- お役立ち記事
- Gear Basics: Strength Design and Vibration/Noise Reduction Techniques
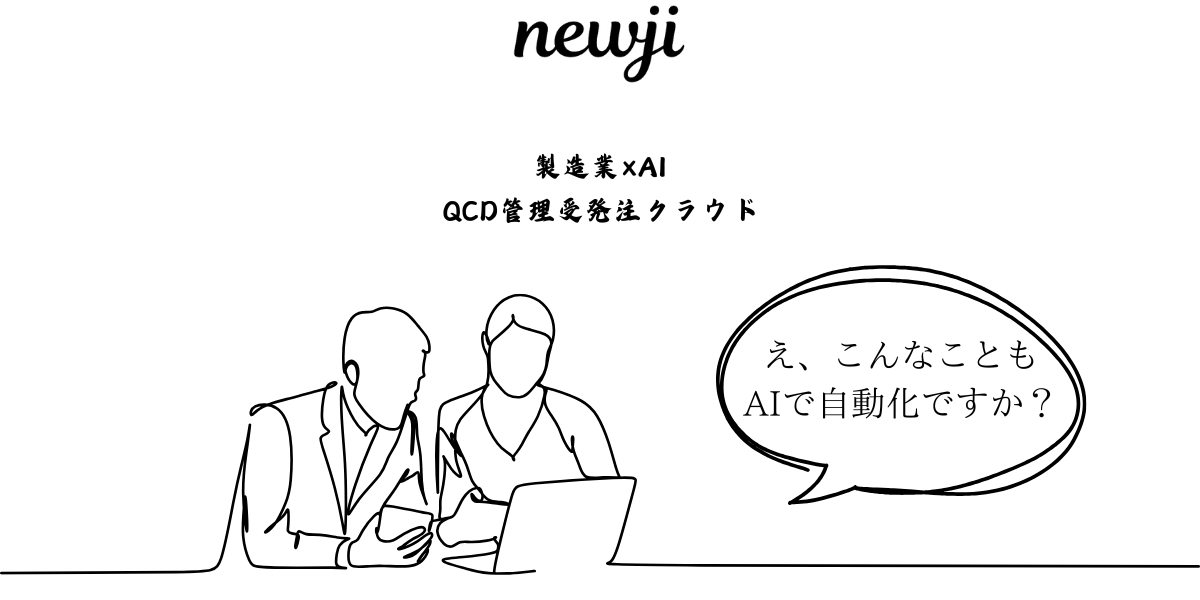
Gear Basics: Strength Design and Vibration/Noise Reduction Techniques
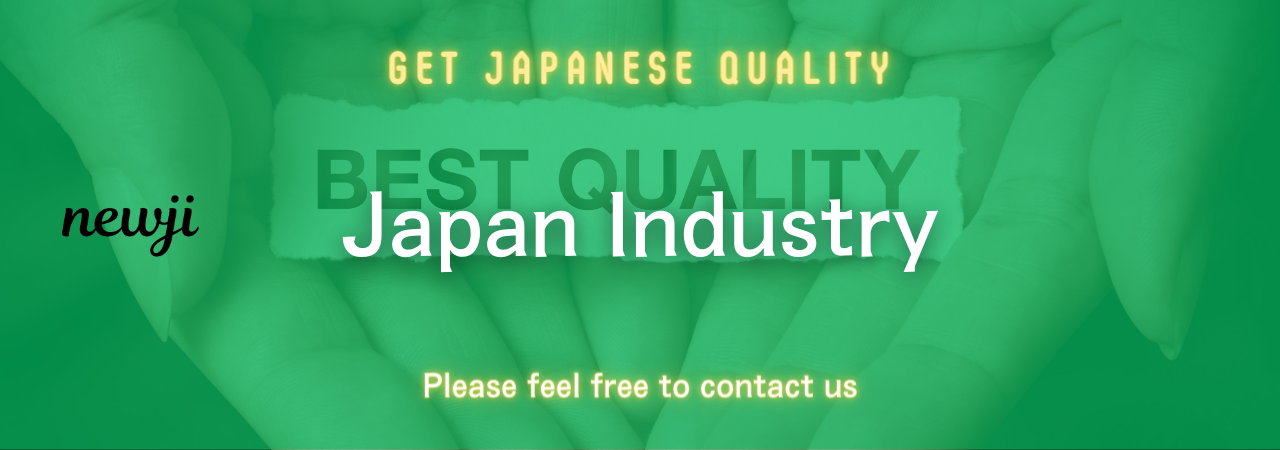
目次
Introduction to Gear Basics
Gears play a crucial role in our daily lives, whether it’s in a child’s toy or a state-of-the-art automobile.
They are mechanical components used to transmit motion and power between machinery parts.
Understanding gears goes beyond seeing them as simple, interlocking teeth; it involves a deep dive into their strength design and vibration/noise reduction techniques.
Gears come in various sizes and shapes, but they all share the same basic principle: they transmit rotational motion and torque between mechanical compoents.
This transmission allows for speed adjustments, direction changes, and force multiplication.
When it comes to designing efficient gears, strength and noise reduction are key considerations that ensure durability and user comfort.
Strength Design of Gears
Understanding Gear Strength
The concept of gear strength revolves around the ability to withstand the forces it encounters during operation.
Each gear is designed to handle stress and strain without failing or deforming.
The material choice, gear size, and tooth shape significantly affect the strength of a gear.
Material Selection
Material choice is a fundamental aspect of gear strength design.
Common materials include steel, iron, and various alloys, each offering a unique blend of strength and durability.
Steel, known for its high tensile strength, is often used for heavy-duty applications.
Iron, although less strong than steel, provides good wear resistance and can be a cost-effective option.
Gear Tooth Design
The shape and size of gear teeth play a critical role in gear strength.
Involute gear teeth are widely used because they provide a constant speed ratio and are easy to manufacture.
The tooth profile needs to be carefully designed to minimize stress concentrations, which can lead to premature failure.
Load Distribution
Proper load distribution is essential to avoid overloading a single gear tooth.
When teeth are subjected to uneven loads, it can lead to excessive wear and potential failure.
Designers utilize helical gears and other strategies to distribute load evenly across multiple teeth, enhancing overall gear strength.
Vibration and Noise Reduction Techniques
Causes of Gear Vibration and Noise
Vibration and noise in gears are caused by misalignment, manufacturing errors, and improper lubrication.
These factors lead to imbalanced rotation, which produces unwanted noise and vibration, degrading user experience and potentially causing mechanical failures.
Precision Manufacturing
Precision in manufacturing is key to reducing gear noise and vibration.
High-quality manufacturing processes, such as grinding and honing, produce smoother gear surfaces, leading to less friction and more silent operation.
Proper Lubrication
Lubrication reduces friction between gear teeth, minimizing wear and noise.
Using the correct lubricant for a particular gear application ensures smooth operation and contributes to longer gear life.
Regular maintenance and checking of lubricant levels are essential for keeping gears operating efficiently and quietly.
Gear Alignment
Proper alignment between gears is critical for reducing vibration and noise.
Misaligned gears can create undesirable forces that lead to excessive vibration.
Adjustments and realignment should be performed during installation and maintenance to maintain optimal performance.
Advanced Techniques for Gear Optimization
Finite Element Analysis (FEA)
Finite Element Analysis (FEA) is a powerful tool for optimizing gear design.
It allows engineers to simulate stress distribution within gears, identify potential failure points, and make necessary adjustments to improve strength and durability.
Dynamic Balancing
Dynamic balancing involves compensating for uneven weight distribution within a gear, reducing vibrations.
This is particularly important in high-speed applications where stability is crucial.
By ensuring the gear’s weight is balanced during rotation, noise and wear can be significantly reduced.
Use of Advanced Materials
The development of advanced materials, such as composites and specialized alloys, offers new opportunities for gear design.
These materials provide enhanced strength and resistance to wear, allowing for lighter and more efficient gears.
Conclusion
Understanding gear basics, including strength design and vibration/noise reduction techniques, is essential for creating efficient and reliable machinery.
The choice of materials, tooth design, and alignment all contribute to a gear’s performance.
Likewise, precision in manufacturing and advanced analysis tools help in reducing noise and vibration, enhancing user experience.
Gears may seem simple, but their design requires meticulous attention to detail and advanced engineering techniques.
Whether for industrial applications or everyday gadgets, well-designed gears ensure smooth and efficient operation.
By continuing to innovate and improve on these basic principles, engineers can develop even more sophisticated mechanical systems for the future.
資料ダウンロード
QCD調達購買管理クラウド「newji」は、調達購買部門で必要なQCD管理全てを備えた、現場特化型兼クラウド型の今世紀最高の購買管理システムとなります。
ユーザー登録
調達購買業務の効率化だけでなく、システムを導入することで、コスト削減や製品・資材のステータス可視化のほか、属人化していた購買情報の共有化による内部不正防止や統制にも役立ちます。
NEWJI DX
製造業に特化したデジタルトランスフォーメーション(DX)の実現を目指す請負開発型のコンサルティングサービスです。AI、iPaaS、および先端の技術を駆使して、製造プロセスの効率化、業務効率化、チームワーク強化、コスト削減、品質向上を実現します。このサービスは、製造業の課題を深く理解し、それに対する最適なデジタルソリューションを提供することで、企業が持続的な成長とイノベーションを達成できるようサポートします。
オンライン講座
製造業、主に購買・調達部門にお勤めの方々に向けた情報を配信しております。
新任の方やベテランの方、管理職を対象とした幅広いコンテンツをご用意しております。
お問い合わせ
コストダウンが利益に直結する術だと理解していても、なかなか前に進めることができない状況。そんな時は、newjiのコストダウン自動化機能で大きく利益貢献しよう!
(Β版非公開)