- お役立ち記事
- The secret to improving procurement efficiency brought about by standardization of machine tool parts
The secret to improving procurement efficiency brought about by standardization of machine tool parts
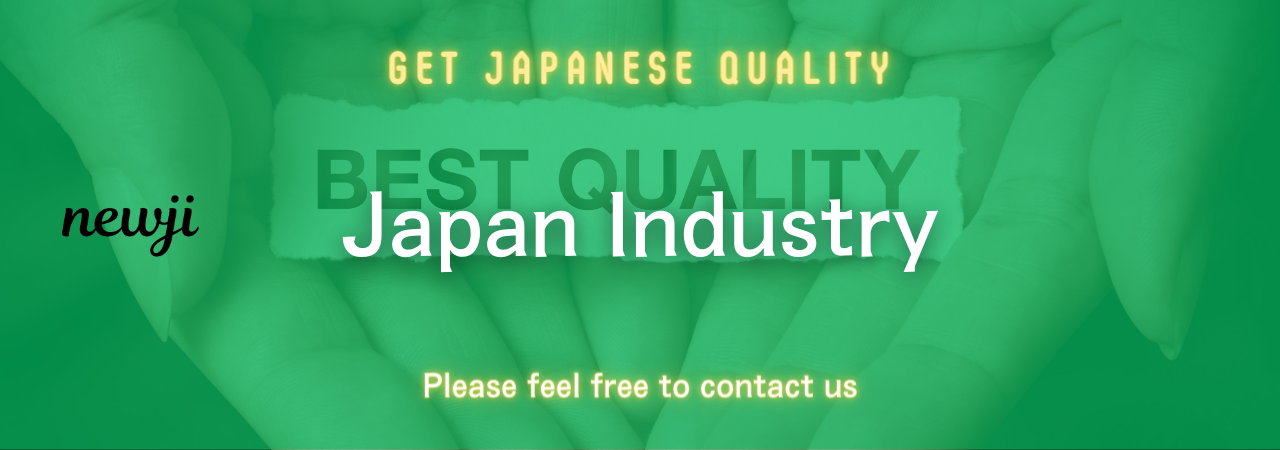
目次
Understanding the Importance of Standardization
Standardization in the manufacturing industry, especially in the production and procurement of machine tool parts, plays a critical role in improving efficiency.
When parts are standardized, it means that they adhere to common standards, making them compatible with a wide range of machines and systems.
This standardization helps in reducing complexities and streamlining processes.
The concept of standardization is like using a universal language in manufacturing.
Just as knowing a common language facilitates communication between people from different regions, standardization facilitates smoother and more efficient processes in manufacturing.
This includes a reduction in errors, easier maintenance, and simplified training for employees.
The Role of Procurement in Manufacturing
Procurement is a crucial component in manufacturing processes that involves obtaining the necessary parts and materials required for production.
For machine tool parts, procurement involves identifying suppliers, negotiating contracts, placing orders, and ensuring timely delivery.
Effective procurement processes can significantly impact a company’s production timelines and overall costs.
Yet, when machine tool parts are not standardized, procurement becomes a more complex task.
It often leads to challenges such as managing a large number of different parts, each requiring specific instructions for purchase and use.
In contrast, standardized parts simplify this process, as they can be used interchangeably, reducing the number and types of parts needed.
Benefits of Standardization in Procurement
Standardization in machine tool parts procurement offers numerous benefits to manufacturers.
One major advantage is the reduction in costs.
When parts are standardized, manufacturers can purchase in bulk, leading to discounts and reduced shipping expenses.
Moreover, standardization minimizes the need for maintaining large inventories, as standardized parts are readily available and easier to source.
This reduces storage costs and the risk of obsolescence.
Another significant benefit is improved efficiency.
With standardized parts, procurement teams spend less time searching for the right components and are less likely to face delays due to incompatible parts.
This efficiency not only speeds up the procurement process but also positively impacts the entire production timeline.
The Impact on Supply Chain Management
Standardization also has a profound impact on supply chain management.
By reducing the number of unique parts in the inventory, companies can streamline their supply chains, making them more robust and less susceptible to disruptions.
A standardized approach allows for better forecasting and inventory management.
Manufacturers can predict demand more accurately and adjust their production schedules seamlessly.
This adaptability is crucial in responding to market changes or unexpected demands.
Furthermore, standardization facilitates better relationships with suppliers.
As companies require fewer unique parts, they can establish long-term partnerships with a smaller selection of suppliers, fostering mutual trust and reliability.
Improving Quality and Consistency
Quality is a top priority in manufacturing, and standardization significantly contributes to maintaining high-quality standards.
When parts are standardized, it ensures consistency and reliability across all products.
This consistency results in fewer defects and higher customer satisfaction.
Furthermore, standardized parts undergo rigorous testing and quality checks before being released into the market.
This ensures that each part meets the required specifications, ultimately leading to better-performing machines and products.
In addition to quality control, standardization simplifies training for employees.
Workers are more easily trained on standardized parts and systems since they do not need to learn multiple variations.
This enhances workforce productivity and reduces the risk of human errors during assembly or maintenance.
Challenges in Implementing Standardization
While the benefits of standardization are clear, implementing it is not without challenges.
One significant hurdle is the initial cost and time required to transition to standardized parts.
This may involve reengineering existing designs, retraining employees, and reevaluating supply chains.
Resistance to change is another challenge.
Teams used to working with non-standardized systems may be reluctant to switch.
Therefore, clear communication and demonstrating the benefits of standardization are key in overcoming such resistance.
Additionally, not all parts and processes can be standardized due to specific requirements or technological limitations.
Manufacturers must carefully evaluate which parts and processes can be standardized without compromising quality or performance.
Real-Life Examples of Success
Numerous companies have successfully improved their procurement efficiency through standardization.
For instance, automotive manufacturers have long embraced standardized parts, allowing for interchangeable components across different models.
This practice has led to reduced production costs and faster assembly lines.
Similarly, in the aerospace industry, standardization helps in maintaining safety and reliability.
Interchangeable parts ensure efficient maintenance and repairs, reducing downtime and keeping aircraft operational.
These industries demonstrate that standardization, when applied effectively, can lead to substantial improvements in procurement efficiency, cost reduction, and product quality.
Steps Towards Achieving Standardization
To successfully implement standardization, companies should start by conducting a thorough assessment of their current processes and components.
Identifying which parts can be standardized and which need customization is a crucial step.
Engaging with cross-functional teams is essential to aligning strategies and ensuring a smooth transition.
Collaboration between designers, engineers, and procurement teams can foster innovative solutions and overcome potential obstacles.
Investing in technology and digital tools can also aid in standardization efforts.
Software solutions for inventory management and procurement can streamline operations and provide better insights into supply chain efficiencies.
Finally, ongoing evaluation and adaptation are key to maintaining standardization.
Markets and technologies evolve, so continuously assessing the effectiveness of standardized parts and making necessary adjustments is vital.
The Future of Standardization in Manufacturing
As technology continues to advance, the opportunities for standardization in manufacturing will expand.
With the rise of automation and the Internet of Things (IoT), standardized machine tool parts will be even more critical in creating efficient, interconnected systems.
Additionally, globalization creates a demand for standardized parts that can be easily sourced and used worldwide, further emphasizing the need for continued innovation in standardization practices.
By embracing standardization, manufacturers position themselves to remain competitive in a rapidly changing market, ensuring not just survival but growth and sustainability in their operations.
資料ダウンロード
QCD調達購買管理クラウド「newji」は、調達購買部門で必要なQCD管理全てを備えた、現場特化型兼クラウド型の今世紀最高の購買管理システムとなります。
ユーザー登録
調達購買業務の効率化だけでなく、システムを導入することで、コスト削減や製品・資材のステータス可視化のほか、属人化していた購買情報の共有化による内部不正防止や統制にも役立ちます。
NEWJI DX
製造業に特化したデジタルトランスフォーメーション(DX)の実現を目指す請負開発型のコンサルティングサービスです。AI、iPaaS、および先端の技術を駆使して、製造プロセスの効率化、業務効率化、チームワーク強化、コスト削減、品質向上を実現します。このサービスは、製造業の課題を深く理解し、それに対する最適なデジタルソリューションを提供することで、企業が持続的な成長とイノベーションを達成できるようサポートします。
オンライン講座
製造業、主に購買・調達部門にお勤めの方々に向けた情報を配信しております。
新任の方やベテランの方、管理職を対象とした幅広いコンテンツをご用意しております。
お問い合わせ
コストダウンが利益に直結する術だと理解していても、なかなか前に進めることができない状況。そんな時は、newjiのコストダウン自動化機能で大きく利益貢献しよう!
(Β版非公開)