- お役立ち記事
- Benefits of component standardization for purchasing leaders in the manufacturing industry
Benefits of component standardization for purchasing leaders in the manufacturing industry
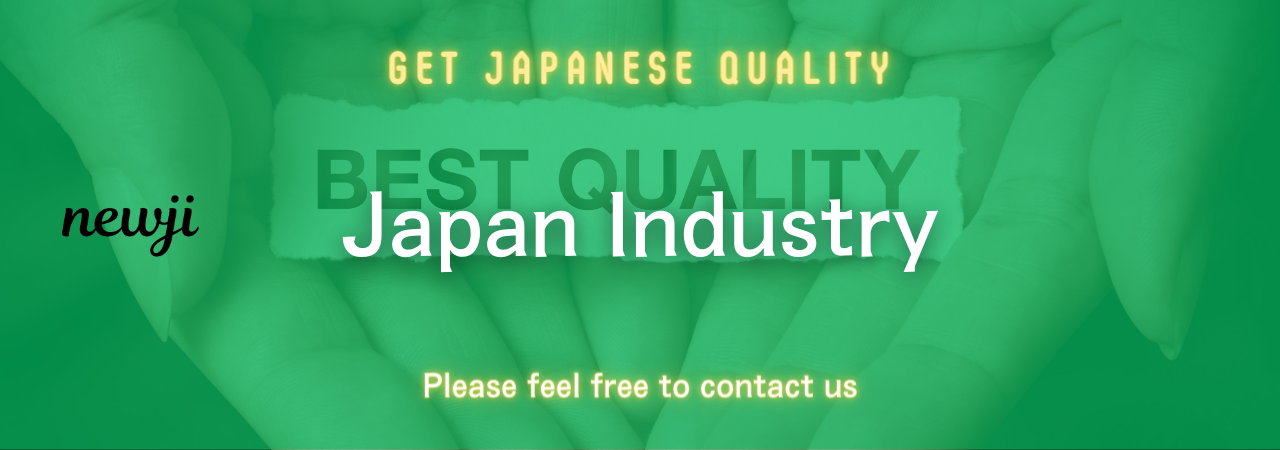
目次
Understanding Component Standardization
Component standardization is a strategic approach used by manufacturing industries to streamline their processes and reduce complexity in production.
It involves using uniform components across different products to simplify procurement, reduce costs, and enhance interoperability.
For purchasing leaders, understanding and implementing component standardization can result in significant operational improvements and cost savings, making it a crucial area of focus in modern manufacturing.
Why Component Standardization Matters
In today’s competitive market, manufacturing firms are constantly seeking ways to optimize their operations and reduce expenses.
Component standardization serves as an effective strategy to achieve these aims.
By standardizing components, companies can purchase in bulk, leverage economies of scale, and reduce waste.
Furthermore, standardized components simplify supply chains and minimize the complexity involved in managing multiple parts inventory.
For purchasing leaders, this standardization means fewer headaches when dealing with suppliers.
They can select fewer suppliers to meet their component needs, streamlining the ordering process and building stronger supplier relationships.
This efficiency not only saves time but also helps in negotiating better prices.
Cost Benefits of Standardization
One of the most tangible benefits of component standardization is cost reduction.
Purchasing leaders can significantly lower procurement costs by buying larger quantities of fewer parts.
Bulk purchases often come with discounts, which can lead to substantial savings over time.
Moreover, standardization reduces the need for specialized parts production.
This reduction cuts down on manufacturing costs as the company can rely on standardized, mass-produced components rather than custom-made parts.
This benefit extends to labor costs as well, as standardized components often require less customization and assembly time on the production line.
Improved Product Quality and Reliability
Standardized components are typically well-tested and proven to perform reliably across different applications.
This reliability contributes to higher overall product quality, which is a key selling point in any industry.
For purchasing leaders, ensuring component reliability means fewer product returns and issues, which ultimately enhances customer satisfaction and brand reputation.
Additionally, standardized components often come from reputable suppliers with established quality control processes.
This quality assurance gives companies confidence in the components they use, reducing the risk of product failure and the subsequent costs of warranty claims or recalls.
Simplified Supply Chain Management
By reducing the number of different parts needed, component standardization simplifies supply chain management.
Purchasing leaders enjoy a more straightforward procurement process, with fewer points of failure in their supply chain.
This simplification also improves inventory management, as there are fewer item variations to track and control.
Standardization can also enhance supplier relationships.
With fewer suppliers to manage, purchasing leaders can develop stronger partnerships, fostering better communication, collaboration, and negotiation power.
These relationships can lead to more favorable terms and priority service when urgent needs arise.
Faster Time to Market
In the fast-paced manufacturing industry, time to market is crucial.
Component standardization allows for quicker product development and production cycles.
With a standardized set of components, designers and engineers can spend less time sourcing and integrating new parts, accelerating the development process.
Moreover, this approach allows manufacturing companies to respond more swiftly to market demands and changes.
When a new product is launched, leveraging existing, standardized components can drastically reduce preparation time and expedite the production phase.
Environmental and Sustainability Benefits
Standardizing components can also contribute to a company’s sustainability efforts.
Using fewer component types reduces waste, as there is less need for different materials and less packaging in transit.
This reduction aligns with growing consumer and industry demands for environmentally responsible practices.
Moreover, by optimizing production lines to work more efficiently with standardized components, energy consumption is reduced.
Companies can lower their carbon footprint, while often enjoying reduced utility costs associated with streamlined operations.
Strategic Implications for Purchasing Leaders
For purchasing leaders, embracing component standardization involves strategic planning and implementation.
It requires evaluating which components can be standardized without compromising product integrity or innovation.
Leaders must also consider the implications for supplier selection, quality control, and contractual arrangements.
Implementing component standardization may necessitate internal adjustments such as retraining staff or reassessing inventory systems.
However, with careful planning and execution, the rewards in terms of efficiency, cost savings, and quality improvements far outweigh the initial efforts.
Conclusion
Component standardization stands as a powerful tool for purchasing leaders in the manufacturing industry.
By leveraging its benefits, companies can enjoy reduced costs, improved product quality, simplified supply chains, and faster time to market.
Additionally, the environmental benefits of such an approach can align with corporate sustainability goals, further enhancing brand reputation in the eyes of consumers.
Purchasing leaders play a pivotal role in driving this standardization, requiring them to be strategic and forward-thinking.
With the right approach, component standardization can serve as a cornerstone of operational success and sustainability for manufacturing firms, now and in the future.
資料ダウンロード
QCD調達購買管理クラウド「newji」は、調達購買部門で必要なQCD管理全てを備えた、現場特化型兼クラウド型の今世紀最高の購買管理システムとなります。
ユーザー登録
調達購買業務の効率化だけでなく、システムを導入することで、コスト削減や製品・資材のステータス可視化のほか、属人化していた購買情報の共有化による内部不正防止や統制にも役立ちます。
NEWJI DX
製造業に特化したデジタルトランスフォーメーション(DX)の実現を目指す請負開発型のコンサルティングサービスです。AI、iPaaS、および先端の技術を駆使して、製造プロセスの効率化、業務効率化、チームワーク強化、コスト削減、品質向上を実現します。このサービスは、製造業の課題を深く理解し、それに対する最適なデジタルソリューションを提供することで、企業が持続的な成長とイノベーションを達成できるようサポートします。
オンライン講座
製造業、主に購買・調達部門にお勤めの方々に向けた情報を配信しております。
新任の方やベテランの方、管理職を対象とした幅広いコンテンツをご用意しております。
お問い合わせ
コストダウンが利益に直結する術だと理解していても、なかなか前に進めることができない状況。そんな時は、newjiのコストダウン自動化機能で大きく利益貢献しよう!
(Β版非公開)