- お役立ち記事
- Revolution in Robotics: Japan’s Pioneering Role in Global Manufacturing
Revolution in Robotics: Japan’s Pioneering Role in Global Manufacturing
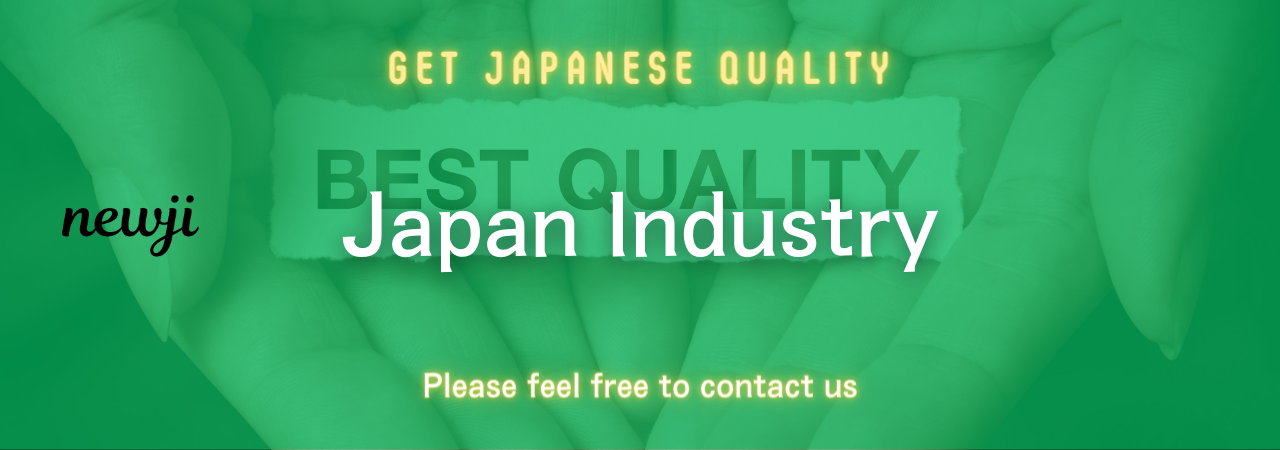
目次
Introduction to Japan’s Robotics Revolution
Japan has long been at the forefront of technological innovation, particularly in the field of robotics.
The country’s commitment to advancing robotics technology has significantly impacted global manufacturing.
Japanese robotics has not only enhanced production efficiency but also set new standards for quality and precision.
This revolution in robotics is a testament to Japan’s dedication to maintaining its competitive edge in the global market.
By integrating cutting-edge technology with robust manufacturing practices, Japan continues to lead the way in robotics-driven manufacturing solutions.
The Evolution of Robotics in Japanese Manufacturing
Japan’s journey in robotics began in the latter half of the 20th century.
Early adoption of industrial robots in the automotive and electronics sectors paved the way for broader applications.
Over the decades, Japanese manufacturers have continually pushed the boundaries of what robotics can achieve.
Advancements in artificial intelligence and machine learning have further enhanced the capabilities of Japanese robots.
Today, robotics in Japan encompasses a wide range of functions, from assembly and welding to quality control and logistics.
This evolution reflects Japan’s strategic approach to integrating technology with manufacturing processes.
Key Areas of Robotics Application in Japan
Automotive Manufacturing
The automotive industry was one of the first to embrace robotics in Japan.
Robots are extensively used in assembly lines for tasks such as welding, painting, and assembly.
This automation has led to increased production rates and consistent quality in vehicle manufacturing.
Japanese automotive robots are renowned for their precision and reliability, contributing to the global reputation of Japanese cars.
Electronics and Semiconductor Manufacturing
In the highly competitive electronics sector, robotics plays a crucial role in maintaining efficiency and quality.
Robotic systems handle intricate tasks like circuit board assembly and component placement with high accuracy.
The ability to produce complex electronic components at scale has been a significant factor in Japan’s success in this industry.
Healthcare and Service Robotics
Beyond industrial applications, Japan has made significant strides in healthcare and service robotics.
Robots are used in hospitals for tasks such as patient care, logistics, and even surgical assistance.
Service robots are also prevalent in various sectors, including hospitality and retail, enhancing customer experiences through automation.
Logistics and Supply Chain Management
Robotics has revolutionized logistics in Japan, with automated guided vehicles and robotic sorting systems optimizing supply chain operations.
These advancements have improved inventory management, reduced operational costs, and increased the speed of goods movement across supply chains.
Advantages of Japanese Robotics in Global Manufacturing
Precision and Quality
Japanese robots are synonymous with high precision and exceptional quality.
Their ability to perform repetitive tasks with consistent accuracy minimizes errors and ensures product reliability.
This level of quality control is crucial in industries where precision is paramount, such as automotive and electronics manufacturing.
Efficiency and Productivity
The integration of robotics in manufacturing processes significantly boosts efficiency and productivity.
Robots can operate continuously without fatigue, leading to higher production output and shorter lead times.
This increased productivity enables Japanese manufacturers to meet global demand effectively and maintain a competitive edge.
Innovation and Technological Leadership
Japan’s focus on innovation has established it as a technological leader in robotics.
Continuous research and development efforts contribute to the creation of advanced robotic solutions that set industry standards.
This leadership fosters a culture of innovation, driving further advancements and maintaining Japan’s position at the cutting edge of robotics technology.
Cost-Effectiveness
While the initial investment in robotics can be substantial, the long-term cost benefits are significant.
Robotic automation reduces labor costs, minimizes material waste, and enhances operational efficiency.
These cost savings make Japanese robotics an attractive option for manufacturers seeking to optimize their production costs and improve profitability.
Disadvantages and Challenges
High Initial Investment
One of the primary challenges in adopting robotics is the high upfront cost associated with purchasing and implementing robotic systems.
This investment can be a barrier for smaller manufacturers or those with limited capital resources.
Technical Complexity
Robotic systems are complex and require specialized knowledge for installation, operation, and maintenance.
The technical expertise needed to manage these systems can be a hurdle, particularly for companies without a strong technical workforce.
Job Displacement Concerns
The increasing use of robotics in manufacturing has raised concerns about job displacement.
As robots take over repetitive and manual tasks, there is a potential impact on the workforce, necessitating strategies for workforce retraining and transition.
Integration with Existing Systems
Integrating new robotic systems with existing manufacturing processes can be challenging.
Ensuring seamless compatibility and minimizing disruptions during the transition requires careful planning and execution.
Supplier Negotiation Techniques with Japanese Robotics Suppliers
Understanding Cultural Nuances
Successful negotiations with Japanese suppliers require a deep understanding of Japanese business culture.
Respect, patience, and building long-term relationships are essential components of effective negotiation strategies in Japan.
Emphasizing Quality and Reliability
Japanese suppliers prioritize quality and reliability in their products.
When negotiating, emphasizing the importance of these factors and aligning them with the supplier’s values can lead to more favorable outcomes.
Leveraging Technical Expertise
Demonstrating a solid understanding of the technical aspects of robotics can enhance credibility during negotiations.
This approach facilitates more meaningful discussions and fosters mutual respect between parties.
Negotiating Long-Term Partnerships
Japanese businesses often seek long-term partnerships rather than one-off transactions.
Focusing on building enduring relationships can lead to more successful negotiations and ongoing collaboration.
Flexibility and Adaptability
Being flexible and adaptable in negotiations allows for accommodating the supplier’s needs and finding mutually beneficial solutions.
This flexibility is crucial in overcoming potential challenges and reaching agreements that satisfy both parties.
Market Conditions and Trends in Japanese Robotics
Growing Demand for Automation
The global demand for automation continues to rise, driven by the need for increased efficiency and productivity.
Japanese robotics companies are well-positioned to capitalize on this trend, offering advanced solutions that cater to diverse industry needs.
Advancements in Artificial Intelligence
Integrating artificial intelligence with robotics is a major trend in the industry.
Japanese manufacturers are at the forefront of developing intelligent robots capable of learning and adapting to complex tasks.
These advancements enhance the functionality and applicability of robotics across various sectors.
Collaborations and Partnerships
Collaborations between Japanese robotics firms and international partners are increasing.
These partnerships foster the exchange of knowledge and technology, expanding the global reach of Japanese robotics solutions.
Focus on Sustainability
Sustainability is becoming a key consideration in robotics development.
Japanese companies are investing in eco-friendly robotic technologies that minimize environmental impact and promote sustainable manufacturing practices.
Customization and Flexibility
There is a growing demand for customized robotic solutions tailored to specific manufacturing needs.
Japanese manufacturers are responding by offering flexible and adaptable robotic systems that can be easily integrated into diverse production environments.
Best Practices in Procuring Japanese Robotics
Thorough Market Research
Conducting comprehensive market research is essential for understanding the available robotic solutions and identifying the best suppliers.
This research should include an analysis of the latest technologies, supplier reputations, and industry trends.
Clear Specification Definition
Defining clear and detailed specifications ensures that the robotic systems meet the specific needs of the manufacturing process.
Accurate specifications help in selecting the right suppliers and avoiding misunderstandings during implementation.
Building Strong Relationships
Establishing and maintaining strong relationships with Japanese suppliers fosters trust and collaboration.
Regular communication and mutual respect are key components of successful long-term partnerships.
Evaluating Supplier Capabilities
Assessing the capabilities of potential suppliers ensures they have the expertise and resources to deliver high-quality robotic solutions.
This evaluation should include reviewing the supplier’s track record, technical capabilities, and financial stability.
Focusing on Total Cost of Ownership
Considering the total cost of ownership, including maintenance, training, and potential upgrades, is crucial when procuring robotics.
This holistic approach ensures that all associated costs are accounted for, leading to more informed purchasing decisions.
Implementing Comprehensive Training Programs
Providing comprehensive training for staff ensures the effective operation and maintenance of robotic systems.
Training programs should cover both the technical aspects of the robots and best practices for integrating them into the manufacturing process.
Ensuring Compliance with Standards
Ensuring that the robotic systems comply with relevant industry standards and regulations is essential for safety and quality assurance.
This compliance minimizes the risk of legal issues and ensures that the robots meet the necessary performance criteria.
Impact of Japanese Robotics on Global Manufacturing
Japanese robotics has had a profound impact on global manufacturing, setting benchmarks for efficiency, quality, and innovation.
The integration of Japanese robotic systems has enabled manufacturers worldwide to enhance their production capabilities and remain competitive in a rapidly evolving market.
Japan’s leadership in robotics has also spurred technological advancements globally, fostering a culture of continuous improvement and innovation in manufacturing practices.
Future Prospects of Japanese Robotics in Manufacturing
The future of Japanese robotics in manufacturing looks promising, with ongoing advancements in technology and increasing global demand.
Emerging trends such as collaborative robots, enhanced AI capabilities, and sustainable robotics solutions are expected to drive further growth.
Japanese manufacturers are likely to continue their focus on innovation, developing advanced robotic systems that address the evolving needs of the global market.
This sustained growth will reinforce Japan’s position as a leader in robotics and contribute to the advancement of global manufacturing standards.
Conclusion
Japan’s pioneering role in robotics has revolutionized global manufacturing, introducing unprecedented levels of efficiency, quality, and innovation.
The country’s commitment to advancing robotics technology, coupled with strategic procurement and purchasing practices, has established Japan as a key player in the global manufacturing landscape.
While challenges such as high initial investment and technical complexity exist, the advantages of Japanese robotics, including precision, productivity, and cost-effectiveness, outweigh the drawbacks.
By adopting best practices in procurement and fostering strong supplier relationships, manufacturers can leverage Japanese robotics to achieve significant competitive advantages.
As technology continues to evolve, Japan’s leadership in robotics is set to further transform manufacturing processes, driving progress and excellence in the global market.
資料ダウンロード
QCD調達購買管理クラウド「newji」は、調達購買部門で必要なQCD管理全てを備えた、現場特化型兼クラウド型の今世紀最高の購買管理システムとなります。
ユーザー登録
調達購買業務の効率化だけでなく、システムを導入することで、コスト削減や製品・資材のステータス可視化のほか、属人化していた購買情報の共有化による内部不正防止や統制にも役立ちます。
NEWJI DX
製造業に特化したデジタルトランスフォーメーション(DX)の実現を目指す請負開発型のコンサルティングサービスです。AI、iPaaS、および先端の技術を駆使して、製造プロセスの効率化、業務効率化、チームワーク強化、コスト削減、品質向上を実現します。このサービスは、製造業の課題を深く理解し、それに対する最適なデジタルソリューションを提供することで、企業が持続的な成長とイノベーションを達成できるようサポートします。
オンライン講座
製造業、主に購買・調達部門にお勤めの方々に向けた情報を配信しております。
新任の方やベテランの方、管理職を対象とした幅広いコンテンツをご用意しております。
お問い合わせ
コストダウンが利益に直結する術だと理解していても、なかなか前に進めることができない状況。そんな時は、newjiのコストダウン自動化機能で大きく利益貢献しよう!
(Β版非公開)