- お役立ち記事
- Practical methods for reducing lead time in purchasing operations
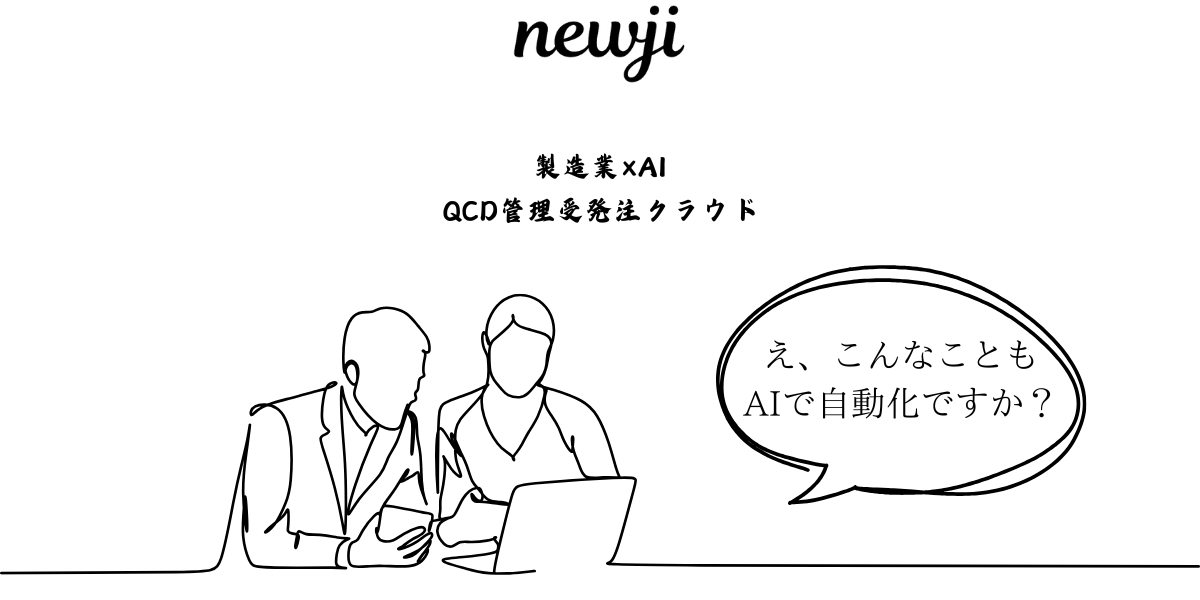
Practical methods for reducing lead time in purchasing operations
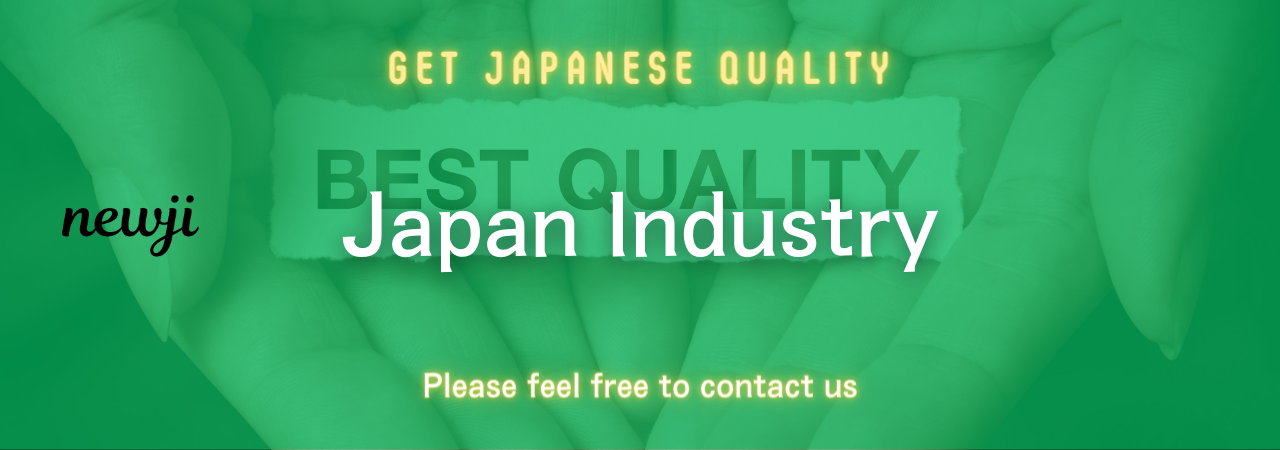
目次
Understanding Lead Time in Purchasing Operations
Purchasing operations play a crucial role in the supply chain.
A significant aspect of these operations is lead time, which is the period between placing an order and receiving it.
For businesses, reducing lead time is essential for improving efficiency, lowering costs, and enhancing customer satisfaction.
Understanding what affects lead time is the first step in effectively managing and reducing it.
Lead times can vary based on several factors such as supplier performance, shipping logistics, and internal processing within a company.
Long lead times can result in increased carrying costs and can negatively impact the ability to meet customer demands promptly.
Efforts to reduce lead time focus on minimizing these delays at every stage of the purchasing process.
Identifying Bottlenecks in the Purchasing Process
To effectively reduce lead time, businesses must first identify any bottlenecks within their purchasing process.
Bottlenecks are areas where delays frequently occur, slowing down the entire operation.
Common bottlenecks include inefficient communication channels, slow decision-making, outdated technology, and lack of coordination with suppliers.
Evaluating each step of the purchasing process can help pinpoint where these delays are happening.
Conducting regular audits and using key performance indicators (KPIs) can provide valuable insights into how time is being spent and where improvements are needed.
By addressing these bottlenecks, companies can streamline operations and reduce unnecessary delays.
Enhancing Supplier Relationships
Supplier performance is a significant factor in determining lead times.
Building strong, cooperative relationships with suppliers can have a profound impact on reducing lead time in purchasing operations.
Open communication, regular feedback, and strategic partnerships can align suppliers more closely with the goals of your business.
Negotiating better terms and conditions, such as shorter delivery times and more flexible order quantities, can also contribute to reducing lead times.
Furthermore, involving suppliers early in the planning stages, such as in the design and forecast process, can lead to more accurate order fulfillment and shorter lead times.
Implementing Supplier Performance Metrics
Introducing supplier performance metrics is another effective way to improve lead time.
These metrics allow businesses to track and measure supplier performance on various aspects like quality, delivery time, and responsiveness.
With these metrics, companies can set standards and expectations for suppliers and hold them accountable for meeting these goals.
Performance data can also be used to make informed decisions about continuing relationships with existing suppliers or finding new ones.
Leveraging Technology to Streamline Operations
Technology plays a vital role in reducing lead times in purchasing operations.
Implementing sophisticated software solutions can automate many of the manual tasks involved in purchasing, resulting in faster and more accurate processes.
Adopting Enterprise Resource Planning (ERP) systems can integrate different departments within an organization, creating a cohesive workflow and reducing lead time.
These systems provide real-time data access and facilitate better decision-making by providing comprehensive visibility into the supply chain.
Automation tools can also automate order placements, track inventory levels, and forecast demand, all of which help in minimizing lead time.
Utilizing E-Procurement Solutions
E-procurement solutions offer businesses an online platform to manage their purchasing activities more efficiently.
By digitizing the procurement process, businesses can reduce paperwork, lower processing times, and improve communication with suppliers.
Through e-procurement, companies can place orders, receive invoices, and make payments electronically, speeding up the transaction process.
Furthermore, these solutions allow businesses to compare different suppliers easily, ensuring the best mix of quality and lead time.
Effective Inventory Management
Efficient inventory management is crucial to reducing lead time in purchasing operations.
Maintaining optimal inventory levels ensures that the business can meet customer demands without delays.
Adopting strategies such as Just-in-Time (JIT) inventory can significantly cut down on lead times.
With JIT, companies receive goods only as they are needed in the production process, which minimizes holding costs and reduces lead times.
Advancements in inventory tracking technologies, such as barcoding and RFID, can provide accurate real-time inventory data, which aids in better planning and decision-making.
Demand Forecasting Techniques
Demand forecasting is another critical aspect of inventory management.
Accurate demand forecasts enable businesses to anticipate customer needs and order the correct quantity of materials from suppliers in a timely manner.
By analyzing historical data, market trends, and consumer behavior, companies can make more informed predictions about future demand.
This can prevent over-ordering or under-ordering, both of which can lead to increased lead times.
Incorporating predictive analytics into demand forecasting processes can enhance accuracy and provide a competitive edge.
Training and Empowering Staff
A knowledgeable and skilled workforce is essential for reducing lead time in purchasing operations.
Training staff to understand the importance of lead time and equipping them with the necessary skills and tools can lead to faster and more efficient purchasing processes.
Empowering employees to make quick and informed decisions also helps decrease delays.
Encouraging open communication within teams and with suppliers can resolve issues swiftly, preventing disruptions in the supply chain.
Regular training sessions and workshops can keep the team updated on the latest technologies, strategies, and industry practices, fostering a culture of continuous improvement.
Conclusion
Reducing lead time in purchasing operations requires a strategic and comprehensive approach that involves analyzing processes, enhancing supplier relationships, leveraging technology, managing inventory effectively, and empowering staff.
By implementing these practical methods, businesses can improve operational efficiency, lower costs, and better meet customer needs.
Ultimately, achieving shorter lead times provides a significant competitive advantage in today’s fast-paced market environment.
資料ダウンロード
QCD調達購買管理クラウド「newji」は、調達購買部門で必要なQCD管理全てを備えた、現場特化型兼クラウド型の今世紀最高の購買管理システムとなります。
ユーザー登録
調達購買業務の効率化だけでなく、システムを導入することで、コスト削減や製品・資材のステータス可視化のほか、属人化していた購買情報の共有化による内部不正防止や統制にも役立ちます。
NEWJI DX
製造業に特化したデジタルトランスフォーメーション(DX)の実現を目指す請負開発型のコンサルティングサービスです。AI、iPaaS、および先端の技術を駆使して、製造プロセスの効率化、業務効率化、チームワーク強化、コスト削減、品質向上を実現します。このサービスは、製造業の課題を深く理解し、それに対する最適なデジタルソリューションを提供することで、企業が持続的な成長とイノベーションを達成できるようサポートします。
オンライン講座
製造業、主に購買・調達部門にお勤めの方々に向けた情報を配信しております。
新任の方やベテランの方、管理職を対象とした幅広いコンテンツをご用意しております。
お問い合わせ
コストダウンが利益に直結する術だと理解していても、なかなか前に進めることができない状況。そんな時は、newjiのコストダウン自動化機能で大きく利益貢献しよう!
(Β版非公開)