- お役立ち記事
- Techniques to improve the procurement process in the aircraft manufacturing industry
月間77,185名の
製造業ご担当者様が閲覧しています*
*2025年2月28日現在のGoogle Analyticsのデータより
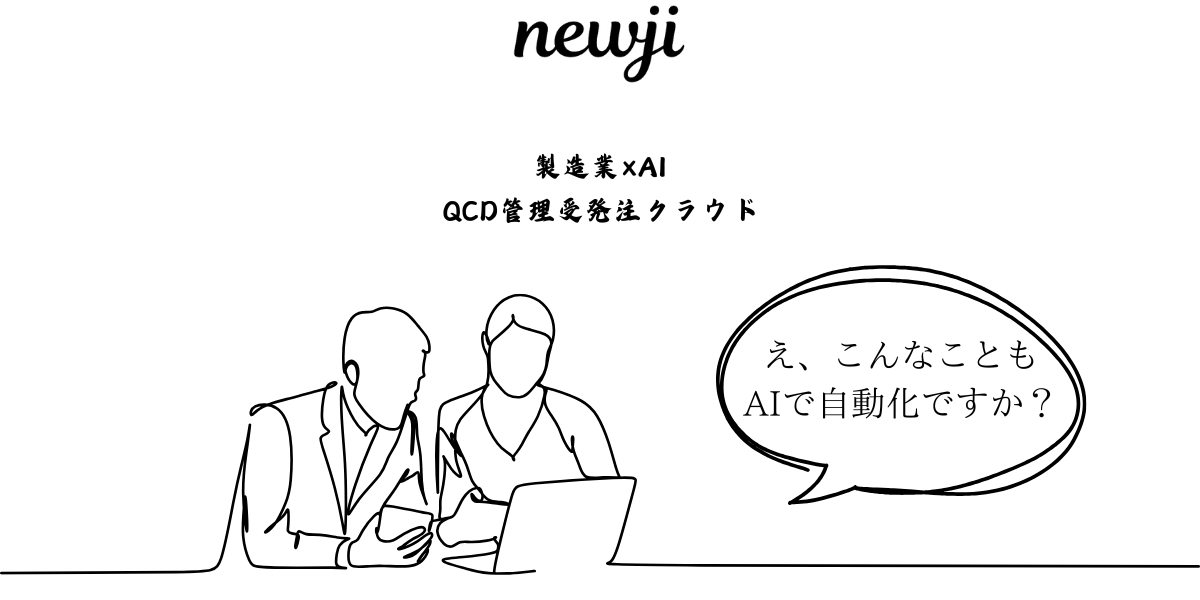
Techniques to improve the procurement process in the aircraft manufacturing industry
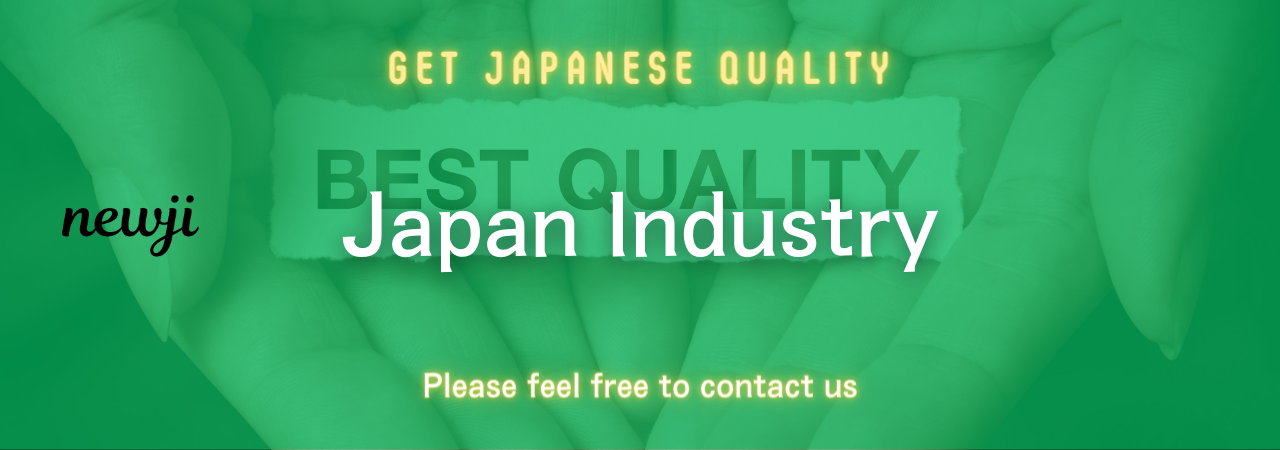
目次
Understanding the Procurement Process in Aircraft Manufacturing
The procurement process in the aircraft manufacturing industry is both critical and complex.
It involves the acquisition of materials, components, and services necessary to construct aircraft.
Given the intricate nature of aircraft, ensuring that all parts meet stringent safety and quality standards is essential.
The procurement function must not only focus on meeting current needs but also anticipate future requirements.
This means maintaining strong relationships with suppliers and ensuring a consistent flow of materials.
Any disruption can lead to costly delays in production.
Challenges in Aircraft Procurement
One of the main challenges is managing a vast array of suppliers.
The aircraft industry requires components from thousands of suppliers worldwide.
Some of these parts are highly specialized and may involve advanced technology or rare materials.
Another challenge is the industry’s tight regulatory environment.
Every component must meet specific regulations and standards.
This not only affects how parts are sourced but also influences the timelines and costs associated with procurement.
Cost management is another critical issue.
The aircraft manufacturing sector has become increasingly competitive, with companies striving to reduce costs without compromising quality.
Procurement teams must negotiate favorable terms with suppliers while also considering long-term partnerships.
Strategies to Enhance Procurement
Supplier Relationship Management
Building strong relationships with suppliers is crucial.
Maintaining open lines of communication and understanding each supplier’s capabilities can help mitigate risks.
Regular assessments and performance reviews ensure that suppliers meet expectations and can adapt to changing needs.
Diversifying the supplier base is also beneficial.
Relying heavily on a single supplier can be risky.
By having multiple sources, companies can prevent disruptions and encourage competitive pricing.
Embrace Technology and Automation
Investing in technology can significantly improve the procurement process.
Using digital platforms for procurement can streamline operations, reduce paperwork, and enhance data accuracy.
Automation tools can handle routine tasks, allowing procurement teams to focus on strategic activities.
Technologies like artificial intelligence and machine learning can provide valuable insights, such as predicting demand trends or identifying potential supply chain disruptions before they occur.
These insights enable better planning and decision-making.
Implement Just-In-Time (JIT) Inventory Management
The Just-In-Time (JIT) inventory management method can be highly effective.
By receiving goods only as they are needed in the production process, companies can reduce inventory costs and minimize waste.
JIT requires precise planning and strong supplier coordination.
While it can increase efficiency, it also necessitates reliable transportation networks and consistent supplier performance.
Focus on Quality Assurance
Quality assurance is paramount in the aircraft manufacturing industry.
Procurement teams must ensure that every component is not only delivered on time but also meets all quality standards.
Implementing thorough quality checks and certifications at every stage of procurement is vital.
Ensuring suppliers adhere to these standards prevents faulty components from entering the production cycle, which could lead to safety risks and reputational damage.
Training and Development
Investing in continuous training and development for procurement personnel can also improve the process.
Understanding new technologies and market dynamics enables procurement teams to be more strategic and effective.
Well-trained staff can better negotiate with suppliers, manage risks, and contribute to more efficient procurement operations.
The Long-Term View
Improving procurement is not just about immediate efficiency gains but also about creating a sustainable future.
This includes adopting environmentally friendly practices and considering the lifecycle impact of materials and components used.
Collaborating with suppliers on sustainable practices can lead to innovations that benefit both parties.
For example, developing lighter or more durable components can enhance aircraft performance and reduce environmental impact.
Conclusion: Embracing Change for Better Procurement
The procurement process in the aircraft manufacturing industry requires careful consideration of numerous factors.
By managing supplier relationships effectively, embracing technological advancements, and maintaining strict quality controls, companies can enhance their procurement processes.
In the long term, focusing on sustainability and continuous improvement will not only reduce costs but also strengthen competitive advantage.
As the industry evolves, those who adapt swiftly to change and innovation will lead the way in efficiency and safety.
Each improvement in the procurement process contributes to safer, more efficient aircraft and aligns with the ultimate goal of advancing aviation technology.
資料ダウンロード
QCD管理受発注クラウド「newji」は、受発注部門で必要なQCD管理全てを備えた、現場特化型兼クラウド型の今世紀最高の受発注管理システムとなります。
ユーザー登録
受発注業務の効率化だけでなく、システムを導入することで、コスト削減や製品・資材のステータス可視化のほか、属人化していた受発注情報の共有化による内部不正防止や統制にも役立ちます。
NEWJI DX
製造業に特化したデジタルトランスフォーメーション(DX)の実現を目指す請負開発型のコンサルティングサービスです。AI、iPaaS、および先端の技術を駆使して、製造プロセスの効率化、業務効率化、チームワーク強化、コスト削減、品質向上を実現します。このサービスは、製造業の課題を深く理解し、それに対する最適なデジタルソリューションを提供することで、企業が持続的な成長とイノベーションを達成できるようサポートします。
製造業ニュース解説
製造業、主に購買・調達部門にお勤めの方々に向けた情報を配信しております。
新任の方やベテランの方、管理職を対象とした幅広いコンテンツをご用意しております。
お問い合わせ
コストダウンが利益に直結する術だと理解していても、なかなか前に進めることができない状況。そんな時は、newjiのコストダウン自動化機能で大きく利益貢献しよう!
(β版非公開)