- お役立ち記事
- Supply chain optimization tips for aerospace procurement departments
Supply chain optimization tips for aerospace procurement departments
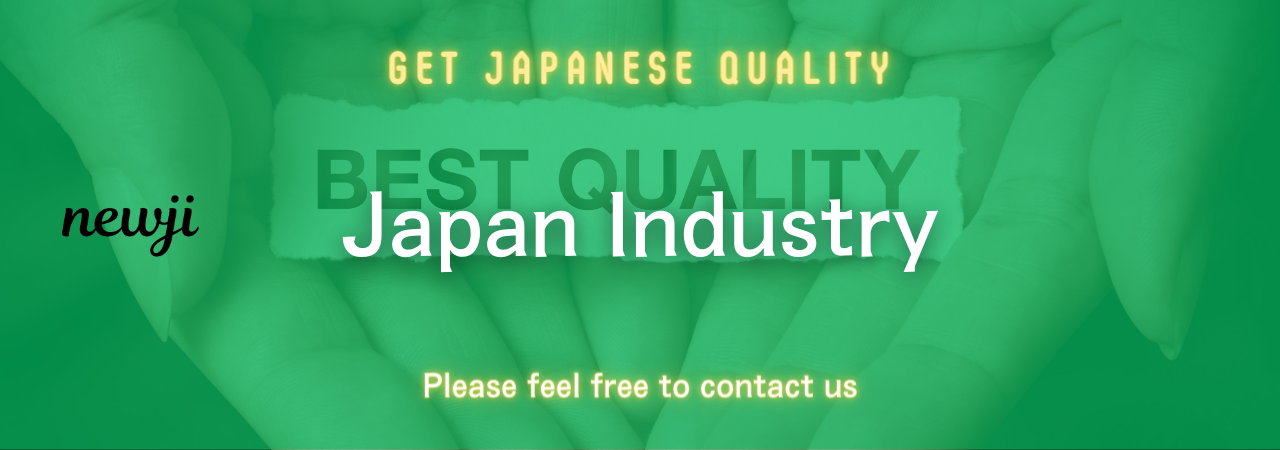
目次
Understanding the Basics of Supply Chain Optimization
Supply chain optimization is a critical process for any aerospace procurement department aiming to improve efficiency and reduce costs.
It involves the strategic management of resources, technologies, and information across the supply chain to ensure that products are delivered as efficiently as possible.
By optimizing a supply chain, aerospace companies can better manage suppliers, reduce lead times, minimize inventory costs, and enhance overall operational performance.
When supply chain operations are streamlined, the entire procurement process becomes more agile and responsive to changing market conditions.
Identifying Key Challenges in Aerospace Supply Chains
The aerospace sector faces unique challenges due to the complexity and precision required in operations.
Key challenges include long lead times, high production costs, regulatory requirements, and the necessity for rigorous quality control.
Supply chain disruptions, such as delays in material supply or quality issues, can significantly affect production schedules and costs.
Additionally, the global nature of aerospace supply chains means that external factors like geopolitical instability or natural disasters can impact operations.
To address these challenges, procurement departments must implement robust risk management strategies and develop strong relationships with reliable suppliers.
Leveraging Technology for Supply Chain Optimization
Technological advancements have introduced powerful tools that can transform supply chain operations.
Automation and data analytics play prominent roles in enhancing supply chain efficiency.
Automated systems can streamline routine processes like order management and inventory tracking, freeing up human resources for more strategic tasks.
Data analytics help procurement professionals gain deep insights into supplier performance, demand forecasting, and market trends.
By leveraging these insights, aerospace procurement departments can make informed decisions to optimize operations.
Incorporating advanced technologies like AI and machine learning can further enhance supply chain optimization by predicting disruptions and identifying cost-saving opportunities.
Implementing Strategic Supplier Management
Supplier management is a crucial aspect of supply chain optimization within aerospace procurement.
Building strong relationships with suppliers ensures timely delivery of materials and components essential for production.
Procurement departments should focus on developing partnerships rather than transactional relationships with suppliers.
This approach provides a more collaborative environment where both parties work towards common goals, such as improving quality and reducing costs.
Implementing performance metrics and regular supplier evaluations can help maintain high standards and address issues proactively.
Moreover, diversifying the supplier base can mitigate risks associated with dependency on a single supplier.
Emphasizing the Importance of Inventory Management
Effective inventory management is vital for keeping the supply chain optimized in the aerospace industry.
Overstocking can lead to increased holding costs, while understocking can cause production delays.
By employing accurate demand forecasting and real-time inventory tracking, procurement departments can ensure optimal inventory levels.
Implementing a just-in-time (JIT) inventory system can further reduce waste and improve cost-effectiveness.
JIT helps align production schedules closely with demand, reducing the excess inventory that can tie up capital.
Integrated digital systems can provide visibility across the supply chain, facilitating better inventory control.
Ensuring Compliance and Quality Assurance
Aerospace products must meet strict regulatory standards and quality requirements, making compliance and quality assurance key concerns for procurement departments.
Ensuring that suppliers adhere to industry standards is paramount for maintaining product integrity and safety.
Procurement professionals should implement rigorous quality checks and assessments as part of the supplier selection process.
Developing a comprehensive quality management system that monitors and evaluates the quality of materials and finished products is essential.
Regular audits and certifications may be necessary to ensure ongoing compliance with regulations, thereby minimizing the risk of non-conformance.
Optimizing Logistics and Transportation
Logistics and transportation are pivotal components of the aerospace supply chain.
Streamlining these components can lead to significant cost reductions and efficiency improvements.
Procurement departments should analyze shipping routes, lead times, and transportation modes to identify areas for optimization.
Using advanced logistics software can provide valuable insights and recommend cost-effective solutions.
Additionally, strategic partnerships with logistics providers can optimize freight management and improve delivery reliability.
By reducing transportation costs and improving delivery times, aerospace companies can enhance customer satisfaction and remain competitive.
The Role of Continuous Improvement
The journey of supply chain optimization does not end with initial improvements.
Aerospace procurement departments must embrace a culture of continuous improvement to stay ahead in a dynamic industry.
Regularly reviewing supply chain processes and performance metrics helps identify new areas for enhancement.
Employing techniques like Six Sigma and Lean management can support the pursuit of continuous improvement by focusing on eliminating waste and enhancing quality.
By fostering an environment of innovation and adaptability, aerospace companies can ensure their supply chains remain efficient and resilient.
Conclusion
Supply chain optimization is a vital undertaking for aerospace procurement departments aiming to excel in a competitive industry.
By understanding the unique challenges faced, leveraging technology, managing suppliers strategically, and focusing on inventory and logistics management, procurement departments can achieve substantial improvements.
Emphasizing compliance, quality assurance, and fostering a culture of continuous improvement are key to maintaining an optimized supply chain.
Through these efforts, aerospace companies can ensure efficient operations, cost savings, and high customer satisfaction.
資料ダウンロード
QCD調達購買管理クラウド「newji」は、調達購買部門で必要なQCD管理全てを備えた、現場特化型兼クラウド型の今世紀最高の購買管理システムとなります。
ユーザー登録
調達購買業務の効率化だけでなく、システムを導入することで、コスト削減や製品・資材のステータス可視化のほか、属人化していた購買情報の共有化による内部不正防止や統制にも役立ちます。
NEWJI DX
製造業に特化したデジタルトランスフォーメーション(DX)の実現を目指す請負開発型のコンサルティングサービスです。AI、iPaaS、および先端の技術を駆使して、製造プロセスの効率化、業務効率化、チームワーク強化、コスト削減、品質向上を実現します。このサービスは、製造業の課題を深く理解し、それに対する最適なデジタルソリューションを提供することで、企業が持続的な成長とイノベーションを達成できるようサポートします。
オンライン講座
製造業、主に購買・調達部門にお勤めの方々に向けた情報を配信しております。
新任の方やベテランの方、管理職を対象とした幅広いコンテンツをご用意しております。
お問い合わせ
コストダウンが利益に直結する術だと理解していても、なかなか前に進めることができない状況。そんな時は、newjiのコストダウン自動化機能で大きく利益貢献しよう!
(Β版非公開)