- お役立ち記事
- How to build a procurement strategy that responds to fluctuations in supply and demand in the electronic parts industry
How to build a procurement strategy that responds to fluctuations in supply and demand in the electronic parts industry
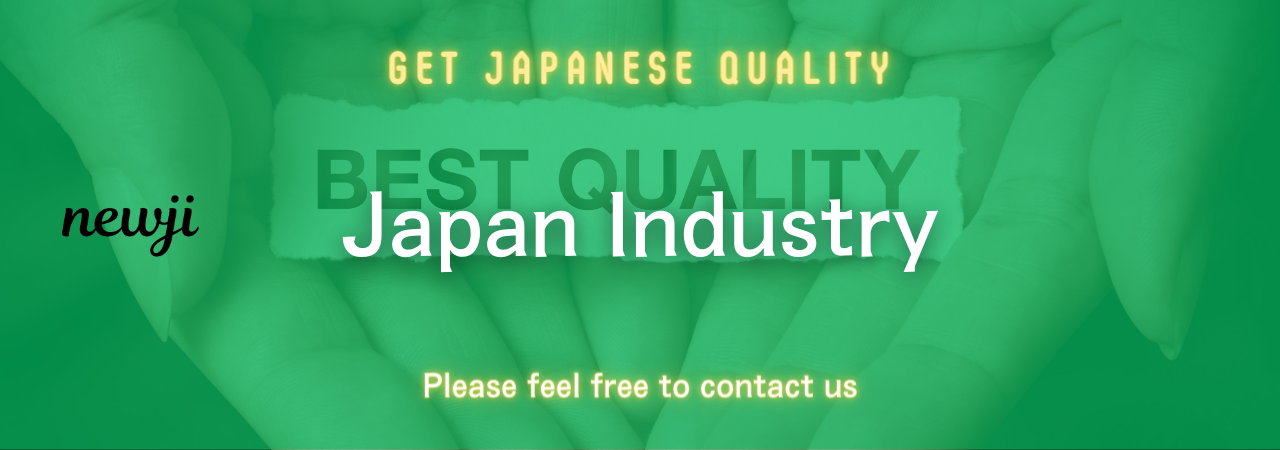
目次
Understanding the Electronic Parts Industry
The electronic parts industry is a vital component of modern technological advancements, driving innovation and facilitating the development of new products.
As essential components, electronic parts include semiconductors, resistors, capacitors, microchips, and connectors, which are used in everything from consumer electronics to industrial machinery.
This industry’s dynamic nature means that businesses must remain agile and responsive to shifting market conditions.
Challenges in the Electronic Parts Industry
One of the most significant challenges faced by companies in this industry is managing fluctuations in supply and demand.
Global events, technological advancements, and changing consumer preferences can all impact the availability and demand for specific electronic components.
Moreover, supply chain disruptions, such as natural disasters or geopolitical tensions, can lead to sudden shortages or surpluses, complicating procurement strategies.
Importance of a Robust Procurement Strategy
A well-designed procurement strategy allows companies to navigate these challenges effectively, minimizing risk and capitalizing on opportunities.
By anticipating market fluctuations and responding accordingly, businesses can ensure they have the necessary electronic parts in stock when needed, avoiding costly delays or excess inventory.
Key Components of an Effective Procurement Strategy
To build a robust procurement strategy that responds to supply and demand fluctuations in the electronic parts industry, consider the following components:
1. **Market Analysis**: Conduct comprehensive research to understand current market trends, competitors, and consumer preferences.
This information will help you anticipate changes in demand and adjust your procurement plans accordingly.
2. **Supplier Relationships**: Develop strong, collaborative relationships with suppliers, fostering open communication and mutual trust.
This can help you secure favorable terms and quickly adapt to any supply chain disruptions.
3. **Inventory Management**: Implement effective inventory management practices to balance stock levels with demand forecasts.
This may involve leveraging advanced software solutions to track inventory in real-time and optimize reorder points.
4. **Risk Management**: Identify potential risks within your supply chain, such as supplier insolvency or transportation disruptions, and develop contingency plans.
This proactive approach can help you mitigate the impact of unforeseen events on your operations.
5. **Cost Control**: Monitor and manage procurement costs by evaluating different suppliers, negotiating favorable contracts, and utilizing bulk purchasing options when appropriate.
Ensuring cost efficiency will help increase profitability.
Developing a Flexible Procurement Strategy
Flexibility is critical in responding to fluctuations in supply and demand within the electronic parts industry.
A flexible procurement strategy enables businesses to adapt quickly to changing market conditions, ensuring stability and growth.
Strategies for Enhancing Flexibility
Here are some strategies to enhance the flexibility of your procurement process:
1. **Supplier Diversification**: Reduce reliance on a single supplier by working with multiple vendors.
This approach helps to minimize risks related to supply shortages and enhances your ability to respond to changes in demand.
2. **Adjustable Contracts**: Negotiate flexible contract terms with suppliers that accommodate fluctuations in order volume or delivery schedules.
This may involve agreements that allow for changes in minimum order quantities, delivery timelines, or pricing.
3. **Agile Workforce**: Invest in cross-training your workforce to ensure they can adapt to new processes, technologies, or requirements as needed.
This agility will help your team respond quickly to shifts in market conditions.
4. **Just-In-Time (JIT) Procurement**: Implement JIT procurement practices to reduce excess inventory and minimize waste while maintaining the ability to meet demand.
This approach focuses on receiving goods only when you need them, which can lead to cost savings and improved efficiency.
Leveraging Technology in Procurement
Incorporating technology is vital to building a procurement strategy that effectively responds to industry fluctuations.
Advanced tools and software can streamline processes, improve data analysis, and enhance communication throughout the supply chain.
Technological Solutions for Procurement
Consider the following technological solutions to optimize your procurement strategy:
1. **Data Analytics**: Utilize data analytics tools to gather, analyze, and interpret market data, allowing for more informed decision-making.
These insights can help you anticipate demand fluctuations and identify potential risks or opportunities.
2. **Supply Chain Management Software**: Implement comprehensive supply chain management software to streamline procurement processes, improve collaboration with suppliers, and enhance visibility across your supply chain.
3. **Artificial Intelligence (AI) and Machine Learning (ML)**: Leverage AI and ML technologies to automate repetitive tasks, optimize inventory management, and predict demand patterns more accurately.
These technologies can significantly improve efficiency and reduce the risk of human error.
4. **Blockchain Technology**: Consider incorporating blockchain technology into your procurement processes to enhance transparency, security, and traceability throughout your supply chain.
This can lead to improved trust and reliability among stakeholders.
Continuous Improvement and Adaptation
Building a procurement strategy that effectively responds to fluctuations in supply and demand requires continuous improvement and adaptation.
As the electronic parts industry evolves, businesses must remain vigilant and agile, regularly reviewing and adjusting their strategies.
Best Practices for Continuous Improvement
Here are some best practices to ensure your procurement strategy remains effective and adaptable:
1. **Regular Performance Reviews**: Conduct regular performance reviews of your procurement processes, suppliers, and strategies to identify areas for improvement.
Use metrics such as cost efficiency, lead times, and supplier performance to evaluate your progress and adjust accordingly.
2. **Industry Engagement**: Stay informed about industry developments and trends through conferences, networking events, and trade publications.
Engage with peers and industry experts to exchange ideas, best practices, and insights.
3. **Feedback Mechanisms**: Implement feedback mechanisms to gather input from your team, suppliers, and customers.
This information can help you identify potential issues and areas for improvement, ensuring that your procurement strategy remains effective and responsive.
By understanding the complexities of the electronic parts industry and developing a procurement strategy that emphasizes flexibility, technology, and continuous improvement, businesses can successfully navigate fluctuations in supply and demand.
This approach ensures a competitive edge and long-term growth in a rapidly evolving market.
資料ダウンロード
QCD調達購買管理クラウド「newji」は、調達購買部門で必要なQCD管理全てを備えた、現場特化型兼クラウド型の今世紀最高の購買管理システムとなります。
ユーザー登録
調達購買業務の効率化だけでなく、システムを導入することで、コスト削減や製品・資材のステータス可視化のほか、属人化していた購買情報の共有化による内部不正防止や統制にも役立ちます。
NEWJI DX
製造業に特化したデジタルトランスフォーメーション(DX)の実現を目指す請負開発型のコンサルティングサービスです。AI、iPaaS、および先端の技術を駆使して、製造プロセスの効率化、業務効率化、チームワーク強化、コスト削減、品質向上を実現します。このサービスは、製造業の課題を深く理解し、それに対する最適なデジタルソリューションを提供することで、企業が持続的な成長とイノベーションを達成できるようサポートします。
オンライン講座
製造業、主に購買・調達部門にお勤めの方々に向けた情報を配信しております。
新任の方やベテランの方、管理職を対象とした幅広いコンテンツをご用意しております。
お問い合わせ
コストダウンが利益に直結する術だと理解していても、なかなか前に進めることができない状況。そんな時は、newjiのコストダウン自動化機能で大きく利益貢献しよう!
(Β版非公開)