- お役立ち記事
- Design FMEA Basics and Application for Troubleshooting Prevention
Design FMEA Basics and Application for Troubleshooting Prevention
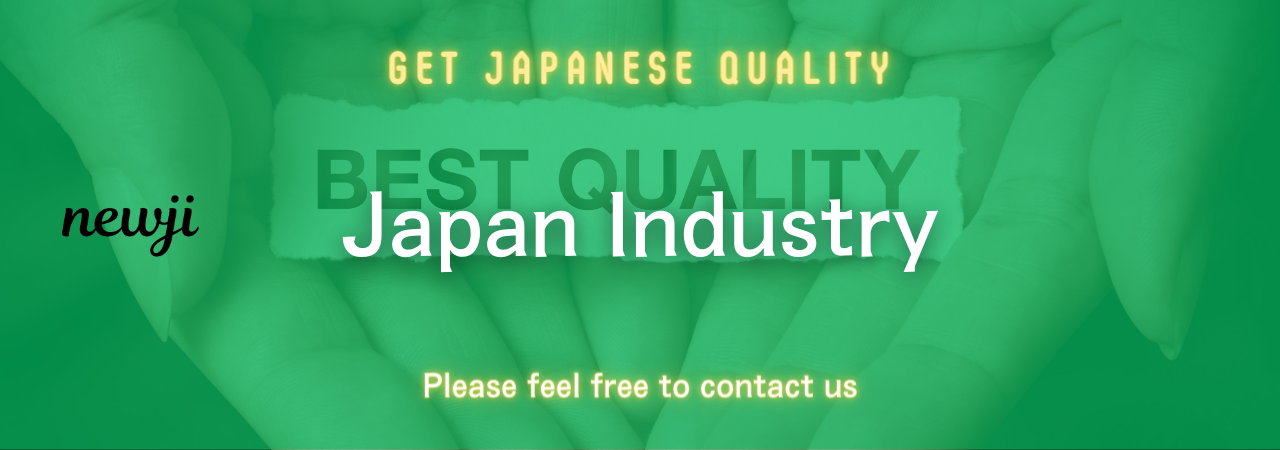
目次
What is Design FMEA?
Design Failure Mode and Effects Analysis, commonly known as Design FMEA, is a structured method used by engineers and designers to identify potential risks and failures in a product design before it goes into production.
It’s a proactive tool aimed at preventing design flaws and ensuring reliability, safety, and effectiveness of products.
Design FMEA involves a team-based approach where cross-functional teams collaborate to analyze every aspect of a design, identifying where things might go wrong.
The goal is to refine the design by anticipating problems and implementing preventive measures before any issues occur in real-world applications.
Why is Design FMEA Important?
Design FMEA is important because it helps ensure that products are built to the highest quality standards, minimizing the risk of failures and the costs associated with post-production fixes.
By identifying potential failure modes early, companies can address them at a lower cost compared to solving them during or after production.
Additionally, Design FMEA enhances customer satisfaction by ensuring that the end product meets expectations in terms of functionality, safety, and durability.
It is particularly essential in industries with stringent safety regulations, such as automotive, aerospace, and medical devices.
Steps in Conducting a Design FMEA
Step 1: Identify the Scope
The initial step in Design FMEA is defining the scope of the analysis.
This involves understanding the product, its intended function, and the customer requirements.
The team should have a clear idea of what to analyze and the boundaries of the analysis.
Step 2: Assemble a Cross-Functional Team
Next, form a team comprising individuals from various departments such as design, engineering, manufacturing, quality control, and customer service.
Diverse perspectives help in identifying potential design failures that a single department might overlook.
Step 3: List Potential Failure Modes
Once the team is in place, brainstorm potential failure modes for each component or functional assembly of the product.
A failure mode represents how a design might fail to perform its desired function.
This step is crucial as it sets the foundation for the rest of the analysis.
Step 4: Determine Effects and Causes
For each failure mode identified, analyze the potential effects it could have on the system and end-user.
Then, determine the possible causes that could lead to such failures.
Understanding the relationship between causes and effects is key to developing effective prevention strategies.
Step 5: Assess the Risk
Evaluate the risk associated with each failure mode using criteria like severity, occurrence, and detection.
A common practice is to use a Risk Priority Number (RPN) calculated by multiplying these factors.
The higher the RPN, the more critical it becomes to address the issue.
Step 6: Develop Action Plans
Based on the risk assessment, develop action plans to optimize the design and prevent potential failures.
Actions may include design modifications, enhanced testing, or additional safety measures.
Assign responsibilities and timelines to ensure follow-through.
Step 7: Review and Update the FMEA
This step involves reviewing the Design FMEA regularly, especially when changes are made to the design.
As the product development evolves, new failure modes might emerge, requiring periodic updates to the FMEA documentation.
Applying Design FMEA for Troubleshooting Prevention
Anticipating Potential Troubles
Design FMEA is a potent tool in troubleshooting prevention because it enables designers and engineers to anticipate possible issues before they manifest in production or field use.
By identifying potential design weaknesses early, teams can implement solutions that effectively reduce or eliminate the likelihood of troubles occurring.
Enhancing Design Robustness
The insights gained from a Design FMEA process lead to more robust product designs.
By systematically addressing weak points identified during the analysis, products become more resilient to failure modes that could have caused significant disruptions or safety hazards.
Reducing Time-to-Market
Though conducting a Design FMEA is a time-consuming process, it ultimately speeds up time-to-market by reducing the likelihood of design iterations and rework.
Preventive measures and a well-validated design process mean fewer surprises and delays during the production phase, leading to a more efficient product launch.
Challenges in Implementing Design FMEA
Resource Intensive
One of the main challenges in implementing Design FMEA is the requirement for significant resources, including time, expertise, and cross-department collaboration.
The process requires commitment from all stakeholders, which can be difficult to consistently achieve.
Complexity in Analysis
The analytical nature of Design FMEA can be complex, especially for products with intricate designs involving numerous components and systems.
Ensuring a thorough yet efficient analysis without overlooking subtle failure modes demands a high level of detail and precision.
Ensuring Proper Documentation
Maintaining accurate documentation throughout the Design FMEA process is critical for future reference and audits.
Without proper documentation, valuable findings and recommended actions can be lost, rendering the entire process ineffectual.
Conclusion
Design FMEA is an invaluable tool for predicting and preventing design-related failures.
By adopting a systematic approach to risk management during the design phase, companies can enhance product quality, ensure safety, and reduce costs associated with post-production failures.
While implementing Design FMEA comes with its own set of challenges, the long-term benefits in terms of reliability and market success make it a worthwhile investment for forward-thinking organizations.
資料ダウンロード
QCD調達購買管理クラウド「newji」は、調達購買部門で必要なQCD管理全てを備えた、現場特化型兼クラウド型の今世紀最高の購買管理システムとなります。
ユーザー登録
調達購買業務の効率化だけでなく、システムを導入することで、コスト削減や製品・資材のステータス可視化のほか、属人化していた購買情報の共有化による内部不正防止や統制にも役立ちます。
NEWJI DX
製造業に特化したデジタルトランスフォーメーション(DX)の実現を目指す請負開発型のコンサルティングサービスです。AI、iPaaS、および先端の技術を駆使して、製造プロセスの効率化、業務効率化、チームワーク強化、コスト削減、品質向上を実現します。このサービスは、製造業の課題を深く理解し、それに対する最適なデジタルソリューションを提供することで、企業が持続的な成長とイノベーションを達成できるようサポートします。
オンライン講座
製造業、主に購買・調達部門にお勤めの方々に向けた情報を配信しております。
新任の方やベテランの方、管理職を対象とした幅広いコンテンツをご用意しております。
お問い合わせ
コストダウンが利益に直結する術だと理解していても、なかなか前に進めることができない状況。そんな時は、newjiのコストダウン自動化機能で大きく利益貢献しよう!
(Β版非公開)