- お役立ち記事
- Grinding technology guidelines to improve machining accuracy
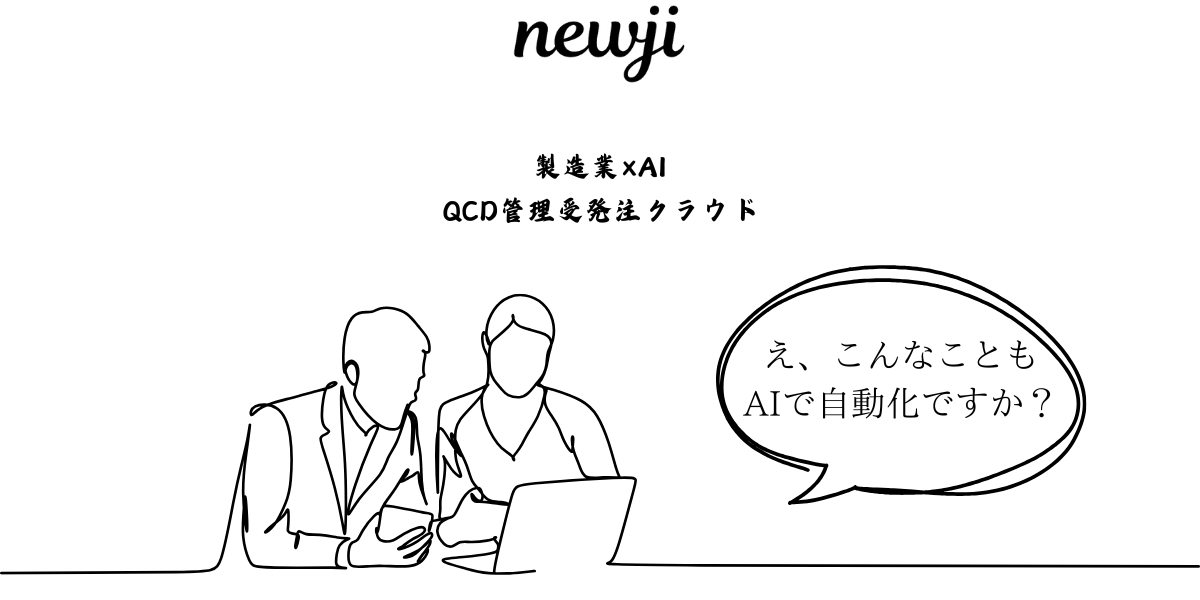
Grinding technology guidelines to improve machining accuracy
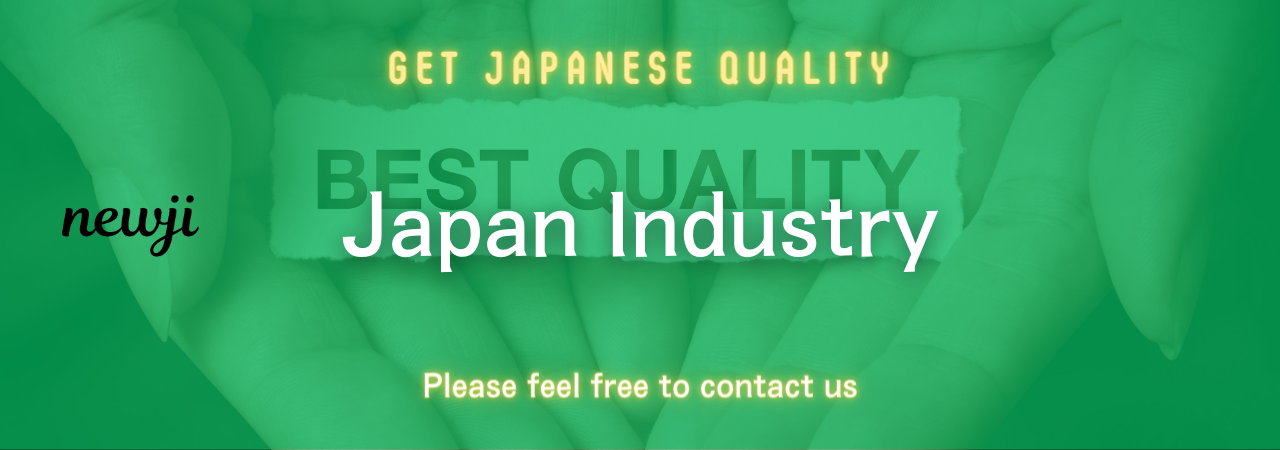
目次
Understanding Grinding Technology
Grinding technology refers to the processes and machinery involved in the act of grinding, an essential step in manufacturing that is used to achieve precision and high-quality finishes in materials, particularly metals.
Machining accuracy is critical in industries like automotive, aerospace, and manufacturing, where component tolerances are tight and system reliability is paramount.
By understanding and applying the right grinding technologies, it is possible to significantly enhance the accuracy and efficiency of machining processes.
The Importance of Machining Accuracy
Machining accuracy is vital because it ensures that parts fit together correctly and function as intended in a larger assembly.
Products with improper dimensions can lead to operational failures or safety hazards.
Thus, high-precision machining reduces waste, lowers costs, and improves product reliability.
By honing in on grinding technology as a key tool for precision, manufacturers can ensure that they meet rigorous quality standards and deliver consistent, reliable products.
Core Principles of Grinding Technology
Understanding Material Properties
The choice of grinding technology hinges largely on the properties of the material being machined.
Hardness, elasticity, and thermal conductivity can all impact how a material reacts to the grinding process.
For example, harder materials might require specific abrasives and machine settings to achieve an optimal finish.
Understanding these properties allows for better selection of tools and techniques, leading to greater machining accuracy.
Selection of Abrasives
Abrasives are materials used during the grinding process to shape and finish the workpiece.
Choosing the right abrasive is crucial; options typically include aluminum oxide, silicon carbide, diamond, and cubic boron nitride (CBN).
Each abrasive possesses unique characteristics suitable for specific material types and surface finishes.
Practitioners must select abrasives that will adequately remove material while maintaining structural integrity and desired surface quality.
Role of Coolants and Lubricants
Coolants and lubricants are critical components in grinding, influencing both the cooling and friction aspects of the grinding process.
They help reduce the amount of heat generated, thus preventing thermal damage or warping.
Without the proper use of cooling liquids, the material being ground might suffer adverse effects that compromise precision.
Manufacturers must carefully choose appropriate coolants and application methods to maintain part quality and extend the life of the grinding tools.
Advanced Grinding Technology Techniques
Computer Numerical Control (CNC) Grinding
Advanced CNC grinding machines offer unprecedented levels of precision.
Through computer automation, CNC grinding processes can achieve accuracy down to fractions of a millimeter.
This level of precision is indispensable in industries requiring high-caliber components.
With CNC machines, operators can program very specific parameters, delivering repeatable and consistent results that ensure all parts meet stringent tolerance requirements.
High-Speed Grinding
High-speed grinding is a technique that uses high rotational speeds and specialized equipment to achieve faster results without sacrificing accuracy.
Operating at higher speeds increases productivity and enables the machining of harder materials with ease.
To implement high-speed grinding effectively, knowledge of equipment capabilities and constraints is imperative, ensuring that the technique aligns with the desired finish and precision criteria.
Innovative Grinding Wheels
The development of innovative grinding wheels continues to push the boundaries of what is possible in machining accuracy.
Advances have been made in hybrid wheels that combine abrasives to use different characteristics synergistically, improving precision.
Additionally, wheel conditioning processes such as dressing and truing play critical roles in ensuring optimal wheel performance and longevity, maintaining the consistency essential to precise machining.
Measuring and Improving Machining Accuracy
Role of Metrology
To improve machining accuracy, meticulous measurement is essential throughout the grinding process.
Metrology, the science of measurement, involves using specialized tools and methodologies to verify that parts meet designated specifications.
Techniques like coordinate measuring machines (CMMs), laser scanning, and tactile gages provide precision measuring options to confirm parts are within acceptable limits.
Employing robust metrology practices ensures continuous monitoring and improvement of machining accuracy.
Feedback and Control Systems
Feedback and control systems are integral to improving grinding accuracy.
These systems monitor real-time data from the process and adjust parameters dynamically to ensure conformity to required specifications.
Machine learning algorithms are increasingly incorporated into feedback systems, offering ways to predict and compensate for variability in processes, thus enhancing accuracy even further.
Continuous Process Evaluation
Grinding technology is not a static discipline but one that requires continuous evaluation and evolution.
Regular analysis of grinding processes, including tools and machinery performance, can lead to step-change improvements in machining precision.
Teams can look at process data, pinpoint inefficiencies, and adjust methods, fostering an environment of constant improvement within the manufacturing process.
Future Trends in Grinding Technology
The landscape of grinding technology continues to evolve through innovations in materials, automation, and manufacturing digitization.
Emerging technologies such as smart sensors and the integration of the Internet of Things (IoT) in machinery are set to advance the precision and efficiency of grinding processes even further.
As manufacturers continue to adapt and adopt these technologies, they are likely to see significant improvements in machining accuracy and overall productivity.
In closing, understanding and leveraging advanced grinding technology is key to achieving enhanced machining accuracy.
As industries progress, staying informed about technological advances and implementing best practices ensures organizations remain competitive and capable of meeting the most demanding manufacturing standards.
資料ダウンロード
QCD調達購買管理クラウド「newji」は、調達購買部門で必要なQCD管理全てを備えた、現場特化型兼クラウド型の今世紀最高の購買管理システムとなります。
ユーザー登録
調達購買業務の効率化だけでなく、システムを導入することで、コスト削減や製品・資材のステータス可視化のほか、属人化していた購買情報の共有化による内部不正防止や統制にも役立ちます。
NEWJI DX
製造業に特化したデジタルトランスフォーメーション(DX)の実現を目指す請負開発型のコンサルティングサービスです。AI、iPaaS、および先端の技術を駆使して、製造プロセスの効率化、業務効率化、チームワーク強化、コスト削減、品質向上を実現します。このサービスは、製造業の課題を深く理解し、それに対する最適なデジタルソリューションを提供することで、企業が持続的な成長とイノベーションを達成できるようサポートします。
オンライン講座
製造業、主に購買・調達部門にお勤めの方々に向けた情報を配信しております。
新任の方やベテランの方、管理職を対象とした幅広いコンテンツをご用意しております。
お問い合わせ
コストダウンが利益に直結する術だと理解していても、なかなか前に進めることができない状況。そんな時は、newjiのコストダウン自動化機能で大きく利益貢献しよう!
(Β版非公開)