- お役立ち記事
- “Revolutionary Layout Design: The Secret to Japanese Manufacturing Excellence”
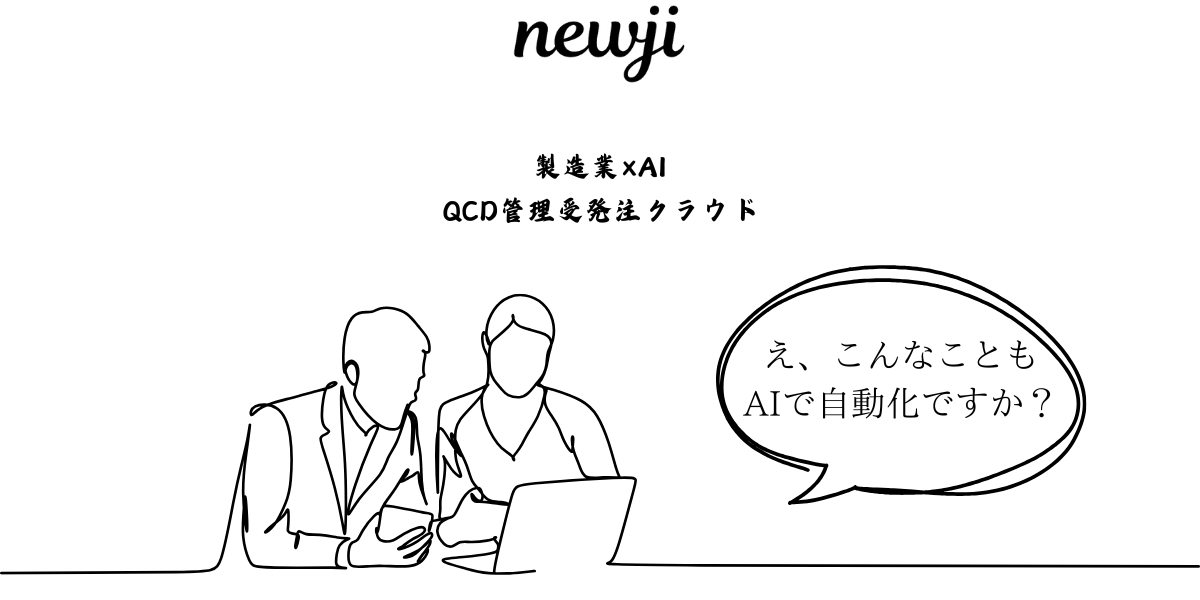
“Revolutionary Layout Design: The Secret to Japanese Manufacturing Excellence”
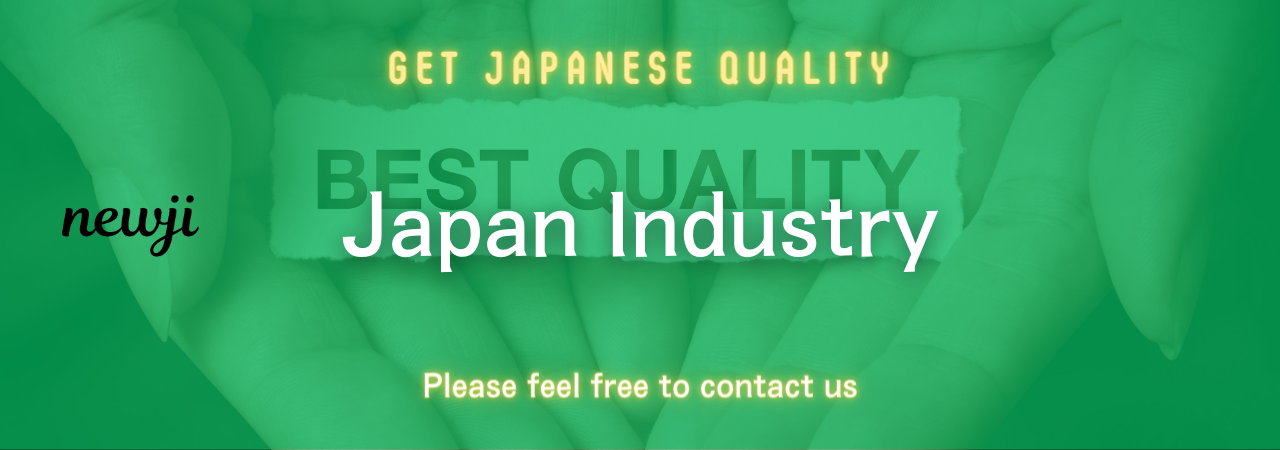
目次
The Importance of Layout Design in Manufacturing
Layout design is a critical component of manufacturing excellence. It determines the efficiency of production processes, the flow of materials, and the overall productivity of a factory. A well-designed layout minimizes waste, reduces production time, and ensures that resources are utilized effectively. In the competitive landscape of global manufacturing, especially in Japan, layout design plays a pivotal role in maintaining high standards of quality and efficiency.
Key Principles of Japanese Layout Design
Japanese manufacturing excellence is often attributed to its unique approach to layout design. Several key principles underpin this approach, ensuring that production processes are optimized for maximum efficiency and quality.
Lean Manufacturing
Lean manufacturing is a core principle in Japanese layout design. It focuses on eliminating waste in all forms, whether it be time, materials, or labor. By streamlining processes and removing non-value-added activities, lean manufacturing ensures that production is both cost-effective and efficient.
Just-In-Time Production
Just-In-Time (JIT) production is another fundamental aspect of Japanese layout design. JIT emphasizes the production of goods only as they are needed, reducing inventory costs and minimizing waste. This approach requires precise coordination and a robust supply chain to ensure that materials arrive exactly when required.
Kaizen
Kaizen, or continuous improvement, is a philosophy that encourages ongoing incremental changes to improve processes. In the context of layout design, Kaizen involves regularly assessing and tweaking the layout to enhance efficiency and adapt to changing production needs.
Procurement and Purchasing in Japanese Manufacturing
Effective procurement and purchasing strategies are integral to the success of Japanese manufacturing layout design. These strategies ensure that the necessary materials and components are available when needed, contributing to the smooth operation of the production process.
Supplier Relationships
Japanese manufacturers prioritize building strong, long-term relationships with their suppliers. Trust and collaboration are central to these relationships, allowing for better communication, more reliable supply chains, and mutual benefits such as cost savings and quality improvements.
Negotiation Techniques
Negotiating with suppliers in the Japanese context involves a blend of respect, understanding, and strategic thinking. Japanese negotiators often focus on building consensus and finding mutually beneficial solutions. Techniques such as thorough preparation, clear communication, and maintaining a long-term perspective are commonly employed.
Quality Control
Quality control is a top priority in Japanese manufacturing. Procurement strategies are designed to ensure that suppliers meet stringent quality standards. This involves regular inspections, audits, and the implementation of quality management systems to maintain consistent product quality.
Advantages of Japanese Layout Design
Japanese layout design offers numerous advantages that contribute to the overall excellence of its manufacturing sector.
Efficiency
The streamlined processes inherent in Japanese layout design lead to high levels of efficiency. By minimizing waste and optimizing resource utilization, manufacturers can produce more with less, enhancing productivity and profitability.
Flexibility
Japanese layout designs are highly adaptable, allowing manufacturers to respond quickly to changes in demand or market conditions. This flexibility is achieved through modular layouts, which can be easily reconfigured to accommodate different production needs.
Quality Improvement
A focus on continuous improvement and rigorous quality control ensures that Japanese manufacturers maintain high product standards. This commitment to quality not only satisfies customers but also reduces costs associated with defects and rework.
Disadvantages and Challenges
While Japanese layout design offers many benefits, it also comes with its own set of challenges and disadvantages.
High Implementation Costs
Implementing Japanese-style layout designs can be costly. The initial investment in technology, training, and process optimization may be substantial, posing a barrier for smaller manufacturers or those with limited resources.
Cultural Barriers
The success of Japanese layout design relies heavily on cultural elements such as teamwork, discipline, and continuous improvement. These cultural aspects may be difficult to replicate in different contexts, leading to challenges in implementation.
Supply Chain Vulnerabilities
Just-In-Time production, while efficient, can make supply chains more vulnerable to disruptions. Any delays or issues with suppliers can halt production, highlighting the need for robust risk management strategies.
Market Conditions and Trends
Understanding the current market conditions and emerging trends is essential for effectively implementing Japanese layout design principles.
Globalization Impact
Globalization has significantly influenced Japanese manufacturing. While it has opened up new markets and opportunities, it has also increased competition. Japanese manufacturers must continually innovate and optimize their layout designs to stay competitive on a global scale.
Technology Integration
Advancements in technology, such as automation and digitalization, are reshaping layout design. Integrating these technologies can enhance efficiency and flexibility, but it also requires significant investment and expertise.
Best Practices for Implementing Japanese Layout Design
Successfully implementing Japanese layout design principles involves several best practices that ensure optimal outcomes.
Understand Core Principles
A deep understanding of the core principles of Japanese layout design, such as Lean Manufacturing, Just-In-Time, and Kaizen, is essential. This foundation allows for the effective application of these concepts in various manufacturing contexts.
Invest in Training
Training employees in the principles and practices of Japanese layout design is crucial. Skilled and knowledgeable staff are better equipped to implement and sustain these practices, driving continuous improvement.
Foster Supplier Partnerships
Building strong partnerships with suppliers ensures a reliable and high-quality supply chain. Collaborative relationships facilitate better communication, joint problem-solving, and mutual benefits.
Continuous Improvement
Embracing a mindset of continuous improvement ensures that layout designs remain effective and adaptable. Regular assessments and incremental changes help maintain high levels of efficiency and quality.
Case Studies
Examining real-world examples of successful implementation of Japanese layout design principles can provide valuable insights into best practices and common challenges.
One notable case is Toyota’s manufacturing system, which exemplifies Lean Manufacturing and Just-In-Time principles. Toyota’s layout design focuses on minimizing waste, optimizing flow, and fostering a culture of continuous improvement. This approach has enabled Toyota to maintain high levels of quality and efficiency, making it a leader in the automotive industry.
Another example is Sony’s flexible manufacturing layout, which allows the company to quickly adapt to changing market demands. By designing production lines that can be easily reconfigured, Sony can efficiently produce a diverse range of products, enhancing its competitiveness in the electronics market.
Conclusion
Revolutionary layout design is a cornerstone of Japanese manufacturing excellence. By adhering to principles such as Lean Manufacturing, Just-In-Time production, and continuous improvement, Japanese manufacturers achieve high levels of efficiency, flexibility, and quality. Effective procurement and purchasing strategies, strong supplier relationships, and robust quality control further enhance these benefits. While challenges such as high implementation costs and cultural barriers exist, the advantages of Japanese layout design make it a valuable model for manufacturing companies worldwide. By adopting best practices and continuously striving for improvement, manufacturers can harness the secrets of Japanese excellence to achieve their own operational success.
資料ダウンロード
QCD調達購買管理クラウド「newji」は、調達購買部門で必要なQCD管理全てを備えた、現場特化型兼クラウド型の今世紀最高の購買管理システムとなります。
ユーザー登録
調達購買業務の効率化だけでなく、システムを導入することで、コスト削減や製品・資材のステータス可視化のほか、属人化していた購買情報の共有化による内部不正防止や統制にも役立ちます。
NEWJI DX
製造業に特化したデジタルトランスフォーメーション(DX)の実現を目指す請負開発型のコンサルティングサービスです。AI、iPaaS、および先端の技術を駆使して、製造プロセスの効率化、業務効率化、チームワーク強化、コスト削減、品質向上を実現します。このサービスは、製造業の課題を深く理解し、それに対する最適なデジタルソリューションを提供することで、企業が持続的な成長とイノベーションを達成できるようサポートします。
オンライン講座
製造業、主に購買・調達部門にお勤めの方々に向けた情報を配信しております。
新任の方やベテランの方、管理職を対象とした幅広いコンテンツをご用意しております。
お問い合わせ
コストダウンが利益に直結する術だと理解していても、なかなか前に進めることができない状況。そんな時は、newjiのコストダウン自動化機能で大きく利益貢献しよう!
(Β版非公開)