- お役立ち記事
- Challenges and solutions for new engine parts procurement in the aerospace industry
月間77,185名の
製造業ご担当者様が閲覧しています*
*2025年2月28日現在のGoogle Analyticsのデータより
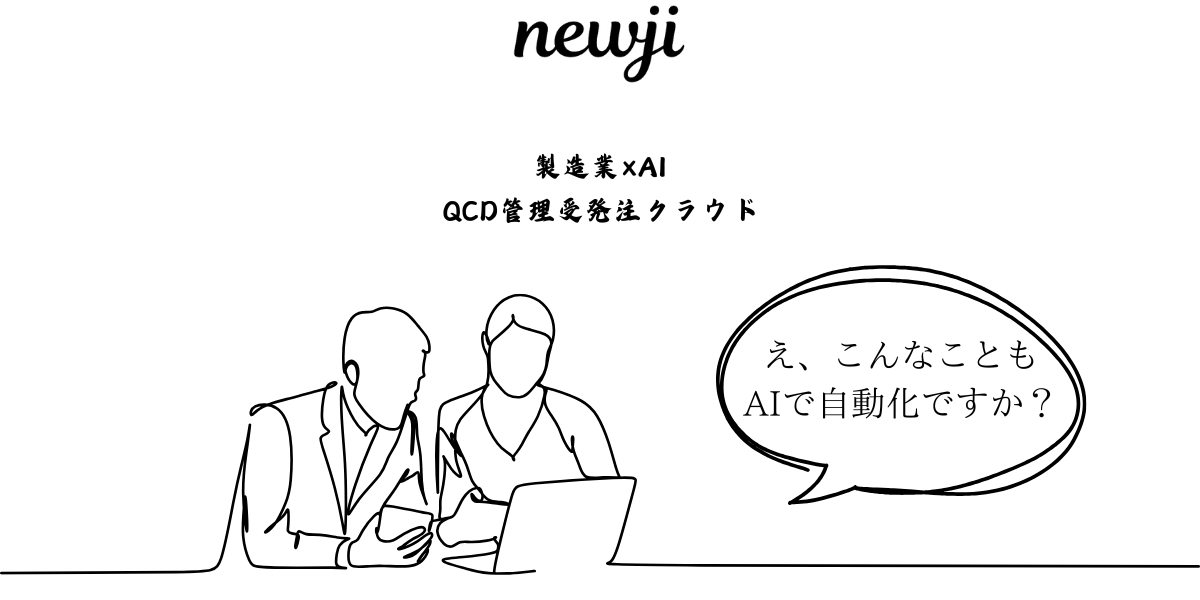
Challenges and solutions for new engine parts procurement in the aerospace industry
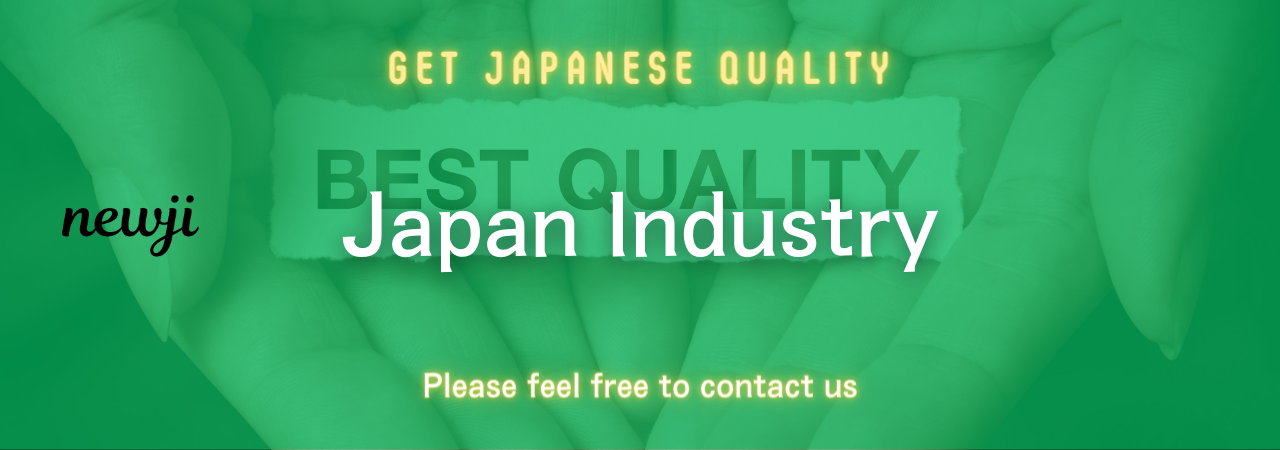
目次
Introduction
The aerospace industry is known for its complexity and innovation, relying heavily on advanced technology and precise engineering.
At the heart of this industry lies new engine parts procurement, a crucial element that ensures aircraft performance and safety.
However, procuring these parts comes with its unique set of challenges.
In this article, we explore these challenges and propose solutions that can enhance the procurement process.
The Importance of Engine Parts Procurement
Engine parts are integral to the functioning of an aircraft.
They contribute to the aircraft’s propulsion, efficiency, and overall safety.
In the aerospace industry, even the smallest malfunction can lead to significant consequences.
Therefore, reliable procurement of quality engine parts is essential.
It’s not just about acquiring parts, but ensuring they meet rigorous standards and compliance requirements.
Key Challenges in Procuring New Engine Parts
Complex Supply Chain
The aerospace supply chain is intricate, involving numerous suppliers and manufacturers worldwide.
Managing this complex network can be daunting.
Coordination and communication are critical, but logistical disruptions, geopolitical issues, and global crises like the COVID-19 pandemic can exacerbate difficulties.
These factors may lead to delays, increased costs, and reduced availability of parts.
Stringent Regulatory Compliance
The aerospace industry is heavily regulated to maintain safety and quality standards.
Procurement teams must ensure that all engine parts comply with these rigorous regulations.
This involves extensive documentation, testing, and certification processes.
Failure to meet these standards can result in severe penalties, including fines and grounding of aircraft.
Technological Advancements
With rapid advancements in technology, aerospace companies must frequently update their procurement strategies.
Integrating new technologies such as 3D printing and artificial intelligence presents opportunities but also challenges.
The procurement teams must stay updated and adapt quickly, which can be resource-intensive.
Supplier Reliability
The reliability of suppliers is crucial for consistent engine parts procurement.
Companies often rely on a limited number of suppliers who can provide specialized components.
Any disruption in the supplier’s operation, whether due to economic issues or natural disasters, can lead to a halt in production and delivery schedules.
Solutions to Overcome Procurement Challenges
Streamlining Supply Chain Management
To address the complexities of the supply chain, aerospace companies can leverage digital solutions.
Utilizing supply chain management software can improve visibility and coordination among stakeholders.
Implementing predictive analytics can help foresee potential disruptions and prepare contingency plans.
Enhancing Regulatory Knowledge
Continuous training and education of procurement teams on regulatory standards are vital.
Partnership with regulatory bodies can help in timely updates about any changes in compliance requirements.
Developing an in-house team of compliance experts can ensure that all parts and processes adhere to necessary standards.
Embracing Technological Innovations
Aerospace companies must invest in the latest technologies to stay competitive.
Adopting 3D printing can localize production, reduce lead times, and customize parts as needed.
Artificial intelligence can automate routine tasks, increase efficiency, and support decision-making by providing data-driven insights.
Diversifying the Supplier Base
Relying on a broader range of suppliers can mitigate risks associated with supplier dependency.
Establishing relationships with multiple suppliers increases options and ensures a steady flow of necessary parts.
Regular audits and assessments can be conducted to ensure supplier reliability and quality.
Collaboration and Industry Partnerships
Aerospace companies can benefit from collaborating with other industry players.
Forming strategic partnerships or alliances can pool resources and expertise.
Such collaborations can lead to joint ventures that enhance the production and distribution of engine parts.
Innovative financing solutions, such as shared investments in research and development, can also reduce costs and foster technological advancements.
Conclusion
The procurement of new engine parts in the aerospace industry is fraught with challenges, ranging from complex supply chains and regulatory compliance to technological and supplier issues.
However, by embracing modern solutions such as digital technologies, continuous education, and strategic collaborations, these challenges can be effectively tackled.
By doing so, aerospace companies can ensure that they maintain high standards of safety and efficiency, paving the way for continued innovation and growth in the industry.
資料ダウンロード
QCD管理受発注クラウド「newji」は、受発注部門で必要なQCD管理全てを備えた、現場特化型兼クラウド型の今世紀最高の受発注管理システムとなります。
ユーザー登録
受発注業務の効率化だけでなく、システムを導入することで、コスト削減や製品・資材のステータス可視化のほか、属人化していた受発注情報の共有化による内部不正防止や統制にも役立ちます。
NEWJI DX
製造業に特化したデジタルトランスフォーメーション(DX)の実現を目指す請負開発型のコンサルティングサービスです。AI、iPaaS、および先端の技術を駆使して、製造プロセスの効率化、業務効率化、チームワーク強化、コスト削減、品質向上を実現します。このサービスは、製造業の課題を深く理解し、それに対する最適なデジタルソリューションを提供することで、企業が持続的な成長とイノベーションを達成できるようサポートします。
製造業ニュース解説
製造業、主に購買・調達部門にお勤めの方々に向けた情報を配信しております。
新任の方やベテランの方、管理職を対象とした幅広いコンテンツをご用意しております。
お問い合わせ
コストダウンが利益に直結する術だと理解していても、なかなか前に進めることができない状況。そんな時は、newjiのコストダウン自動化機能で大きく利益貢献しよう!
(β版非公開)