- お役立ち記事
- LQI State Feedback Control Design and System Identification Basics
LQI State Feedback Control Design and System Identification Basics
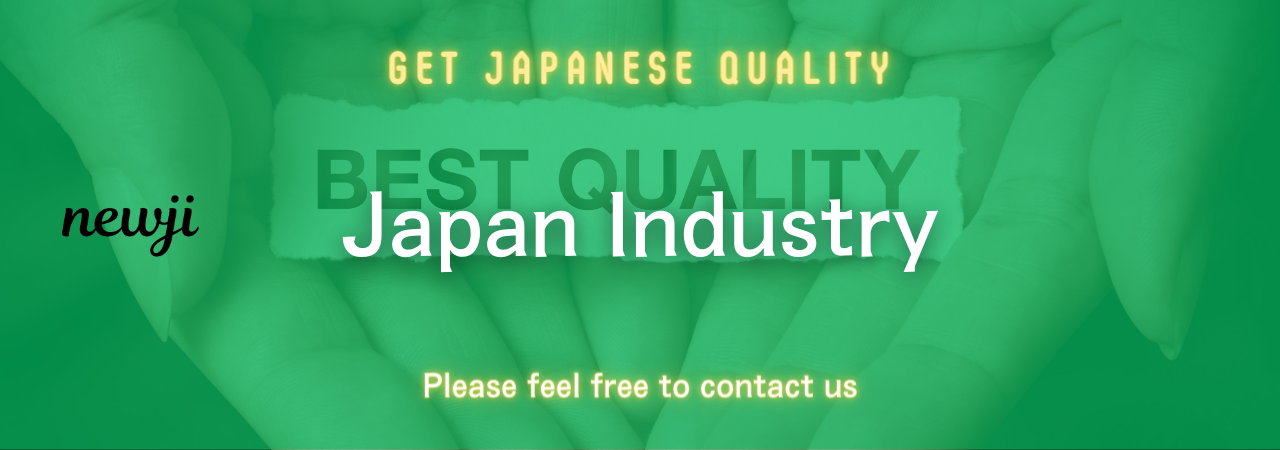
目次
Introduction to LQI State Feedback Control
Linear Quadratic Integral (LQI) state feedback control is a method used in control systems to ensure system stability and optimal performance.
It is widely used in various engineering fields such as aerospace, automotive, and robotics.
The LQI control strategy combines state feedback control with an integral action to address steady-state errors, providing an effective way to manage dynamic systems.
A feedback control system is designed to adjust control inputs based on the state of the system.
The LQI approach does this efficiently by minimizing a cost function that accounts for both state errors and control effort.
This makes LQI valuable for systems requiring precision and stability.
Understanding State Feedback Control
State feedback control is concerned with using the current state of a system to determine the control actions that should be executed.
In a typical system, the state is a set of variables that contains all the necessary information to describe the system’s dynamic behavior at any given time.
In state feedback control, you use a feedback gain matrix to multiply the current state vector.
This matrix is crucial as it influences how the system responds to changes or disturbances.
The central aim is to find an appropriate gain matrix that ensures the system performs optimally.
The advantage of state feedback control lies in its capacity to stabilize systems that may otherwise be unstable.
By continually adjusting the control inputs based on the system’s state, the desired output can be achieved with high accuracy.
Linear Quadratic Regulator (LQR) Framework
The foundation of LQI control starts with the Linear Quadratic Regulator (LQR).
LQR is a method in control theory that determines the optimal state feedback control law to minimize a given quadratic cost function.
The cost function typically penalizes deviations in state and control inputs from their desired levels.
Mathematically, the LQR problem involves designing a control input to minimize the cost function:
\[ J = \int (x^T Q x + u^T R u) dt \]
where \(x\) is the state vector, \(u\) is the control input, \(Q\) is a symmetric positive definite matrix that penalizes deviations in state, and \(R\) is a symmetric positive definite matrix that penalizes control effort.
Solving the LQR problem yields a gain matrix \(K\), which minimizes the cost function.
This gain matrix is used to compute the control law \(u = -Kx\).
Incorporating Integral Action in LQI Control
While the LQR method provides optimal performance within certain parameters, it does not inherently address steady-state errors.
Steady-state errors occur when the system output does not reach the desired value, even under stable conditions.
To manage this, LQI control integrates an integral action into the feedback mechanism.
This modification introduces an additional term to the cost function, penalizing accumulated errors over time.
The updated control law includes an integral feedback component, which helps eliminate steady-state error.
By incorporating integral action, LQI control adjusts system inputs continuously to counteract any persistent errors, improving long-term system accuracy.
Designing an LQI Control System
The design process for an LQI control system involves a series of steps:
1. **Model the Dynamic System**: Establish a mathematical model that accurately represents the system dynamics.
This could be through differential equations or state-space representations.
2. **Set Performance Criteria**: Determine what states need to be controlled and specify the desired system performance, including settling time, overshoot, and steady-state error.
3. **Formulate Cost Function**: Choose appropriate weighting matrices \(Q\) and \(R\) that reflect performance priorities.
The \(Q\) matrix weights state errors, while the \(R\) matrix decides the trade-off between performance and control effort.
4. **Compute the Gain Matrix**: Solve the associated algebraic Riccati equation to find the optimal gain matrix \(K\) for the system.
5. **Implement the Control Law**: Apply the computed gain matrix in the feedback loop to control the system, using the rule \(u = -Kx\).
6. **Evaluate and Tune**: Continuously monitor system performance, making adjustments to the weighting matrices or gain matrix as necessary.
Intro to System Identification Basics
System identification is the process of developing a mathematical model of a system based on measured data.
In control systems, accurate models are crucial for designing controllers like LQI.
There are several steps in system identification:
1. **Data Collection**: Gather input-output data from the system under various operating conditions.
2. **Model Structure Selection**: Choose the structure of the model (e.g., linear, nonlinear, time-invariant) that best fits the observed data.
3. **Parameter Estimation**: Use statistical methods to estimate the parameters of the model.
Optimization techniques are often employed to minimize the difference between model outputs and actual system data.
4. **Model Validation**: Test the model with different data sets to confirm its predictive capability and generalization.
System identification helps provide a reliable foundation for control system design, ensuring models align closely with real-world dynamics.
The Importance of LQI and System Identification
Combining LQI control with system identification offers a structured approach to managing complex systems.
By accurately modeling system dynamics and designing precise control actions, LQI ensures stability and optimal performance even in the presence of disturbances and uncertainties.
Whether in industrial automation, robotics, or any other domain requiring precision control, understanding LQI and system identification lays the groundwork for developing advanced control solutions.
Together, they provide the tools needed to manage and optimize complex dynamic systems effectively.
資料ダウンロード
QCD調達購買管理クラウド「newji」は、調達購買部門で必要なQCD管理全てを備えた、現場特化型兼クラウド型の今世紀最高の購買管理システムとなります。
ユーザー登録
調達購買業務の効率化だけでなく、システムを導入することで、コスト削減や製品・資材のステータス可視化のほか、属人化していた購買情報の共有化による内部不正防止や統制にも役立ちます。
NEWJI DX
製造業に特化したデジタルトランスフォーメーション(DX)の実現を目指す請負開発型のコンサルティングサービスです。AI、iPaaS、および先端の技術を駆使して、製造プロセスの効率化、業務効率化、チームワーク強化、コスト削減、品質向上を実現します。このサービスは、製造業の課題を深く理解し、それに対する最適なデジタルソリューションを提供することで、企業が持続的な成長とイノベーションを達成できるようサポートします。
オンライン講座
製造業、主に購買・調達部門にお勤めの方々に向けた情報を配信しております。
新任の方やベテランの方、管理職を対象とした幅広いコンテンツをご用意しております。
お問い合わせ
コストダウンが利益に直結する術だと理解していても、なかなか前に進めることができない状況。そんな時は、newjiのコストダウン自動化機能で大きく利益貢献しよう!
(Β版非公開)