- お役立ち記事
- Latest trends in component standardization in the electronics manufacturing industry
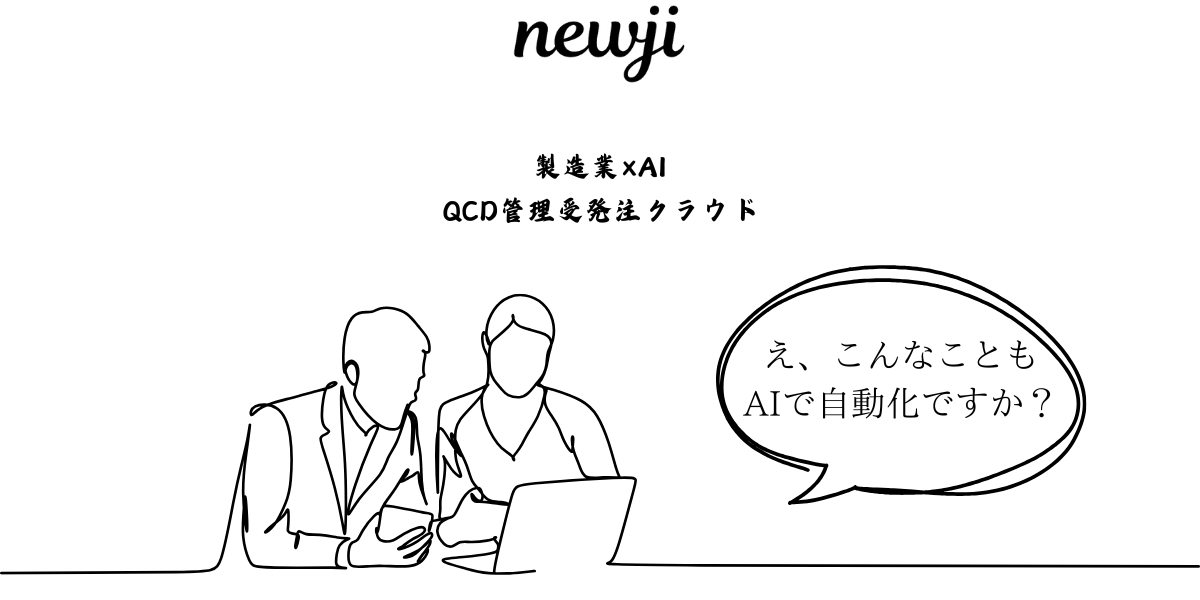
Latest trends in component standardization in the electronics manufacturing industry
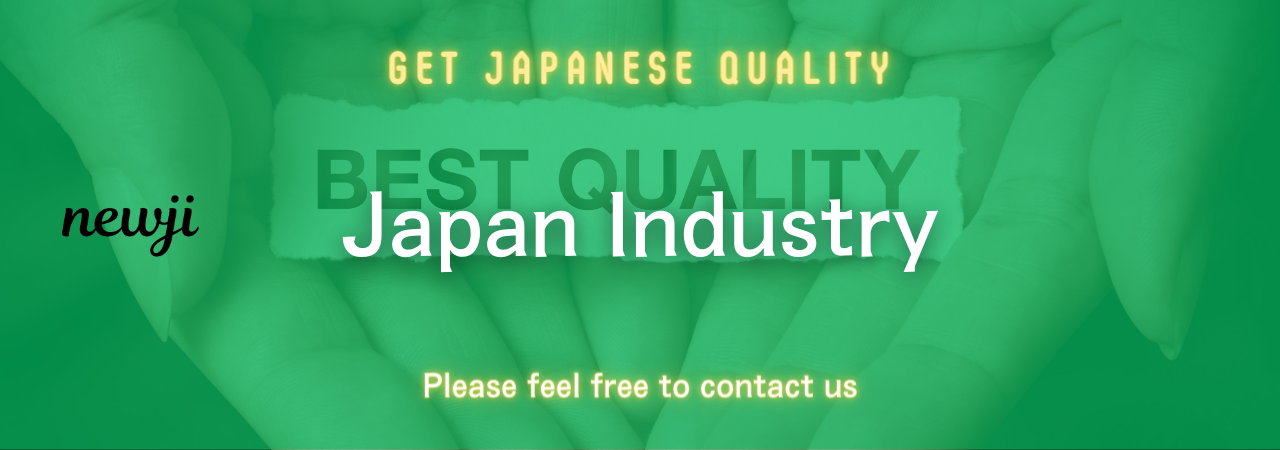
目次
Understanding Component Standardization
In the rapidly evolving electronics manufacturing industry, component standardization has emerged as a critical factor in maintaining competitiveness and efficiency.
As products become increasingly complex, the need for consistency and interchangeability of components has become more apparent.
Component standardization involves establishing and adhering to a set of agreed-upon criteria to ensure that parts can be easily swapped or integrated across different projects or products.
This approach not only simplifies the manufacturing process but also helps in reducing costs, improving quality, and speeding up time-to-market.
Why Standardization Matters
The core advantage of component standardization lies in its ability to streamline production.
When components are standardized, manufacturers can source these parts from multiple suppliers with confidence that they will function interchangeably.
This minimizes the risk of supply chain disruptions and decreases dependency on any single supplier.
Moreover, using standardized components simplifies the design process.
Engineers can focus on innovation and improvement rather than re-designing parts for each new product.
This leads to faster development cycles and allows manufacturers to respond quickly to market demands.
Technological Advancements Driving Standardization
Technological advancements continue to fuel component standardization in several ways.
The rise of the Internet of Things (IoT) and the proliferation of smart devices demand components that can communicate seamlessly.
Standardized interfaces and communication protocols are essential for ensuring compatibility across diverse devices.
Furthermore, advancements in Artificial Intelligence (AI) and machine learning have driven the need for standardized components that can handle complex computations effectively.
As these technologies continue to evolve, the demand for more adaptable and standardized parts is set to increase.
Industry-Led Standardization Initiatives
Several industry consortia and organizations are actively working to develop and promote standardization within electronics manufacturing.
For instance, the Institute of Electrical and Electronics Engineers (IEEE) plays a pivotal role in defining global standards for electronics components.
Organizations like the International Electrotechnical Commission (IEC) and the Joint Electron Device Engineering Council (JEDEC) are also instrumental in setting industry standards, ensuring that manufacturers around the globe adhere to a common set of guidelines.
These initiatives not only facilitate international trade but also foster innovation by providing a solid foundation upon which new technologies can be built.
Through collaborative efforts, the industry can better address common challenges and streamline the adoption of best practices.
Challenges in Implementing Standardization
Despite the numerous benefits, implementing standardization across the electronics manufacturing sector is not without its challenges.
One of the primary obstacles is achieving consensus among manufacturers with varied interests and priorities.
Balancing the need for standardized components with the unique requirements of different products can be complex.
Moreover, rapid technological change often outpaces the standardization process.
By the time a standard is widely accepted, emerging technologies might render it obsolete.
This dynamic environment requires a flexible approach to standardization that can adapt quickly to new advancements.
The Role of Sustainability
Sustainability is becoming an increasingly important consideration in component standardization.
Manufacturers are recognizing the environmental benefits of standardizing components, such as reducing electronic waste and enhancing the recyclability of products.
Standardized components can be more easily repurposed or recycled, aligning with global efforts to minimize the environmental impact of manufacturing.
Organizations are also exploring the use of sustainable materials in standardized components, promoting eco-friendly manufacturing practices.
As consumers become more environmentally conscious, incorporating sustainability into standardization strategies can enhance brand reputation and drive consumer loyalty.
Future Trends in Component Standardization
Looking ahead, several trends are poised to shape the future of component standardization in the electronics manufacturing industry.
Customization within standardization is gaining traction, allowing manufacturers to offer personalized products while maintaining the benefits of standardized components.
Mass customization leverages advanced manufacturing technologies like 3D printing and automation to tailor components to specific needs without deviating from standard practices.
Additionally, the integration of digital twins—virtual models of physical components—enables real-time monitoring and optimization, enhancing the efficiency and reliability of standardized components.
Digital twins also facilitate predictive maintenance, reducing downtime and extending the lifecycle of products.
Interoperability will remain a key focus, particularly as 5G networks expand and the demand for interconnected devices grows.
Standardization efforts will continue to ensure that components can operate seamlessly across various platforms and networks.
Conclusion
Component standardization is transforming the electronics manufacturing industry by fostering efficiency, reducing costs, and driving innovation.
As technological advancements continue to emerge, the role of standardization is expected to expand, accommodating new trends and addressing future challenges.
Manufacturers must remain agile, embracing standardization as a dynamic and integral part of their strategy to thrive in a competitive and fast-paced market.
By balancing innovation with standardization, the electronics manufacturing industry can achieve sustainable growth, benefiting businesses, consumers, and the environment alike.
資料ダウンロード
QCD調達購買管理クラウド「newji」は、調達購買部門で必要なQCD管理全てを備えた、現場特化型兼クラウド型の今世紀最高の購買管理システムとなります。
ユーザー登録
調達購買業務の効率化だけでなく、システムを導入することで、コスト削減や製品・資材のステータス可視化のほか、属人化していた購買情報の共有化による内部不正防止や統制にも役立ちます。
NEWJI DX
製造業に特化したデジタルトランスフォーメーション(DX)の実現を目指す請負開発型のコンサルティングサービスです。AI、iPaaS、および先端の技術を駆使して、製造プロセスの効率化、業務効率化、チームワーク強化、コスト削減、品質向上を実現します。このサービスは、製造業の課題を深く理解し、それに対する最適なデジタルソリューションを提供することで、企業が持続的な成長とイノベーションを達成できるようサポートします。
オンライン講座
製造業、主に購買・調達部門にお勤めの方々に向けた情報を配信しております。
新任の方やベテランの方、管理職を対象とした幅広いコンテンツをご用意しております。
お問い合わせ
コストダウンが利益に直結する術だと理解していても、なかなか前に進めることができない状況。そんな時は、newjiのコストダウン自動化機能で大きく利益貢献しよう!
(Β版非公開)