- お役立ち記事
- Welding Techniques and Their Industrial Uses
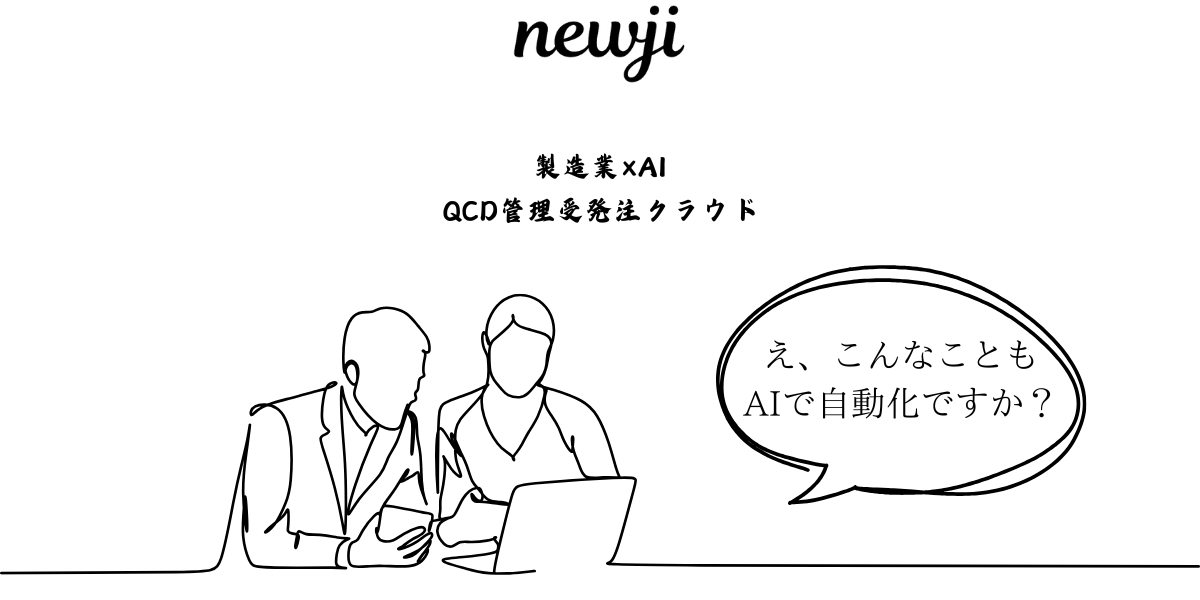
Welding Techniques and Their Industrial Uses
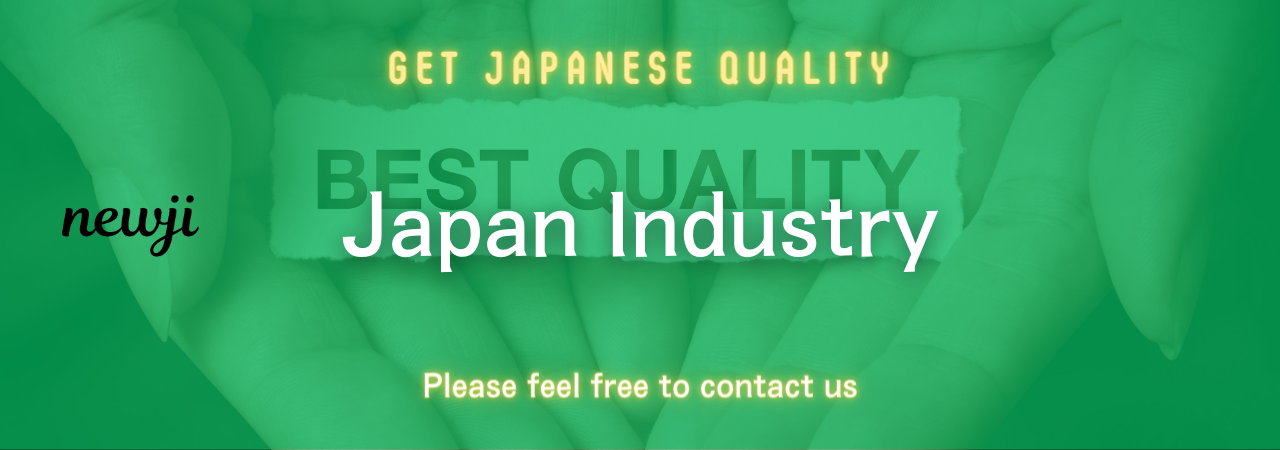
目次
Introduction to Welding
Welding is a critical process in various industries, combining metals to create structures and components that are both strong and durable.
Wherever you look—from towering skyscrapers to tiny electronic gadgets—welding is at the heart of their construction.
It plays an essential role in manufacturing, construction, automotive, aerospace, and many other sectors.
Understanding the different techniques of welding and their industrial uses aids in selecting the right method for each specific project.
Basic Welding Techniques
1. Shielded Metal Arc Welding (SMAW)
Shielded Metal Arc Welding, also known as stick welding, is one of the most commonly used types of welding.
It employs a consumable electrode coated with flux to lay the weld.
This technique is popular because of its simplicity and versatility, making it suitable for outdoor settings and on-site work.
SMAW is often used in construction, maintenance, and repair work due to its ability to weld in almost any condition.
2. Gas Metal Arc Welding (GMAW)
Gas Metal Arc Welding, or MIG welding, uses a wire feeding gun that constantly feeds wire and gas through a nozzle to create the weld.
This process is semi-automatic or fully automatic, which makes it quicker and less expensive than many other welding techniques.
GMAW is ideal for welding thin to medium thickness metal pieces and is widely used in automotive industries and for fabrication of metal structures.
3. Gas Tungsten Arc Welding (GTAW)
Gas Tungsten Arc Welding, also known as TIG welding, uses a non-consumable tungsten electrode to produce the weld.
This method provides a very high weld quality and is capable of welding a wide variety of metals, including stainless steel and non-ferrous metals like aluminum.
TIG welding is precision-oriented and is often used in industries where high standards of clean welds and utmost precision are required, such as aerospace and automotive engine manufacturing.
Advanced Welding Techniques
1. Flux-Cored Arc Welding (FCAW)
Flux-Cored Arc Welding is similar to MIG welding but uses a special tubular wire filled with flux.
This method is particularly advantageous for projects requiring deep weld penetration.
It is especially useful in industrial settings, for construction, and for heavy-duty repair work.
The flux-cored process can be performed outdoors and in windy environments, making it versatile.
2. Submerged Arc Welding (SAW)
Submerged Arc Welding involves forming an arc between a continuously fed electrode and the workpiece while the weld area is submerged under a blanket of granular fusible flux.
This process is efficient due to the deep penetration and high speed it offers.
SAW is extensively used in shipbuilding, large machine construction, and heavy equipment production.
3. Laser Beam Welding (LBW)
Laser Beam Welding utilizes a laser to join multiple pieces of metal through its concentrated energy, which produces high-quality, deep welds.
This technique is valuable for its precision and the ability to weld small, intricate parts without causing distortion.
LBW is prevalent in the automotive industry and electronics manufacturing for precision assemblies.
Industrial Applications of Welding
Manufacturing Industry
The manufacturing sector heavily relies on welding for fabricating a multitude of products from automobiles to home appliances.
Each welding technique accommodates different types of material and specifications, ensuring robust production standards.
Construction Industry
Welding is fundamental in the construction industry for erecting homes, buildings, bridges, and highways.
SMAW and FCAW are particularly favored due to their adaptability to different environments and conditions found on construction sites.
Automotive Industry
In the automotive industry, welding is instrumental in assembling frames, exhaust systems, and various other components.
GMAW and LBW are employed for their speed and accuracy, producing high-quality welds necessary for vehicle integrity.
Aerospace Industry
Within the aerospace field, highly precise welding is a must.
GTAW shines in this area due to its excellent control, making it suitable for spacecraft and aircraft engineering where perfect seams and joints are non-negotiable.
Challenges and Future of Welding
While welding is indispensable, it faces challenges such as ensuring high-quality welds, adapting to new materials, and maintaining safety standards.
Advancements in automation and robotics are transforming the field, increasing efficiency and accuracy in welding operations.
Moreover, the continued development of new materials and technologies promises to refine traditional techniques and usher in innovative practices for future projects.
Conclusion
Welding remains a cornerstone in industrial production and construction, with each technique offering specific advantages suited for particular applications.
From fundamental methods like SMAW and GMAW to advanced techniques like LBW, understanding their industrial uses ensures appropriate choices in diverse projects.
As technology evolves, so too will welding processes, continuing to support and advance industries worldwide.
資料ダウンロード
QCD調達購買管理クラウド「newji」は、調達購買部門で必要なQCD管理全てを備えた、現場特化型兼クラウド型の今世紀最高の購買管理システムとなります。
ユーザー登録
調達購買業務の効率化だけでなく、システムを導入することで、コスト削減や製品・資材のステータス可視化のほか、属人化していた購買情報の共有化による内部不正防止や統制にも役立ちます。
NEWJI DX
製造業に特化したデジタルトランスフォーメーション(DX)の実現を目指す請負開発型のコンサルティングサービスです。AI、iPaaS、および先端の技術を駆使して、製造プロセスの効率化、業務効率化、チームワーク強化、コスト削減、品質向上を実現します。このサービスは、製造業の課題を深く理解し、それに対する最適なデジタルソリューションを提供することで、企業が持続的な成長とイノベーションを達成できるようサポートします。
オンライン講座
製造業、主に購買・調達部門にお勤めの方々に向けた情報を配信しております。
新任の方やベテランの方、管理職を対象とした幅広いコンテンツをご用意しております。
お問い合わせ
コストダウンが利益に直結する術だと理解していても、なかなか前に進めることができない状況。そんな時は、newjiのコストダウン自動化機能で大きく利益貢献しよう!
(Β版非公開)