- お役立ち記事
- Understanding the Versatile Fin-Shaped Heat Sink: A Guide to Japanese Manufacturing Techniques
Understanding the Versatile Fin-Shaped Heat Sink: A Guide to Japanese Manufacturing Techniques
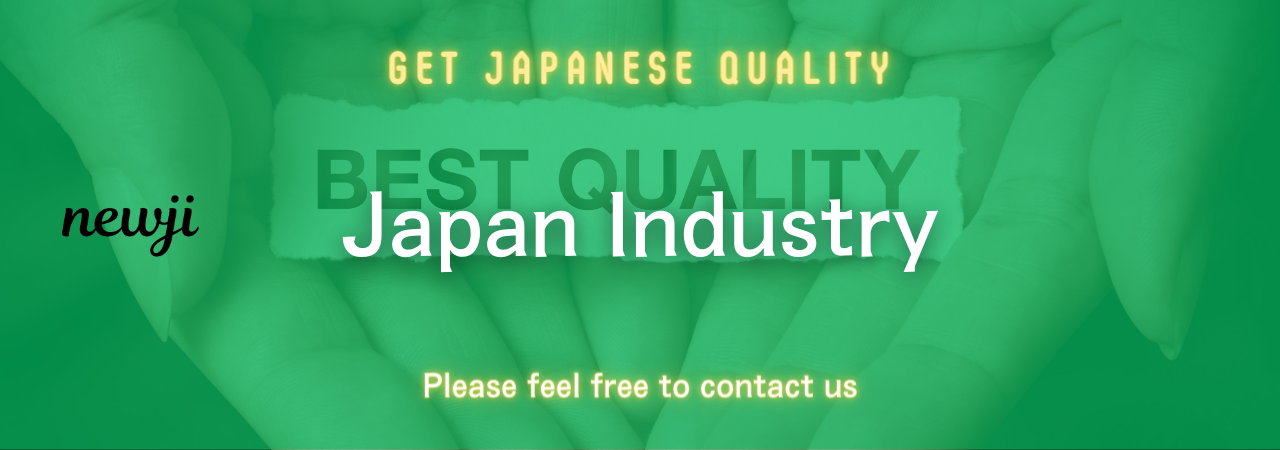
目次
Introduction
Fin-shaped heat sinks are integral components in thermal management systems across various industries.
They play a crucial role in dissipating heat from electronic devices, ensuring optimal performance and longevity.
Japanese manufacturing techniques have set a benchmark in the production of these versatile heat sinks.
This guide delves into the intricacies of fin-shaped heat sinks, exploring the advanced manufacturing methods employed by Japanese companies.
It also provides insights into procurement and purchasing strategies, supplier negotiation techniques, and best practices for leveraging Japanese manufacturing prowess.
Understanding Fin-Shaped Heat Sinks
Fin-shaped heat sinks are designed to enhance heat dissipation through increased surface area.
They typically consist of a base plate attached to multiple fins that facilitate the transfer of heat away from critical components.
These heat sinks are commonly used in electronics, automotive applications, and industrial machinery.
Their efficiency depends on factors such as fin geometry, material conductivity, and manufacturing precision.
Components of a Fin-Shaped Heat Sink
The primary components of a fin-shaped heat sink include the base, fins, and sometimes integrated fans.
The base acts as the interface between the heat sink and the device generating heat.
Fins are arranged in a pattern that maximizes surface area while allowing for airflow.
In some designs, fans are incorporated to enhance convective cooling.
Materials Used
Aluminum and copper are the most commonly used materials for fin-shaped heat sinks.
Aluminum is favored for its lightweight properties and good thermal conductivity.
Copper, while more expensive, offers superior thermal conductivity, making it ideal for high-performance applications.
Advanced composites and alloys are also emerging as viable materials in specialized applications.
Japanese Manufacturing Techniques
Japanese manufacturing is renowned for its emphasis on precision, quality control, and continuous improvement.
These principles are deeply embedded in the production of fin-shaped heat sinks, contributing to their reliability and performance.
Advanced Manufacturing Processes
Japanese manufacturers employ state-of-the-art machinery and automation to ensure consistency in heat sink production.
CNC machining is commonly used to achieve precise fin geometries and tolerances.
Additive manufacturing techniques are also being explored for creating complex fin structures that enhance thermal performance.
Quality Control and Assurance
Stringent quality control measures are a hallmark of Japanese manufacturing.
Every heat sink undergoes rigorous testing to verify its thermal performance and structural integrity.
Statistical process control (SPC) is implemented to monitor and maintain manufacturing standards.
This commitment to quality ensures that the heat sinks meet the stringent demands of various applications.
Lean Manufacturing and Just-In-Time (JIT) Practices
Japanese manufacturers often adopt lean manufacturing principles to minimize waste and optimize efficiency.
Just-In-Time (JIT) inventory management reduces excess inventory and enhances responsiveness to market demands.
These practices not only improve production efficiency but also contribute to cost savings for procurement departments.
Advantages of Japanese Fin-Shaped Heat Sinks
Japanese-manufactured fin-shaped heat sinks offer several advantages that make them a preferred choice in the global market.
Their high quality, reliability, and innovative designs provide significant benefits to end-users and procurement teams.
Superior Thermal Performance
The precision in manufacturing processes ensures that Japanese heat sinks have optimal fin geometries and material properties.
This results in enhanced thermal conductivity and efficient heat dissipation.
Industries such as electronics and automotive benefit from the superior cooling performance of these heat sinks.
Reliability and Durability
Rigorous quality control guarantees that Japanese heat sinks are free from defects and capable of withstanding demanding environments.
Their durability reduces the need for frequent replacements, offering long-term cost savings.
This reliability is crucial for applications where overheating can lead to critical failures.
Innovative Designs
Japanese manufacturers invest in research and development to create innovative heat sink designs that cater to evolving technological needs.
Customizable fin patterns and materials allow for tailored solutions that meet specific thermal management requirements.
Such innovation ensures that Japanese heat sinks remain at the forefront of the market.
Disadvantages of Japanese Fin-Shaped Heat Sinks
While Japanese fin-shaped heat sinks offer numerous benefits, there are certain drawbacks that procurement and purchasing departments should consider.
Higher Costs
The advanced manufacturing techniques and high-quality materials used in Japanese heat sinks often result in higher production costs.
This can translate to higher prices for end-users compared to alternatives from other regions.
Budget constraints may necessitate a careful cost-benefit analysis when considering Japanese suppliers.
Longer Lead Times
Due to the meticulous quality control and efficient manufacturing processes, lead times for Japanese heat sinks can be longer.
This may impact projects with tight deadlines or require larger inventory buffers.
Effective supply chain management is essential to mitigate potential delays.
Limited Customization Options
While Japanese manufacturers excel in standardization and quality, customization options may be limited.
Specialized or highly customized heat sink designs may require additional time and resources.
Collaborative negotiations with suppliers can help address specific customization needs.
Supplier Negotiation Techniques
Establishing strong relationships with Japanese suppliers is key to successful procurement and purchasing.
Effective negotiation techniques can lead to favorable terms, better pricing, and enhanced cooperation.
Building Trust and Long-Term Relationships
Japanese business culture places a high value on trust and long-term partnerships.
Invest time in building rapport with suppliers through regular communication and mutual respect.
Demonstrating reliability and commitment can lead to more favorable negotiation outcomes.
Understanding Cultural Differences
Cultural awareness is crucial when negotiating with Japanese suppliers.
Understanding Japanese business etiquette, such as the importance of formality and indirect communication, can facilitate smoother negotiations.
Respect for hierarchy and decision-making processes is also important.
Leveraging Volume and Long-Term Contracts
Negotiating based on purchase volume or committing to long-term contracts can provide leverage in securing better pricing and terms.
Japanese suppliers value stability and predictability, making them more open to favorable negotiations in exchange for guaranteed business.
Transparent Communication
Clear and transparent communication helps in aligning expectations and avoiding misunderstandings.
Provide detailed specifications and requirements to ensure that suppliers can meet your needs effectively.
Regular updates and feedback can enhance the negotiation process.
Market Conditions and Trends
Staying informed about market conditions and emerging trends is essential for effective procurement and purchasing of fin-shaped heat sinks.
Technological Advancements
Advancements in materials science and manufacturing technologies are driving innovation in heat sink design.
Emerging trends such as additive manufacturing and the use of advanced composites are influencing market offerings.
Staying abreast of these developments can help procurement teams make informed decisions.
Supply Chain Dynamics
Global supply chain disruptions, such as those caused by natural disasters or geopolitical tensions, can impact the availability and pricing of heat sinks.
Diversifying the supplier base and fostering strong relationships with multiple Japanese manufacturers can mitigate risks associated with supply chain fluctuations.
Environmental Regulations
Increasingly stringent environmental regulations are shaping the manufacturing processes and materials used in heat sinks.
Japanese suppliers are often at the forefront of adopting eco-friendly practices and materials.
Procurement teams should consider the environmental impact and compliance of heat sinks to align with sustainability goals.
Best Practices for Procurement and Purchasing
Implementing best practices can enhance the efficiency and effectiveness of procuring Japanese fin-shaped heat sinks.
Comprehensive Supplier Evaluation
Conduct thorough evaluations of potential suppliers, assessing factors such as quality, reliability, financial stability, and compliance with industry standards.
Use criteria-based assessments to ensure that suppliers meet your organization’s requirements.
Strategic Sourcing
Adopt a strategic sourcing approach that aligns procurement activities with overall business objectives.
Identify key suppliers that offer the best value in terms of quality, cost, and innovation.
Develop sourcing strategies that leverage the strengths of Japanese manufacturers.
Performance Monitoring and Feedback
Regularly monitor supplier performance using key performance indicators (KPIs) such as delivery times, defect rates, and responsiveness.
Provide constructive feedback to suppliers to foster continuous improvement and address any performance issues promptly.
Collaboration and Joint Development
Engage in collaborative initiatives with Japanese suppliers to co-develop advanced heat sink technologies.
Joint development projects can lead to customized solutions that offer a competitive edge in the market.
Such partnerships enhance innovation and align supplier capabilities with your specific needs.
Conclusion
Fin-shaped heat sinks are vital components in modern thermal management systems, and Japanese manufacturing techniques have established a standard of excellence in their production.
By understanding the advanced manufacturing processes, advantages, and potential drawbacks, procurement and purchasing professionals can make informed decisions.
Effective supplier negotiation, awareness of market conditions, and adherence to best practices further enhance the benefits of sourcing fin-shaped heat sinks from Japan.
Embracing these strategies allows organizations to leverage the technical prowess of Japanese manufacturers, ensuring high-performance thermal solutions that meet the evolving demands of various industries.
資料ダウンロード
QCD調達購買管理クラウド「newji」は、調達購買部門で必要なQCD管理全てを備えた、現場特化型兼クラウド型の今世紀最高の購買管理システムとなります。
ユーザー登録
調達購買業務の効率化だけでなく、システムを導入することで、コスト削減や製品・資材のステータス可視化のほか、属人化していた購買情報の共有化による内部不正防止や統制にも役立ちます。
NEWJI DX
製造業に特化したデジタルトランスフォーメーション(DX)の実現を目指す請負開発型のコンサルティングサービスです。AI、iPaaS、および先端の技術を駆使して、製造プロセスの効率化、業務効率化、チームワーク強化、コスト削減、品質向上を実現します。このサービスは、製造業の課題を深く理解し、それに対する最適なデジタルソリューションを提供することで、企業が持続的な成長とイノベーションを達成できるようサポートします。
オンライン講座
製造業、主に購買・調達部門にお勤めの方々に向けた情報を配信しております。
新任の方やベテランの方、管理職を対象とした幅広いコンテンツをご用意しております。
お問い合わせ
コストダウンが利益に直結する術だと理解していても、なかなか前に進めることができない状況。そんな時は、newjiのコストダウン自動化機能で大きく利益貢献しよう!
(Β版非公開)