- お役立ち記事
- Evolving weight reduction technology in the automobile industry and its procurement issues
Evolving weight reduction technology in the automobile industry and its procurement issues
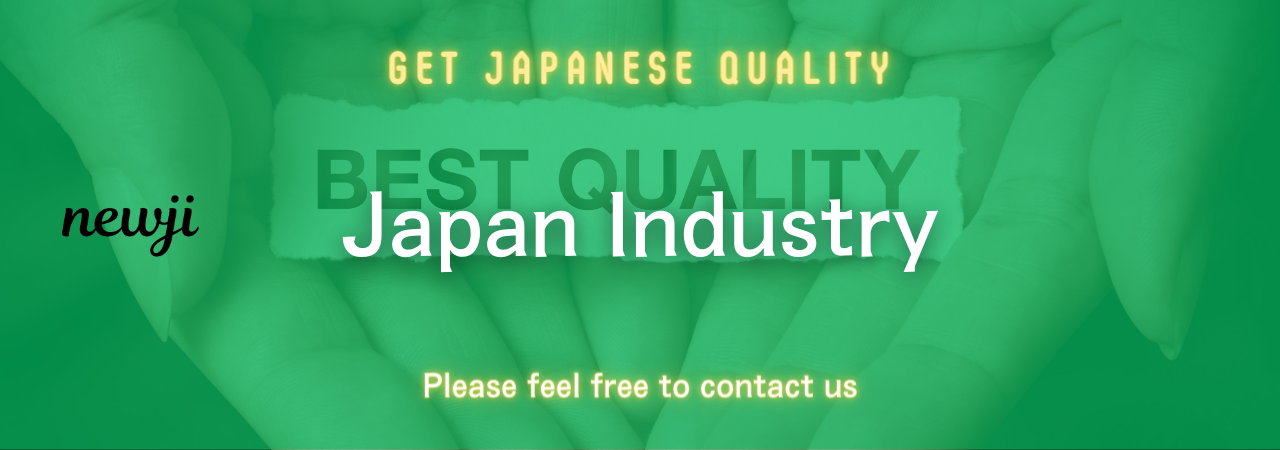
目次
Introduction to Weight Reduction Technology
The automobile industry is a constantly evolving field, driven by the need for innovation and efficiency.
Among the many challenges facing this industry, weight reduction technology has emerged as a significant focus area.
By reducing the weight of vehicles, automakers can improve fuel efficiency, reduce emissions, and enhance overall performance.
This technology is not only about shedding pounds but also about maintaining safety, durability, and cost-effectiveness.
Importance of Weight Reduction
Weight reduction is becoming increasingly crucial as regulations on emissions and fuel consumption tighten across the globe.
Lighter vehicles require less energy to operate, which directly translates to better fuel economy and lower greenhouse gas emissions.
Moreover, reducing weight contributes to the dynamic performance of a vehicle, improving acceleration, braking, and handling.
The focus on reducing weight is further driven by consumer demand for more sustainable and economical vehicles.
Modern consumers are becoming ever more conscious of their carbon footprints and are gravitating towards vehicles that offer environmentally friendly alternatives without sacrificing performance.
Technologies Driving Weight Reduction
In recent years, several innovative technologies have propelled the automobile industry’s weight reduction efforts.
One of the most significant advancements in this area is the use of lightweight materials.
Traditional steel components are increasingly being replaced by high-strength steel, aluminum, magnesium, and carbon fiber composites.
These materials provide the necessary strength and safety while considerably reducing the weight of the vehicle.
High-Strength Steel
High-strength steel offers a favorable balance between weight and durability.
It’s increasingly used in car frames and body panels, allowing for thinner structures without compromising safety.
This material aids manufacturers in meeting stringent safety standards while contributing to weight reduction.
Aluminum
Aluminum is another material that’s gaining traction.
It is about one-third the weight of steel, which makes it perfect for vehicles targeting weight savings.
While more expensive, advances in manufacturing have been bringing down costs, making aluminum an attractive option for automakers, particularly in the production of engine blocks, wheels, and some body panels.
Magnesium
Magnesium is the lightest structural metal available, which makes it valuable for automotive applications.
It is often used in interior components, gearbox housings, and steering columns.
Given its weight advantage, the use of magnesium helps to achieve significant weight savings across various vehicle parts.
Carbon Fiber Composites
Carbon fiber is renowned for its exceptional strength-to-weight ratio.
While traditionally used in high-performance and luxury cars, advances in production techniques are making carbon fiber composites more accessible for mass-market vehicles.
This material is particularly useful in components like hoods, roof panels, and drive shafts, where substantial weight savings can be realized.
Challenges in Procuring Lightweight Materials
Despite the advantages of lightweight materials, the procurement process presents several challenges.
Firstly, the cost of these advanced materials can be prohibitive.
High-strength steel, aluminum, magnesium, and carbon fiber are all generally more expensive than conventional materials.
This necessitates strategic trade-offs, balancing the benefit of weight reduction against increased material costs.
Supply Chain Complexity
The supply chain for lightweight materials is complex.
It often involves multiple suppliers from different parts of the world, which can lead to logistics challenges and increased lead times.
Automakers need to carefully manage these supply chains to maintain a steady flow of materials, ensure quality, and remain cost-effective.
Technological Limitations
The development of new manufacturing processes for handling lightweight materials is evolving but still presents technological challenges.
For instance, the welding and joining of aluminum or carbon fiber require specialized techniques and machinery, which can lead to increased production costs and complexity.
Material Properties
Each lightweight material comes with its own set of properties that need to be considered.
For example, while magnesium is light, it can be prone to corrosion and requires coatings to enhance durability.
Similarly, carbon fiber is difficult to repair once damaged.
Understanding and mitigating these weaknesses is essential for successful implementation.
Collaboration and Innovation
Collaborative innovation is driving progress in weight reduction technology.
Automotive manufacturers are increasingly partnering with materials scientists, suppliers, and research institutions to develop better materials and methods.
Such cooperation accelerates the advancement of technology, ensuring the industry can meet both regulatory and consumer demands.
Open platforms and shared learning are helping the industry overcome procurement challenges, as companies are more willing to share knowledge and resources in the pursuit of common goals.
This collaborative spirit is a silver lining, fostering an environment where challenges are addressed collectively.
Looking Forward
The ongoing evolution of weight reduction technology in the automobile industry is a testament to the sector’s commitment to sustainability and efficiency.
As technology advances, the cost and complexity of using lightweight materials are expected to reduce, broadening their application across more vehicle models.
The continued focus on research and development will yield new materials and processes that further optimize weight reduction while maintaining safety and performance standards.
Ultimately, the success of weight reduction technology lies in balancing performance, safety, sustainability, and cost.
While several hurdles remain, the future of automobile weight reduction holds promising prospects for creating greener, more efficient vehicles that meet the demands of the modern world.
資料ダウンロード
QCD調達購買管理クラウド「newji」は、調達購買部門で必要なQCD管理全てを備えた、現場特化型兼クラウド型の今世紀最高の購買管理システムとなります。
ユーザー登録
調達購買業務の効率化だけでなく、システムを導入することで、コスト削減や製品・資材のステータス可視化のほか、属人化していた購買情報の共有化による内部不正防止や統制にも役立ちます。
NEWJI DX
製造業に特化したデジタルトランスフォーメーション(DX)の実現を目指す請負開発型のコンサルティングサービスです。AI、iPaaS、および先端の技術を駆使して、製造プロセスの効率化、業務効率化、チームワーク強化、コスト削減、品質向上を実現します。このサービスは、製造業の課題を深く理解し、それに対する最適なデジタルソリューションを提供することで、企業が持続的な成長とイノベーションを達成できるようサポートします。
オンライン講座
製造業、主に購買・調達部門にお勤めの方々に向けた情報を配信しております。
新任の方やベテランの方、管理職を対象とした幅広いコンテンツをご用意しております。
お問い合わせ
コストダウンが利益に直結する術だと理解していても、なかなか前に進めることができない状況。そんな時は、newjiのコストダウン自動化機能で大きく利益貢献しよう!
(Β版非公開)