- お役立ち記事
- Cutting-Edge Japanese Methods for Reducing Waste in Manufacturing: Boost Efficiency and Sustainability
Cutting-Edge Japanese Methods for Reducing Waste in Manufacturing: Boost Efficiency and Sustainability
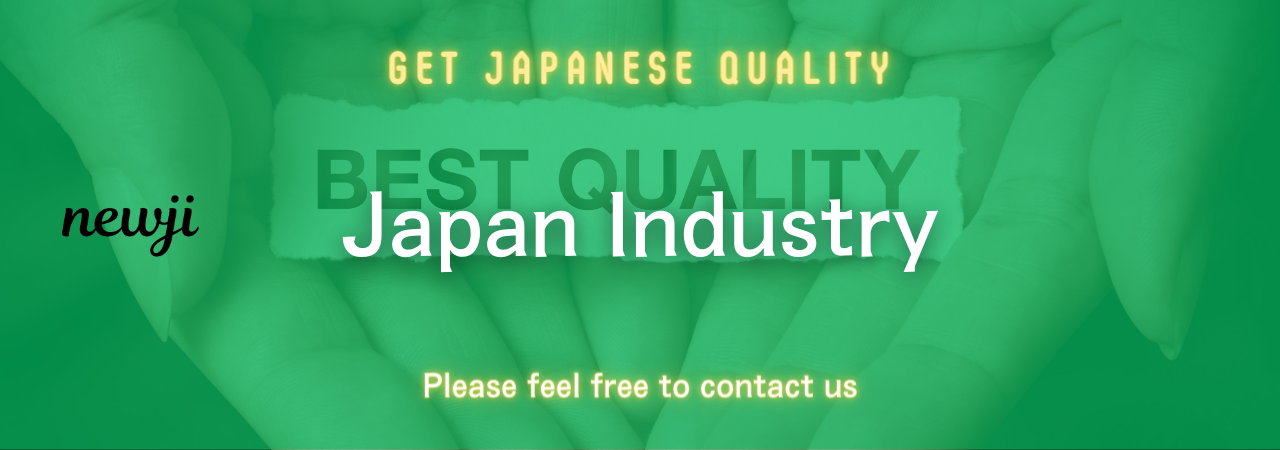
目次
Introduction to Japanese Waste Reduction Methods
Japanese manufacturing is renowned for its efficiency and sustainability.
One of the key factors contributing to this reputation is the implementation of cutting-edge waste reduction methods.
These techniques not only enhance productivity but also promote environmental responsibility.
By adopting these practices, manufacturers can achieve significant improvements in both operational efficiency and sustainability.
The Importance of Waste Reduction in Manufacturing
Waste reduction is critical in manufacturing for several reasons.
It helps in minimizing costs by eliminating unnecessary materials and processes.
Moreover, reducing waste contributes to environmental conservation by lowering resource consumption and emissions.
In the competitive manufacturing landscape, companies that effectively manage waste can gain a substantial advantage.
Lean Manufacturing: The Foundation of Japanese Efficiency
Lean manufacturing is a core principle in Japanese production systems.
It focuses on identifying and eliminating waste within manufacturing processes.
The five types of waste targeted in lean manufacturing are defects, overproduction, waiting, non-utilized talent, transportation, inventory, motion, and extra processing.
By addressing these areas, manufacturers can streamline operations and enhance overall efficiency.
Just-In-Time (JIT) Production
Just-In-Time is a pivotal aspect of lean manufacturing.
It entails producing only what is needed, when it is needed, and in the exact quantity required.
JIT minimizes inventory levels, reduces waste, and ensures a more responsive supply chain.
This method relies heavily on precise demand forecasting and reliable supplier relationships.
Kaizen: Continuous Improvement
Kaizen, meaning “continuous improvement,” is a philosophy that encourages ongoing enhancements in processes.
It involves every employee, from top management to the shop floor, in identifying and implementing improvements.
Kaizen fosters a culture of constant evaluation and incremental change, leading to sustained waste reduction and efficiency gains.
Practical Procurement and Purchasing Strategies
Effective procurement and purchasing are integral to waste reduction in manufacturing.
Japanese methods emphasize strategic sourcing, strong supplier relationships, and meticulous inventory management.
Strategic Sourcing
Strategic sourcing involves selecting suppliers based on their ability to deliver quality materials consistently and efficiently.
By partnering with reliable suppliers, manufacturers can reduce defects, minimize delays, and lower overall costs.
This approach also facilitates better alignment with production schedules and demand forecasts.
Strong Supplier Relationships
Building robust relationships with suppliers is a hallmark of Japanese procurement practices.
Trust and collaboration are essential for ensuring timely deliveries and high-quality materials.
Regular communication and mutual support help in resolving issues promptly and fostering long-term partnerships.
Inventory Management
Japanese methods advocate for precise inventory management to prevent overstocking and understocking.
Techniques such as Kanban systems help in maintaining optimal inventory levels.
This ensures that materials are available when needed, reducing holding costs and minimizing waste due to obsolescence or spoilage.
Advantages of Japanese Waste Reduction Methods
Implementing Japanese waste reduction methods offers numerous benefits to manufacturers.
Enhanced Efficiency
These methods streamline operations, leading to faster production cycles and increased throughput.
Efficiency gains translate into higher profitability and better competitiveness in the market.
Cost Savings
By eliminating waste, manufacturers can significantly reduce operational costs.
Lower material usage, reduced inventory holding, and minimized defects contribute to substantial cost savings.
Improved Quality
Japanese waste reduction techniques emphasize quality at every stage of production.
This leads to higher product standards, increased customer satisfaction, and fewer returns or rework.
Sustainability
Waste reduction aligns with environmental sustainability goals.
Less resource consumption and lower emissions contribute to a greener manufacturing process, enhancing the company’s reputation and compliance with environmental regulations.
Disadvantages and Challenges
Despite the advantages, there are challenges associated with implementing Japanese waste reduction methods.
Initial Implementation Costs
Adopting these methods may require significant upfront investment in training, equipment, and process redesign.
Small and medium-sized enterprises might find these initial costs prohibitive.
Cultural Barriers
Japanese methods often rely on a culture of continuous improvement and employee involvement.
Companies with hierarchical structures or resistance to change may struggle to implement these practices effectively.
Supplier Dependence
Strong reliance on suppliers is necessary for Just-In-Time and other lean practices.
If suppliers fail to meet commitments, it can disrupt production schedules and compromise efficiency.
Supplier Negotiation Techniques
Effective negotiation with suppliers is crucial for the success of waste reduction initiatives.
Win-Win Negotiations
Japanese negotiation approaches focus on creating mutually beneficial agreements.
This fosters long-term partnerships and encourages suppliers to prioritize quality and reliability.
Transparent Communication
Clear and honest communication about expectations, standards, and requirements helps in aligning supplier capabilities with manufacturing needs.
Transparency builds trust and facilitates problem-solving when issues arise.
Performance-Based Agreements
Contracts that include performance metrics motivate suppliers to maintain high standards.
Incentives for meeting or exceeding targets can drive continuous improvement and reliability.
Market Conditions and Adaptability
Japanese waste reduction methods are adaptable to various market conditions, but certain factors influence their effectiveness.
Economic Stability
During economic downturns, maintaining lean operations can provide a competitive edge through lower costs.
However, fluctuations in demand require flexible implementation to avoid overextending resources.
Technological Advancements
Embracing new technologies, such as automation and data analytics, enhances the effectiveness of waste reduction methods.
Staying current with technological trends is essential for sustaining efficiency improvements.
Global Supply Chain Dynamics
Globalization introduces complexities in supply chain management.
Manufacturers must navigate diverse supplier standards, lead times, and geopolitical factors to maintain lean operations.
Best Practices for Implementing Japanese Waste Reduction Methods
Adopting Japanese waste reduction methods requires strategic planning and commitment.
Leadership Commitment
Top management must champion waste reduction initiatives, providing the necessary resources and fostering a culture of continuous improvement.
Employee Training and Engagement
Investing in training equips employees with the skills needed to identify and eliminate waste.
Engaging the workforce in improvement activities ensures widespread participation and ownership of processes.
Process Standardization
Standardizing processes minimizes variability and streamlines operations.
Clear procedures and consistent practices are fundamental for maintaining efficiency and quality.
Continuous Monitoring and Feedback
Ongoing evaluation of processes and performance metrics helps in identifying areas for improvement.
Regular feedback loops enable timely adjustments and sustain momentum in waste reduction efforts.
Case Studies: Success Stories from Japanese Manufacturing
Examining real-world examples illustrates the practical application and benefits of Japanese waste reduction methods.
Toyota Production System
Toyota’s renowned production system epitomizes lean manufacturing principles.
Through Just-In-Time, Jidoka (automation with a human touch), and continuous improvement, Toyota has achieved exceptional efficiency and quality standards.
Honda’s Lean Initiatives
Honda has successfully implemented lean methodologies to reduce waste and enhance production flexibility.
Their focus on supplier integration and employee involvement has led to significant cost savings and quality improvements.
Panasonic’s Sustainability Efforts
Panasonic integrates waste reduction with sustainability goals.
By optimizing resource usage and minimizing emissions, Panasonic has established itself as a leader in environmentally responsible manufacturing.
Conclusion
Japanese waste reduction methods offer a comprehensive framework for enhancing manufacturing efficiency and sustainability.
By embracing lean principles, fostering strong supplier relationships, and committing to continuous improvement, manufacturers can achieve significant operational gains and environmental benefits.
While challenges exist, the advantages of reduced costs, improved quality, and sustainable practices make these methods invaluable in today’s competitive manufacturing landscape.
Adopting best practices and learning from successful case studies can guide organizations in effectively implementing these strategies, positioning them for long-term success.
資料ダウンロード
QCD調達購買管理クラウド「newji」は、調達購買部門で必要なQCD管理全てを備えた、現場特化型兼クラウド型の今世紀最高の購買管理システムとなります。
ユーザー登録
調達購買業務の効率化だけでなく、システムを導入することで、コスト削減や製品・資材のステータス可視化のほか、属人化していた購買情報の共有化による内部不正防止や統制にも役立ちます。
NEWJI DX
製造業に特化したデジタルトランスフォーメーション(DX)の実現を目指す請負開発型のコンサルティングサービスです。AI、iPaaS、および先端の技術を駆使して、製造プロセスの効率化、業務効率化、チームワーク強化、コスト削減、品質向上を実現します。このサービスは、製造業の課題を深く理解し、それに対する最適なデジタルソリューションを提供することで、企業が持続的な成長とイノベーションを達成できるようサポートします。
オンライン講座
製造業、主に購買・調達部門にお勤めの方々に向けた情報を配信しております。
新任の方やベテランの方、管理職を対象とした幅広いコンテンツをご用意しております。
お問い合わせ
コストダウンが利益に直結する術だと理解していても、なかなか前に進めることができない状況。そんな時は、newjiのコストダウン自動化機能で大きく利益貢献しよう!
(Β版非公開)