- お役立ち記事
- Injection Molding Basics: Defect Reduction and Quality Stabilization
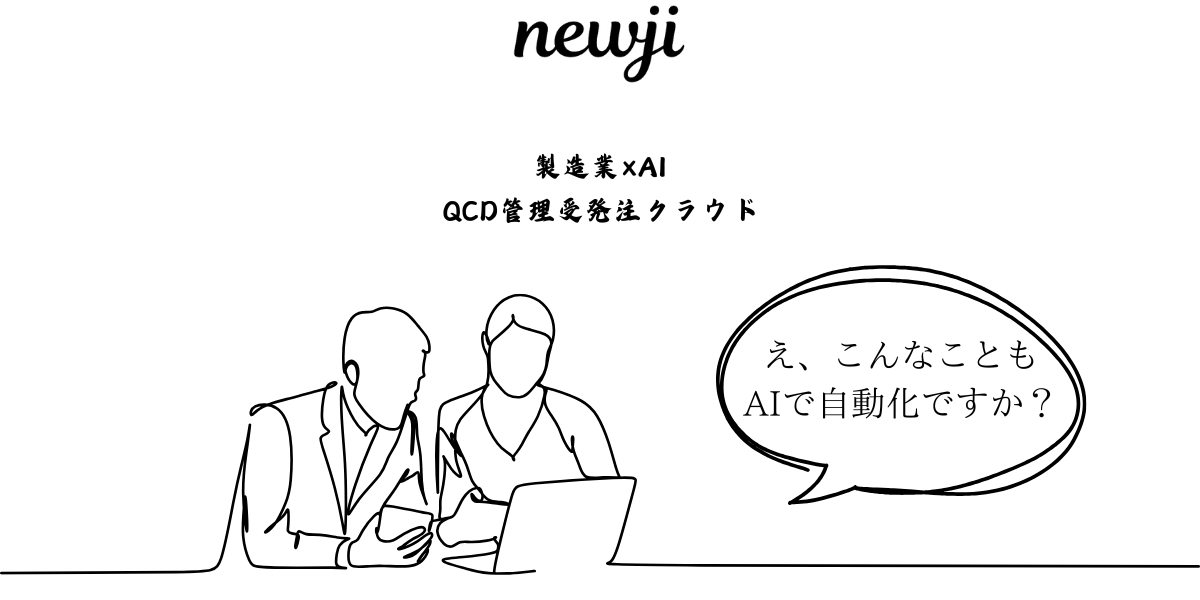
Injection Molding Basics: Defect Reduction and Quality Stabilization
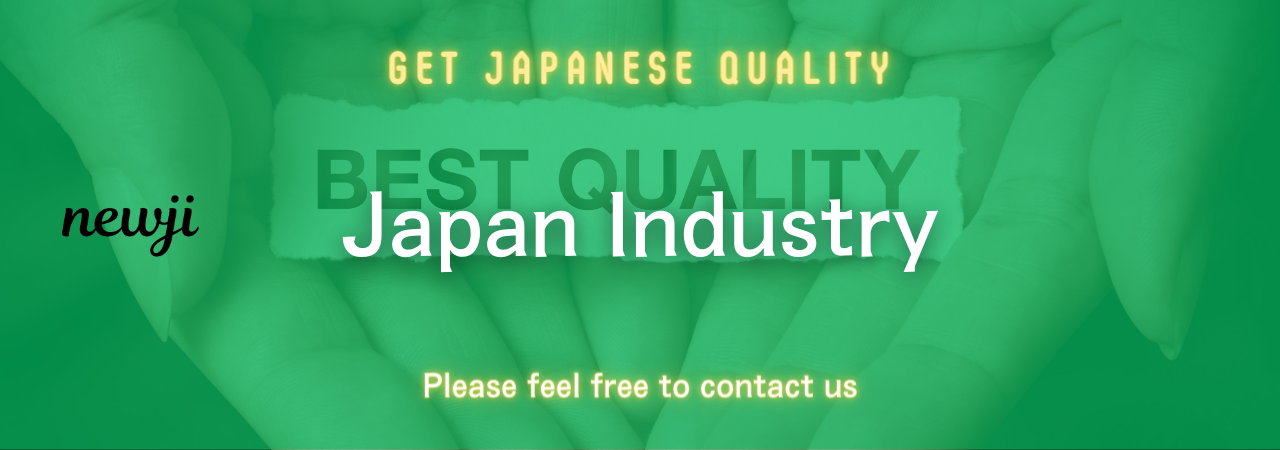
目次
Understanding Injection Molding
Injection molding is a popular manufacturing process used to create a wide variety of parts and products, from small plastic items to larger components in appliances and vehicles.
By injecting molten material into a mold and allowing it to cool and solidify, manufacturers can produce parts with high precision and consistency.
The Injection Molding Process
The process begins with feeding the raw plastic material, typically supplied in granule form, into a heated barrel.
Here, the plastic is melted and mixed before being injected into a mold under high pressure.
Once the material fills the mold cavity, it cools and solidifies, forming the final part.
The mold is then opened, and the part is ejected.
The cycle is repeated for high volume production runs, making this process efficient and cost-effective.
Common Defects in Injection Molding
Despite its efficiency, injection molding can encounter various defects, which impact the quality and functionality of the final product.
Some of the most common defects include:
Sink Marks
Sink marks are small, recessed areas that appear on the surface of the molded part due to uneven cooling and shrinkage of the material.
These marks can reduce the aesthetic appeal of a product and may also indicate inconsistencies in its structural integrity.
Warping
Warping occurs when different sections of a molded part cool at different rates, leading to distortion and deformation.
This defect can result in parts that do not fit together properly or perform as expected.
Flow Lines
Flow lines are streaks or patterns that appear on the surface of a molded part, caused by variations in the speed at which the molten plastic flows through the mold.
These lines can lead to a compromised appearance and may be indicative of underlying manufacturing issues.
Short Shots
A short shot occurs when the molten material does not completely fill the mold cavity, leading to an incomplete part.
This defect can result from several factors, including insufficient material or pressure, poor venting, or inadequate mold temperature.
Strategies for Reducing Defects
To ensure the production of high-quality parts, manufacturers must implement strategies to minimize defects and stabilize the molding process.
Here are some effective approaches to achieve this:
Optimize Mold Design
The design of the mold plays a critical role in preventing defects.
Ensuring uniform wall thickness, proper venting, and suitable gate locations can help in achieving consistent part quality.
Computer-aided design (CAD) software and simulation tools can be used to optimize mold designs before they are manufactured.
Control Process Parameters
Precise control of process parameters, such as temperature, pressure, and injection speed, can prevent defects from occurring.
By closely monitoring these parameters and making necessary adjustments, inconsistencies can be minimized, ensuring more stable and repeatable outcomes.
Material Selection and Conditioning
Choosing the right material for the product is crucial, as different materials have varying flow characteristics and cooling rates.
Proper material conditioning, such as drying plastic pellets to the correct moisture levels, can also reduce the likelihood of defects like warping and flow lines.
Regular Maintenance and Calibration
Regular maintenance of injection molding machines and molds can prevent issues that lead to defects.
This includes cleaning and lubricating equipment, checking for wear-and-tear, and calibrating settings to maintain accurate control over the process.
Implement Quality Assurance Practices
Adopting quality assurance practices, such as regular inspections and in-process testing, can help in identifying defects early in the production process.
Using statistical process control (SPC) techniques allows manufacturers to monitor and control variations, ensuring consistent product quality.
Stabilizing Quality in Injection Molding
Achieving quality stabilization in injection molding is critical for maintaining customer satisfaction and reducing costs.
Here are some practices that can help stabilize quality:
Standardize Work Procedures
Consistently following standardized work procedures ensures that best practices are applied throughout every stage of the molding process.
This consistency reduces variability and helps in achieving stabilized quality.
Employee Training and Development
Training employees on the latest injection molding technologies and techniques enables them to identify potential problems and apply corrective measures efficiently.
Skilled and knowledgeable operators are essential for maintaining high quality standards.
Invest in Advanced Technologies
Investing in advanced technologies, such as automated quality inspection systems and real-time monitoring, provides immediate feedback and helps in quickly identifying issues.
These systems improve the accuracy and reliability of defect detection and correction.
Continuous Improvement Initiatives
Adopting a culture of continuous improvement encourages ongoing evaluation and enhancement of manufacturing processes.
By using feedback loops and data analysis, manufacturers can implement changes that lead to better quality and efficiency over time.
Engage Suppliers and Partners
Collaborating with material suppliers and technology partners can provide valuable insights and support for quality improvement efforts.
Engagement with these stakeholders enables access to new materials and process advancements, fostering innovation in production practices.
In conclusion, injection molding is a powerful manufacturing process that, when executed effectively, can produce high-quality, defect-free products.
By understanding and addressing common defects, optimizing process parameters, and investing in quality assurance measures, manufacturers can achieve stable and reliable outcomes in injection molding.
Ongoing attention to process improvement and technological advancements will further enhance the quality and efficiency of this critical manufacturing technique.
資料ダウンロード
QCD調達購買管理クラウド「newji」は、調達購買部門で必要なQCD管理全てを備えた、現場特化型兼クラウド型の今世紀最高の購買管理システムとなります。
ユーザー登録
調達購買業務の効率化だけでなく、システムを導入することで、コスト削減や製品・資材のステータス可視化のほか、属人化していた購買情報の共有化による内部不正防止や統制にも役立ちます。
NEWJI DX
製造業に特化したデジタルトランスフォーメーション(DX)の実現を目指す請負開発型のコンサルティングサービスです。AI、iPaaS、および先端の技術を駆使して、製造プロセスの効率化、業務効率化、チームワーク強化、コスト削減、品質向上を実現します。このサービスは、製造業の課題を深く理解し、それに対する最適なデジタルソリューションを提供することで、企業が持続的な成長とイノベーションを達成できるようサポートします。
オンライン講座
製造業、主に購買・調達部門にお勤めの方々に向けた情報を配信しております。
新任の方やベテランの方、管理職を対象とした幅広いコンテンツをご用意しております。
お問い合わせ
コストダウンが利益に直結する術だと理解していても、なかなか前に進めることができない状況。そんな時は、newjiのコストダウン自動化機能で大きく利益貢献しよう!
(Β版非公開)