- お役立ち記事
- Mechanisms of careless mistakes and points for countermeasures and prevention of recurrence through poka-yoke
Mechanisms of careless mistakes and points for countermeasures and prevention of recurrence through poka-yoke
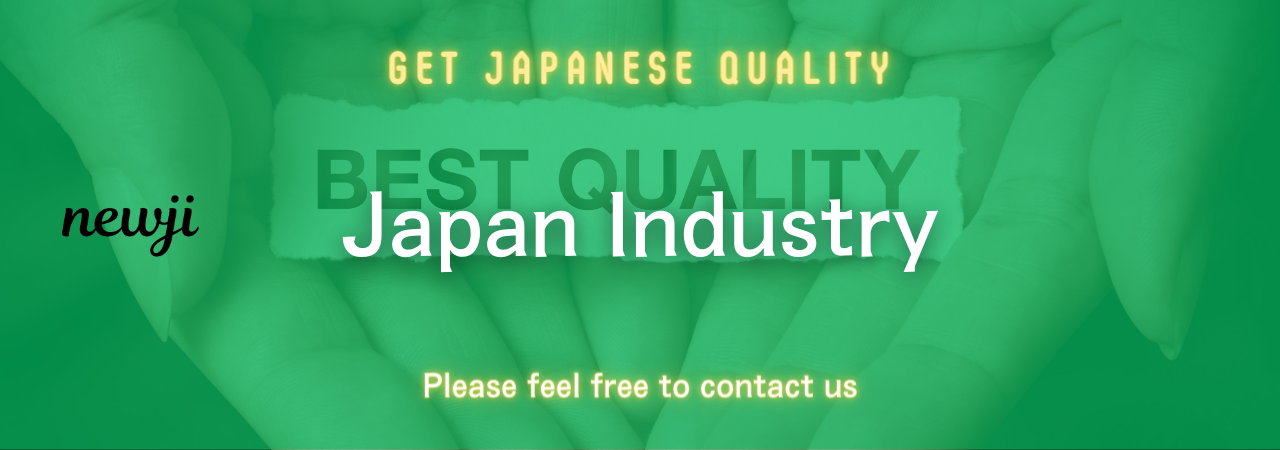
目次
Understanding Careless Mistakes
Careless mistakes are those pesky errors that appear even when we believe we’re giving our full attention to a task.
These errors can occur in various scenarios, from school exams to workplace projects.
The nature of these mistakes is often linked to human fallibility, where a momentary lapse in concentration can lead to errors.
While they may seem insignificant at first glance, the repercussions can accumulate over time, affecting performance and outcomes.
At the core, careless mistakes stem from our brain’s natural tendency to seek efficiency.
Our brains often try to conserve energy by operating on autopilot.
When we repeat tasks regularly, our minds sometimes skip steps or don’t pay full attention to the details, assuming the task is routine.
Consequently, this can lead to oversight and mistakes that slip through unnoticed.
The Role of Poka-Yoke
Poka-Yoke, a Japanese term meaning “mistake-proofing,” offers a systematic approach to prevent and rectify careless mistakes.
Originally developed by Shigeo Shingo for the Toyota Production System, poka-yoke aims to eliminate errors in manufacturing processes.
However, its principles can be applied across various domains to minimize human error.
The essence of poka-yoke is to design processes in such a way that human mistakes become unlikely or impossible.
This methodology involves creating mechanisms that either detect errors before they cause harm or prevent them altogether.
For instance, in a manufacturing setup, a poka-yoke mechanism might be a sensor that stops a machine if parts aren’t aligned correctly, preventing defective products.
Principles of Poka-Yoke
1. **Prevention**: Design processes so that errors cannot occur.
For example, creating a task checklist ensures that no step is forgotten.
2. **Detection**: Implement systems that identify errors as soon as they happen, allowing for immediate correction.
This could be as simple as a visual aid or indicator light to signal a problem.
3. **Feedback**: Provide immediate feedback to the person involved to correct the mistake right away.
Clear feedback mechanisms help in learning and avoiding future errors.
Implementing Poka-Yoke in Daily Life
While poka-yoke started in industrial settings, its principles are universally applicable.
Let’s explore ways to incorporate poka-yoke into everyday activities to minimize careless mistakes.
At Home
At home, we often face a multitude of routine tasks that can lead to mistakes out of familiarity.
Implementing simple poka-yoke strategies can greatly enhance productivity and reduce errors.
– **Organized Layouts**: Keep things in designated places.
For instance, use specific areas for commonly misplaced items like keys.
Labeling or using color codes can also aid in easy identification and organization.
– **Routine Checklist**: Prepare a checklist for daily tasks.
This prevents forgetting crucial activities like locking doors or turning off appliances.
In Education
Students can vastly benefit from the principles of poka-yoke to improve their learning efficiency and exam performance.
– **Practice Tests**: Simulate exam conditions with practice tests to identify common areas of error.
This practice helps in developing strategies to avoid similar mistakes in actual exams.
– **Study Patterns**: Implement feedback systems, like reviewing previous mistakes to learn and adapt study habits.
Encouraging self-assessment can help students become more aware of potential errors.
At Work
In the workplace, reducing careless mistakes can lead to improved efficiency and productivity.
– **Standard Operating Procedures (SOPs)**: Develop SOPs for recurring tasks.
This provides clear guidelines and reduces ambiguity, ensuring consistency and accuracy.
– **Feedback Loops**: Use feedback systems such as peer reviews or automated alerts to catch errors swiftly.
Continuous improvement and training can help employees refine their skills and be more mindful of their work.
Countermeasures Against Careless Mistakes
Implementing countermeasures helps in building resilience against recurring errors and enhances the overall quality of processes.
Let’s consider some effective counter-strategies.
Environment Design
Create an environment that minimizes distractions and provides clear paths for tasks.
Organized and visually intuitive workspaces naturally reduce the likelihood of mistakes.
Focus on Processes, Not People
Poka-yoke emphasizes that errors often arise from processes rather than individuals.
Instead of attributing mistakes to personal failures, focus on improving the processes.
Analyze the workflow to identify potential points of failure, and adjust as necessary.
Encourage a Culture of Open Communication
Foster an environment where team members feel comfortable discussing mistakes without the fear of stigma.
Open communication can lead to collaborative solutions and effective problem-solving.
This culture not only helps in rectifying immediate errors but also aids in preventing similar issues in the future.
Conclusion
Careless mistakes are an inevitable aspect of human activity, but with structured approaches like poka-yoke, they can be minimized.
By understanding the mechanisms behind these errors and implementing preventive measures, individuals and organizations can significantly improve their efficiency and accuracy.
Whether it’s in personal life, education, or work environments, mistake-proofing strategies offer a pathway to more reliable and error-free outcomes.
The key lies in continuous assessment and adaptation, ensuring that small slip-ups do not turn into significant problems.
資料ダウンロード
QCD調達購買管理クラウド「newji」は、調達購買部門で必要なQCD管理全てを備えた、現場特化型兼クラウド型の今世紀最高の購買管理システムとなります。
ユーザー登録
調達購買業務の効率化だけでなく、システムを導入することで、コスト削減や製品・資材のステータス可視化のほか、属人化していた購買情報の共有化による内部不正防止や統制にも役立ちます。
NEWJI DX
製造業に特化したデジタルトランスフォーメーション(DX)の実現を目指す請負開発型のコンサルティングサービスです。AI、iPaaS、および先端の技術を駆使して、製造プロセスの効率化、業務効率化、チームワーク強化、コスト削減、品質向上を実現します。このサービスは、製造業の課題を深く理解し、それに対する最適なデジタルソリューションを提供することで、企業が持続的な成長とイノベーションを達成できるようサポートします。
オンライン講座
製造業、主に購買・調達部門にお勤めの方々に向けた情報を配信しております。
新任の方やベテランの方、管理職を対象とした幅広いコンテンツをご用意しております。
お問い合わせ
コストダウンが利益に直結する術だと理解していても、なかなか前に進めることができない状況。そんな時は、newjiのコストダウン自動化機能で大きく利益貢献しよう!
(Β版非公開)