- お役立ち記事
- Introducing the latest tools to strengthen collaboration between production planning and purchasing operations
月間77,185名の
製造業ご担当者様が閲覧しています*
*2025年2月28日現在のGoogle Analyticsのデータより
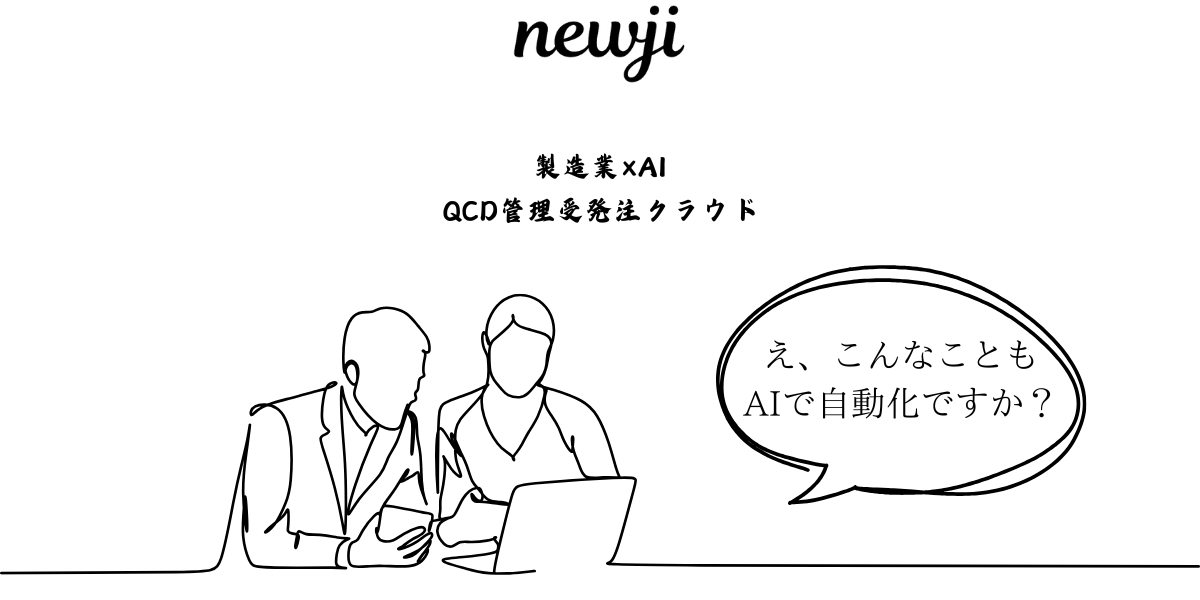
Introducing the latest tools to strengthen collaboration between production planning and purchasing operations
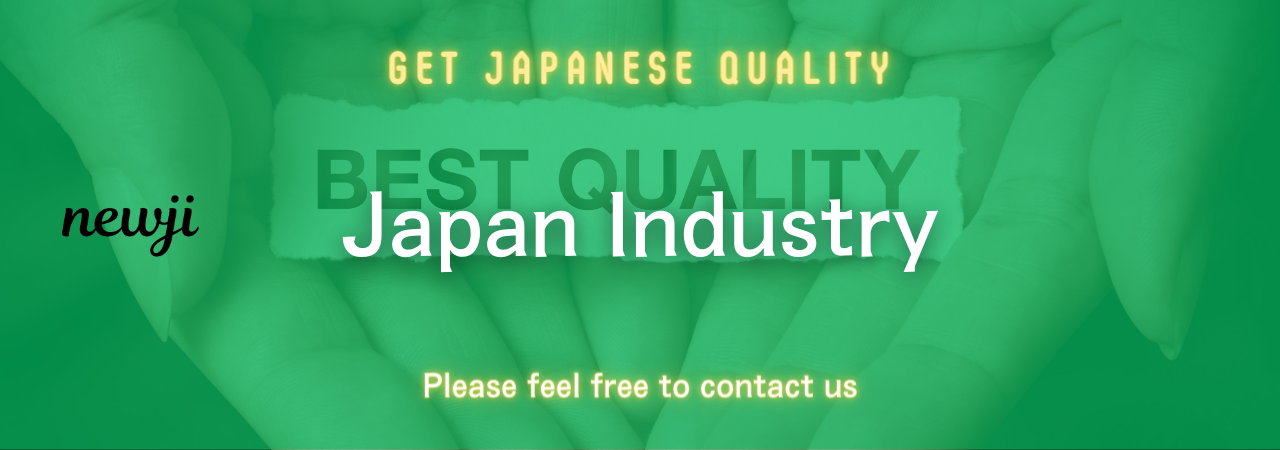
目次
Understanding the Importance of Collaboration
In the world of manufacturing, collaboration between production planning and purchasing operations is vital for success.
When these two departments work seamlessly together, businesses can improve efficiency, reduce costs, and maintain a more agile production line.
But why is this collaboration so crucial?
Let’s explore the key reasons.
Firstly, production planning is responsible for deciding what should be produced, when, and how much.
Meanwhile, purchasing operations are tasked with ensuring that the necessary materials and components are available at the right time and at the right cost.
Both functions must align perfectly to ensure that production schedules are met, and supply chains are not disrupted.
A disconnect between these departments can lead to production delays, increased costs, and unsatisfied customers.
By strengthening collaboration, companies can anticipate potential issues and adjust plans accordingly to avoid interruptions.
Identifying Challenges in Collaboration
Before delving into the tools that can enhance the synergy between production planning and purchasing operations, it is essential to identify the common challenges faced by these teams.
By understanding these obstacles, businesses can select the right tools to address their specific needs.
One significant challenge is communication.
In many organizations, communication between departments can be disjointed, leading to misaligned goals and actions.
Without real-time information sharing, it becomes difficult to coordinate, resulting in inefficiencies.
Another challenge is data management.
Production planning and purchasing require access to the same set of data, such as inventory levels, supplier information, and production schedules.
Without a centralized system, data silos can form, impeding collaboration.
Furthermore, managing complex supply chains and rapidly changing market demands can overwhelm teams.
They must have a clear understanding of priorities and potential risks to navigate these challenges effectively.
Embracing the Latest Tools for Better Collaboration
To tackle these challenges, businesses are increasingly turning to advanced tools designed to strengthen collaboration between production planning and purchasing operations.
Let’s take a closer look at some of the latest tools that can make a significant difference.
1. Integrated Software Solutions
Integrated software solutions, such as Enterprise Resource Planning (ERP) systems, are becoming essential in fostering collaboration.
These platforms provide a centralized hub where both production planners and purchasing teams can access critical information in real-time.
ERPs streamline workflows, eliminate data silos, and ensure that everyone is working from the same page.
For example, an ERP system can automatically update inventory levels and notify purchasing teams of low-stock items, enabling them to reorder materials promptly.
Similarly, production planners can use these systems to adjust schedules based on real-time insights from purchasing teams.
2. Cloud-Based Collaboration Platforms
Cloud-based collaboration platforms offer a flexible and accessible solution for remote and distributed teams.
These platforms provide tools such as shared calendars, document repositories, and communication channels, which facilitate seamless interaction between production planning and purchasing operations.
Using cloud-based platforms, teams can collaborate on projects, share updates, and coordinate tasks without being bound by physical locations.
This increased accessibility leads to faster decision-making and greater alignment between departments.
3. Predictive Analytics Tools
Predictive analytics tools allow businesses to anticipate future trends, demand patterns, and potential supply chain disruptions.
By leveraging these insights, production planners and purchasing teams can make proactive decisions that align with market demands.
For instance, predictive analytics can forecast raw material availability based on supplier performance data.
This information empowers purchasing teams to negotiate better terms or seek alternative suppliers in advance.
Production planners can then adapt schedules to accommodate these changes, ensuring seamless production runs.
4. Automation and Artificial Intelligence
Automation and artificial intelligence (AI) are transforming collaboration by taking over repetitive tasks and providing valuable insights.
Automated systems can handle routine procurement tasks such as order processing, invoice management, and vendor communication, freeing up time for strategic decision-making.
AI-driven tools can analyze large datasets to identify patterns and trends that might be missed by human eyes.
This enables both production planning and purchasing teams to make data-driven decisions that enhance efficiency and reduce risks.
Implementing Collaboration Tools Successfully
While adopting these tools is a step in the right direction, successful implementation requires a strategic approach.
Here are a few key steps to consider:
1. **Assess Current Processes**: Before introducing new tools, conduct a thorough assessment of current collaboration processes.
Identify pain points and areas where technology can add value.
2. **Involve All Stakeholders**: Engage team members from both production planning and purchasing operations in the decision-making process.
Their input is valuable in selecting the right tools and ensuring that they address the needs of all users.
3. **Provide Adequate Training**: Introduce training programs to familiarize users with new tools and methodologies.
Proper training ensures that everyone can utilize the tools effectively and maximize their benefits.
4. **Monitor and Adjust**: Continuously monitor the impact of new tools on collaboration processes.
Be prepared to make adjustments based on feedback and evolving business needs.
The Future of Collaboration in Manufacturing
As technology continues to advance, the future of collaboration between production planning and purchasing operations looks promising.
With the help of innovative tools, businesses can foster a culture of collaboration, agility, and informed decision-making.
This not only benefits the organization but also contributes to a more efficient and resilient manufacturing sector, ready to meet the challenges of tomorrow.
By embracing the latest tools and strategies, organizations can redefine the way they operate, paving the way for increased productivity and sustained growth.
In this dynamic environment, the collaboration between production planning and purchasing operations will remain a cornerstone of success, driving the industry forward into a new era.
資料ダウンロード
QCD管理受発注クラウド「newji」は、受発注部門で必要なQCD管理全てを備えた、現場特化型兼クラウド型の今世紀最高の受発注管理システムとなります。
ユーザー登録
受発注業務の効率化だけでなく、システムを導入することで、コスト削減や製品・資材のステータス可視化のほか、属人化していた受発注情報の共有化による内部不正防止や統制にも役立ちます。
NEWJI DX
製造業に特化したデジタルトランスフォーメーション(DX)の実現を目指す請負開発型のコンサルティングサービスです。AI、iPaaS、および先端の技術を駆使して、製造プロセスの効率化、業務効率化、チームワーク強化、コスト削減、品質向上を実現します。このサービスは、製造業の課題を深く理解し、それに対する最適なデジタルソリューションを提供することで、企業が持続的な成長とイノベーションを達成できるようサポートします。
製造業ニュース解説
製造業、主に購買・調達部門にお勤めの方々に向けた情報を配信しております。
新任の方やベテランの方、管理職を対象とした幅広いコンテンツをご用意しております。
お問い合わせ
コストダウンが利益に直結する術だと理解していても、なかなか前に進めることができない状況。そんな時は、newjiのコストダウン自動化機能で大きく利益貢献しよう!
(β版非公開)