- お役立ち記事
- Unraveling the Role of Thermal Cracking in Revolutionizing Japanese Manufacturing Innovation
Unraveling the Role of Thermal Cracking in Revolutionizing Japanese Manufacturing Innovation
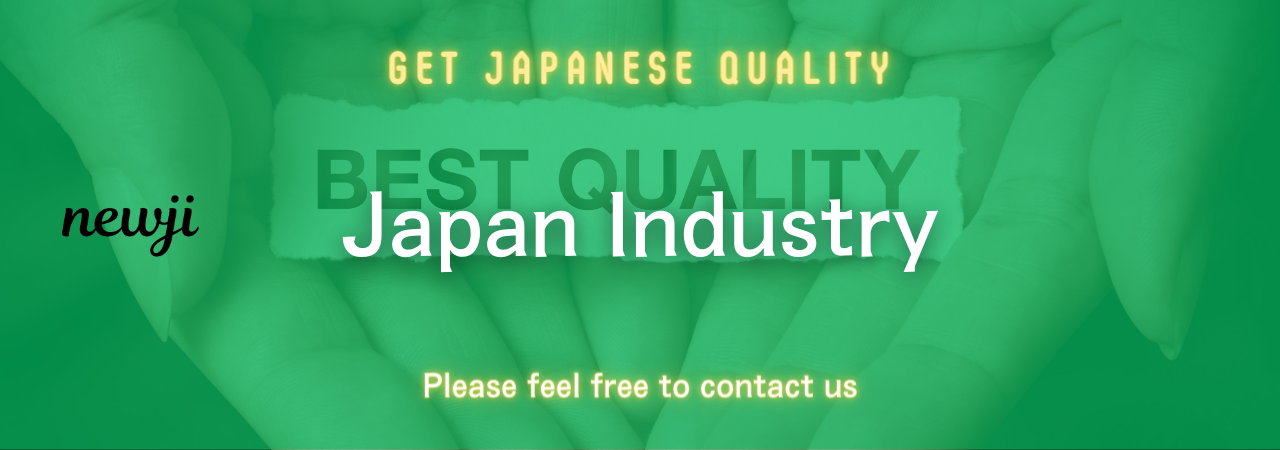
目次
Introduction to Thermal Cracking in Japanese Manufacturing
Thermal cracking plays a pivotal role in the evolution of Japanese manufacturing. As a fundamental process in chemical engineering, thermal cracking involves breaking down large hydrocarbon molecules into smaller, more valuable products through the application of heat. This process not only enhances the efficiency of production lines but also contributes significantly to innovation within the industry. Japanese manufacturers have harnessed thermal cracking to streamline their operations, reduce costs, and improve product quality, thereby maintaining their competitive edge in the global market.
The Significance of Thermal Cracking in Modern Manufacturing
Thermal cracking is essential for several reasons. It enables the conversion of heavy oils into lighter, more useful fractions such as gasoline, diesel, and other petrochemicals. This transformation is crucial for meeting the increasing demand for energy-efficient and environmentally friendly products. Additionally, thermal cracking supports the production of high-purity chemicals, which are vital for various industrial applications, including pharmaceuticals, plastics, and synthetic fibers.
Enhancing Production Efficiency
Japanese manufacturers leverage thermal cracking to maximize production efficiency. By optimizing the cracking process, they can achieve higher yields with lower energy consumption. Advanced control systems and automation technologies play a significant role in maintaining consistent process conditions, thus minimizing waste and reducing operational costs.
Improving Product Quality
The precision and control inherent in thermal cracking processes allow for the consistent production of high-quality products. Japanese companies invest heavily in research and development to refine cracking techniques, ensuring that their products meet stringent quality standards. This commitment to excellence not only satisfies customer expectations but also strengthens brand reputation.
Advantages of Implementing Thermal Cracking in Japanese Manufacturing
Thermal cracking offers numerous advantages that contribute to Japan’s manufacturing prowess. These benefits encompass economic, environmental, and technological aspects, providing a comprehensive foundation for sustainable industrial growth.
Economic Benefits
One of the primary economic advantages of thermal cracking is cost reduction. By efficiently converting feedstocks into high-value products, manufacturers can achieve better profit margins. Moreover, the scalability of thermal cracking processes allows companies to adjust production levels in response to market demand, enhancing financial stability.
Environmental Sustainability
Thermal cracking supports environmental sustainability by enabling the production of cleaner fuels and reducing the reliance on non-renewable resources. Japanese manufacturers are committed to minimizing their environmental footprint through advanced cracking technologies that lower greenhouse gas emissions and promote the use of recyclable materials.
Technological Innovation
The integration of thermal cracking with cutting-edge technologies such as artificial intelligence and machine learning facilitates continuous improvement and innovation. These technologies enable real-time monitoring and optimization of cracking processes, leading to enhanced performance and the development of new applications.
Challenges and Disadvantages of Thermal Cracking
Despite its numerous benefits, thermal cracking presents certain challenges that must be addressed to ensure its effective implementation.
High Energy Consumption
Thermal cracking is an energy-intensive process, requiring substantial heat input to break molecular bonds. This high energy demand can lead to increased operational costs and a larger carbon footprint if not managed properly.
Complexity of Process Control
Maintaining precise control over thermal cracking processes is complex and demanding. Variations in feedstock composition and process conditions can affect product quality and yield, necessitating sophisticated control systems and skilled personnel.
Environmental Concerns
While thermal cracking contributes to environmental sustainability, it also poses environmental challenges. The process can generate pollutants such as volatile organic compounds and particulate matter, which must be effectively managed to comply with environmental regulations.
Supplier Negotiation Techniques in Thermal Cracking
Effective supplier negotiations are crucial for Japanese manufacturers to secure the necessary materials and technologies for thermal cracking. Building strong relationships with suppliers can lead to favorable terms, reliable supply chains, and access to cutting-edge innovations.
Establishing Long-Term Partnerships
Japanese companies prioritize long-term partnerships with suppliers to ensure stability and consistency in their supply chains. These relationships are built on trust, mutual respect, and a shared commitment to quality and innovation.
Leveraging Local Expertise
Collaborating with local suppliers who understand the specific needs and challenges of the Japanese market can provide significant advantages. Local suppliers often offer customized solutions, faster response times, and greater flexibility in meeting production requirements.
Implementing Strategic Sourcing
Strategic sourcing involves identifying and selecting suppliers that align with the company’s long-term goals and values. This approach helps manufacturers optimize costs, improve quality, and enhance supply chain resilience.
Market Conditions Impacting Thermal Cracking in Japan
The success of thermal cracking in Japanese manufacturing is influenced by various market conditions, including global demand for petrochemicals, fluctuations in raw material prices, and regulatory frameworks.
Global Demand for Petrochemicals
The increasing global demand for petrochemicals drives the need for efficient thermal cracking processes. Japanese manufacturers must stay abreast of market trends and adjust their production strategies accordingly to meet international demand.
Raw Material Price Volatility
Fluctuations in raw material prices can impact the cost-effectiveness of thermal cracking operations. Manufacturers must employ effective procurement strategies and hedge against price volatility to maintain profitability.
Regulatory Environment
Strict environmental regulations in Japan and other countries influence the design and operation of thermal cracking facilities. Compliance with these regulations necessitates investments in pollution control technologies and sustainable practices.
Best Practices for Optimizing Thermal Cracking Processes
Implementing best practices is essential for maximizing the benefits of thermal cracking while mitigating its challenges. Japanese manufacturers employ a range of strategies to optimize their cracking processes.
Continuous Process Monitoring
Real-time monitoring of process parameters such as temperature, pressure, and reactor conditions allows for swift adjustments and maintains optimal operating conditions. Advanced sensors and automation systems are integral to this practice.
Investing in Research and Development
Ongoing research and development efforts focus on improving cracking technologies and discovering new applications. Collaboration with academic institutions and research organizations drives innovation and keeps Japanese manufacturers at the forefront of the industry.
Energy Efficiency Measures
Implementing energy-efficient technologies and practices reduces the energy consumption of thermal cracking processes. Strategies include heat recovery systems, energy-efficient reactors, and optimizing process conditions to minimize energy usage.
Employee Training and Development
Skilled personnel are essential for the effective operation of thermal cracking facilities. Japanese companies invest in comprehensive training programs to ensure that their workforce is proficient in the latest technologies and best practices.
Case Studies: Success Stories in Japanese Manufacturing
Examining successful implementations of thermal cracking in Japanese manufacturing provides valuable insights into effective strategies and practices.
Company A: Enhancing Efficiency through Automation
Company A, a leading petrochemical manufacturer in Japan, integrated advanced automation systems into their thermal cracking operations. This transition resulted in a 15% increase in production efficiency and a significant reduction in energy consumption. The use of real-time monitoring and automated control systems ensured consistent product quality and minimized operational downtime.
Company B: Sustainable Practices and Environmental Compliance
Company B adopted sustainable practices in their thermal cracking processes by implementing heat recovery systems and investing in pollution control technologies. These measures not only reduced their environmental impact but also lowered operational costs. Company B’s commitment to sustainability enhanced their reputation and compliance with stringent environmental regulations.
Company C: Innovation through Research Collaboration
Company C partnered with a leading Japanese university to develop a novel thermal cracking catalyst. This collaboration led to the creation of a more efficient catalyst that increased product yields by 10% while reducing energy consumption. The innovative catalyst provided Company C with a competitive advantage in the market and spurred further research and development initiatives.
Future Trends in Thermal Cracking and Japanese Manufacturing
The landscape of thermal cracking is continually evolving, driven by advancements in technology and shifting market dynamics. Japanese manufacturers must anticipate and adapt to these trends to maintain their leadership position.
Integration of Digital Technologies
The future of thermal cracking lies in the integration of digital technologies such as the Internet of Things (IoT), artificial intelligence (AI), and machine learning. These technologies enable predictive maintenance, process optimization, and enhanced decision-making, leading to more efficient and reliable operations.
Focus on Green Chemistry
There is a growing emphasis on green chemistry and sustainable practices in thermal cracking. Innovations aimed at reducing emissions, minimizing waste, and utilizing renewable feedstocks will shape the future of the industry. Japanese manufacturers are at the forefront of these developments, investing in sustainable technologies and practices.
Advanced Material Development
The development of advanced materials for reactors and catalysts is critical for improving the efficiency and durability of thermal cracking processes. Innovations in material science can lead to longer-lasting equipment, higher reaction rates, and reduced maintenance requirements.
Global Collaboration and Market Expansion
Japanese manufacturers are expanding their global footprint through strategic collaborations and market expansion efforts. By partnering with international companies and exploring new markets, they can leverage global expertise and diversify their operations to mitigate risks and capitalize on growth opportunities.
Conclusion
Thermal cracking remains a cornerstone of Japanese manufacturing innovation, driving efficiency, sustainability, and technological advancement. By addressing the challenges and leveraging the advantages of thermal cracking, Japanese manufacturers continue to set high standards in the global market. Effective supplier negotiations, adherence to best practices, and a focus on continuous improvement are essential for sustaining their leadership position. As the industry evolves, embracing future trends and innovations will ensure that thermal cracking continues to play a significant role in revolutionizing Japanese manufacturing.
資料ダウンロード
QCD調達購買管理クラウド「newji」は、調達購買部門で必要なQCD管理全てを備えた、現場特化型兼クラウド型の今世紀最高の購買管理システムとなります。
ユーザー登録
調達購買業務の効率化だけでなく、システムを導入することで、コスト削減や製品・資材のステータス可視化のほか、属人化していた購買情報の共有化による内部不正防止や統制にも役立ちます。
NEWJI DX
製造業に特化したデジタルトランスフォーメーション(DX)の実現を目指す請負開発型のコンサルティングサービスです。AI、iPaaS、および先端の技術を駆使して、製造プロセスの効率化、業務効率化、チームワーク強化、コスト削減、品質向上を実現します。このサービスは、製造業の課題を深く理解し、それに対する最適なデジタルソリューションを提供することで、企業が持続的な成長とイノベーションを達成できるようサポートします。
オンライン講座
製造業、主に購買・調達部門にお勤めの方々に向けた情報を配信しております。
新任の方やベテランの方、管理職を対象とした幅広いコンテンツをご用意しております。
お問い合わせ
コストダウンが利益に直結する術だと理解していても、なかなか前に進めることができない状況。そんな時は、newjiのコストダウン自動化機能で大きく利益貢献しよう!
(Β版非公開)