- お役立ち記事
- Revolutionizing Precision: How Japanese Manufacturing Leads the Future of MEMS Sensors
Revolutionizing Precision: How Japanese Manufacturing Leads the Future of MEMS Sensors
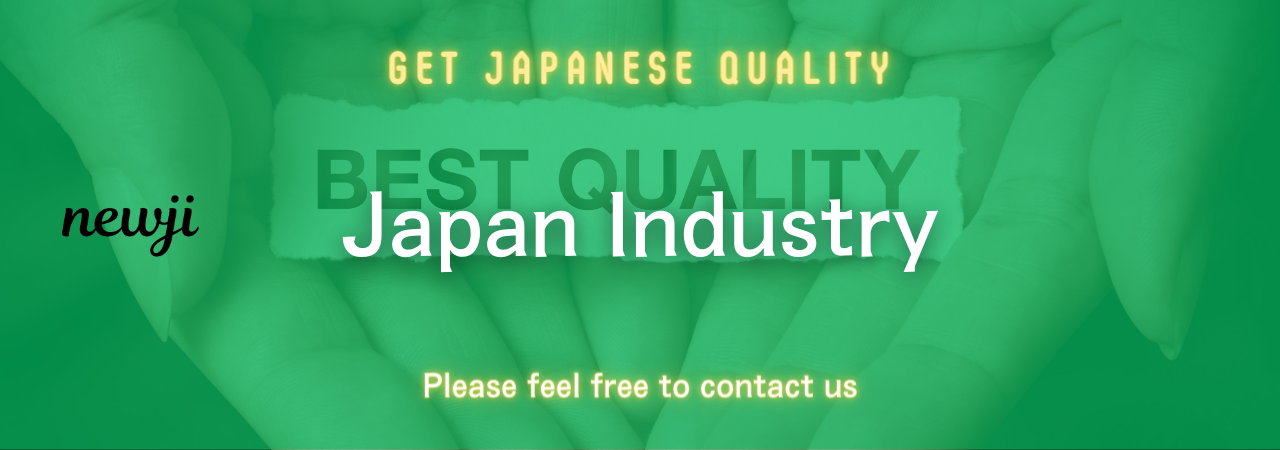
目次
Introduction
In the rapidly evolving landscape of technology, MEMS (Micro-Electro-Mechanical Systems) sensors have emerged as pivotal components in various applications.
From automotive safety systems to consumer electronics, the demand for high-precision MEMS sensors is soaring.
Japanese manufacturing has consistently been at the forefront of this revolution, setting standards in quality, innovation, and reliability.
This article delves into how Japanese manufacturing is shaping the future of MEMS sensors, with a particular focus on procurement and purchasing strategies.
Overview of Japanese Manufacturing in MEMS Sensors
Japanese manufacturers have long been synonymous with precision engineering and technological advancement.
In the MEMS sensor sector, Japan stands out due to its commitment to quality and continuous improvement.
Companies like Sony, TDK, and Epson have made significant strides in MEMS technology, integrating it seamlessly into a wide array of products.
The Japanese approach to manufacturing emphasizes meticulous attention to detail, robust quality control systems, and a culture of innovation.
These factors collectively contribute to the leadership position of Japanese manufacturers in the MEMS sensor market.
Advantages of Japanese MEMS Sensor Manufacturing
Superior Quality Control
One of the foremost advantages of sourcing MEMS sensors from Japanese manufacturers is their unparalleled quality control.
Japanese companies implement stringent quality assurance processes at every stage of production.
This commitment ensures that each MEMS sensor meets the highest standards of accuracy and reliability.
The use of advanced testing equipment and continuous monitoring minimizes defects and enhances product consistency.
For procurement professionals, this translates to fewer returns, lower warranty claims, and greater customer satisfaction.
Advanced Technology and Innovation
Japanese manufacturers are renowned for their cutting-edge technology and innovative capabilities.
In the realm of MEMS sensors, Japan leads in developing miniaturized, high-efficiency sensors that cater to diverse applications.
Investment in research and development is a cornerstone of Japanese manufacturing, fostering breakthroughs in sensor design and functionality.
This focus on innovation ensures that suppliers can offer the latest advancements, providing a competitive edge to purchasing companies.
Strong Supplier Relationships
Japanese business culture places a high value on long-term relationships and mutual trust.
This translates into stable and reliable partnerships between manufacturers and their clients.
For procurement and purchasing departments, working with Japanese suppliers means access to dedicated support, consistent supply chains, and collaborative problem-solving.
Such strong relationships can lead to preferential pricing, customization options, and enhanced service levels.
Disadvantages of Japanese MEMS Sensor Manufacturing
Higher Costs
While the quality and innovation of Japanese MEMS sensors are commendable, they often come at a higher price point compared to competitors.
The emphasis on superior materials, advanced technology, and rigorous quality control adds to the production costs.
For companies with tight budgets, this can pose a significant challenge in procurement decisions.
However, the long-term benefits of reliability and performance may offset the initial higher investment.
Cultural and Language Barriers
Engaging with Japanese suppliers can sometimes be complicated by cultural and language differences.
Japanese business practices emphasize formality, respect, and indirect communication, which may differ from Western business norms.
Language barriers can further complicate negotiations and contractual agreements.
These challenges necessitate effective communication strategies and possibly the involvement of cultural consultants to bridge the gap.
Longer Lead Times
Japanese manufacturing processes, with their focus on meticulous quality control and precision, may result in longer lead times.
For industries that require rapid turnaround and quick scaling, this can be a limiting factor.
Procurement teams must plan accordingly, allowing ample time for production and delivery to meet project timelines.
Procurement and Purchasing Strategies for Japanese MEMS Sensors
Market Conditions and Trends
Understanding the current market conditions is crucial for effective procurement.
The MEMS sensor market is influenced by factors such as technological advancements, regulatory changes, and shifting demand across industries.
Japanese manufacturers often lead these trends, setting benchmarks that others follow.
Procurement professionals should stay informed about these developments to make proactive sourcing decisions and leverage the latest innovations.
Supplier Negotiation Techniques
Negotiating with Japanese suppliers requires a nuanced approach that respects cultural norms and business etiquette.
Building rapport and demonstrating a genuine commitment to a long-term partnership are essential.
Negotiations should focus on building mutual trust, exploring value-added services, and discussing volume discounts or preferential terms.
Flexibility and patience are key, as rushing negotiations can jeopardize the relationship and result in less favorable terms.
Best Practices in Managing Japanese Suppliers
Effective supplier management is vital for maintaining a productive relationship with Japanese MEMS sensor manufacturers.
Regular communication, clear expectations, and collaborative problem-solving foster a strong partnership.
Implementing performance metrics and conducting periodic reviews can help ensure that suppliers meet agreed-upon standards.
Additionally, investing in supplier development and sharing forecasts can enhance alignment and responsiveness to market demands.
Case Studies and Examples
Case Study 1: Automotive MEMS Sensors
A leading automotive manufacturer sought high-precision MEMS sensors for their advanced driver-assistance systems (ADAS).
After evaluating multiple suppliers, they partnered with a Japanese manufacturer known for its superior quality control and innovative sensor technology.
The collaboration resulted in sensors with enhanced accuracy and reliability, significantly improving the performance of the ADAS.
The long-term relationship enabled the automotive company to benefit from ongoing technological advancements and preferential pricing.
Case Study 2: Consumer Electronics
A consumer electronics company aimed to integrate MEMS sensors into their latest smartphone model.
They opted for a Japanese supplier renowned for miniaturized and energy-efficient sensors.
Despite higher costs and longer lead times, the procurement team justified the investment based on the sensors’ performance and longevity.
The final product received positive market feedback for its superior sensor functionality, validating the strategic sourcing decision.
Future Outlook for Japanese MEMS Sensor Manufacturing
The future of Japanese MEMS sensor manufacturing looks promising, driven by continuous innovation and strategic investment in research and development.
Advancements in areas such as IoT, wearable technology, and autonomous systems are expected to increase the demand for sophisticated MEMS sensors.
Japanese manufacturers are well-positioned to capitalize on these trends, offering state-of-the-art solutions that meet evolving market needs.
Moreover, initiatives to enhance global supply chain integration and reduce lead times could address some of the current disadvantages, making Japanese MEMS sensors even more attractive to international buyers.
Conclusion
Japanese manufacturing plays a critical role in the advancement and adoption of MEMS sensors across various industries.
Their commitment to quality, innovation, and strong supplier relationships provides significant advantages to procurement and purchasing departments.
While challenges such as higher costs and cultural barriers exist, the benefits of partnering with Japanese suppliers often outweigh the drawbacks.
By adopting effective procurement strategies and fostering robust supplier relationships, companies can leverage the strengths of Japanese MEMS sensor manufacturers to drive technological advancement and achieve operational excellence.
資料ダウンロード
QCD調達購買管理クラウド「newji」は、調達購買部門で必要なQCD管理全てを備えた、現場特化型兼クラウド型の今世紀最高の購買管理システムとなります。
ユーザー登録
調達購買業務の効率化だけでなく、システムを導入することで、コスト削減や製品・資材のステータス可視化のほか、属人化していた購買情報の共有化による内部不正防止や統制にも役立ちます。
NEWJI DX
製造業に特化したデジタルトランスフォーメーション(DX)の実現を目指す請負開発型のコンサルティングサービスです。AI、iPaaS、および先端の技術を駆使して、製造プロセスの効率化、業務効率化、チームワーク強化、コスト削減、品質向上を実現します。このサービスは、製造業の課題を深く理解し、それに対する最適なデジタルソリューションを提供することで、企業が持続的な成長とイノベーションを達成できるようサポートします。
オンライン講座
製造業、主に購買・調達部門にお勤めの方々に向けた情報を配信しております。
新任の方やベテランの方、管理職を対象とした幅広いコンテンツをご用意しております。
お問い合わせ
コストダウンが利益に直結する術だと理解していても、なかなか前に進めることができない状況。そんな時は、newjiのコストダウン自動化機能で大きく利益貢献しよう!
(Β版非公開)