- お役立ち記事
- Basics of Vibration and Noise Reduction Techniques for Machinery
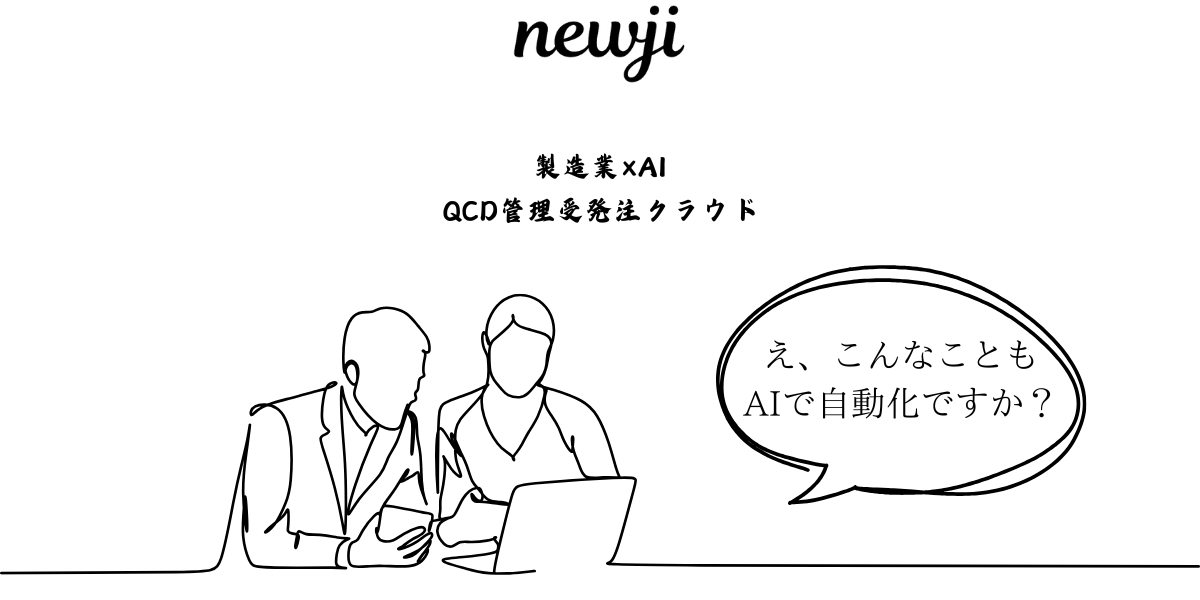
Basics of Vibration and Noise Reduction Techniques for Machinery
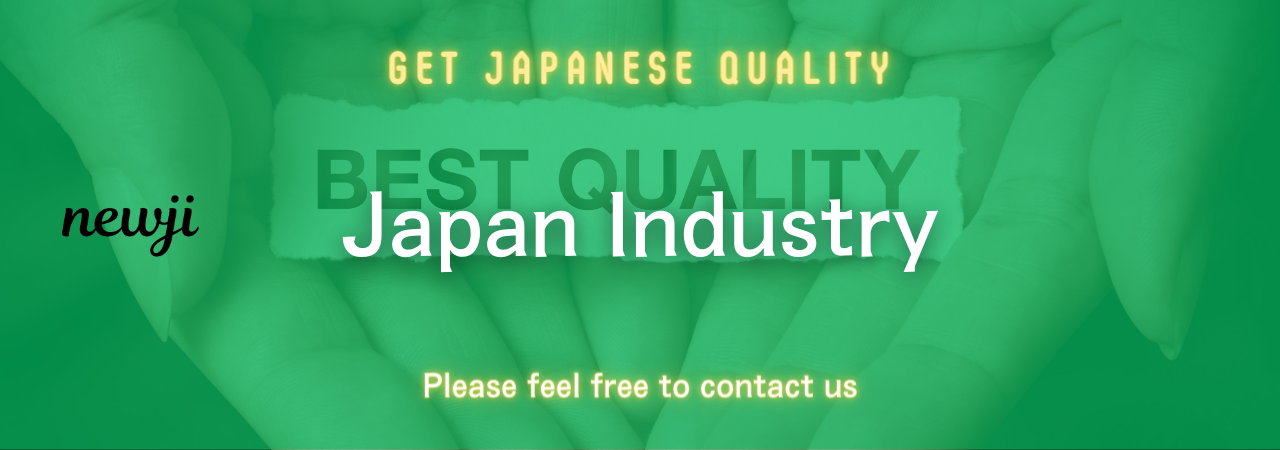
目次
Understanding Vibration and Noise in Machinery
Vibration and noise are common challenges faced in the operation of machinery.
They not only affect the efficiency and longevity of machines but also pose risks to the health and comfort of individuals working around them.
Understanding the basics of vibration and noise is the first step towards effectively managing these phenomena.
Vibration in machinery occurs when parts of the machine move back and forth or oscillate rapidly.
This movement can be due to various reasons such as imbalances, misalignments, or external forces acting on the machine.
Noise, on the other hand, is a by-product of these vibrations and can be a combination of various sound frequencies emitted by the machine.
Addressing vibration and noise is crucial as excessive levels can lead to equipment failure, increased maintenance costs, and workplace safety issues.
Therefore, it’s essential to employ effective techniques to reduce these unwanted effects.
Causes of Vibration and Noise in Machinery
Identifying the root causes of vibration and noise is crucial for implementing the right solutions.
Here’s a look at the most common causes:
1. Imbalance
Imbalance occurs when the machine’s rotating parts are not evenly distributed around the axis of rotation.
This leads to uneven centrifugal forces, resulting in vibration and noise.
Imbalances can arise due to manufacturing defects, wear and tear, or material build-up.
2. Misalignment
Misalignment happens when components in a machine are not properly aligned, causing parts to rub or strike against each other.
This can result in significant vibrations and increased noise levels.
Misalignment can occur during assembly or due to changes over time as components settle.
3. Loose Parts
Loose parts within machinery can vibrate independently when the machine operates.
These parts can cause rattling noises and increase the wear on components, leading to further noise and vibration issues.
4. External Forces
Machinery exposed to environmental forces, such as wind or seismic activity, can experience additional stresses that manifest as vibrations.
These external forces can amplify existing vibration and noise issues.
Techniques to Reduce Vibration and Noise
Once the causes of vibration and noise are identified, implementing reduction techniques can help improve machinery performance and workplace conditions.
1. Balancing Rotating Parts
To address imbalance, it’s important to ensure that all rotating parts are balanced.
This can be done by adding or removing weight from the rotor or using balancing machines to correct the imbalance.
Regular maintenance and inspections can help identify and rectify imbalances early on.
2. Proper Alignment
Ensuring that all machine components are correctly aligned is key to reducing vibration and noise caused by misalignment.
Precision tools and alignment instruments can be used during the assembly and maintenance of machinery to achieve this.
3. Secure Fastenings
Tightening and securing all parts and fastenings within the machinery can prevent them from becoming loose over time.
Regular checks and tightening sessions are recommended to maintain machine integrity and reduce noise.
4. Use of Damping Materials
Damping materials can help absorb and dissipate vibrations, reducing the resultant noise.
Materials such as rubber, foam, or acoustic panels can be strategically placed within machinery to minimize vibration transmission.
5. Isolation Techniques
Vibration isolation involves decoupling the machine from its surroundings to prevent vibration transmission.
This can be achieved using isolators such as spring mounts, rubber pads, or inertia blocks that absorb and neutralize vibrations.
6. Lubrication
Proper lubrication of moving parts reduces friction and wear, thereby decreasing the amount of vibration and noise produced.
Frequent checks on lubrication levels and conditions can help maintain optimal machinery performance.
The Importance of Monitoring and Maintenance
Continuous monitoring and maintenance play critical roles in managing vibration and noise levels.
Implementing regular maintenance schedules helps in early detection of issues that may lead to excessive vibration or noise.
Condition monitoring tools, such as vibration analyzers and sound level meters, can provide valuable data to identify unwanted changes in machine behavior.
By addressing these potential issues promptly, companies can enhance machine lifespan, reduce operational costs, and create a safer work environment for their employees.
Conclusion
Understanding and addressing vibration and noise in machinery is vital for ensuring efficient operations and maintaining a comfortable work environment.
By identifying the root causes and employing effective reduction techniques, companies can significantly reduce the negative impacts of these phenomena.
Regular maintenance and condition monitoring are essential in sustaining optimal machine performance and preventing costly repairs and downtime.
Through continuous efforts and advancements in technology, vibration and noise challenges can be managed effectively, paving the way for better machinery performance and workplace conditions.
資料ダウンロード
QCD調達購買管理クラウド「newji」は、調達購買部門で必要なQCD管理全てを備えた、現場特化型兼クラウド型の今世紀最高の購買管理システムとなります。
ユーザー登録
調達購買業務の効率化だけでなく、システムを導入することで、コスト削減や製品・資材のステータス可視化のほか、属人化していた購買情報の共有化による内部不正防止や統制にも役立ちます。
NEWJI DX
製造業に特化したデジタルトランスフォーメーション(DX)の実現を目指す請負開発型のコンサルティングサービスです。AI、iPaaS、および先端の技術を駆使して、製造プロセスの効率化、業務効率化、チームワーク強化、コスト削減、品質向上を実現します。このサービスは、製造業の課題を深く理解し、それに対する最適なデジタルソリューションを提供することで、企業が持続的な成長とイノベーションを達成できるようサポートします。
オンライン講座
製造業、主に購買・調達部門にお勤めの方々に向けた情報を配信しております。
新任の方やベテランの方、管理職を対象とした幅広いコンテンツをご用意しております。
お問い合わせ
コストダウンが利益に直結する術だと理解していても、なかなか前に進めることができない状況。そんな時は、newjiのコストダウン自動化機能で大きく利益貢献しよう!
(Β版非公開)