- お役立ち記事
- A real case of reducing component costs required by manufacturing sites
A real case of reducing component costs required by manufacturing sites
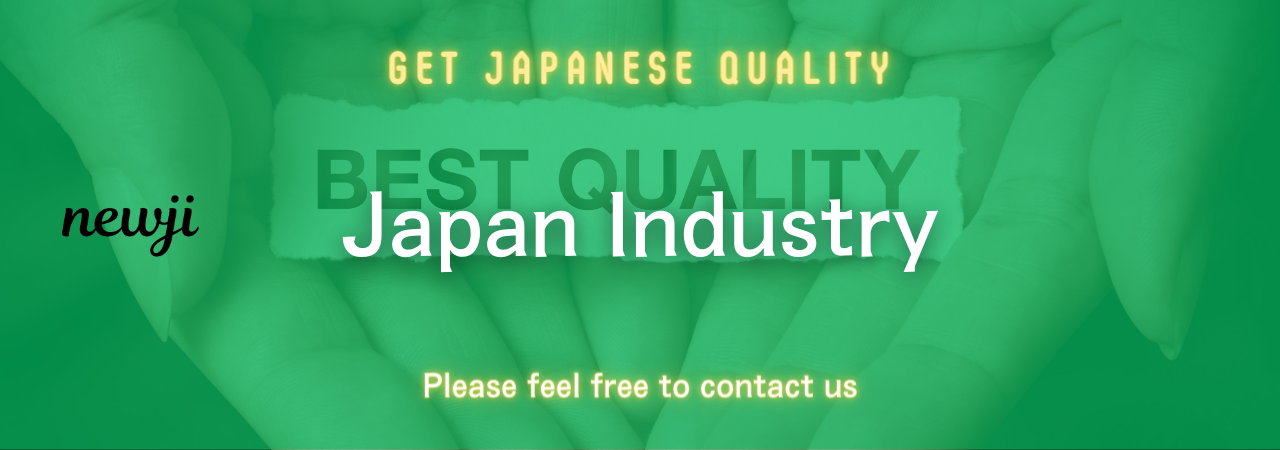
目次
Understanding Component Costs
Component costs are a significant part of any manufacturing process.
They encompass the expenses incurred in obtaining the raw materials and parts required to produce a finished product.
For manufacturers, controlling these costs is crucial in maintaining profitability and competitiveness.
In the world of manufacturing, every penny counts.
As businesses strive to reduce their overheads and maximize efficiency, component costs are constantly under scrutiny.
Reducing these expenses can lead to substantial savings, not just in the short term, but also in the long run.
However, achieving this requires a strategic approach and a good understanding of the factors that influence component costs.
Factors Affecting Component Costs
Several factors can influence component costs.
Understanding these can help manufacturers develop strategies to reduce expenses effectively.
Supplier Relationships
The relationship between manufacturers and suppliers plays a critical role in determining component costs.
Finding the right suppliers who provide quality materials at reasonable prices is essential.
Negotiating terms, maintaining good communication, and building long-term relationships can significantly impact costs.
Market Dynamics
The market conditions, including supply and demand, greatly affect component prices.
When demand is high and supply is low, prices increase.
Conversely, when supply exceeds demand, prices tend to drop.
Keeping an eye on market trends can help manufacturers time their purchases more strategically.
Technological Advancements
Technological advancements can lead to more efficient production processes, which often reduce component costs.
Implementing innovative technologies, such as automation and machine learning, can optimize resource use and reduce waste, thereby decreasing overall component costs.
Quality Control
While using cheaper components might seem like a quick way to cut costs, it can lead to quality issues that might incur greater expenses down the line.
Therefore, striking a balance between cost and quality is critical.
Strategies to Reduce Component Costs
Developing effective strategies to reduce component costs is crucial for manufacturers aiming to maintain competitiveness and profitability.
Streamlining Supply Chain Management
An efficient supply chain is vital in reducing component costs.
By streamlining processes, manufacturers can reduce lead times, minimize inventory levels, and lower transportation costs.
This can be achieved through expanding supplier networks, improving logistics, and employing just-in-time inventory systems.
Bulk Purchasing
Buying in bulk is a proven method to reduce unit costs.
When manufacturers purchase larger quantities, they can often negotiate better deals with suppliers, leading to significant savings.
However, it’s crucial to balance this with inventory management to avoid excess stock.
Leveraging Technology
Harnessing technology to improve operational efficiency can significantly impact component costs.
Investing in accurate forecasting software can enhance demand prediction, ensuring that manufacturers only purchase the components they truly need, which reduces waste and excess costs.
Supplier Partnerships
Establishing strong partnerships with suppliers can lead to mutual benefits.
This relationship can pave the way for better negotiating power, improved payment terms, and access to suppliers’ expertise in cost-saving measures.
A Real-Life Example of Reducing Component Costs
A case in point is a mid-sized electronics manufacturing company.
The company faced high costs for a specific component, which was essential for their flagship product.
By analyzing the factors impacting their costs, they identified that their reliance on a single supplier was the main issue.
After thorough market research, they identified alternative suppliers who could provide the same quality component at a reduced price.
The company implemented a dual-sourcing strategy, diversifying their supply base, which not only reduced costs but also mitigated risks associated with relying on one supplier.
Additionally, they invested in technology to optimize their production line, thereby reducing waste and improving overall efficiency.
This approach led to a 15% reduction in component costs, directly influencing their bottom line positively.
Conclusion
Reducing component costs is an ongoing challenge for any manufacturing business.
However, with a strategic approach that includes understanding market dynamics, leveraging technology, and establishing strong supplier relationships, manufacturers can achieve significant savings.
By continuously evaluating and optimizing processes, companies can stay competitive in a constantly evolving market.
The real-world example we examined demonstrates the potential benefits of these strategies, showcasing the tangible effects of careful and considered cost management.
資料ダウンロード
QCD調達購買管理クラウド「newji」は、調達購買部門で必要なQCD管理全てを備えた、現場特化型兼クラウド型の今世紀最高の購買管理システムとなります。
ユーザー登録
調達購買業務の効率化だけでなく、システムを導入することで、コスト削減や製品・資材のステータス可視化のほか、属人化していた購買情報の共有化による内部不正防止や統制にも役立ちます。
NEWJI DX
製造業に特化したデジタルトランスフォーメーション(DX)の実現を目指す請負開発型のコンサルティングサービスです。AI、iPaaS、および先端の技術を駆使して、製造プロセスの効率化、業務効率化、チームワーク強化、コスト削減、品質向上を実現します。このサービスは、製造業の課題を深く理解し、それに対する最適なデジタルソリューションを提供することで、企業が持続的な成長とイノベーションを達成できるようサポートします。
オンライン講座
製造業、主に購買・調達部門にお勤めの方々に向けた情報を配信しております。
新任の方やベテランの方、管理職を対象とした幅広いコンテンツをご用意しております。
お問い合わせ
コストダウンが利益に直結する術だと理解していても、なかなか前に進めることができない状況。そんな時は、newjiのコストダウン自動化機能で大きく利益貢献しよう!
(Β版非公開)