- お役立ち記事
- Method for strengthening cooperation between equipment maintenance and procurement operations at production sites
Method for strengthening cooperation between equipment maintenance and procurement operations at production sites
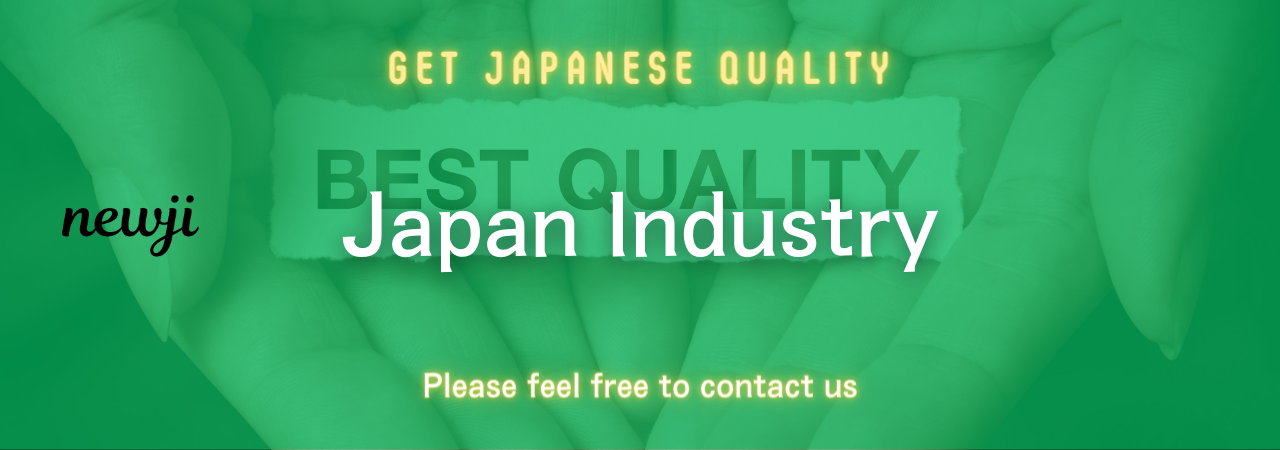
目次
Understanding the Importance of Cooperation
In the dynamic world of production, the smooth operation of equipment is crucial for maintaining efficiency and productivity.
With multiple processes happening simultaneously, any disruption can lead to significant delays and potential financial losses.
Thus, cooperation between equipment maintenance and procurement operations at production sites is essential.
The primary goal of equipment maintenance is to ensure that all machinery and tools are functioning optimally.
They are tasked with regular checks, troubleshooting issues, and performing necessary repairs.
On the other hand, the procurement team is responsible for acquiring the parts and materials needed to keep operations running.
Without effective collaboration, these two departments might face delays in communication, causing hold-ups that can affect the entire production line.
Communication: The Backbone of Effective Collaboration
For any cooperation to be fruitful, communication is key.
In a production environment, both maintenance and procurement teams must establish open lines of communication.
Regular meetings, either daily or weekly, can help both departments stay on the same page regarding the status of equipment and any upcoming needs for parts or tools.
Digital communication tools can facilitate this process.
Platforms like Slack, Microsoft Teams, or specialized industrial software can provide real-time updates and messaging, ensuring that information flows seamlessly between teams.
These tools can be used to create shared logs or databases where any team member can update the status of equipment or the procurement process.
Streamlining Processes Through Shared Goals
Setting shared goals can align the priorities of both equipment maintenance and procurement teams.
This could involve objectives like reducing downtime, improving the lifespan of machinery, or cutting costs by sourcing more effective materials.
When teams work towards common objectives, their efforts become synchronized, improving overall efficiency.
To further streamline their processes, the teams can adopt an integrated approach.
This might involve joint decision-making in selecting suppliers who can provide quality parts swiftly or investing in preventive maintenance to reduce the frequency of breakdowns.
Shared goals can also motivate both teams to innovate, finding ways to enhance their operations through technology or improved techniques.
Leveraging Technology for Better Coordination
In today’s digital age, technology can play a crucial role in strengthening cooperation between equipment maintenance and procurement operations.
Implementing software solutions that are accessible to both teams can enhance coordination and decision-making.
Manufacturing Execution Systems (MES) or Enterprise Resource Planning (ERP) systems are examples of such technology.
These systems offer functionalities that allow for tracking the condition of equipment, forecasting when parts might be needed, and managing inventory in real-time.
Moreover, predictive maintenance technologies, such as IoT sensors, can provide valuable data on equipment performance.
This data can be analyzed to predict when maintenance is due, allowing procurement to be proactive in acquiring necessary parts.
Such technology reduces unexpected downtimes and ensures smoother operation at production sites.
Training and Development for Both Teams
Training and development play a vital role in fostering better cooperation between equipment maintenance and procurement operations.
Regular training sessions can ensure that all team members understand the intricacies of both fields.
Cross-training, where procurement staff are familiarized with basic maintenance concepts and vice versa, can foster empathy and a deeper understanding.
This awareness can break down silos, encouraging individuals from both departments to collaborate more efficiently.
Leadership in both departments should also advocate for continuous professional development.
Encouraging team members to attend workshops, seminars, and courses specific to their fields can significantly broaden their knowledge and keep them updated with industry trends.
Building a Culture of Collaboration
At the heart of effective cooperation is a culture that values collaboration.
Leaders and managers should emphasize the importance of teamwork and recognize the contributions of both teams in achieving production objectives.
By cultivating a collaborative culture, barriers are minimized, and employees are more encouraged to share their expertise and insights.
Team-building activities can foster stronger relationships between the departments.
By engaging in activities outside the regular work environment, team members can connect on a personal level, improving interaction and teamwork back at the production site.
Feedback mechanisms can also be established, where both teams can provide constructive criticism and suggestions without fear of reprisal.
Such mechanisms can lead to continuous improvements and identify areas where cooperation can be further enhanced.
Evaluating and Adapting Cooperation Strategies
Continuous evaluation of collaboration strategies can help in identifying strengths and areas for improvement.
Regular assessments can involve measuring key performance indicators (KPIs) such as equipment downtime, procurement lead times, or cost-efficiency.
By analyzing these metrics, the teams can adapt their strategies to better meet overall production goals.
They might find opportunities for improvements, such as adjusting the maintenance schedule to align with procurement cycles or renegotiating supplier contracts for faster delivery.
Adaptability is essential as production environments are dynamic and subject to change.
Through regular assessments and flexible strategies, cooperation between equipment maintenance and procurement operations can evolve to meet new challenges and opportunities effectively.
- In conclusion, strengthening cooperation between equipment maintenance and procurement operations at production sites is integral to enhancing production efficiency.
- Through effective communication, shared goals, leveraging technology, training and development, fostering a collaborative culture, and continuous evaluation of strategies, both teams can work more cohesively.
- By doing so, production sites can reduce downtime, optimize resource use, and ultimately achieve greater productivity and profitability.
資料ダウンロード
QCD調達購買管理クラウド「newji」は、調達購買部門で必要なQCD管理全てを備えた、現場特化型兼クラウド型の今世紀最高の購買管理システムとなります。
ユーザー登録
調達購買業務の効率化だけでなく、システムを導入することで、コスト削減や製品・資材のステータス可視化のほか、属人化していた購買情報の共有化による内部不正防止や統制にも役立ちます。
NEWJI DX
製造業に特化したデジタルトランスフォーメーション(DX)の実現を目指す請負開発型のコンサルティングサービスです。AI、iPaaS、および先端の技術を駆使して、製造プロセスの効率化、業務効率化、チームワーク強化、コスト削減、品質向上を実現します。このサービスは、製造業の課題を深く理解し、それに対する最適なデジタルソリューションを提供することで、企業が持続的な成長とイノベーションを達成できるようサポートします。
オンライン講座
製造業、主に購買・調達部門にお勤めの方々に向けた情報を配信しております。
新任の方やベテランの方、管理職を対象とした幅広いコンテンツをご用意しております。
お問い合わせ
コストダウンが利益に直結する術だと理解していても、なかなか前に進めることができない状況。そんな時は、newjiのコストダウン自動化機能で大きく利益貢献しよう!
(Β版非公開)