- お役立ち記事
- “Decoding ‘Grain Size’: The Hidden Power Behind Japanese Manufacturing Excellence”
“Decoding ‘Grain Size’: The Hidden Power Behind Japanese Manufacturing Excellence”
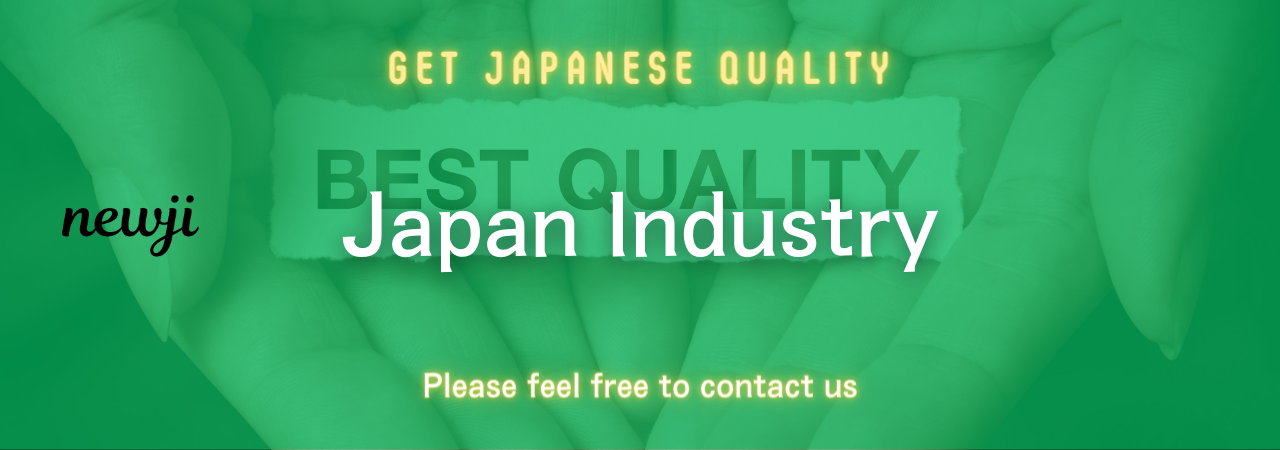
目次
Understanding Grain Size in Japanese Manufacturing
Grain size is a pivotal factor in the manufacturing processes that underpin Japan’s reputation for excellence. This concept, rooted in materials science, refers to the dimensions and distribution of grains within a metal or alloy. The meticulous control of grain size directly influences the mechanical properties, durability, and performance of the final product. In Japanese manufacturing, especially in industries like automotive and electronics, maintaining optimal grain size is crucial for achieving superior quality and reliability.
Grain size affects several key properties of materials, including strength, toughness, ductility, and resistance to wear and corrosion. Smaller grains typically enhance strength and toughness, making the material more resilient to stress and impact. Conversely, larger grains can improve ductility, allowing the material to deform without breaking. Japanese manufacturers leverage these properties to tailor materials for specific applications, ensuring that each product meets stringent quality standards.
The Role of Grain Size in Procurement and Purchasing
In the context of procurement and purchasing, understanding grain size is essential for selecting the right materials and suppliers. Japanese suppliers are renowned for their ability to precisely control grain size through advanced metallurgical techniques. This capability ensures that the materials they provide meet exact specifications, reducing the likelihood of defects and enhancing the overall quality of the final product.
When procuring materials, companies must evaluate suppliers based on their ability to maintain consistent grain size. This involves assessing the supplier’s manufacturing processes, quality control measures, and certifications. Partnering with suppliers who excel in grain size management can lead to long-term benefits, including lower production costs, fewer quality issues, and increased customer satisfaction.
Additionally, knowledge of grain size allows procurement professionals to make informed decisions about material specifications and cost trade-offs. For instance, selecting a supplier that can offer smaller grain sizes may come at a higher cost, but the resulting increase in material strength and durability can justify the investment by reducing maintenance and replacement expenses over time.
Advantages of Precision Grain Size Control
Precision control of grain size offers numerous advantages in manufacturing:
1. **Enhanced Material Properties:** Consistent grain size improves mechanical properties such as strength and toughness, leading to more reliable products.
2. **Improved Consistency:** Tight control over grain size ensures uniformity across batches, which is critical for maintaining product quality.
3. **Reduced Defects:** Better grain size control minimizes defects like cracks and fractures, enhancing the lifespan of products.
4. **Increased Efficiency:** High-quality materials reduce the need for rework and repairs, improving overall production efficiency.
Disadvantages of Grain Size Variability
Conversely, variability in grain size can lead to several challenges:
1. **Inconsistent Quality:** Variations in grain size can result in uneven product performance and reduced reliability.
2. **Increased Costs:** Defects and variability necessitate additional quality control measures and can lead to higher production costs.
3. **Supply Chain Disruptions:** Inconsistent material properties can disrupt manufacturing processes and timelines, affecting overall supply chain efficiency.
Supplier Negotiation Techniques
Effective negotiation with Japanese suppliers requires a deep understanding of their emphasis on grain size and material quality. Here are some strategies to consider:
Building Strong Relationships
Japanese business culture places high value on long-term relationships and trust. Investing time in building strong, respectful relationships with suppliers can lead to more favorable negotiations and better collaboration on quality control initiatives.
Emphasizing Quality Requirements
Clearly communicate the importance of grain size and other material specifications. Providing detailed requirements and expectations helps suppliers understand the critical nature of these factors and encourages them to align their processes accordingly.
Leveraging Technical Expertise
Demonstrating a solid understanding of grain size and its impact on product quality can enhance credibility and facilitate more effective negotiations. Collaborate with suppliers on technical aspects to find mutually beneficial solutions that meet quality and cost objectives.
Exploring Joint Development Opportunities
Engage suppliers in joint development projects aimed at improving grain size control and material performance. This collaborative approach can lead to innovations that benefit both parties and strengthen the partnership.
Market Conditions Affecting Grain Size Control
The global market for high-precision materials is highly competitive, with Japanese manufacturers maintaining a significant edge through their mastery of grain size control. Several factors influence this dynamic:
Technological Advancements
Continuous advancements in manufacturing technology enable Japanese suppliers to achieve better grain size precision. Investments in research and development, coupled with automation and advanced quality control systems, keep Japanese manufacturers at the forefront of material science.
Supply Chain Resilience
Japanese suppliers’ ability to maintain strict quality standards, including grain size control, contributes to their resilience in the global supply chain. This reliability is particularly valuable during disruptions, as consistent material quality helps ensure uninterrupted production for their clients.
Regulatory Standards
International regulatory standards increasingly demand high precision in material properties. Japanese manufacturers’ expertise in controlling grain size positions them well to meet these stringent requirements, enhancing their appeal to global clients.
Economic Factors
Economic fluctuations can impact the cost and availability of materials. Japanese suppliers often navigate these challenges by maintaining strong relationships with raw material providers and investing in efficient production processes that mitigate cost increases without compromising grain size control.
Best Practices for Managing Grain Size in Procurement
Implementing best practices in procurement can help maximize the benefits of working with Japanese suppliers skilled in grain size control:
Comprehensive Supplier Evaluation
Conduct thorough evaluations of potential suppliers, focusing on their capabilities in grain size management. Assess their manufacturing processes, quality control systems, and track record in delivering consistent material quality.
Detailed Specification Documentation
Provide clear and detailed specifications regarding grain size and other material properties. This ensures that suppliers understand the exact requirements and can adjust their processes to meet these standards.
Regular Quality Audits
Implement regular quality audits to monitor supplier performance in maintaining grain size consistency. These audits help identify any deviations early, allowing for corrective actions before issues escalate.
Collaborative Improvement Initiatives
Engage in collaborative initiatives aimed at continuous improvement of grain size control. Sharing knowledge and jointly developing solutions can enhance material quality and operational efficiency for both parties.
Investing in Training and Development
Provide training and development opportunities for procurement and quality assurance teams to deepen their understanding of grain size and its implications. This knowledge enables more effective communication and decision-making regarding material procurement.
Case Studies: Successful Grain Size Management in Japanese Manufacturing
Examining real-world examples can illustrate the impact of grain size management on manufacturing excellence:
Automotive Industry
Japanese automotive manufacturers, such as Toyota and Honda, rely heavily on precise grain size control to enhance the strength and durability of vehicle components. By partnering with suppliers who meticulously manage grain size, these companies ensure that their cars meet high safety and performance standards, contributing to their global reputation for reliability.
Electronics Sector
In the electronics industry, Japanese suppliers produce materials with exact grain size specifications to ensure the performance and longevity of components like semiconductors and circuit boards. This precision is crucial for maintaining the intricate functionality of modern electronic devices, allowing Japanese manufacturers to lead in innovation and quality.
Steel Manufacturing
Japanese steel manufacturers excel in controlling grain size to produce high-quality steel with superior mechanical properties. This expertise is leveraged in various applications, from construction to machinery, where consistent material performance is essential for safety and efficiency.
Challenges in Grain Size Optimization
While grain size control offers significant advantages, it also presents certain challenges that manufacturers need to address:
Complexity of Processes
Achieving precise grain size control requires sophisticated manufacturing processes and advanced technologies. This complexity can increase production costs and necessitate specialized knowledge and equipment.
Resource Intensity
Optimizing grain size often involves intensive use of resources, including energy and raw materials. Balancing resource consumption with the need for high-quality materials is a critical consideration for manufacturers striving for sustainability.
Variability in Raw Materials
Variations in the quality and composition of raw materials can impact grain size consistency. Ensuring a steady supply of high-quality raw materials is essential for maintaining grain size control and overall product quality.
Skilled Workforce Requirement
Effective grain size management requires a highly skilled workforce with expertise in materials science and advanced manufacturing techniques. Investing in training and retaining skilled employees is crucial for sustaining excellence in grain size control.
Future Trends in Grain Size Control
Looking ahead, several trends are shaping the future of grain size control in Japanese manufacturing:
Advanced Materials Development
The development of new materials with tailored grain sizes is an area of active research. Innovations in alloy composition and processing techniques will enable the creation of materials with superior properties for specialized applications.
Automation and AI Integration
Automation and artificial intelligence are increasingly being integrated into manufacturing processes to enhance grain size control. AI-driven analytics can predict and adjust process parameters in real-time, ensuring consistent material quality and reducing human error.
Sustainability Initiatives
There is a growing emphasis on sustainable manufacturing practices, which include optimizing grain size control to reduce waste and energy consumption. Sustainable methods of grain size management will become more prevalent as manufacturers seek to minimize their environmental impact.
Global Collaboration
Global collaboration among manufacturers, suppliers, and research institutions is fostering advancements in grain size control. Sharing knowledge and best practices across borders will drive innovation and elevate standards in the manufacturing industry.
Implementing Grain Size Control in Your Supply Chain
Integrating grain size control into your supply chain requires a strategic approach that encompasses supplier selection, process optimization, and continuous improvement:
Supplier Selection and Qualification
Choose suppliers with proven expertise in grain size management. Evaluate their capabilities through audits, certifications, and performance history to ensure they can meet your material quality requirements consistently.
Process Optimization
Work with suppliers to optimize manufacturing processes for better grain size control. This may involve adopting advanced thermal treatments, refining alloy compositions, and implementing precise cooling and heating cycles to achieve the desired grain structure.
Quality Assurance and Testing
Establish robust quality assurance protocols to monitor grain size and other material properties. Utilize advanced testing techniques, such as microscopy and spectroscopy, to verify that materials meet specified grain size criteria.
Continuous Improvement and Feedback
Promote a culture of continuous improvement by regularly reviewing performance data and providing feedback to suppliers. Encourage collaborative efforts to innovate and enhance grain size control methods, ensuring ongoing advancements in material quality.
Conclusion: Harnessing the Power of Grain Size
Grain size control is a fundamental element that drives Japanese manufacturing excellence. By understanding and leveraging the impact of grain size on material properties, procurement and purchasing professionals can make informed decisions that enhance product quality, reduce costs, and foster strong supplier relationships. The meticulous attention to grain size exemplifies the precision and dedication that underpin Japan’s manufacturing prowess, offering valuable lessons and opportunities for global industries seeking to achieve similar levels of excellence.
Embracing best practices in grain size management, investing in supplier partnerships, and staying abreast of technological advancements will enable companies to harness the hidden power of grain size. As the manufacturing landscape continues to evolve, the ability to control and optimize grain size will remain a key differentiator, driving innovation, sustainability, and competitive advantage in the global market.
資料ダウンロード
QCD調達購買管理クラウド「newji」は、調達購買部門で必要なQCD管理全てを備えた、現場特化型兼クラウド型の今世紀最高の購買管理システムとなります。
ユーザー登録
調達購買業務の効率化だけでなく、システムを導入することで、コスト削減や製品・資材のステータス可視化のほか、属人化していた購買情報の共有化による内部不正防止や統制にも役立ちます。
NEWJI DX
製造業に特化したデジタルトランスフォーメーション(DX)の実現を目指す請負開発型のコンサルティングサービスです。AI、iPaaS、および先端の技術を駆使して、製造プロセスの効率化、業務効率化、チームワーク強化、コスト削減、品質向上を実現します。このサービスは、製造業の課題を深く理解し、それに対する最適なデジタルソリューションを提供することで、企業が持続的な成長とイノベーションを達成できるようサポートします。
オンライン講座
製造業、主に購買・調達部門にお勤めの方々に向けた情報を配信しております。
新任の方やベテランの方、管理職を対象とした幅広いコンテンツをご用意しております。
お問い合わせ
コストダウンが利益に直結する術だと理解していても、なかなか前に進めることができない状況。そんな時は、newjiのコストダウン自動化機能で大きく利益貢献しよう!
(Β版非公開)