- お役立ち記事
- Bottleneck Processing Techniques
月間77,185名の
製造業ご担当者様が閲覧しています*
*2025年2月28日現在のGoogle Analyticsのデータより
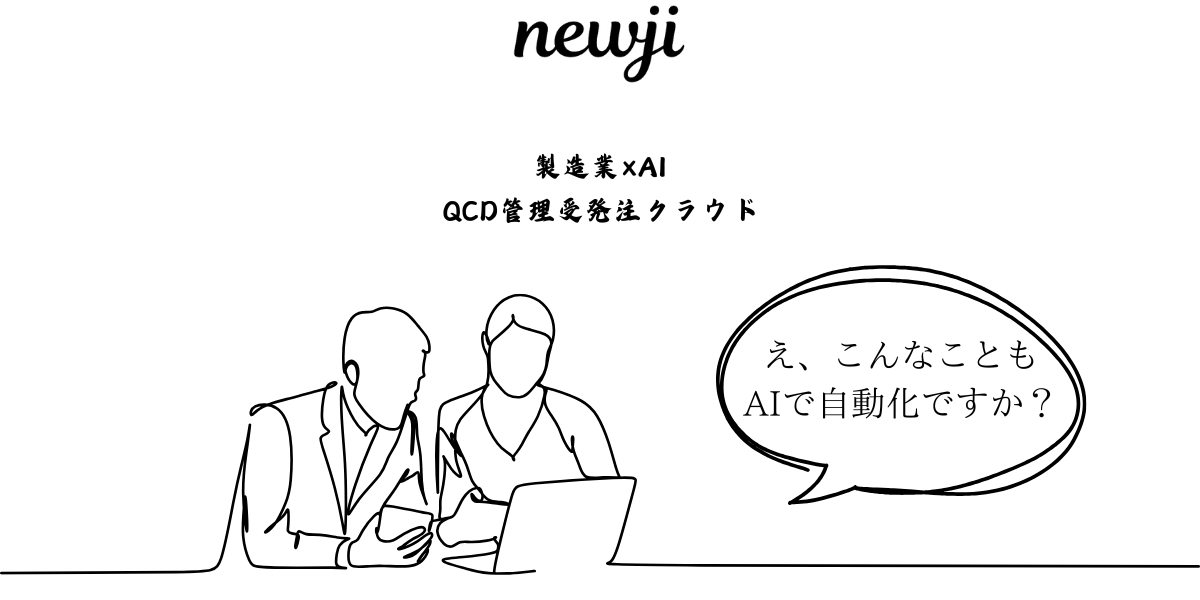
Bottleneck Processing Techniques
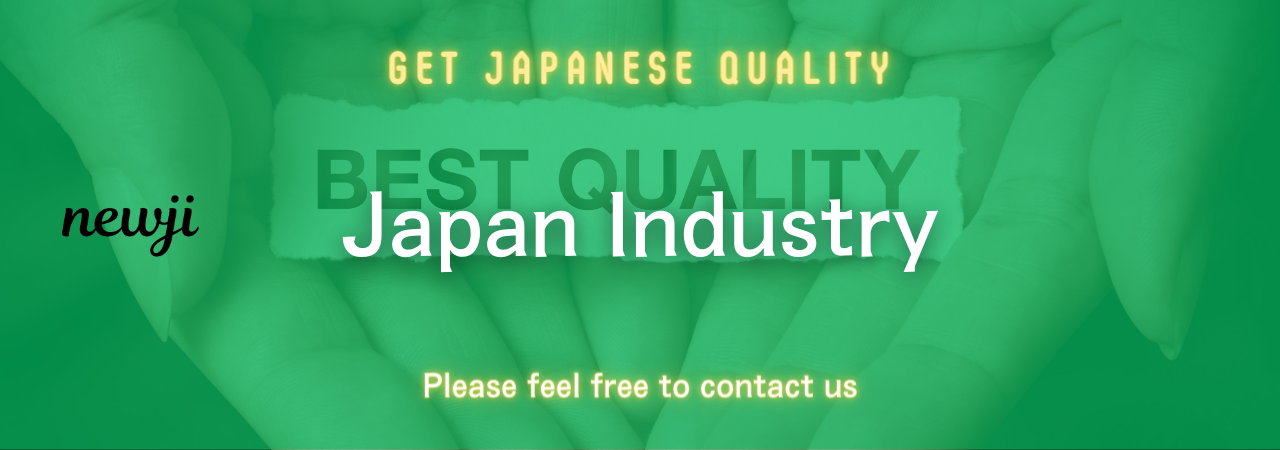
目次
Understanding Bottleneck Processing
Bottleneck processing refers to identifying obstacles or slow points in a workflow and finding ways to resolve them.
In any system, a bottleneck can significantly hinder productivity and efficiency.
The term “bottleneck” compares the constricted neck of a bottle, where liquid flow is slowed, to points in a process that limit throughput.
When a bottleneck occurs, it creates a chain reaction, slowing down subsequent tasks and causing delays.
Identifying bottlenecks is the first critical step to optimizing performance.
Often, managers and team leaders rely on visual tools such as flowcharts and diagrams to pinpoint these slowdowns.
Additionally, analyzing data through time studies and measuring key performance indicators (KPIs) provides quantitative evidence of where efficiencies may be lacking.
Common Causes of Bottlenecks
Bottlenecks can arise from several sources within a process.
Understanding these causes can help businesses find effective solutions.
Lack of Resources
One primary cause of bottlenecks is the shortage of essential resources.
This can include inadequate staffing, an insufficient supply of materials, or outdated machinery.
When resources are lacking, work halts, and productivity diminishes.
Ensuring that necessary resources are available is crucial for smooth operations.
Inefficient Workflow Design
Workflows that are poorly structured or not well-thought-out can become prone to bottlenecks.
If work is routed through unnecessary or cumbersome steps, it can slow down the overall process.
Regularly evaluating and optimizing workflow design can help eliminate unnecessary tasks and streamline the process.
High Variability in Task Times
Significant variations in how long it takes to complete tasks are another reason for bottlenecks.
When certain tasks take much longer than others, they can create a backlog.
Implementing standardized procedures or training to ensure uniform task completion times can alleviate this issue.
Communication Gaps
Lack of communication between team members, departments, or stakeholders can also lead to bottlenecks.
When clear, timely communication is missing, errors or misalignments can occur, causing delays in execution.
Improving communication channels and standards can greatly reduce these gaps.
Techniques to Address Bottleneck Processing
Once a bottleneck has been identified, various techniques can be employed to address the issue.
These techniques aim to increase throughput and improve overall efficiency.
Task Prioritization
Prioritizing tasks effectively can help manage workload and reduce bottleneck effects.
By identifying the most critical tasks, resources can be allocated accordingly to ensure that these are completed first.
This approach supports a smoother flow of work and prevents pile-ups of less crucial tasks.
Resource Allocation
Balancing resources effectively addresses bottlenecks caused by shortages.
This may involve hiring additional staff, cross-training employees to handle multiple tasks, or upgrading equipment.
The goal is to ensure that essential resources are always available to maintain a steady flow of work.
Process Automation
Introducing automation into a workflow can significantly ease bottleneck pressures.
Automation software can handle repetitive and time-consuming tasks, freeing up human resources for more complex activities.
Automating processes not only speeds up work but also minimizes human error, leading to more efficient operations.
Continuous Process Improvement
Strive for ongoing process improvement through methodologies such as Lean, Six Sigma, or Total Quality Management (TQM).
These frameworks focus on continuous assessment and enhancement of processes.
By actively seeking out inefficiencies and implementing iterative improvements, organizations can better manage bottlenecks and achieve higher efficiency levels.
Monitoring and Maintaining Workflow Efficiency
Monitoring and maintaining an efficient workflow is an ongoing task.
Regularly reviewing processes with a critical eye can prevent future bottlenecks.
Utilizing Performance Metrics
Setting up KPIs and other performance metrics helps track the efficiency of the workflow.
Metrics like cycle time, throughput, and yield can give a clear picture of where bottlenecks might exist.
Consistent monitoring ensures that potential issues are identified before they develop into serious bottlenecks.
Feedback Mechanisms
Creating channels for team feedback is essential in maintaining efficiency.
Employees directly involved in processes can offer invaluable insights into areas needing attention.
Feedback helps identify hidden bottlenecks and enables managers to make informed decisions for improvements.
Regular Audits
Conducting regular audits on workflows and processes can uncover inefficiencies that lead to bottlenecks.
Audits assess every step in a process to ensure each one adds value and operates effectively.
Regular reviews allow companies to adapt to changes and find innovative solutions for ongoing challenges.
The Benefits of Effective Bottleneck Management
Effectively managing bottlenecks leads to numerous advantages for any organization.
Increased Productivity
When bottlenecks are minimized, work moves through the system quickly and efficiently.
Increased throughput results in higher productivity rates, allowing the organization to achieve more in less time.
Improved Customer Satisfaction
Efficient processes mean timelier deliveries and a higher quality of service, leading to satisfied customers.
When customer expectations are met or exceeded, it fosters loyalty and positive brand reputation.
Cost Savings
Reducing bottlenecks often leads to cost savings through more efficient use of resources and less waste.
Streamlined operations cut down on unnecessary expenses, boosting the company’s bottom line.
Bottleneck processing requires careful observation, analysis, and action.
Through understanding and implementing these techniques, businesses can promote smoother workflows and achieve their performance goals.
資料ダウンロード
QCD管理受発注クラウド「newji」は、受発注部門で必要なQCD管理全てを備えた、現場特化型兼クラウド型の今世紀最高の受発注管理システムとなります。
ユーザー登録
受発注業務の効率化だけでなく、システムを導入することで、コスト削減や製品・資材のステータス可視化のほか、属人化していた受発注情報の共有化による内部不正防止や統制にも役立ちます。
NEWJI DX
製造業に特化したデジタルトランスフォーメーション(DX)の実現を目指す請負開発型のコンサルティングサービスです。AI、iPaaS、および先端の技術を駆使して、製造プロセスの効率化、業務効率化、チームワーク強化、コスト削減、品質向上を実現します。このサービスは、製造業の課題を深く理解し、それに対する最適なデジタルソリューションを提供することで、企業が持続的な成長とイノベーションを達成できるようサポートします。
製造業ニュース解説
製造業、主に購買・調達部門にお勤めの方々に向けた情報を配信しております。
新任の方やベテランの方、管理職を対象とした幅広いコンテンツをご用意しております。
お問い合わせ
コストダウンが利益に直結する術だと理解していても、なかなか前に進めることができない状況。そんな時は、newjiのコストダウン自動化機能で大きく利益貢献しよう!
(β版非公開)