- お役立ち記事
- Revolutionizing Japanese Manufacturing: The Impact of Project Progress Management Systems
Revolutionizing Japanese Manufacturing: The Impact of Project Progress Management Systems
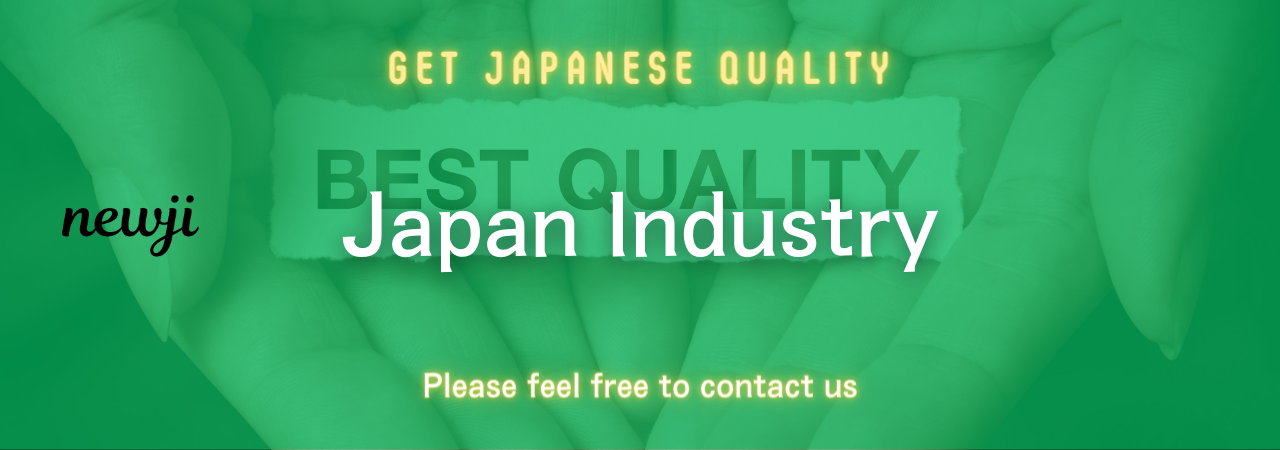
目次
Introduction
In the rapidly evolving landscape of global manufacturing, Japanese companies have consistently stood out for their commitment to quality, efficiency, and innovation. Central to this success is the implementation of sophisticated Project Progress Management Systems. These systems have revolutionized Japanese manufacturing by enhancing operational efficiency, fostering better supplier relationships, and ensuring the highest standards of quality control. This article delves into the impact of Project Progress Management Systems on Japanese manufacturing, exploring their advantages, challenges, and best practices from a procurement and purchasing perspective.
Overview of Project Progress Management Systems
Project Progress Management Systems (PPMS) are comprehensive tools designed to oversee and manage the various facets of a manufacturing project. These systems integrate planning, execution, monitoring, and control processes to ensure that projects are completed on time, within scope, and budget. In the context of Japanese manufacturing, PPMS are tailored to align with the country’s renowned production methodologies, such as Lean Manufacturing and Just-In-Time (JIT) inventory systems.
The Role of Project Management in Japanese Manufacturing
Japanese manufacturing has long been associated with meticulous planning and continuous improvement. Project management plays a crucial role in this paradigm by providing a structured approach to achieving manufacturing excellence. Effective project management ensures that all aspects of production, from procurement to quality control, are seamlessly coordinated, leading to enhanced productivity and reduced waste.
Advantages of Implementing Project Progress Management Systems
Enhanced Efficiency
PPMS streamline manufacturing processes by automating routine tasks and optimizing resource allocation. This leads to significant time savings and increased operational efficiency. By providing real-time data and analytics, these systems enable managers to make informed decisions swiftly, minimizing delays and bottlenecks in the production line.
Improved Quality Control
Maintaining high-quality standards is paramount in Japanese manufacturing. PPMS facilitate rigorous quality control by tracking performance metrics, identifying defects, and implementing corrective actions promptly. This proactive approach helps in maintaining consistent product quality and reducing the incidence of defects.
Better Resource Allocation
Effective resource management is critical for minimizing costs and maximizing output. PPMS provide comprehensive visibility into resource utilization, enabling managers to allocate manpower, materials, and machinery more effectively. This ensures that resources are used optimally, reducing wastage and enhancing productivity.
Increased Transparency and Accountability
Transparency is a cornerstone of Japanese manufacturing practices. PPMS promote transparency by providing detailed reports and dashboards that track project progress and individual performance. This fosters a culture of accountability, as employees are aware of their responsibilities and the impact of their work on overall project outcomes.
Disadvantages and Challenges
High Initial Investment
Implementing a robust PPMS requires significant financial investment in software, hardware, and training. For smaller manufacturers, this initial cost can be a barrier to adoption. However, the long-term benefits often outweigh the initial expenditure through increased efficiency and cost savings.
Complexity of Integration
Integrating PPMS with existing manufacturing systems and processes can be complex and time-consuming. It requires careful planning and expertise to ensure seamless integration without disrupting ongoing operations. This challenge necessitates the involvement of skilled professionals during the implementation phase.
Resistance to Change
Change management is a critical aspect of implementing PPMS. Employees accustomed to traditional manufacturing processes may resist adopting new systems and technologies. Overcoming this resistance requires effective communication, training, and fostering a culture that embraces continuous improvement.
Training Requirements
To fully leverage the capabilities of PPMS, comprehensive training is essential. Employees need to be proficient in using the system to maximize its benefits. This entails ongoing training programs and support to ensure that staff members are comfortable and competent in utilizing the new tools.
Impact on Procurement and Purchasing
Streamlining Supply Chain Processes
PPMS enhance the efficiency of supply chain management by providing real-time visibility into procurement activities. This allows for better demand forecasting, inventory management, and supplier coordination. Consequently, manufacturers can reduce lead times, minimize inventory costs, and ensure timely delivery of materials.
Enhancing Supplier Relationships
Effective project management fosters stronger relationships with suppliers by facilitating clear communication and collaboration. PPMS enable manufacturers to share project timelines, quality standards, and performance expectations with suppliers, ensuring alignment and mutual understanding. This collaboration leads to improved supplier performance and reliability.
Supplier Negotiation Techniques in the Context of Project Management Systems
Data-Driven Negotiations
PPMS provide access to detailed data and analytics, empowering procurement teams to engage in informed negotiations with suppliers. By leveraging performance metrics, cost analyses, and market trends, manufacturers can negotiate better terms, prices, and delivery schedules, ensuring mutually beneficial agreements.
Collaborative Planning
Collaborative planning through PPMS fosters a partnership approach with suppliers. By involving suppliers in the project planning process, manufacturers can align their objectives, address potential challenges proactively, and develop strategies that benefit both parties. This collaborative stance enhances trust and fosters long-term partnerships.
Long-term Partnerships
PPMS facilitate the development of long-term relationships with key suppliers by establishing clear expectations and consistent performance standards. These systems enable continuous monitoring and evaluation of supplier performance, ensuring that only reliable and high-performing suppliers are retained, thereby enhancing the overall supply chain resilience.
Market Conditions Influencing Project Management Systems in Japanese Manufacturing
Globalization and Competition
In an increasingly globalized market, Japanese manufacturers face intense competition from both domestic and international players. PPMS provide a competitive edge by enabling manufacturers to optimize their operations, reduce costs, and respond swiftly to market changes, thereby maintaining their market position.
Technological Advancements
Advancements in technology, such as artificial intelligence, machine learning, and the Internet of Things (IoT), are transforming manufacturing processes. PPMS integrate these technologies to offer enhanced capabilities, such as predictive maintenance, real-time monitoring, and advanced data analytics, driving innovation and efficiency.
Changing Customer Demands
Customers today demand higher quality, customization, and faster delivery. PPMS enable manufacturers to be more responsive to these demands by providing the tools necessary for agile project management, flexible production scheduling, and efficient resource allocation. This adaptability is critical for meeting evolving customer expectations.
Best Practices for Implementing Project Progress Management Systems
Comprehensive Planning
Successful implementation of PPMS begins with thorough planning. This involves defining clear objectives, assessing current processes, and identifying the specific needs of the organization. A well-crafted implementation plan ensures that the system aligns with the company’s goals and integrates seamlessly with existing workflows.
Stakeholder Engagement
Engaging all relevant stakeholders, including management, employees, and suppliers, is crucial for the successful adoption of PPMS. Stakeholder involvement fosters buy-in, ensures that diverse perspectives are considered, and mitigates resistance to change. Regular communication and collaboration are key to maintaining stakeholder support throughout the implementation process.
Continuous Monitoring and Improvement
PPMS should not be viewed as a one-time implementation but as an ongoing process of continuous improvement. Regular monitoring of system performance, user feedback, and project outcomes allows manufacturers to identify areas for enhancement and make necessary adjustments. This iterative approach ensures that the system remains effective and evolves with changing business needs.
Case Studies: Success Stories in Japanese Manufacturing
Several Japanese manufacturers have successfully leveraged PPMS to achieve remarkable results. For instance, Toyota’s implementation of advanced project management systems has been instrumental in maintaining its leadership in Lean Manufacturing. By integrating PPMS into its production processes, Toyota has enhanced efficiency, reduced waste, and consistently delivered high-quality vehicles. Similarly, Panasonic has utilized PPMS to streamline its supply chain operations, resulting in improved supplier collaboration and faster time-to-market for its products. These success stories underscore the transformative impact of PPMS on Japanese manufacturing.
Future Trends in Project Progress Management Systems
The future of PPMS in Japanese manufacturing is poised to be shaped by several emerging trends. The integration of artificial intelligence and machine learning will enable more predictive and adaptive project management, allowing manufacturers to anticipate and respond to changes proactively. The adoption of blockchain technology can enhance transparency and traceability in supply chains, further strengthening supplier relationships. Additionally, the rise of remote and hybrid work models will necessitate the development of PPMS that support seamless collaboration and communication across diverse and geographically dispersed teams. These trends will continue to drive innovation and efficiency in Japanese manufacturing.
Conclusion
Project Progress Management Systems have fundamentally transformed Japanese manufacturing by enhancing efficiency, improving quality control, and fostering stronger supplier relationships. Despite the challenges associated with implementation, the long-term benefits of PPMS make them an invaluable asset for manufacturers striving for excellence in a competitive global market. By embracing best practices and staying abreast of emerging trends, Japanese manufacturers can continue to leverage PPMS to drive innovation, optimize operations, and maintain their esteemed position in the global manufacturing landscape.
資料ダウンロード
QCD調達購買管理クラウド「newji」は、調達購買部門で必要なQCD管理全てを備えた、現場特化型兼クラウド型の今世紀最高の購買管理システムとなります。
ユーザー登録
調達購買業務の効率化だけでなく、システムを導入することで、コスト削減や製品・資材のステータス可視化のほか、属人化していた購買情報の共有化による内部不正防止や統制にも役立ちます。
NEWJI DX
製造業に特化したデジタルトランスフォーメーション(DX)の実現を目指す請負開発型のコンサルティングサービスです。AI、iPaaS、および先端の技術を駆使して、製造プロセスの効率化、業務効率化、チームワーク強化、コスト削減、品質向上を実現します。このサービスは、製造業の課題を深く理解し、それに対する最適なデジタルソリューションを提供することで、企業が持続的な成長とイノベーションを達成できるようサポートします。
オンライン講座
製造業、主に購買・調達部門にお勤めの方々に向けた情報を配信しております。
新任の方やベテランの方、管理職を対象とした幅広いコンテンツをご用意しております。
お問い合わせ
コストダウンが利益に直結する術だと理解していても、なかなか前に進めることができない状況。そんな時は、newjiのコストダウン自動化機能で大きく利益貢献しよう!
(Β版非公開)