- お役立ち記事
- Measures to address the supplier shortage issue faced by purchasing managers in the aviation industry
月間76,176名の
製造業ご担当者様が閲覧しています*
*2025年3月31日現在のGoogle Analyticsのデータより
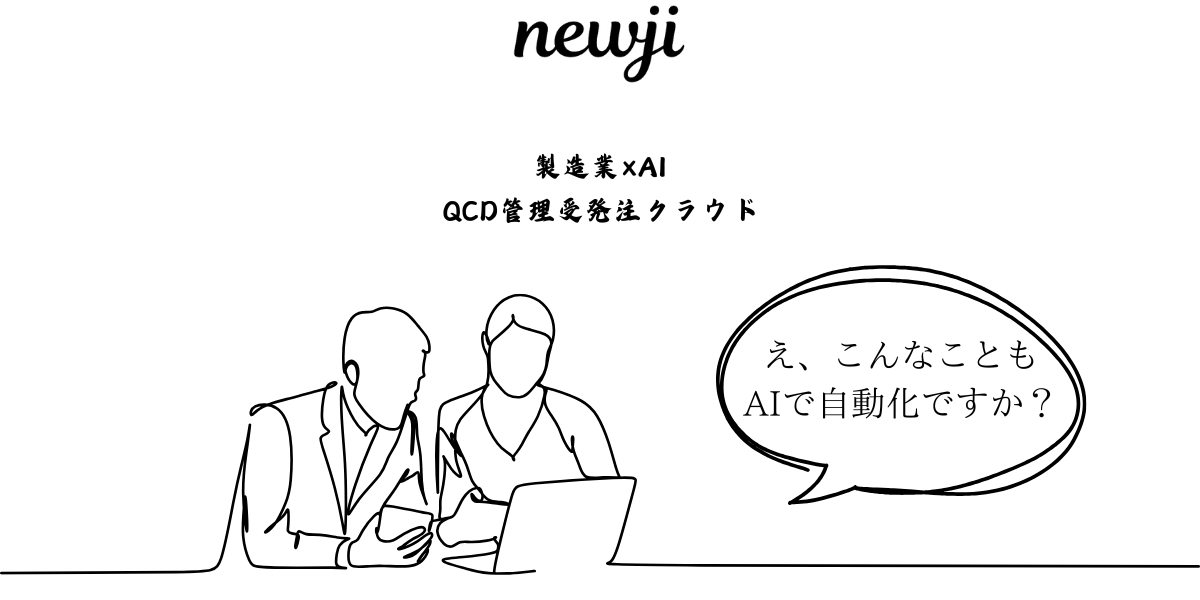
Measures to address the supplier shortage issue faced by purchasing managers in the aviation industry
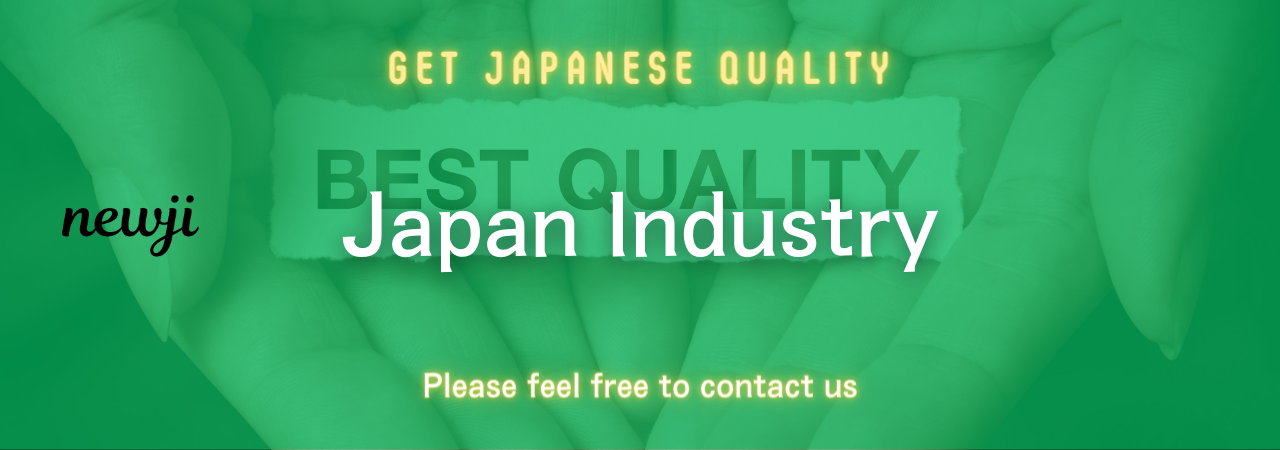
目次
Understanding the Supplier Shortage Issue in the Aviation Industry
In recent years, the aviation industry has been grappling with a significant challenge—supplier shortages.
This issue has affected the entire supply chain, leading to delays and increased costs.
Purchasing managers, in particular, have found themselves at the forefront of navigating these turbulent waters.
Supplier shortages occur when there is an insufficient supply of materials or components, necessary for production or service delivery.
The causes of these shortages can be varied, including natural disasters, political factors, pandemics, or even the sudden rise in demand outpacing suppliers’ ability to deliver.
For the aviation industry, which depends heavily on various components sourced globally, these shortages have historically posed significant hurdles.
From aluminium and titanium used in aircraft manufacturing to electronic components, the lack of essential materials can halt production altogether.
Challenges Faced by Purchasing Managers
Purchasing managers in the aviation sector are tasked with the daunting responsibility of keeping the supply chain moving smoothly, despite these shortages.
They face several challenges such as dealing with volatile prices, finding new suppliers, and ensuring quality standards are met consistently.
One of the immediate challenges is the unpredictability of costs.
As supplies become scarce, prices can skyrocket, blowing budgets out of the water.
This volatility makes it difficult for purchasing managers to forecast expenses accurately and maintain profitability.
Additionally, locating alternative suppliers who can meet strict aviation standards is far from easy.
Given the rigorous safety and quality standards in the aviation industry, it’s not just about finding a supplier who can deliver on time, but one who can deliver components that meet these exacting standards.
Effective Measures to Address Supplier Shortages
To effectively tackle supplier shortages, a strategic approach is required.
Below are several approaches that purchasing managers in the aviation industry can adopt to mitigate the impacts of this ongoing issue.
Diversification of Supplier Base
One of the most effective strategies for overcoming supplier shortages is diversification.
Relying on a single supplier or a limited number of suppliers for crucial components can be risky, especially in times when scarcity hits.
Purchasing managers should actively work towards building a robust network of reliable suppliers.
By having multiple sources, the odds of being impacted by a single supplier’s disruption are significantly reduced.
Moreover, diversifying geographically can also protect against region-specific disturbances, like natural disasters or political unrest, which can delay supplies from specific locations.
Long-term Partnerships and Agreements
Building long-term partnerships with suppliers can ensure a more resilient supply chain.
These partnerships often come with agreements that prioritize consistent supply and can sometimes lock in prices to guard against volatility.
Establishing solid relationships can also lead to more transparency and communication, allowing purchasers to forecast potential issues and plan accordingly.
Such agreements can incentivize suppliers to allocate resources and prioritize deliveries to long-term partners even in times of scarcity.
Inventory Management and Just-in-Time Production
Effective inventory management can buffer the impact of supplier shortages.
While ‘just-in-time’ production systems can reduce waste and increase efficiency, there’s inherent risk if suppliers cannot deliver on time.
Purchasing managers should assess the feasibility of increasing buffer stocks or safety stocks for critical components.
Although this may involve higher holding costs, it safeguards against production halts due to delayed supplies.
Balancing inventory levels with cost considerations is key to striking a sustainable chord.
The Role of Technology and Data Analytics
Technology and data analytics also play a pivotal role in addressing supplier shortages.
Implementing advanced technologies like AI and machine learning can offer predictive analytics that forewarns of potential shortages and optimizes procurement strategies.
By analyzing usage patterns, demand forecasts, and supplier performance, purchasing managers can make informed decisions to preempt supply chain disruptions.
Leveraging Digital Solutions
Digital platforms that connect buyers with a global network of suppliers provide visibility into available resources, enabling a quick pivot when current supplies run low.
These platforms can automate purchasing processes and streamline communications with suppliers, cutting down on lead times and enhancing efficiency.
This digital transformation makes supply chains more agile, allowing purchasing managers to respond swiftly to changing market conditions.
Risk Management and Scenario Planning
Proactively managing risks through scenario planning can prepare purchasing managers for supplier shortages.
By evaluating potential risks and mapping out contingency plans, managers can ensure that their teams are ready to implement alternative strategies swiftly.
Scenario planning involves simulating various shortage scenarios and assessing the impact on the supply chain, followed by developing actionable steps to minimize disruption.
Conclusion: Navigating Through Supplier Shortages
In conclusion, addressing supplier shortages in the aviation industry requires a comprehensive approach, focusing on diversification, strategic partnerships, and leveraging technology.
The role of purchasing managers in navigating these challenges cannot be underestimated.
By implementing strategic measures and adopting a forward-thinking mindset, they can mitigate risks and ensure continued operations within the aviation sector.
As the industry evolves, staying agile and adapting to change will be crucial for overcoming future supply chain disruptions.
資料ダウンロード
QCD管理受発注クラウド「newji」は、受発注部門で必要なQCD管理全てを備えた、現場特化型兼クラウド型の今世紀最高の受発注管理システムとなります。
ユーザー登録
受発注業務の効率化だけでなく、システムを導入することで、コスト削減や製品・資材のステータス可視化のほか、属人化していた受発注情報の共有化による内部不正防止や統制にも役立ちます。
NEWJI DX
製造業に特化したデジタルトランスフォーメーション(DX)の実現を目指す請負開発型のコンサルティングサービスです。AI、iPaaS、および先端の技術を駆使して、製造プロセスの効率化、業務効率化、チームワーク強化、コスト削減、品質向上を実現します。このサービスは、製造業の課題を深く理解し、それに対する最適なデジタルソリューションを提供することで、企業が持続的な成長とイノベーションを達成できるようサポートします。
製造業ニュース解説
製造業、主に購買・調達部門にお勤めの方々に向けた情報を配信しております。
新任の方やベテランの方、管理職を対象とした幅広いコンテンツをご用意しております。
お問い合わせ
コストダウンが利益に直結する術だと理解していても、なかなか前に進めることができない状況。そんな時は、newjiのコストダウン自動化機能で大きく利益貢献しよう!
(β版非公開)