- お役立ち記事
- Revolutionizing Japanese Manufacturing: The Impact of 3D Inspection Systems
Revolutionizing Japanese Manufacturing: The Impact of 3D Inspection Systems
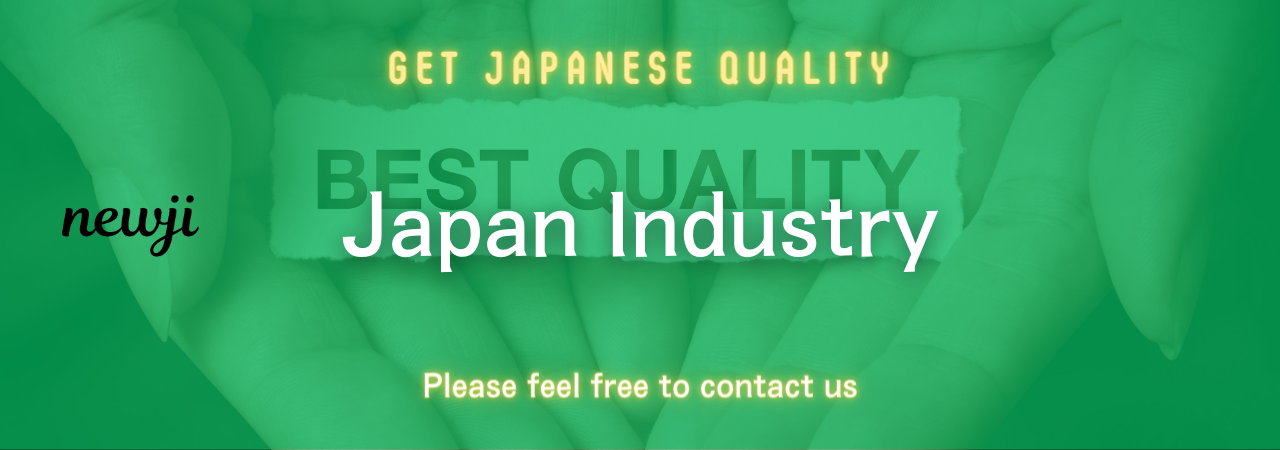
目次
Introduction to 3D Inspection Systems in Japanese Manufacturing
In the rapidly evolving landscape of manufacturing, precision and efficiency are paramount.
Japanese manufacturing has long been synonymous with quality and innovation.
One of the key advancements contributing to this reputation is the adoption of 3D inspection systems.
These systems are revolutionizing manufacturing processes by enhancing accuracy, reducing errors, and streamlining production.
This article delves into the impact of 3D inspection systems on Japanese manufacturing, exploring their advantages, challenges, and best practices.
Understanding 3D Inspection Systems
3D inspection systems utilize advanced technology to measure and analyze the dimensions and geometry of manufactured parts.
Unlike traditional 2D inspection methods, 3D systems provide a comprehensive view, capturing intricate details and complex shapes.
These systems employ various techniques such as laser scanning, structured light, and coordinate measuring machines (CMM) to acquire precise measurements.
The data collected is then processed and compared against design specifications to ensure accuracy and quality.
Components of 3D Inspection Systems
A typical 3D inspection system comprises several key components:
- Data Acquisition Devices: These include lasers, cameras, and sensors that capture the physical attributes of the part.
- Software: Advanced software processes the raw data, creating detailed 3D models and performing analyses.
- Automation Integration: Integration with manufacturing systems allows for seamless data flow and real-time quality control.
Advantages of 3D Inspection Systems
The implementation of 3D inspection systems offers numerous benefits to Japanese manufacturers.
Enhanced Accuracy and Precision
3D systems provide unparalleled accuracy in measuring complex geometries, reducing the likelihood of defects.
This precision ensures that products meet stringent quality standards, enhancing customer satisfaction.
Increased Efficiency
Automated 3D inspections significantly speed up the quality control process.
Manufacturers can conduct inspections faster than manual methods, leading to shorter production cycles and increased throughput.
Cost Savings
By minimizing errors and reducing the need for rework, 3D inspection systems contribute to substantial cost savings.
Additionally, early detection of defects prevents costly recalls and maintains the integrity of the supply chain.
Improved Data Analysis
3D inspection systems generate detailed data that can be analyzed to identify trends and areas for improvement.
This data-driven approach facilitates continuous improvement and innovation in manufacturing processes.
Challenges in Implementing 3D Inspection Systems
While the advantages are significant, there are challenges associated with the adoption of 3D inspection systems.
High Initial Investment
The acquisition and installation of 3D inspection systems require a substantial financial investment.
For some companies, especially small and medium-sized enterprises, the upfront costs can be a barrier to implementation.
Technical Expertise
Operating and maintaining 3D inspection systems necessitates specialized technical knowledge.
Japanese manufacturers must invest in training their workforce to effectively utilize and manage these advanced systems.
Integration with Existing Systems
Integrating 3D inspection systems with existing manufacturing and quality control processes can be complex.
Ensuring seamless data flow and compatibility requires careful planning and coordination.
Supplier Negotiation Techniques for 3D Inspection Systems
Effective negotiation with suppliers is crucial to securing the best terms for 3D inspection systems.
Understanding Market Conditions
Japanese manufacturers should stay informed about market trends and pricing for 3D inspection technologies.
This knowledge enables informed negotiations and helps anticipate supplier pricing strategies.
Building Strong Relationships
Cultivating strong, long-term relationships with suppliers can lead to better terms, priority support, and access to the latest technologies.
Trust and collaboration are key components of successful supplier partnerships.
Leveraging Competitive Bidding
Engaging multiple suppliers in a competitive bidding process encourages competitive pricing and fosters innovation.
It also provides manufacturers with options to select the supplier that best meets their quality and service requirements.
Negotiating Flexibility and Support
In addition to price, manufacturers should negotiate for flexibility in payment terms, warranties, and ongoing support services.
Comprehensive support ensures that the systems operate efficiently and that any issues are promptly addressed.
Best Practices for Implementing 3D Inspection Systems
To maximize the benefits of 3D inspection systems, Japanese manufacturers should adhere to several best practices.
Comprehensive Training Programs
Investing in thorough training ensures that employees are proficient in operating and maintaining 3D inspection systems.
Ongoing education keeps the workforce updated on technological advancements and best practices.
Integration with Quality Management Systems
Seamlessly integrating 3D inspection data with existing quality management systems enhances data utilization and decision-making.
This integration supports a holistic approach to quality control and continuous improvement.
Regular Maintenance and Calibration
Routine maintenance and calibration of 3D inspection systems are essential to maintain accuracy and reliability.
Scheduled upkeep prevents system degradation and extends the lifespan of the equipment.
Data Security and Management
Protecting the data generated by 3D inspection systems is critical.
Implementing robust data security measures and efficient data management practices safeguards intellectual property and sensitive information.
Impact on Supply Chain and Logistics
3D inspection systems also influence supply chain and logistics operations.
Streamlined Supply Chain
Accurate inspections reduce the likelihood of defects passing through the supply chain, minimizing disruptions and ensuring smooth operations.
Enhanced Supplier Coordination
Detailed inspection data facilitates better communication and coordination with suppliers, fostering collaborative relationships and mutual improvements.
Reduced Lead Times
Efficient quality control processes contribute to shorter lead times, enhancing the overall responsiveness of the supply chain.
Future Trends in 3D Inspection Systems
The evolution of 3D inspection systems is set to continue, bringing new advancements and capabilities.
Integration with Artificial Intelligence
AI-powered analytics will enhance the capabilities of 3D inspection systems, enabling predictive maintenance and more sophisticated defect detection.
IoT and Real-Time Monitoring
The Internet of Things (IoT) will facilitate real-time monitoring and data sharing, further integrating 3D inspection systems into the digital manufacturing ecosystem.
Advancements in Imaging Technology
Improvements in imaging technologies will increase the resolution and speed of 3D inspections, enabling even more precise measurements.
Sustainability and Green Manufacturing
3D inspection systems contribute to sustainability by reducing waste and improving resource efficiency, aligning with the growing emphasis on green manufacturing practices.
Case Studies: Success Stories in Japanese Manufacturing
Several Japanese manufacturers have successfully implemented 3D inspection systems, yielding significant benefits.
Automotive Industry
Leading automotive manufacturers have integrated 3D inspection systems into their production lines, enhancing the precision of components and reducing assembly errors. This integration has led to improved vehicle quality and customer satisfaction.
Electronics Manufacturing
In the electronics sector, 3D inspection systems are used to ensure the exact placement of components on circuit boards, minimizing defects and enhancing product reliability.
Precision Machinery
Manufacturers of precision machinery utilize 3D inspection systems to maintain tight tolerances and high-quality standards, reinforcing their reputation for excellence and reliability.
Conclusion
3D inspection systems are transforming Japanese manufacturing by providing enhanced accuracy, increased efficiency, and substantial cost savings.
Despite the challenges of high initial investment and the need for technical expertise, the benefits outweigh the drawbacks.
By adopting best practices and effective supplier negotiation techniques, Japanese manufacturers can successfully implement 3D inspection systems.
Looking ahead, continued advancements in technology will further solidify the role of 3D inspections in driving innovation and maintaining Japan’s competitive edge in the global manufacturing arena.
Embracing these systems not only ensures high-quality production but also fosters a culture of continuous improvement and excellence.
資料ダウンロード
QCD調達購買管理クラウド「newji」は、調達購買部門で必要なQCD管理全てを備えた、現場特化型兼クラウド型の今世紀最高の購買管理システムとなります。
ユーザー登録
調達購買業務の効率化だけでなく、システムを導入することで、コスト削減や製品・資材のステータス可視化のほか、属人化していた購買情報の共有化による内部不正防止や統制にも役立ちます。
NEWJI DX
製造業に特化したデジタルトランスフォーメーション(DX)の実現を目指す請負開発型のコンサルティングサービスです。AI、iPaaS、および先端の技術を駆使して、製造プロセスの効率化、業務効率化、チームワーク強化、コスト削減、品質向上を実現します。このサービスは、製造業の課題を深く理解し、それに対する最適なデジタルソリューションを提供することで、企業が持続的な成長とイノベーションを達成できるようサポートします。
オンライン講座
製造業、主に購買・調達部門にお勤めの方々に向けた情報を配信しております。
新任の方やベテランの方、管理職を対象とした幅広いコンテンツをご用意しております。
お問い合わせ
コストダウンが利益に直結する術だと理解していても、なかなか前に進めることができない状況。そんな時は、newjiのコストダウン自動化機能で大きく利益貢献しよう!
(Β版非公開)