- お役立ち記事
- How to increase production efficiency through “raw material standardization” promoted by the purchasing department
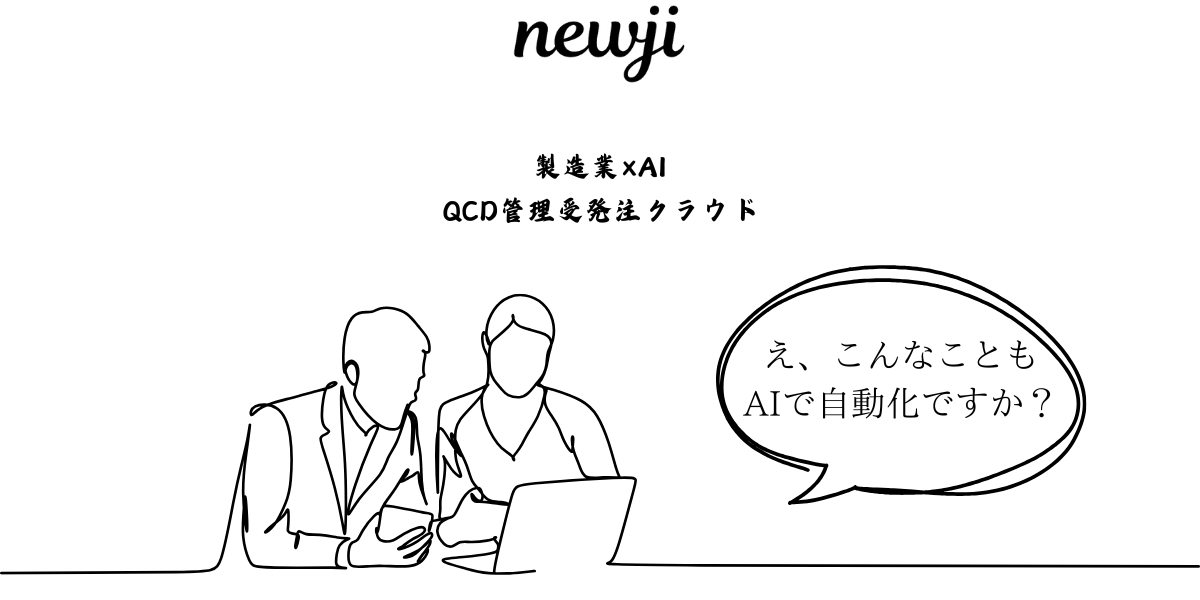
How to increase production efficiency through “raw material standardization” promoted by the purchasing department
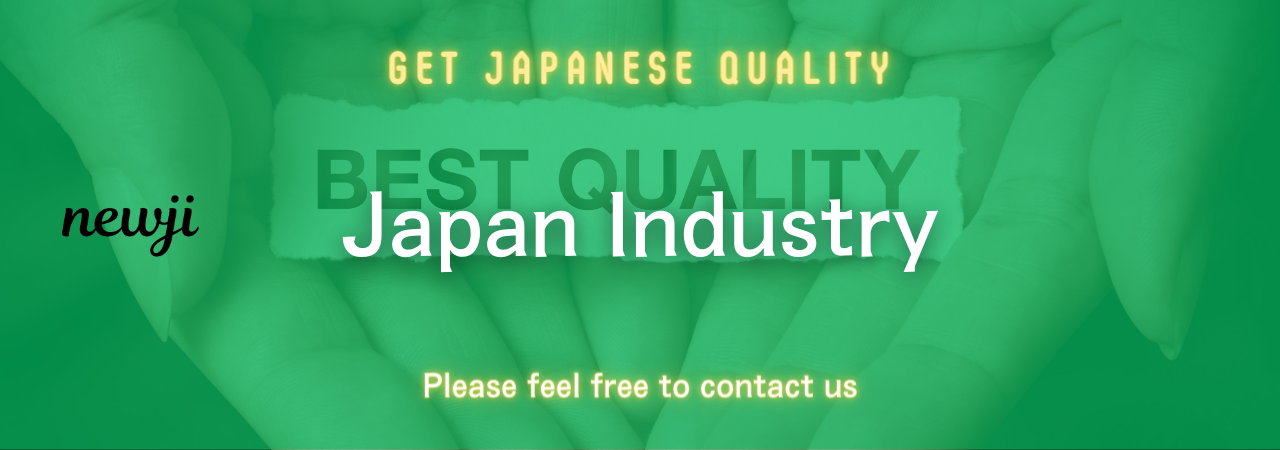
目次
Understanding the Importance of Raw Material Standardization
Raw material standardization is a vital strategy for companies aiming to enhance production efficiency.
The purchasing department plays a crucial role in implementing this strategy, ensuring that materials are of consistent quality and specification.
This practice aids in streamlining production processes, reducing waste, and improving overall productivity.
The importance of standardization cannot be overstated, as it helps in minimizing variations that can lead to inefficiencies.
When materials vary, production may face unexpected challenges, impacting the quality of the final product.
By standardizing raw materials, companies can predict and manage production outcomes more effectively.
The Role of the Purchasing Department
The purchasing department is instrumental in establishing and maintaining raw material standards.
Their primary responsibility is to identify reliable suppliers who can consistently provide materials that meet the organization’s specifications.
Building strong relationships with these suppliers ensures a steady supply of quality resources, which is crucial for smooth production.
Moreover, the purchasing department must continually monitor and evaluate suppliers’ performance.
This evaluation involves checking material quality, delivery time, and compliance with agreed standards.
By doing this diligently, the department ensures that the production line is never halted due to material issues.
Steps to Implement Raw Material Standardization
1. Define Material Specifications
The first step towards raw material standardization is to clearly define the specifications required for each material.
These specifications should align with the company’s production needs and quality expectations.
Involving engineers and production managers in this process can help ensure that all technical requirements are addressed.
2. Source Reliable Suppliers
After defining the specifications, the purchasing department must identify and engage with suppliers who can meet these requirements consistently.
It’s essential to conduct thorough research and assessments during this phase to verify each supplier’s capability and reliability.
3. Negotiate Contracts and Agreements
Once potential suppliers are shortlisted, the next step is negotiating contracts that formalize the commitment to quality and standards.
Contracts should include clauses related to material specifications, delivery schedules, and penalties for non-compliance.
These agreements help protect the company’s interests and ensure suppliers are accountable for their deliveries.
4. Implement Quality Control Measures
Even after establishing standards and agreements, it is vital to have robust quality control measures in place.
Regular inspections and testing of incoming materials can identify any inconsistencies early in the process.
Both the purchasing and quality assurance teams should work closely to monitor and address any issues promptly.
5. Review and Update Standards Regularly
Production needs can evolve, and it is crucial to periodically review and update material standards.
This review should include feedback from production teams and consider any changes in technology or market demands.
Keeping material standards relevant ensures that the company remains competitive and efficient.
Benefits of Raw Material Standardization
Raw material standardization offers several significant benefits that enhance production efficiency.
Improved Quality Control
By ensuring that all raw materials meet the same standards, companies can produce goods of consistent quality.
This consistency not only satisfies customers but also reduces the time and costs associated with quality inspections and rework.
Cost Reduction
Standardizing raw materials can lead to cost reductions in multiple areas.
Bulk purchasing agreements with suppliers often result in lower material costs.
Moreover, consistent material quality reduces waste and minimizes instances of production downtime.
Streamlined Production Processes
With standardized raw materials, the production process becomes more predictable and streamlined.
It allows for better planning and scheduling, reducing bottlenecks and improving throughput.
Employees can work more efficiently when they can rely on the consistency of materials.
Enhanced Supplier Relationships
When a company commits to standardized materials, it often leads to stronger relationships with suppliers.
Long-term contracts based on mutual trust benefit both parties and can lead to more favorable terms and conditions.
Challenges and Considerations
Despite the numerous benefits, implementing raw material standardization can present some challenges.
Cultural Resistance
Sometimes, staff may be resistant to change, particularly if it involves altering habitual processes.
Addressing this challenge requires effective communication about the benefits of standardization and training to ease the transition.
Supply Chain Disruptions
Supply chain disruptions can impact the availability of standardized materials.
Having contingency plans and multiple suppliers can mitigate this risk, ensuring continuity despite unforeseen challenges.
Initial Setup Costs
The initial investment required for standardization, such as new supplier relationships or updated quality control measures, can be significant.
However, these costs are often outweighed by the long-term savings and efficiency gains.
Conclusion
Raw material standardization, driven by a diligent purchasing department, plays a critical role in improving production efficiency.
Through well-defined specifications, reliable supplier engagements, and strong quality control, companies can realize significant benefits.
While challenges exist, addressing them strategically can further strengthen a company’s production capabilities and competitive edge.
Ultimately, the commitment to maintaining high standards in raw materials translates to consistent quality, cost savings, and streamlined operations.
資料ダウンロード
QCD調達購買管理クラウド「newji」は、調達購買部門で必要なQCD管理全てを備えた、現場特化型兼クラウド型の今世紀最高の購買管理システムとなります。
ユーザー登録
調達購買業務の効率化だけでなく、システムを導入することで、コスト削減や製品・資材のステータス可視化のほか、属人化していた購買情報の共有化による内部不正防止や統制にも役立ちます。
NEWJI DX
製造業に特化したデジタルトランスフォーメーション(DX)の実現を目指す請負開発型のコンサルティングサービスです。AI、iPaaS、および先端の技術を駆使して、製造プロセスの効率化、業務効率化、チームワーク強化、コスト削減、品質向上を実現します。このサービスは、製造業の課題を深く理解し、それに対する最適なデジタルソリューションを提供することで、企業が持続的な成長とイノベーションを達成できるようサポートします。
オンライン講座
製造業、主に購買・調達部門にお勤めの方々に向けた情報を配信しております。
新任の方やベテランの方、管理職を対象とした幅広いコンテンツをご用意しております。
お問い合わせ
コストダウンが利益に直結する術だと理解していても、なかなか前に進めることができない状況。そんな時は、newjiのコストダウン自動化機能で大きく利益貢献しよう!
(Β版非公開)