- お役立ち記事
- Stress Corrosion Cracking: Mechanisms, Prevention, and Life Prediction
Stress Corrosion Cracking: Mechanisms, Prevention, and Life Prediction
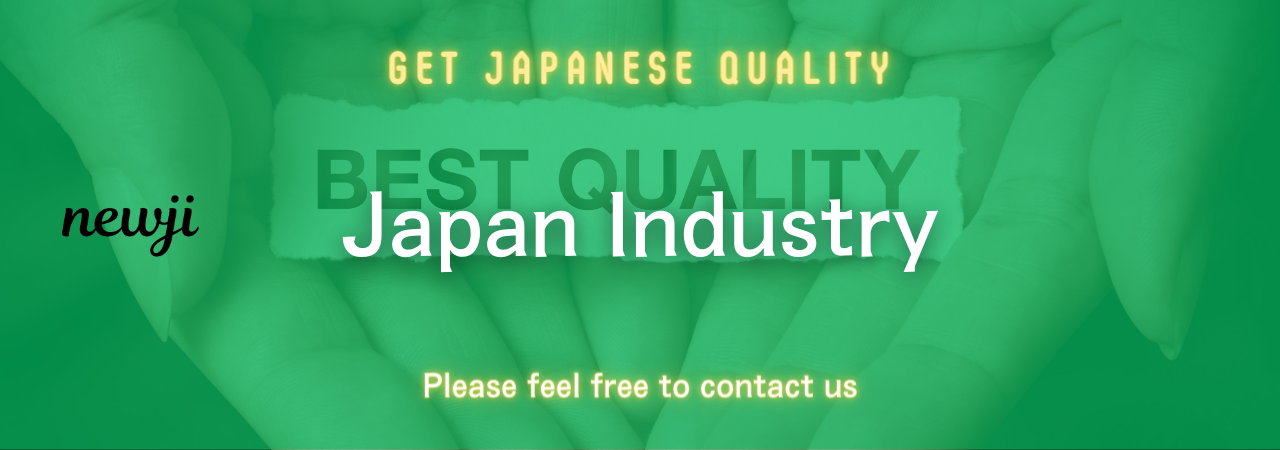
目次
Understanding Stress Corrosion Cracking
Stress corrosion cracking (SCC) is a phenomenon that affects materials, leading to unexpected failures in environments where corrosion occurs.
It is a complex process where mechanical stress and corrosive elements work together to create cracks in the material.
These cracks can develop over time, often without noticeable signs until a significant failure occurs.
SCC is particularly harmful because it combines the effects of tensile stress and a specific corrosive environment, often causing more damage than either factor alone.
Various industries, including chemical processing, nuclear energy, and oil and gas, are affected by stress corrosion cracking.
Understanding the mechanisms, prevention methods, and how to predict the lifespan of affected materials is crucial for safety and durability.
Mechanisms of Stress Corrosion Cracking
The Role of Stress
Stress is a critical factor in the SCC process.
Tensile stress can be internal, created during the manufacturing process, or applied externally during use.
It is important to note that even low levels of stress can contribute to SCC if the conditions are favorable.
The stress level required to induce SCC is lower than the material’s yield strength, making it more challenging to predict and manage.
Stress locally concentrates at microscopic sites, initiating and propagating cracks under the combined influence of corrosion.
Corrosive Environments
The environment plays an equally vital role in the development of SCC.
Certain corrosive agents, such as chlorides, sulfides, or hydroxides, are particularly notorious for promoting SCC in specific metals and alloys.
For example, stainless steel is susceptible to chloride-induced SCC, while mild steel may experience SCC in the presence of caustic environments.
Metals or alloys that are resistant to uniform corrosion might still be vulnerable to SCC if exposed to particular conditions.
Factors such as temperature, pressure, and the presence of particular ions or chemicals in the environment can accelerate SCC.
Material Susceptibility
Different materials and alloys exhibit varying degrees of susceptibility to SCC.
Some materials, like certain stainless steels, nickel-based alloys, and high-strength aluminum alloys, are more prone to this phenomenon due to their metallurgical composition or microstructure.
The grain boundaries, surface finish, and heat treatment of a material can also influence its susceptibility to SCC.
Materials with a coarse grain structure or those that have undergone specific processing techniques may have an increased risk.
Preventing Stress Corrosion Cracking
Material Selection
A primary strategy for preventing SCC is choosing materials that are less susceptible to its effects in the given environment.
Using alloys specifically designed to resist certain types of corrosion can significantly reduce the risk.
For instance, duplex stainless steels are often chosen in environments with a high risk of chloride-induced SCC.
Environmental Control
Controlling the environment is another effective way to prevent SCC.
Reducing or eliminating corrosive agents from the environment where the material is used can diminish the chances of SCC occurring.
For example, using inhibitors or coating systems to protect metals from environments rich in chlorides can be beneficial.
Stress Management
Stress management is crucial in minimizing the risk of SCC.
Designing components to minimize tensile stress concentrations and ensuring proper stress-relief techniques during manufacturing can help.
Regularly inspecting and maintaining equipment also ensures that any signs of wear or damage that could lead to stress are addressed promptly.
Predicting the Lifespan of Materials Affected by SCC
Understanding Crack Initiation and Growth
Predicting the lifespan of materials prone to SCC involves understanding crack initiation and growth rates.
Crack initiation might occur almost instantly in some materials, whereas others may experience a delayed onset.
Once a crack initiates, its growth rate depends on several factors, including stress intensity and corrosive environment severity.
Monitoring and Inspection
Regular monitoring and inspection are critical for predicting and managing SCC.
Methods such as ultrasonic testing, radiography, and acoustic emission testing can detect the early development of cracks.
Routine inspections help identify potential SCC sites before they become critical, allowing for preventative measures to be taken.
Simulation and Modeling
Advanced simulation and modeling techniques are utilized to predict SCC behavior.
These tools consider the material properties, environmental factors, and stress conditions to simulate SCC progression over time.
Using such models, engineers and scientists can estimate the remaining service life of materials and make informed decisions about maintenance and replacement schedules.
The Importance of Research and Innovation
Addressing the challenges of SCC requires continuous research and innovation.
Developing new materials with enhanced resistance to stress corrosion cracking and improving existing preventive techniques remains a focus area for engineers and scientists.
Collaborative efforts across industries help share knowledge and improve practices, ensuring the longevity and safety of structures and components.
Ongoing research aims to understand better the underlying mechanisms of SCC and discover new solutions for prevention and prediction.
By leveraging state-of-the-art technology and scientific discoveries, industries can significantly reduce the risks associated with stress corrosion cracking, leading to safer and more reliable operations.
Conclusion
Understanding the mechanisms, prevention strategies, and lifespan prediction of materials susceptible to stress corrosion cracking is vital across various industries.
By acknowledging the roles stress and environmental factors play in SCC, adopting preventative measures, and utilizing advanced tools for monitoring and prediction, industries can mitigate risks and ensure the structural integrity of their components.
As research and technology advance, the ability to combat SCC will continue to improve, leading to safer, longer-lasting materials.
資料ダウンロード
QCD調達購買管理クラウド「newji」は、調達購買部門で必要なQCD管理全てを備えた、現場特化型兼クラウド型の今世紀最高の購買管理システムとなります。
ユーザー登録
調達購買業務の効率化だけでなく、システムを導入することで、コスト削減や製品・資材のステータス可視化のほか、属人化していた購買情報の共有化による内部不正防止や統制にも役立ちます。
NEWJI DX
製造業に特化したデジタルトランスフォーメーション(DX)の実現を目指す請負開発型のコンサルティングサービスです。AI、iPaaS、および先端の技術を駆使して、製造プロセスの効率化、業務効率化、チームワーク強化、コスト削減、品質向上を実現します。このサービスは、製造業の課題を深く理解し、それに対する最適なデジタルソリューションを提供することで、企業が持続的な成長とイノベーションを達成できるようサポートします。
オンライン講座
製造業、主に購買・調達部門にお勤めの方々に向けた情報を配信しております。
新任の方やベテランの方、管理職を対象とした幅広いコンテンツをご用意しております。
お問い合わせ
コストダウンが利益に直結する術だと理解していても、なかなか前に進めることができない状況。そんな時は、newjiのコストダウン自動化機能で大きく利益貢献しよう!
(Β版非公開)