- お役立ち記事
- Fundamentals of metal fatigue fracture and practical points for prevention measures
Fundamentals of metal fatigue fracture and practical points for prevention measures
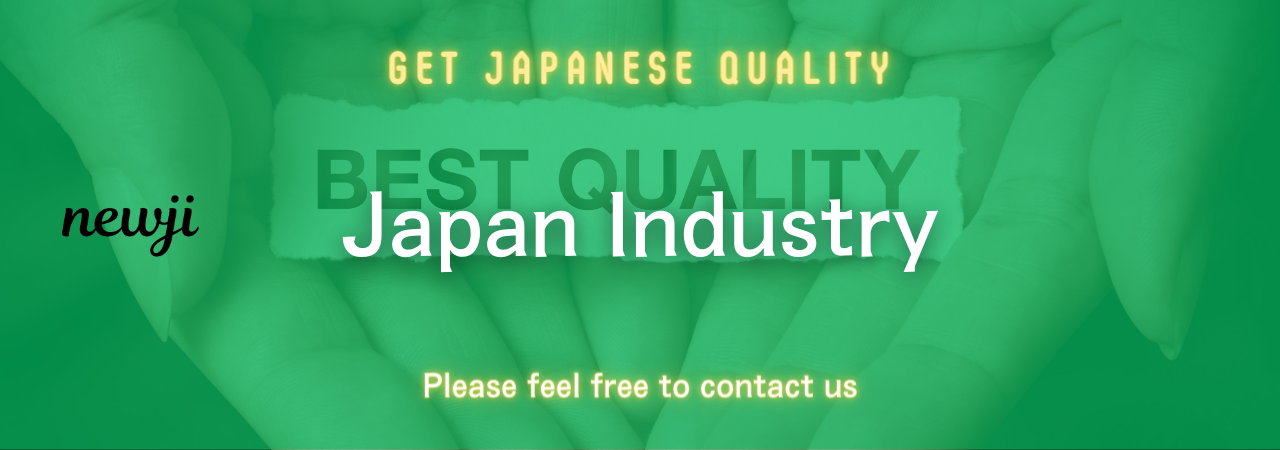
目次
Understanding Metal Fatigue Fracture
Metal fatigue fracture is a common phenomenon that affects the durability and functionality of metal components and structures.
It occurs when a metal is subjected to repeated loading and unloading cycles, leading to the initiation and growth of cracks over time.
This process eventually results in complete fracture, even if the material’s maximum stress level is below its ultimate tensile strength.
Understanding how metal fatigue works is essential for engineers and designers looking to enhance the longevity and safety of metal products.
The concept of metal fatigue can be traced back to the mid-19th century when it was first observed in railway axles.
Since then, numerous studies and experiments have been conducted to understand its underlying mechanics and develop methods to mitigate its impact.
Metal fatigue continues to be a critical concern in industries such as aviation, automotive, construction, and infrastructure, where the unexpected failure of metallic components can lead to catastrophic outcomes.
The Mechanics Behind Metal Fatigue
The fatigue process can be broken down into three distinct stages: crack initiation, crack propagation, and final fracture.
In the initial stage, micro-cracks form at points of stress concentration, such as surface imperfections, internal defects, or material discontinuities.
Once initiated, these cracks begin to propagate during the loading cycles.
The rate of crack growth depends on several factors, including the magnitude of the stress, the material’s properties, and environmental conditions.
The crack grows progressively with each cycle, eventually leading to the final stage—fracture.
One of the key factors influencing metal fatigue is the stress range experienced by the material.
High-stress ranges lead to faster crack growth, reducing the component’s fatigue life.
Additionally, environmental factors, such as temperature, corrosion, and other chemical interactions, can exacerbate fatigue by weakening the material and accelerating crack growth.
Preventive Measures for Metal Fatigue
Preventing metal fatigue fracture requires a comprehensive approach that includes proper material selection, design optimization, periodic inspection, and maintenance strategies.
Material Selection
Choosing the right material for a specific application is crucial for minimizing fatigue risks.
Materials with high fatigue strength and good toughness, such as certain alloys and composites, are more resistant to crack formation and propagation.
Engineers must consider both the mechanical properties and environmental factors when selecting materials for fatigue-prone applications.
Design Optimization
Designing components with smooth surfaces and appropriate geometry can reduce stress concentrations, which are often the starting points for crack initiation.
Avoiding sharp corners, using fillets, and incorporating load-distributing features can significantly enhance the fatigue resistance of a component.
Furthermore, ensuring that parts are adequately sized to handle maximal load conditions without excessive strain can prevent fatigue.
In some cases, incorporating redundancy into design can help manage unexpected fatigue failures without catastrophic outcomes.
Periodic Inspection and Maintenance
Regular inspection and maintenance are vital to detect early signs of fatigue before they result in failure.
Non-destructive testing methods, such as ultrasound, radiography, and magnetic particle inspection, are valuable tools for identifying internal and surface cracks.
Timely detection allows for corrective actions, such as crack repair or component replacement, extending the equipment’s service life.
Stress Reduction Techniques
Measures to reduce operational stress on components can also mitigate fatigue risks.
This can include vibration damping, load redistribution, and optimizing operational parameters to minimize stress cycles.
Ensuring that components are used within their designed stress limits and avoiding overload conditions is critical for enhancing fatigue life.
Implementing these practices in conjunction with consistent monitoring can effectively extend a component’s durability.
Innovations in Metal Fatigue Research
Recent advancements in technology and research have introduced new methods to understand and prevent metal fatigue.
Computational models and simulations now play a significant role in analyzing fatigue behavior, enabling engineers to predict and design for fatigue resistance more accurately.
Material science has also progressed, with the development of novel materials that exhibit superior fatigue properties.
Emerging surface treatment techniques, such as shot peening and laser peening, enhance fatigue life by inducing compressive stresses in surface layers, making them more resistant to crack propagation.
Conclusion
Understanding and addressing metal fatigue fracture is critical for ensuring the safety and reliability of metal components and structures.
Through informed material selection, optimized design, regular maintenance, and modern technological advancements, engineers can significantly reduce the risk of fatigue-related failures.
By considering the practical points discussed here, industries can better manage metal fatigue, enhancing both performance and safety across various applications.
資料ダウンロード
QCD調達購買管理クラウド「newji」は、調達購買部門で必要なQCD管理全てを備えた、現場特化型兼クラウド型の今世紀最高の購買管理システムとなります。
ユーザー登録
調達購買業務の効率化だけでなく、システムを導入することで、コスト削減や製品・資材のステータス可視化のほか、属人化していた購買情報の共有化による内部不正防止や統制にも役立ちます。
NEWJI DX
製造業に特化したデジタルトランスフォーメーション(DX)の実現を目指す請負開発型のコンサルティングサービスです。AI、iPaaS、および先端の技術を駆使して、製造プロセスの効率化、業務効率化、チームワーク強化、コスト削減、品質向上を実現します。このサービスは、製造業の課題を深く理解し、それに対する最適なデジタルソリューションを提供することで、企業が持続的な成長とイノベーションを達成できるようサポートします。
オンライン講座
製造業、主に購買・調達部門にお勤めの方々に向けた情報を配信しております。
新任の方やベテランの方、管理職を対象とした幅広いコンテンツをご用意しております。
お問い合わせ
コストダウンが利益に直結する術だと理解していても、なかなか前に進めることができない状況。そんな時は、newjiのコストダウン自動化機能で大きく利益貢献しよう!
(Β版非公開)