- お役立ち記事
- A practical guide to utilizing “manufacturing cost accounting” in purchasing operations
月間77,185名の
製造業ご担当者様が閲覧しています*
*2025年2月28日現在のGoogle Analyticsのデータより
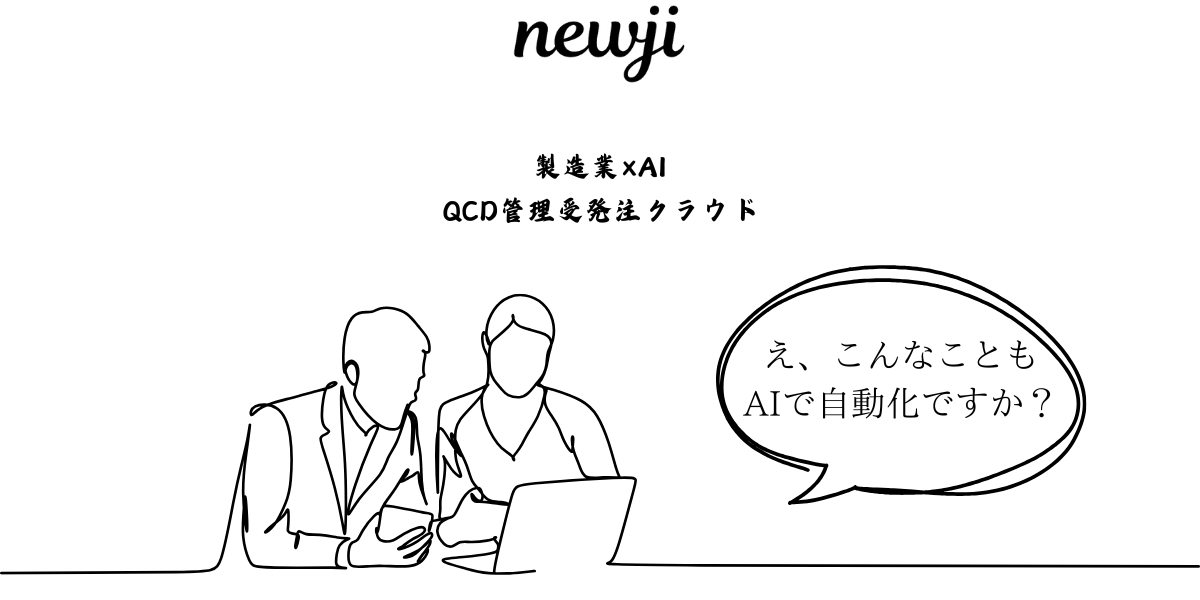
A practical guide to utilizing “manufacturing cost accounting” in purchasing operations
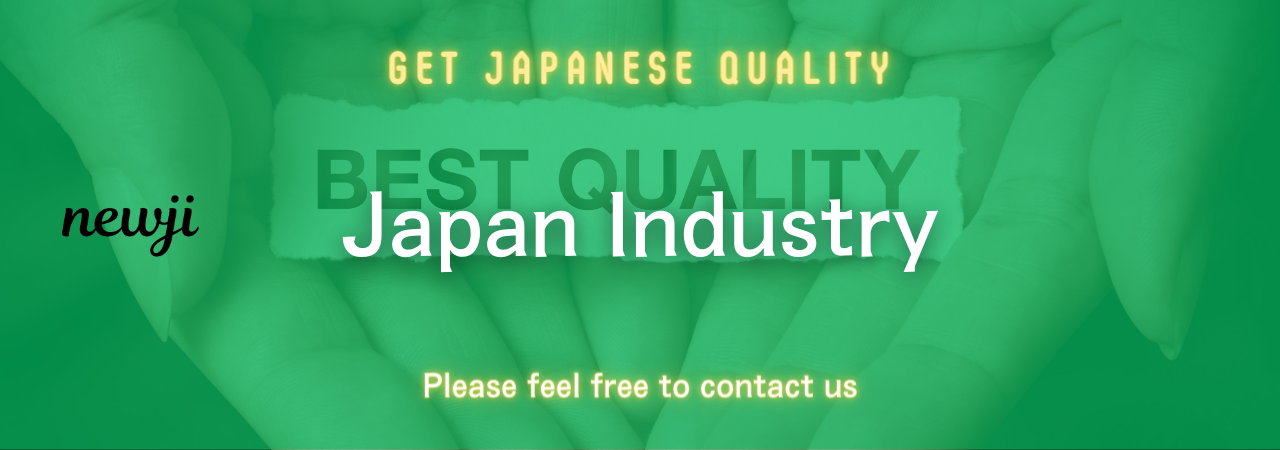
目次
Understanding Manufacturing Cost Accounting
Manufacturing cost accounting is an essential aspect of financial management in any production-oriented business.
It involves tracking and analyzing all costs related to the manufacturing process.
This includes direct materials, direct labor, and manufacturing overhead costs.
By understanding these costs, businesses can make informed decisions about pricing, budgeting, and overall financial planning.
Manufacturing cost accounting helps businesses to understand their production costs in detail.
This knowledge allows companies to identify areas where they can reduce expenses and improve efficiency.
For instance, if a company realizes that their direct material costs are high, they can negotiate better prices with suppliers or explore alternative materials.
Overall, learning and applying manufacturing cost accounting principles can lead to significant savings and increased profitability.
The Importance of Cost Accounting in Purchasing
In purchasing operations, manufacturing cost accounting holds substantial importance.
Purchasing departments rely on accurate cost data to make informed decisions about vendor selection and contract negotiations.
With a clear understanding of manufacturing costs, purchasing managers can evaluate the cost-effectiveness of different suppliers.
This information is crucial when deciding which vendors to partner with for raw materials and other manufacturing necessities.
Moreover, cost accounting helps purchasing departments manage budgets more effectively.
By analyzing historical cost data, they can forecast future expenses and ensure that they are adhering to financial plans.
This proactive approach to budgeting helps prevent overspending and ensures that there is always enough capital available to support the manufacturing process.
Cost accounting also plays a critical role in risk management.
With accurate cost data, purchasing managers can identify potential financial risks and develop strategies to mitigate them.
For example, if a supplier’s prices begin to rise, the company can quickly respond by seeking alternative suppliers or adjusting their manufacturing process.
Implementing Cost Accounting in Purchasing Operations
To effectively implement manufacturing cost accounting in purchasing operations, businesses must take several strategic steps.
Step 1: Collect Accurate Data
The first step in implementing cost accounting is to collect accurate and comprehensive data.
This data should include all costs associated with the manufacturing process, from raw materials to labor and overhead expenses.
Many companies use software and automated systems to streamline data collection and ensure accuracy.
Step 2: Analyze Costs
Once data is collected, businesses must analyze it to gain insights into their production costs.
This analysis involves comparing costs over time, identifying trends, and pinpointing areas of inefficiency or overspending.
Tools such as cost variance analysis and standard costing can be beneficial in this stage.
Step 3: Optimize Purchasing Decisions
With a clear understanding of manufacturing costs, companies can begin to optimize their purchasing decisions.
This could involve renegotiating supplier contracts, seeking bulk discounts, or choosing alternative suppliers to reduce costs.
The key is to use the cost data to make informed decisions that align with the company’s overall financial goals.
Step 4: Communicate with Stakeholders
Effective communication is essential when implementing cost accounting practices.
Purchasing managers should regularly share cost insights with other departments, such as finance and production, to ensure everyone is aligned on cost-saving strategies.
Collaboration between departments can lead to innovative solutions and improved efficiency across the business.
Benefits of Manufacturing Cost Accounting in Purchasing
Utilizing manufacturing cost accounting in purchasing operations offers numerous benefits, including:
Cost Reduction
By understanding the intricacies of manufacturing costs, companies can implement strategies to reduce expenses.
Cost accounting highlights areas of inefficiency and potential savings, allowing businesses to reduce their overall production costs.
Improved Budgeting
Manufacturing cost accounting helps businesses create more accurate budgets by providing detailed insights into past and projected expenses.
This allows for better financial planning and ensures that purchasing operations remain within budget.
Enhanced Financial Decision-Making
With precise cost data, purchasing managers can make more informed financial decisions.
They can assess supplier performance, evaluate contract terms, and allocate resources effectively to maximize value and return on investment.
Risk Mitigation
Manufacturing cost accounting allows businesses to identify potential financial risks early.
By monitoring cost trends, companies can develop risk mitigation strategies and respond quickly to changes in supplier pricing or market conditions.
Challenges in Cost Accounting Implementation
While manufacturing cost accounting offers numerous benefits, there can be challenges in its implementation.
Data Accuracy
Ensuring the accuracy of cost data can be difficult, especially if data is manually recorded or collected from disparate sources.
Using automated systems can help improve data accuracy and streamline the collection process.
System Integration
Integrating cost accounting systems with existing business processes and technology can be challenging.
Businesses need to ensure that their accounting systems work seamlessly with other software used in purchasing and production.
Training and Expertise
Effective cost accounting requires skilled personnel with expertise in accounting and financial analysis.
Businesses may need to invest in training to ensure that their staff understand and can effectively utilize cost accounting principles.
Conclusion
Manufacturing cost accounting is a critical component of purchasing operations.
By understanding and applying cost accounting principles, companies can reduce expenses, improve budgeting, enhance decision-making, and mitigate risks.
While challenges exist in implementation, the benefits of cost accounting in purchasing operations far outweigh these obstacles.
With accurate data collection, thorough analysis, and effective communication, businesses can harness the power of cost accounting to drive efficiency and profitability in their purchasing processes.
資料ダウンロード
QCD管理受発注クラウド「newji」は、受発注部門で必要なQCD管理全てを備えた、現場特化型兼クラウド型の今世紀最高の受発注管理システムとなります。
ユーザー登録
受発注業務の効率化だけでなく、システムを導入することで、コスト削減や製品・資材のステータス可視化のほか、属人化していた受発注情報の共有化による内部不正防止や統制にも役立ちます。
NEWJI DX
製造業に特化したデジタルトランスフォーメーション(DX)の実現を目指す請負開発型のコンサルティングサービスです。AI、iPaaS、および先端の技術を駆使して、製造プロセスの効率化、業務効率化、チームワーク強化、コスト削減、品質向上を実現します。このサービスは、製造業の課題を深く理解し、それに対する最適なデジタルソリューションを提供することで、企業が持続的な成長とイノベーションを達成できるようサポートします。
製造業ニュース解説
製造業、主に購買・調達部門にお勤めの方々に向けた情報を配信しております。
新任の方やベテランの方、管理職を対象とした幅広いコンテンツをご用意しております。
お問い合わせ
コストダウンが利益に直結する術だと理解していても、なかなか前に進めることができない状況。そんな時は、newjiのコストダウン自動化機能で大きく利益貢献しよう!
(β版非公開)