tier supplier management is a procurement strategy used by manufacturing companies to enhance supply chain efficiency.
It involves overseeing not only direct suppliers but also their suppliers and sub-suppliers.
This approach helps companies gain greater visibility and control over their entire supply chain.
In the fast-paced manufacturing industry, companies need to move beyond managing just their immediate suppliers.
Globalization and complex products often require hundreds, if not thousands, of suppliers, contributing parts or services.
By implementing a multi-tier supplier management strategy, a company can ensure that all levels of the supply chain meet specific standards, reducing risks and improving overall procurement efficiency.
Key Benefits of Multi-Tier Supplier Management
Improved Supply Chain Visibility
One of the significant advantages of multi-tier supplier management is increased supply chain visibility.
By identifying and tracking sub-suppliers, manufacturers can better anticipate potential disruptions.
For example, if a third-level supplier faces shortages, the manufacturer can act proactively to mitigate its impact.
Reduced Risk
With clear visibility at all levels, companies can identify potential risks before they escalate.
Whether it’s price volatility, geopolitical issues, or quality concerns, having insights into every tier allows manufacturers to react swiftly and minimize risk.
Enhanced Collaboration
Multi-tier supplier management fosters better collaboration between all parties in the supply chain.
When everyone is aligned and understands the expectations, communication becomes more effective, leading to higher quality outputs and more efficient procurement processes.
Effective Cost Management
Understanding the entire supply chain’s cost structures enables manufacturers to negotiate better terms, identify cost-saving opportunities, and minimize waste.
Real-time data from each tier can be leveraged to optimize procurement costs.
Compliance and Sustainability
Monitoring suppliers across all levels ensures compliance with regulations and sustainability standards.
It provides manufacturers with the confidence that their entire supply chain adheres to necessary legal and ethical requirements.
The Process of Implementing Multi-Tier Supplier Management
Mapping the Supply Chain
The first step is mapping out the entire supply chain from raw materials to the final product.
Manufacturers need to identify who their suppliers are, and more importantly, who their suppliers’ suppliers are.
This comprehensive mapping helps identify key touchpoints that may impact efficiency.
Supplier Evaluation
Once a complete map is established, the next step is evaluating each supplier’s capabilities, performance, and compliance.
This assessment should factor in potential risks at each level and gauge the reliability and quality standards of each supplier.
Technology Utilization
Leveraging advanced technology solutions is critical in multi-tier supplier management.
Tools such as supply chain management software and analytics platforms can provide real-time insights and streamline communication between different tiers.
Implementing these technologies aids in the efficient monitoring and management of the extended supply chain.
Strengthening Relationships
Building strong, long-lasting relationships with suppliers is essential.
Manufacturers should regularly engage with suppliers, providing them with regular feedback and recognizing their contributions to the supply chain.
Effective relationship management ensures all parties are working collaboratively towards common goals.
A Successful Example of Multi-Tier Supplier Management
A notable example of successful multi-tier supplier management can be seen in the automotive industry’s approach.
Automakers often manage complex supply chains involving numerous suppliers across different tiers.
Let’s look at one of the leading automotive companies, Toyota, to exemplify success.
Toyota’s Approach
Toyota pioneered the ‘Toyota Production System,’ focusing on lean manufacturing and efficiency.
This system includes a detailed multi-tier supplier management strategy, where Toyota collaborates with numerous suppliers across various tiers.
Toyota views its suppliers as partners and invests in their mutual growth and development.
They work together on innovation and efficiency improvements, ensuring that quality standards remain high across the board.
Direct Communication and Feedback
Toyota’s approach includes establishing direct communication channels with sub-suppliers, not just a primary point of contact.
This ensures fast information flow and immediate feedback, preventing small issues from evolving into major disruptions.
Continuous Improvement Initiatives
Toyota also engages in continuous improvement initiatives, encouraging all suppliers to adopt similar practices.
Sharing best practices among suppliers allows them to improve their processes and performance levels.
Conclusion
Multi-tier supplier management holds the key to improving procurement efficiency in the manufacturing industry.
With its benefits of enhanced visibility, risk reduction, cost management, and compliance, manufacturers can secure a competitive edge in the market.
By adopting strategies such as those implemented by Toyota, companies can ensure a robust and efficient supply chain that withstands the challenges of a dynamic business environment.
Embedding a culture of collaboration and continuous improvement across the supply chain will lead to long-term procurement success.
資料ダウンロード
QCD調達購買管理クラウド「newji」は、調達購買部門で必要なQCD管理全てを備えた、現場特化型兼クラウド型の今世紀最高の購買管理システムとなります。
ユーザー登録
調達購買業務の効率化だけでなく、システムを導入することで、コスト削減や製品・資材のステータス可視化のほか、属人化していた購買情報の共有化による内部不正防止や統制にも役立ちます。
NEWJI DX
製造業に特化したデジタルトランスフォーメーション(DX)の実現を目指す請負開発型のコンサルティングサービスです。AI、iPaaS、および先端の技術を駆使して、製造プロセスの効率化、業務効率化、チームワーク強化、コスト削減、品質向上を実現します。このサービスは、製造業の課題を深く理解し、それに対する最適なデジタルソリューションを提供することで、企業が持続的な成長とイノベーションを達成できるようサポートします。
オンライン講座
製造業、主に購買・調達部門にお勤めの方々に向けた情報を配信しております。
新任の方やベテランの方、管理職を対象とした幅広いコンテンツをご用意しております。
お問い合わせ
コストダウンが利益に直結する術だと理解していても、なかなか前に進めることができない状況。そんな時は、newjiのコストダウン自動化機能で大きく利益貢献しよう!
(Β版非公開)