- お役立ち記事
- A method to improve procurement efficiency by standardizing parts in the auto parts manufacturing industry
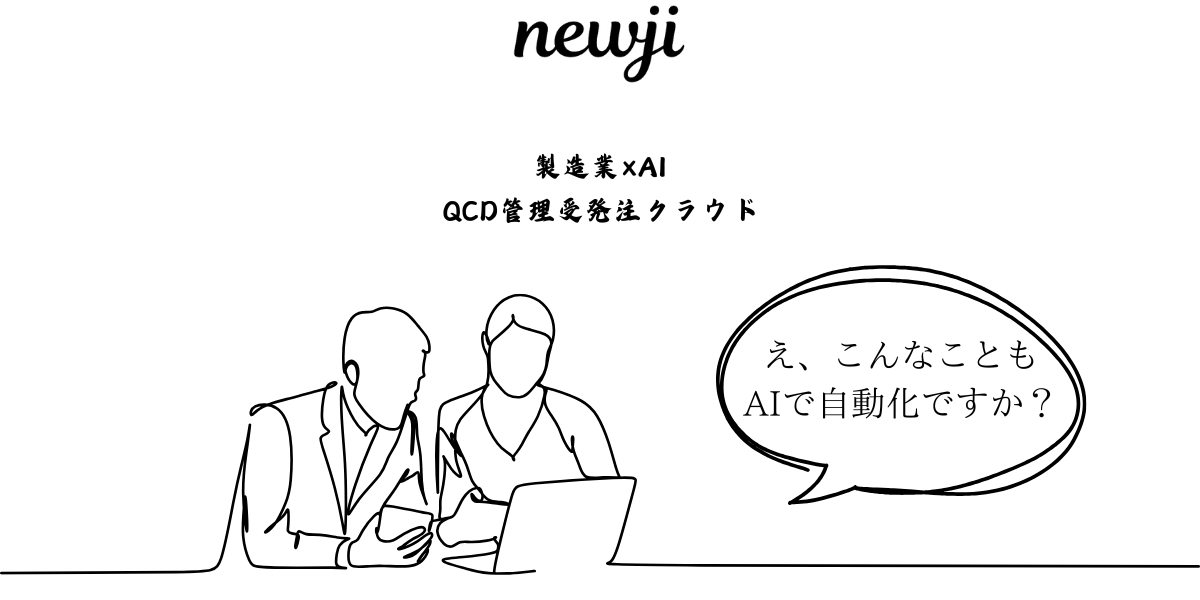
A method to improve procurement efficiency by standardizing parts in the auto parts manufacturing industry
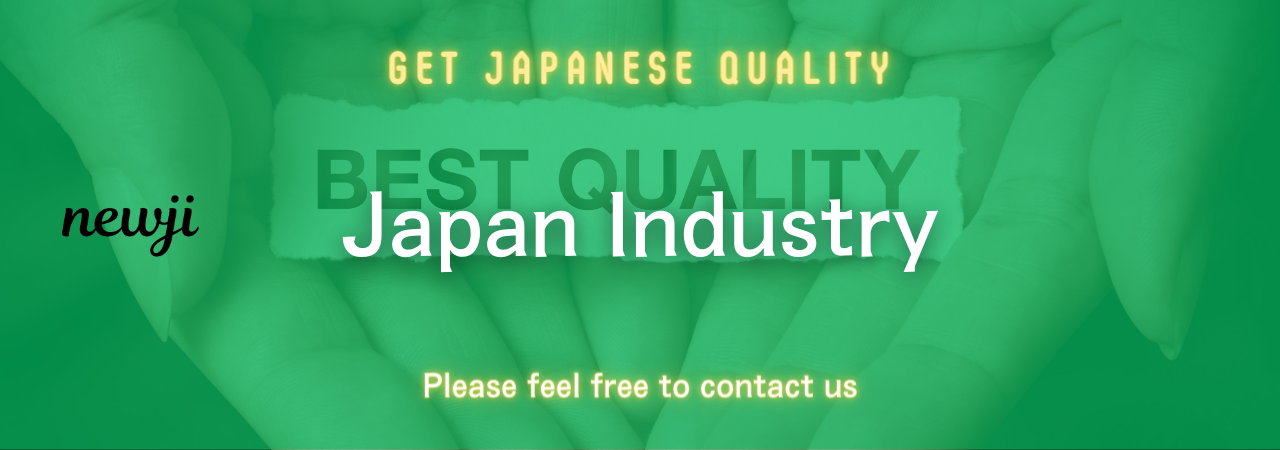
目次
Introduction to Procurement in Auto Parts Manufacturing
Procurement in the auto parts manufacturing industry is a complex process that involves purchasing various materials and components necessary for vehicle production.
The efficiency of procurement directly impacts the overall productivity and cost-effectiveness of manufacturing operations.
One way to enhance procurement efficiency is by standardizing parts, which helps streamline operations, reduce costs, and improve supply chain performance.
In this article, we’ll explore how standardizing parts can improve procurement efficiency in the auto parts manufacturing industry.
Understanding the Role of Standardization
At its core, standardization involves creating and implementing uniform specifications and guidelines for parts used in manufacturing.
In the auto parts industry, this means developing a set of universal standards for components, which ensures consistency in quality and compatibility.
By adhering to these standards, auto parts manufacturers can achieve several benefits, including reduced production times, lower inventory costs, and fewer errors during assembly.
Standardization fosters better collaboration among suppliers, manufacturers, and stakeholders in the supply chain.
Benefits of Standardization in Procurement
One of the significant advantages of standardizing parts is cost reduction.
With uniform parts, manufacturers can buy in bulk, which lowers the cost per unit due to economies of scale.
Additionally, standardized parts simplify the sourcing process, reducing the time and effort needed to procure components.
This streamlined approach allows procurement teams to negotiate better terms with suppliers and can lead to more favorable prices.
Having a standardized inventory also decreases warehousing costs as the volume and variety of parts that need to be stored are minimized.
Another benefit is improved product quality and reliability.
Standardized components ensure that only parts meeting specific quality criteria are used in production, lowering the risk of defects during manufacturing.
As a result, the final products are more reliable, which enhances customer satisfaction and brand reputation.
Furthermore, standardization aids in maintenance and repairs by ensuring that replacement parts are readily available and consistent, minimizing downtime.
Implementing Standardization in the Auto Parts Manufacturing Industry
Introducing standardization in an established manufacturing process may seem daunting, but with a structured approach, it can be effectively achieved.
The first step is to conduct a thorough analysis of the current procurement process to identify areas where standardization could be beneficial.
This involves assessing the variety of parts used and understanding the specifications that can be unified.
Collaborating with Suppliers and Stakeholders
Engaging with suppliers and stakeholders early in the standardization process is crucial.
Collaboration ensures that the parts selected for standardization are feasible and that suppliers can meet the required specifications consistently.
Open communication helps in building strong relationships with suppliers, leading to a more resilient supply chain.
It’s also essential to involve design and engineering teams to ensure that the standardized parts do not compromise the functionality, design, or performance of the final product.
Once standardized parts are identified, the next step is to update procurement policies and systems to support the adoption of these standards.
This may involve revising contracts, updating inventory management systems, and training staff to adhere to new procedures.
Implementing digital solutions, like procurement software, can also assist in managing the transition efficiently by automating processes and providing better visibility into inventory levels and supplier performance.
Monitoring and Continuous Improvement
After implementing standardization, continuous monitoring of the process is vital to ensure success.
Regular audits and performance reviews help identify any issues or deviations from the standards.
Gathering data on procurement efficiency, cost savings, and product quality provides insights into areas for further improvement.
Feedback from all stakeholders, including suppliers, production teams, and customers, should be considered to refine the standardization process continuously.
Challenges and Considerations
Despite the many advantages, standardizing parts in the auto parts manufacturing industry comes with its challenges.
One significant challenge is the resistance to change.
Employees and suppliers may be accustomed to existing processes, and shifting to standardized parts can meet with reluctance.
Overcoming this requires effective change management strategies, including clear communication of the benefits and adequate training for all involved.
Another consideration is the potential impact on innovation and customization.
While standardization is beneficial, it should not stifle innovation or prevent the development of new, customized products when necessary.
A balance must be maintained between standardization and the ability to adapt to evolving customer needs and technological advancements.
Conclusion
Standardizing parts can significantly improve procurement efficiency in the auto parts manufacturing industry by reducing costs, enhancing product quality, and streamlining operations.
By engaging with stakeholders, updating procurement systems, and adopting a continuous improvement mindset, manufacturers can successfully implement standardization.
While challenges exist, the long-term benefits of improved efficiency and stronger supplier relationships make standardization a worthwhile pursuit.
As the industry continues to evolve, standardization will remain a critical strategy for achieving competitive advantage and operational excellence.
資料ダウンロード
QCD調達購買管理クラウド「newji」は、調達購買部門で必要なQCD管理全てを備えた、現場特化型兼クラウド型の今世紀最高の購買管理システムとなります。
ユーザー登録
調達購買業務の効率化だけでなく、システムを導入することで、コスト削減や製品・資材のステータス可視化のほか、属人化していた購買情報の共有化による内部不正防止や統制にも役立ちます。
NEWJI DX
製造業に特化したデジタルトランスフォーメーション(DX)の実現を目指す請負開発型のコンサルティングサービスです。AI、iPaaS、および先端の技術を駆使して、製造プロセスの効率化、業務効率化、チームワーク強化、コスト削減、品質向上を実現します。このサービスは、製造業の課題を深く理解し、それに対する最適なデジタルソリューションを提供することで、企業が持続的な成長とイノベーションを達成できるようサポートします。
オンライン講座
製造業、主に購買・調達部門にお勤めの方々に向けた情報を配信しております。
新任の方やベテランの方、管理職を対象とした幅広いコンテンツをご用意しております。
お問い合わせ
コストダウンが利益に直結する術だと理解していても、なかなか前に進めることができない状況。そんな時は、newjiのコストダウン自動化機能で大きく利益貢献しよう!
(Β版非公開)