- お役立ち記事
- Fundamentals and high functionality of film formation by aerosol deposition (AD) method and its key points
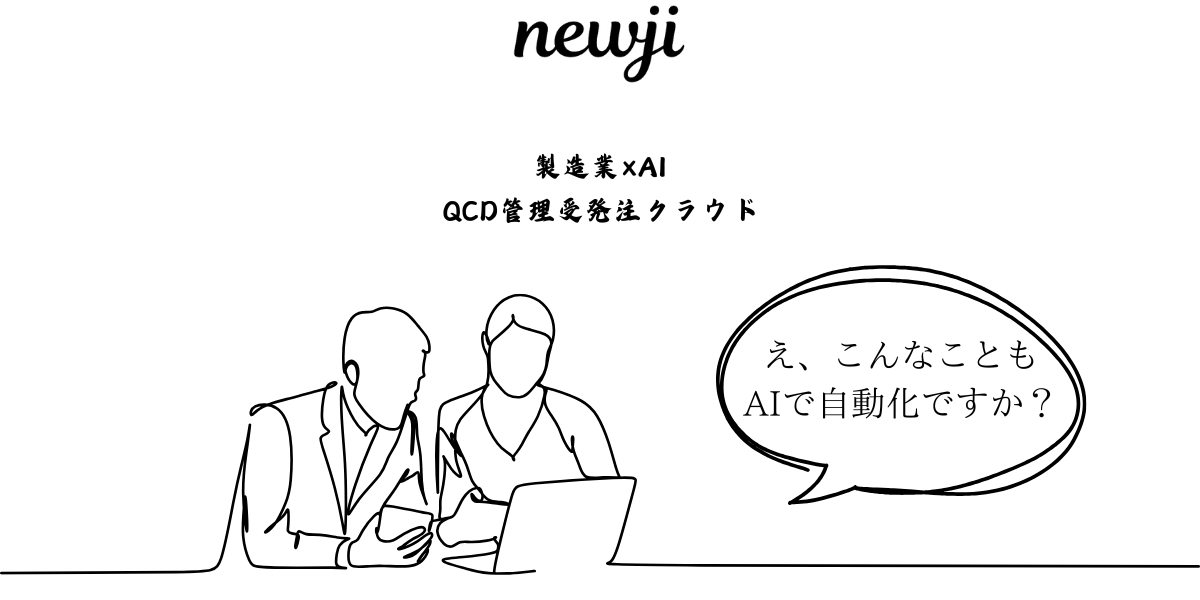
Fundamentals and high functionality of film formation by aerosol deposition (AD) method and its key points
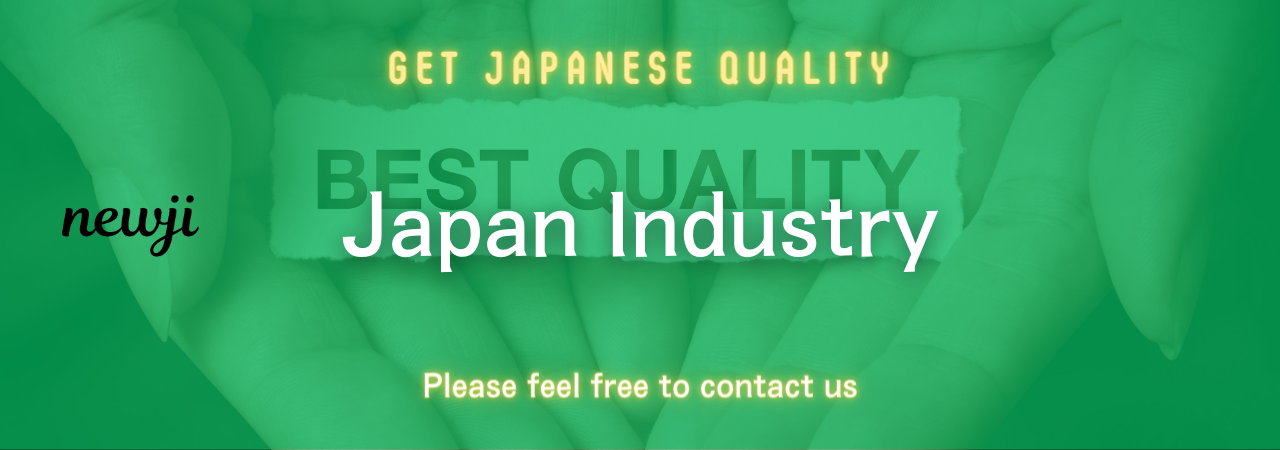
目次
Understanding the Basics of Aerosol Deposition (AD) Method
The aerosol deposition (AD) method is a groundbreaking technique in the field of film formation.
It involves the deposition of materials in the form of aerosols onto a substrate, creating a thin film that has numerous applications across various industries.
To truly appreciate the potential and functionality of the AD method, it is important to first understand its basic principles.
In AD, powders of the desired material are converted into aerosols by dispersing them in a carrier gas.
These aerosols travel through a vacuum chamber, eventually impinging on a substrate surface.
What makes this process unique is its ability to produce dense films at room temperature, avoiding the high temperatures required in traditional film formation techniques.
This not only saves energy but also enhances the range of materials and substrates that can be used, such as polymers and low melting point metals.
The High Functionality of AD Method
AD is distinguished by its high functionality, which opens up numerous possibilities in the field of thin film technology.
One major advantage of the AD method is its ability to produce films with excellent adhesion due to the kinetic energy involved in the aerosol particles’ impact on the substrate.
This feature ensures the durability and longevity of films, even in challenging environmental conditions.
Furthermore, the AD method is highly versatile, accommodating a wide range of materials such as ceramics, metals, and composites.
Such versatility is vital for industries like electronics, where different materials are needed for various components of devices.
For instance, AD can be used to create dielectric films for capacitors, conductive films for flexible electronics, or protective coatings for corrosion resistance.
Moreover, the AD process allows for precise control over film thickness, density, and composition, which is essential for advanced applications that require exact specifications.
This control not only enhances performance but also reduces the likelihood of defects, improving the overall quality of the product.
Key Points in Optimizing the AD Method
While the aerosol deposition method offers substantial benefits, there are key points that need attention to maximize its capabilities and efficiency.
Particle Size and Distribution
One of the critical factors in achieving optimal film properties through AD is the size and distribution of particles in the aerosol.
Smaller particles generally lead to better film density and smoothness due to their ability to pack more closely and uniformly on the substrate.
Controlling particle size can enhance the mechanical and electrical properties of the resulting film.
It is also important to maintain a uniform distribution of particles in the aerosol to avoid issues like agglomeration, which can result in uneven film surfaces or inconsistent thickness.
Choice of Carrier Gas
The selection of an appropriate carrier gas is another crucial aspect.
The carrier gas not only helps transport aerosolized particles to the substrate but also influences the deposition rate and particle energy.
Gases such as helium or argon are commonly used due to their inertness, which prevents unwanted chemical reactions during deposition.
The choice of carrier gas can be tailored to adjust the deposition speed and film characteristics, enhancing process control.
Substrate Preparation and Position
For optimal film quality, substrate preparation is vital.
Any impurities or irregularities on the substrate surface can lead to adhesion issues or defects in the film.
Proper cleaning and surface treatment ensure a clean, smooth base for aerosol deposition.
Additionally, the position and orientation of the substrate during deposition can impact film uniformity, making it a key consideration for technicians.
Applications and Future Potential of the AD Method
The applications of the AD method are extensive and continually expanding as technologies advance.
Electronics and Energy
In the electronics industry, AD is used for fabricating components like capacitors, batteries, and sensors, where thin and precise films are crucial.
The ability to deposit films at room temperature helps in working with heat-sensitive materials, broadening the possibilities for product innovation and integration.
Biomedical Devices
Biomedical applications also benefit from the AD technique through its ability to create biocompatible and antimicrobial coatings.
These coatings are essential for medical devices, prosthetics, and implants to reduce infection risks and improve device longevity.
Aerospace and Defense
In aerospace and defense, the AD method is employed to produce coatings that offer thermal protection and structural reinforcement.
These coatings provide resistance against extreme temperatures and mechanical stresses, which are common in these demanding environments.
Future Outlook
The future potential of the aerosol deposition method is immense.
With ongoing research and development, further improvements in cost-efficiency, material diversity, and film performance are anticipated.
These advancements will likely lead to broader adoption across industries and the emergence of new applications, paving the way for more sustainable and innovative products.
In summary, understanding and implementing the fundamentals and advanced functionalities of the aerosol deposition method can significantly enhance film formation processes.
By focusing on key optimization points such as particle size, carrier gas selection, and substrate preparation, industries can fully leverage the advantages of this versatile and efficient deposition technique for a wide array of applications.
資料ダウンロード
QCD調達購買管理クラウド「newji」は、調達購買部門で必要なQCD管理全てを備えた、現場特化型兼クラウド型の今世紀最高の購買管理システムとなります。
ユーザー登録
調達購買業務の効率化だけでなく、システムを導入することで、コスト削減や製品・資材のステータス可視化のほか、属人化していた購買情報の共有化による内部不正防止や統制にも役立ちます。
NEWJI DX
製造業に特化したデジタルトランスフォーメーション(DX)の実現を目指す請負開発型のコンサルティングサービスです。AI、iPaaS、および先端の技術を駆使して、製造プロセスの効率化、業務効率化、チームワーク強化、コスト削減、品質向上を実現します。このサービスは、製造業の課題を深く理解し、それに対する最適なデジタルソリューションを提供することで、企業が持続的な成長とイノベーションを達成できるようサポートします。
オンライン講座
製造業、主に購買・調達部門にお勤めの方々に向けた情報を配信しております。
新任の方やベテランの方、管理職を対象とした幅広いコンテンツをご用意しております。
お問い合わせ
コストダウンが利益に直結する術だと理解していても、なかなか前に進めることができない状況。そんな時は、newjiのコストダウン自動化機能で大きく利益貢献しよう!
(Β版非公開)